Углеродное волокно — Википедия
Углеродное волокно — материал, состоящий из тонких нитей диаметром от 5 до 15 мкм, образованных преимущественно атомами углерода. Атомы углерода объединены в микроскопические кристаллы, выровненные параллельно друг другу. Выравнивание кристаллов придает волокну большую прочность на растяжение. Углеродные волокна характеризуются высокой силой натяжения, низким удельным весом, низким коэффициентом температурного расширения и химической инертностью.
Углеродное волокно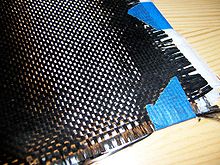
Впервые получение и применение углеродных волокон было предложено и запатентовано в 1880 г. американским изобретателем Эдисоном для нитей накаливания в электрических лампах. Эти волокна получались в результате пиролиза хлопкового или вискозного волокна и отличались высокой пористостью и хрупкостью.
Вторично интерес к углеродным волокнам появился, когда велись поиски материалов, пригодных для использования в качестве компонентов для изготовления ракетных двигателей. Углеродные волокна по своим качествам оказались одними из наиболее подходящих для такой роли армирующими материалами, поскольку они обладают высокой термостойкостью, хорошими теплоизоляционными свойствами, коррозионной стойкостью к воздействию газовых и жидких сред, высокими удельными прочностью и жёсткостью.
В 1958 г. в США были получены УВ на основе вискозных волокон. При изготовлении углеродных волокон нового поколения применялась ступенчатая высокотемпературная обработка гидратцеллюлозных (ГТЦ) волокон (900 °C, 2500 °C), что позволило достичь значений предела прочности при растяжении 330—1030 МПа и модуля упругости 40 ГПа. Несколько позднее (в 1960 г.) была предложена технология производства коротких монокристаллических волокон («усов») графита с прочностью 20 ГПа и модулем упругости 690 ГПа. «Усы» выращивались в электрической дуге при температуре 3600 °C и давлении 0,27 МПа (2,7 атм). Совершенствованию этой технологии уделялось много времени и внимания на протяжении ряда лет, однако в настоящее время она применяется редко ввиду своей высокой стоимости по сравнению с другими методами получения углеродных волокон.
Почти в то же время в СССР и несколько позже, в 1961 г., в Японии были получены УВ на основе полиакрилонитрильных (ПАН) волокон. Характеристики первых углеродных волокон на основе ПАН были невысоки, но постепенно технология совершенствовалась и уже через 10 лет (к 1970 г.) были получены углеродные волокна на основе ПАН-волокон с пределом прочности 2070 МПа и модулем упругости 480 ГПа. Тогда же была показана возможность получения углеродных волокон по этой технологии с ещё более высокими механическими характеристиками: модулем упругости до 800 ГПа и пределом прочности более 3 ГПа. УВ на основе нефтяных пеков были получены в 1970 г. также в Японии.
Углеродная ткань плотностью 200 гр/м2Алхадиси Абдул Кадир и другие исследовали влияние добавки углеродного волокна на механические свойства легкого бетона. Волокно было добавлено в соотношении 0,5 %, 0,1 %, 1,5 % по объёму. Все составы характеризовалось повышенной прочностью на сжатие и прочностью на разрыв, а также сопротивлению изгибу около 30 %, 58 % и 35 %, соответственно, по сравнению с эталонной смеси[2].
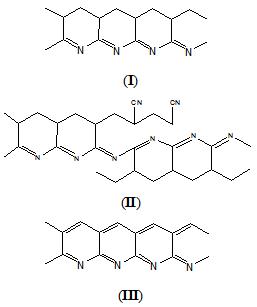
Рис. 1. Структуры, образующиеся при окислении ПАН-волокна
УВ обычно получают термической обработкой химических или природных органических волокон, при которой в материале волокна остаются главным образом атомы углерода. Температурная обработка состоит из нескольких этапов. Первый из них представляет собой окисление исходного (полиакрилонитрильного, вискозного) волокна на воздухе при температуре 250 °C в течение 24 часов. В результате окисления образуются лестничные структуры, представленные на рис. 1. После окисления следует стадия карбонизации — нагрева волокна в среде азота или аргона при температурах от 800 до 1500 °C. В результате карбонизации происходит образование графитоподобных структур. Процесс термической обработки заканчивается графитизацией при температуре 1600-3000 °C, которая также проходит в инертной среде. В результате графитизации количество углерода в волокне доводится до 99 %. Помимо обычных органических волокон (чаще всего вискозных и полиакрилонитрильных), для получения УВ могут быть использованы специальные волокна из фенольных смол, лигнина, каменноугольных и нефтяных пеков.
Углеродные волокна могут выпускаться в разнообразном виде: штапелированные (резаные, короткие) нити, непрерывные нити, тканые и нетканые материалы. Наиболее распространенный вид продукции — жгуты, пряжа, ровинг, нетканые холсты. Изготовление всех видов текстильной продукции производится по обычным технологиям, так же, как для других видов волокон. Вид текстильной продукции определяется предполагаемым способом использования УВ в композиционном материале, точно так же, как и сам метод получения композита. Основные методы получения композитов, армированных углеродными волокнами, являются обычными для волокнистых материалов: выкладка, литье под давлением, пултрузия и другие. В настоящее время выпускается ряд видов УВ и УВМ, основные из которых перечислены ниже.
- На основе вискозных нитей и волокон:
- нити, ленты, ткани;
- нетканый материал;
- активированные сорбирующие ткани;
- активированные сорбирующие нетканые материалы.
- На основе вискозных штапельных волокон:
- волокна и нетканые материалы: карбонизованые и графитированые;
- На основе ПАН-нитей и жгутов:
- ленты и ткани ;
- активированные сорбирующие волокна и нетканые материалы;
- дисперсный порошок из размолотых волокон.
- На основе ПАН-волокон:
- Волокна и нетканые материалы: карбонизованные и графитированные.
УВ имеют исключительно высокую теплостойкость: при тепловом воздействии вплоть до 1600—2000 °С в отсутствие кислорода механические показатели волокна не изменяются. Это предопределяет возможность применения УВ в качестве тепловых экранов и теплоизоляционного материала в высокотемпературной технике. На основе УВ изготавливают углерод-углеродные композиты, которые отличаются высокой абляционной стойкостью. УВ устойчивы к агрессивным химическим средам, однако окисляются при нагревании в присутствии кислорода. Их предельная температура эксплуатации в воздушной среде составляет 300—370 °С. Нанесение на УВ тонкого слоя карбидов, в частности, SiC или нитрида бора, позволяет в значительной мере устранить этот недостаток. Благодаря высокой химической стойкости УВ применяют для фильтрации агрессивных сред, очистки газов, изготовления защитных костюмов и др. Изменяя условия термообработки, можно получить УВ с различными электрофизическими свойствами (удельное объёмное электрическое сопротивление от 2⋅10
Активацией УВ получают материалы с большой активной поверхностью (300—1500 м²/г), являющиеся прекрасными сорбентами. Нанесение на волокно катализаторов позволяет создавать каталитические системы с развитой поверхностью.
Обычно УВ имеют прочность порядка 0,5—1 ГПа и модуль 20—70 ГПа, а подвергнутые ориентационной вытяжке — прочность 2,5—3,5 ГПа и модуль 200—450 ГПа. Благодаря низкой плотности (1,7—1,9 г/см³) по удельному значению (отношение прочности и модуля к плотности) механических свойств лучшие УВ превосходят все известные жаростойкие волокнистые материалы. Удельная прочность УВ уступает удельной прочности стекловолокна и арамидных волокон. На основе высокопрочных и высокомодульных УВ с использованием полимерных связующих получают конструкционные углеродопласты. Разработаны композиционные материалы на основе УВ и керамических связующих, УВ и углеродной матрицы, а также УВ и металлов, способные выдерживать более жёсткие температурные воздействия, чем обычные пластики.
УВ применяют для армирования композиционных, теплозащитных, химостойких и других материалов в качестве наполнителей в различных видах углепластиков. Наиболее ёмкий рынок для УВ в настоящее время — производство первичных и вторичных структур в самолетах различных производителей, в том числе таких компаний как «Boeing» и «Airbus» (до 30 тонн на одно изделие). По причине резко возросшего спроса в 2004—2006 гг. на рынке наблюдался большой дефицит волокна, что привело к его резкому подорожанию.
Из УВ изготавливают электроды, термопары, экраны, поглощающие электромагнитное излучение, изделия для электро- и радиотехники. На основе УВ получают жёсткие и гибкие электронагреватели, в том числе ставшие популярными т. н. «карбоновые нагреватели», обогревающие одежду и обувь. Углеродный войлок — единственно возможная термоизоляция в вакуумных печах, работающих при температуре 1100 °C и выше. Благодаря химической инертности углеволокнистые материалы используют в качестве фильтрующих слоёв для очистки агрессивных жидкостей и газов от дисперсных примесей, а также в качестве уплотнителей и сальниковых набивок. УВА и углеволокнистые ионообменники служат для очистки воздуха, а также технологических газов и жидкостей, выделения из последних ценных компонентов, изготовления средств индивидуальной защиты органов дыхания. Широкое применение находят УВА (в частности, актилен) в медицине для очистки крови и других биологических жидкостей. В специальных салфетках для лечения гнойных ран, ожогов и диабетических язв незаменима ткань АУТ-М, разработанная в начале 80-х годов и опробованная при боевых действиях в Афганистане [3]. Как лекарственное средство применяют при отравлениях (благодаря высокой способности сорбировать яды. Например, препарат «Белосорб», или АУТ-МИ на основе светлогорского сорбента), как носители лекарственных и биологически активных веществ. УВ-катализаторы используют в высокотемпературных процессах неорганического и органического синтеза, а также для окисления содержащихся в газах примесей (СО до CO2, SO2 до SO3 и др.). Широко применяется при изготовлении деталей кузова в автоспорте, а также в производстве спортивного инвентаря (клюшки, вёсла, лыжи, велосипедные рамы и компоненты, обувь) и т. д.
Углеволокно применяется в строительстве в различных системах внешнего армирования (СВА) — при его помощи усиливают железобетонные, металлические, каменные и деревянные конструктивные элементы зданий и сооружений с целью устранения последствий разрушения материала и коррозии арматуры в результате длительного воздействия природных факторов и агрессивных сред в процессе эксплуатации, а также для сейсмоусиления. Суть данного метода заключается в повышении прочности элементов, воспринимающих нагрузки в процессе эксплуатации зданий и сооружений, с помощью углеродных тканей, ламелей и сеток. Усиление строительных конструкций углеволокном повышает несущую способность без изменения структурной схемы объекта.
- С. Симамура. Углеродные волокна. М.: «Мир», 1987.
- Конкин А. А., Углеродные и другие жаростойкие волокнистые материалы, М., 1974.
Углеводородное волокно, карбоновая нить, производство полимерных материалов и карбона, углеволокно цена
Углеродное волокно — материал, состоящий из тонких нитей диаметром от 3 до 15 микрон, образованных преимущественно атомами углерода. Атомы углерода объединены в микроскопические кристаллы, выровненные параллельно друг другу. Выравнивание кристаллов придает волокну большую прочность на растяжение. Углеродные волокна характеризуются высокой силой натяжения, низким удельным весом, низким коэффициентом температурного расширения и химической инертностью.
Производством углеродного волокна в России занимается компания ООО «Композит-Волокно», входящее в холдинг «Композит»
Углеродное волокно является основой для производства углепластиков (или карбона, карбонопластиков, от «carbon», «carbone» — углерод). Углепластики — полимерные композиционные материалы из переплетенных нитей углеродного волокна, расположенных в матрице из полимерных (чаще эпоксидных) смол.
Углеродные композиционные материалы отличаются высокой прочностью, жесткостью и малой массой, часто прочнее стали, но гораздо легче.
Производство полимерных материалов
Наше предложение
Производство полимерных материалов требует значительного опыта. Для достижения принятых стандартов качества необходимы не только квалифицированные сотрудники, но и налаженная технология изготовления изделий. По этим причинам все представленные позиции в каталоге имеют высокое качество, гарантируют достижение поставленных перед ними задач и обладают регулярными положительными отзывами.
В каталоге вы сможете подобрать изделия для таких сфер:
- машиностроение;
- космическая и авиационная промышленность;
- ветроэнергетика;
- строительство;
- спортивный инвентарь;
- товары народного потребления
Наше производство изделий из полимерных материалов может обеспечить вас тем количеством изделий, которое вам будет необходимо. Отсутствуют ограничения по объему заказа. При этом вы можете рассчитывать на полную консультацию от профессионалов и оперативное выполнение поставленных задач. Производство полимерных материалов в России, которое мы осуществляем, дает возможность приобретения необходимых единиц каталога по оптовой системе. Изучите наш каталог, а также, если у вас остались какие-либо вопросы — не откладывайте их на потом и обращайтесь прямо сейчас в нашу службу поддержки.
Почему цена на углеволокно так высока?
Большие затраты энергии — основная причина высокой себестоимости углеродного волокна. Впрочем, это с лихвой компенсируется впечатляющим результатом. Даже не верится, что все начиналось с «мягкого и пушистого» материала, содержащегося в довольно прозаических вещах и известных не только сотрудникам химических лабораторий. Белые волокна — так называемые сополимеры полиакрилонитрила — широко используются в текстильной промышленности. Они входят в состав плательных, костюмных и трикотажных тканей, ковров, брезента, обивочных и фильтрующих материалов. Иными словами, сополимеры полиакрилонитрила присутствуют везде, где на прилагающейся этикетке упомянуто акриловое волокно. Некоторые из них «несут службу» в качестве пластмасс. Наиболее распространенный среди таковых — АБС-пластик. Вот и получается, что «двоюродных родственников» у карбона полным-полно. Карбоновая нить имеет впечатляющие показатели по усилию на разрыв, но ее способность «держать удар» на изгиб «подкачала». Поэтому, для равной прочности изделий, предпочтительнее использовать ткань. Организованные в определенном порядке волокна «помогают» друг другу справиться с нагрузкой. Однонаправленные ленты лишены такого преимущества. Однако, задавая различную ориентацию слоев, можно добиться искомой прочности в нужном направлении, значительно сэкономить на массе детали и излишне не усиливать непринципиальные места.
Что такое карбоновая ткань?
Для изготовления карбоновых деталей применяется как просто углеродное волокно с хаотично расположенными и заполняющими весь объем материала нитями, так и ткань (Carbon Fabric). Существуют десятки видов плетений. Наиболее распространены Plain, Twill, Satin. Иногда плетение условно — лента из продольно расположенных волокон «прихвачена» редкими поперечными стежками только для того, чтобы не рассыпаться. Плотность ткани, или удельная масса, выраженная в г/м2, помимо типа плетения зависит от толщины волокна, которая определяется количеством угленитей. Данная характеристика кратна тысячи. Так, аббревиатура 1К означает тысячу нитей в волокне. Чаще всего в автоспорте и тюнинге применяются ткани плетения Plain и Twill плотностью 150–600 г/м2, с толщиной волокон 1K, 2.5K, 3К, 6K, 12K и 24К. Ткань 12К широко используется и в изделиях военного назначения (корпуса и головки баллистических ракет, лопасти винтов вертолетов и подводных лодок, и пр.), то есть там, где детали испытывают колоссальные нагрузки.
Бывает ли цветной карбон? Желтый карбон бывает?
Часто от производителей тюнинговых деталей и, как следствие, от заказчиков можно услышать про «серебристый» или «цветной» карбон. «Серебряный» или «алюминиевый» цвет — всего лишь краска или металлизированное покрытие на стеклоткани. И называть карбоном такой материал неуместно — это стеклопластик. Отрадно, что и в данной области продолжают появляться новые идеи, но по характеристикам стеклу с углем углеродным никак не сравниться. Цветные же ткани чаще всего выполнены из кевлара. Хотя некоторые производители и здесь применяют стекловолокно; встречается даже окрашенные вискоза и полиэтилен. При попытке сэкономить, заменив кевлар на упомянутые полимерные нити, ухудшается адгезия такого продукта со смолами. Ни о какой прочности изделий с такими тканями не может быть и речи. Отметим, что «Кевлар», «Номекс» и «Тварон» — патентованные американские марки полимеров. Их научное название «арамиды». Это родственники нейлонов и капронов. В России есть собственные аналоги — СВМ, «Русар», «Терлон» СБ и «Армос». Но, как часто бывает, наиболее «раскрученное» название — «Кевлар» — стало именем нарицательным для всех материалов.
Что такое кевлар и какие у него свойства?
По весовым, прочностным и температурным свойствам кевлар уступает углеволокну. Способность же кевлара воспринимать изгибающие нагрузки существенно выше. Именно с этим связано появление гибридных тканей, в которых карбон и кевлар содержатся примерно поровну. Детали с угольно-арамидными волокнами воспринимают упругую деформацию лучше, чем карбоновые изделия. Однако есть у них и минусы. Карбон-кевларовый композит менее прочен. Кроме того, он тяжелее и «боится» воды. Арамидные волокна склонны впитывать влагу, от которой страдают и они сами, и большинство смол. Дело не только в том, что «эпоксидка» постепенно разрушается водно-солевым раствором на химическом уровне. Нагреваясь и охлаждаясь, а зимой вообще замерзая, вода механически расшатывает материал детали изнутри. И еще два замечания. Кевлар разлагается под воздействием ультрафиолета, а формованный материал в смоле утрачивает часть своих замечательных качеств. Высокое сопротивление разрыву и порезам отличают кевларовую ткань только в «сухом» виде. Потому свои лучшие свойства арамиды проявляют в других областях. Маты, сшитые из нескольких слоев таких материалов, — основной компонент для производства легких бронежилетов и прочих средств безопасности. Из нитей кевлара плетут тонкие и прочные корабельные канаты, делают корд в шинах, используют в приводных ремнях механизмов и ремнях безопасности на автомобилях.
А можно обклеить деталь карбоном?
Непреодолимое желание иметь в своей машине детали в черно-черную или черно-цветную клетку привели к появлению диковинных суррогатов карбона. Тюнинговые салоны обклеивают деревянные и пластмассовые панели салонов углеродной тканью и заливают бесчисленными слоями лака, с промежуточной ошкуриванием. На каждую деталь уходят килограммы материалов и масса рабочего времени. Перед трудолюбием мастеров можно преклоняться, но такой путь никуда не ведет. Выполненные в подобной технике «украшения» порой не выдерживают температурных перепадов. Со временем появляется паутина трещин, детали расслаиваются. Новые же детали неохотно встают на штатные места из-за большой толщины лакового слоя.
Как производятся карбоновые и/или композитные изделия?
Технология производства настоящих карбоновых изделий основывается на особенностях применяемых смол. Компаундов, так правильно называют смолы, великое множество. Наиболее распространены среди изготовителей стеклопластиковых обвесов полиэфирная и эпоксидная смолы холодного отверждения, однако они не способны полностью выявить все преимущества углеволокна. Прежде всего, по причине слабой прочности этих связующих компаундов. Если же добавить к этому плохую стойкость к воздействию повышенных температур и ультрафиолетовых лучей, то перспектива применения большинства распространенных марок весьма сомнительна. Сделанный из таких материалов карбоновый капот в течение одного жаркого летнего месяца успеет пожелтеть и потерять форму. Кстати, ультрафиолет не любят и «горячие» смолы, поэтому, для сохранности, детали стоит покрывать хотя бы прозрачным автомобильным лаком.
Компаунды холодного твердения.
«Холодные» технологии мелкосерийного выпуска малоответственных деталей не позволяют развернуться, поскольку имеют и другие серьезные недостатки. Вакуумные способы изготовления композитов (смола подается в закрытую матрицу, из которой откачан воздух) требуют продолжительной подготовки оснастки. Добавим к этому и перемешивание компонентов смолы, «убивающее» массу времени, что тоже не способствует производительности. Говорить о ручной выклейке вообще не стоит. Метод же напыления рубленого волокна в матрицу не позволяет использовать ткани. Собственно, все идентично стеклопластиковому производству. Просто вместо стекла применяется уголь. Даже самый автоматизированный из процессов, который к тому же позволяет работать с высокотемпературными смолами (метод намотки), годится для узкого перечня деталей замкнутого сечения и требует очень дорогого оборудования.
Эпоксидные смолы горячего отверждения прочнее, что позволяет выявить качества карбонов в полной мере. У некоторых «горячих» смол механизм полимеризации при «комнатной» температуре запускается очень медленно. На чем, собственно, и основана так называемая технология препрегов, предполагающая нанесение готовой смолы на углеткань или углеволокно задолго до процесса формования. Приготовленные материалы просто ждут своего часа на складах.
В зависимости от марки смолы время жидкого состояния обычно длится от нескольких часов до нескольких недель. Для продления сроков жизнеспособности, приготовленные препреги, иногда хранят в холодильных камерах. Некоторые марки смол «живут» годами в готовом виде. Прежде чем добавить отвердитель, смолы разогревают до 50–60 C, после чего, перемешав, наносят посредством специального оборудования на ткань. Затем ткань прокладывают полиэтиленовой пленкой, сворачивают в рулоны и охлаждают до 20–25 C. В таком виде материал будет храниться очень долго. Причем остывшая смола высыхает и становится практически не заметной на поверхности ткани. Непосредственно при изготовлении детали нагретое связующее вещество становится жидким как вода, благодаря чему растекается, заполняя весь объем рабочей формы и процесс полимеризации ускоряется.
Компаунды горячего твердения.
«Горячих» компаундов великое множество, при этом у каждой собственные температурные и временные режимы отверждения. Обычно, чем выше требуемые показания термометра в процессе формовки, тем прочнее и устойчивее к нагреву готовое изделие. Исходя из возможностей имеющегося оборудования и требуемых характеристик конечного продукта, можно не только выбирать подходящие смолы, но делать их на заказ. Некоторые отечественные заводы-изготовители предлагают такую услугу. Естественно, не бесплатно.
Препреги как нельзя лучше подходят для производства карбона в автоклавах. Перед загрузкой в рабочую камеру нужное количество материала тщательно укладывается в матрице и накрывается вакуумным мешком на специальных распорках. Правильное расположение всех компонентов очень важно, иначе не избежать нежелательных складок, образующихся под давлением. Исправить ошибку впоследствии будет невозможно. Если бы подготовка велась с жидким связующим, то стала бы настоящим испытанием для нервной системы рабочих с неясными перспективами успеха операции.
Процессы, происходящие внутри установки, незатейливы. Высокая температура расплавляет связующее и «включает» полимеризацию, вакуумный мешок удаляет воздух и излишки смолы, а повышенное давление в камере прижимает все слои ткани к матрице. Причем происходит все одновременно.
С одной стороны, одни преимущества. Прочность такого углепластика практически максимальна, объекты самой затейливой формы делаются за один «присест». Сами матрицы не монументальны, поскольку давление распределено равномерно во всех направлениях и не нарушает геометрию оснастки. Что означает быструю подготовку новых проектов. С другой стороны, нагрев до нескольких сотен градусов и давление, порой доходящее до 20 атм., делают автоклав очень дорогостоящим сооружением. В зависимости от его габаритов цены на оборудование колеблются от нескольких сотен тысяч до нескольких миллионов долларов. Прибавим к этому нещадное потребление электроэнергии и трудоемкость производственного цикла. Результат — высокая себестоимость продукции. Есть, впрочем, технологии подороже и посложнее, чьи результаты впечатляют еще больше. Углерод-углеродные композиционные материалы (УУКМ) в тормозных дисках на болидах Формулы-1 и в соплах ракетных двигателей выдерживают чудовищные нагрузки при температурах эксплуатации, достигающих 3000 C. Эту разновидность карбона получают путем графитизации термореактивной смолы, которой пропитывают спрессованное углеродное волокно заготовки. Операция чем-то похожа на производство самого углеволокна, только происходит она при давлении 100 атмосфер. Да, большой спорт и военно-космическая сфера деятельности способны потреблять штучные вещи по «заоблачным» ценам. Для тюнинга и, тем более, для серийной продукции такое соотношение «цены-качества» неприемлемо.
Если решение найдено, оно выглядит настолько простым, что удивляешься: «Что же мешало додуматься раньше?». Тем не менее, идея разделить процессы, происходящие в автоклаве, возникла спустя годы поиска. Так появилась и стала набирать обороты технология, сделавшая горячее формование карбона похожим на штамповку. Препрег готовится в виде сэндвича. После нанесения смолы ткань с обеих сторон покрывается либо полиэтиленовой, либо более термостойкой пленкой. «Бутерброд» пропускается между двух валов, прижатых друг к другу. При этом лишняя смола и нежелательный воздух удаляются, примерно так же, как и при отжиме белья в стиральных машинах образца 1960-х годов. В матрицу препрег вдавливается пуансоном, который фиксируется резьбовыми соединениями. Далее вся конструкция помещается в термошкаф.
Тюнинговые фирмы изготавливают матрицы из того же карбона и даже прочных марок алебастра. Гипсовые рабочие формы, правда, недолговечны, но пара-тройка изделий им вполне по силам. Более «продвинутые» матрицы делаются из металла и иногда оснащаются встроенными нагревательными элементами. В серийном производстве они оптимальны. Кстати, метод подходит и для некоторых деталей замкнутого сечения. В этом случае легкий пуансон из вспененного материала остается внутри готового изделия. Антикрыло Mitsubishi Evo — пример такого рода.
Механические усилия заставляют думать о прочности оснастки, да и система матрица — пуансон требует либо 3D-моделирования, либо модельщика экстра-класса. Но это, все же, в сотни раз дешевле технологии с автоклавом.
Алексей Романов редактор журнала «ТЮНИНГ Автомобилей»
Углеродное волокно – характеристики и особенности хранения.
В наиболее ответственных изделиях применяют углекомпозиты (углепластики). Согласно расчетам, среди всех возможных соединений, на основе периодической системы элементов, графит имеет самые высокие прочностные и термические характеристики. Углеродное волокно имеет один из наиболее высоких показателей по удельной прочности среди других волокон. Имеет высокую стойкость к кручению и усталости. Уступая лишь в ударной прочности арамиду и стеклу.
Углеродное волокно-производство
Столь высокую стоимость углеродного волокна обуславливает сложность и энергоемкость процесса его получения. Смысл процесса состоит в поэтапной чистке углеродосодержащих нитей от ненужных атомов, оставляя в конце процесса до 99% углерода в объеме нити.
УВ получают путем термического разложения (пиролизом) исходных нитей: гидратоцеллюлозных, полиакрилонитрильных (ПАН). Так же нефтяных или каменноугольных пеков. В настоящее время, промышленное значение имеет производство УВ на базе вискозы или ПАН.
Процесс получения УВ на основе ПАН
Следует заметить, что химический состав и структура УВ зависит от состава исходного сырья.
В первую очередь, полиакриловые жгуты подвергают окислению, проводя термическую обработку на воздухе при температуре около 200 °С.
Окисленный ПАН так же представляет интерес в некоторых сферах производства как термостойкий и трудно горючий материал.
После окисления, полотно проходит через печи карбонизации (около 1500 °С) и графитизации (около 3000 °С). На этой стадии удаляются остатки водорода и гетероатомов, происходит образование двойных связей между атомами углерода. Процессы карбонизации и графитизации проводятся в инертной среде.
В завершении процесса карбонизации (в некоторых случаях стадия графитизации может исключаться) жгут имеет готовый химический состав и структуру, но проходит еще ряд этапов для повешения адгезии с матрицей:
— обработка поверхности. Поверхность карбонового полотна вследствие данной реакции становится «шероховатой». Обнажая атомы углерода и создавая свободные функциональные группы способные к ионному обмену.
— нанесение ПАВ (поверхностно активное вещество). Оно же, так называемое аппретирование. В качестве аппрета чаще наносятся эпоксидные смолы без отвердителя. Аппрет защищает от истирания в процессе хранения, транспортировки и текстильной переработки. Вытесняет из пор влагу и воздух.
Этап сушки после нанесения аппрета является завершающим этапом, после которого жгуты наматываются на бобины (обычно массой до 8 кг).
Характеристики углеродного волокна
Модуль упругости. УВ обычно группируются в соответствии со своим модулем:
- Низкомодульное (HS): 160-270 ГПа;
- Средний модуль (IM): 270-325ГПа;
- Высокомодульное (НМ): 325-440 ГПа;
- Сверхвысокий модуль (UHM): 440+ ГПа;
Диаметр и количество элементарных нитей. Каждый жгут состоит из тысяч элементарных нитей (филаментов). Диаметр такой углеродной нити: 5-7 мкм, что в 2-3 раза тоньше человеческого волоса. В маркировке у любого типа волокна есть обозначения: 3К, 6К, 12К, 24К- это и есть количество филаментов в жгуте (в тысячах).
Линейная плотность. Кроме обычной плотности, у волокон принято выделять так же линейную. Измеряется она в тексах (tex). Если линейная плотность указана 800 tex, значит, километр этого жгута имеет массу 800гр.
Прочностные характеристики
Итоговое значение прочности, указываемое в сертификатах качества и т.д. снимается уже с пропитанного и отвержденного жгутика (микропластика). Микропластик- жгут пропитанный полимерным связующим и отвержденный при воздействии растягивающего напряжения.
УВ достаточно хрупкое поэтому не имеет большого смысла снимать с него прочностные характеристики в непропитанном виде. Так же, для конечного потребителя важнее знать свойства углеродного волокна в отвержденной полимерной матрице, то есть в композите. Поэтому в чаще всего указывают:
- Прочность при растяжении комплексной нити в микропластике. ГПа
- Модуль упругости при растяжении комплексной нити в микропластике. ГПа
Условия транспортировки и хранения углеродного волокна
- Бобины должны храниться в крытых складских помещениях в упакованном виде, коробки должны находиться в горизонтальном положении.
- Рекомендуемые условия хранения.
- Температура: 0-40 °С. Хранение при минусовой температуре не рекомендуется.
- Влажность: 40-80%.
- Допускается перевозка в неотапливаемом транспорте при температуре до -30 °С.
- Во избежание конденсации влаги на поверхности. Перед использованием, нераспакованные бобины должны быть выдержаны не менее 48 часов при температуре от 20 до 30 °С и влажности от 40 до 80%.
- При правильных условиях хранения, производитель гарантирует сохранность свойств в течение 2 лет с даты производства.
Заключение
Надо понимать, УВ не является гарантией качества и гарантией сверх прочностных свойств изделия. Сами по себе углеродные нити довольно хрупкие и ломкие. Без правильных условий полимеризации или при не правильном подборе матрицы или ее не совместимости с нитью можно и не достигнуть заявленных производителем свойств. К тому же УВ уступает базальту и стеклу в некоторых видах мех. испытаний. При том, что даже самое дорогое стекло и базальт в 10ки раз дешевле, чем самое дешевое углеродное волокно. В дополнение ко всему, по причине широкого применения углеродных волокон в оборонной промышленности, для того чтобы купить его за рубежом напрямую у производителя необходимо получение лицензии.
Углеродное волокно — это… Что такое Углеродное волокно?
Углеродное волокно — материал, состоящий из тонких нитей диаметром от 3 до 15 микрон, образованных преимущественно атомами углерода. Атомы углерода объединены в микроскопические кристаллы, выровненные параллельно друг другу. Выравнивание кристаллов придает волокну большую прочность на растяжение. Углеродные волокна характеризуются высокой силой натяжения, низким удельным весом, низким коэффициентом температурного расширения и химической инертностью.
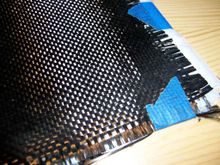
История
Впервые получение и применение углеродных волокон (УВ) (точнее, нитей) было предложено и запатентовано известным американским изобретателем — Томасом Эдисоном — в 1880 г. в качестве нитей накаливания в электрических лампах. Эти волокна получались в результате пиролиза хлопкового или вискозного волокна и отличались хрупкостью и высокой пористостью и впоследствии были заменены вольфрамовыми нитями. В течение последующих 20 лет он же предложил получать углеродные и графитированные волокна на основе различных природных волокон.
Вторично интерес к углеродным волокнам появился в середине XX в., когда велись поиски материалов, пригодных для использования в качестве компонентов композитов для изготовления ракетных двигателей. УВ по своим качествам оказались одними из наиболее подходящих для такой роли армирующими материалами, поскольку они обладают высокой термостойкостью, хорошими теплоизоляционными свойствами, коррозионной стойкостью к воздействию газовых и жидких сред, высокими удельными прочностью и жесткостью.
В 1958 г. в США были получены УВ на основе вискозных волокон. При изготовлении углеродных волокон нового поколения применялась ступенчатая высокотемпературная обработка гидратцеллюлозных (ГТЦ) волокон (900 °C, 2500 °C), что позволило достичь значений предела прочности при растяжении 330—1030 МПа и модуля упругости 40 ГПа. Несколько позднее (в 1960 г.) была предложена технология производства коротких монокристаллических волокон («усов») графита с прочностью 20 ГПа и модулем упругости 690 ГПа. «Усы» выращивались в электрической дуге при температуре 3600 °C и давлении 0,27 МПа (2,7 атм). Совершенствованию этой технологии уделялось много времени и внимания на протяжении ряда лет, однако в настоящее время она применяется редко ввиду своей высокой стоимости по сравнению с другими методами получения углеродных волокон.
Почти в то же время в СССР и несколько позже, в 1961 г., в Японии были получены УВ на основе полиакрилонитрильных (ПАН) волокон. Характеристики первых углеродных волокон на основе ПАН были невысоки, но постепенно технология совершенствовалась и уже через 10 лет (к 1970 г.) были получены углеродные волокна на основе ПАН-волокон с пределом прочности 2070 МПа и модулем упругости 480 ГПа. Тогда же была показана возможность получения углеродных волокон по этой технологии с еще более высокими механическими характеристиками: модулем упругости до 800 ГПа и пределом прочности более 3 ГПа. УВ на основе нефтяных пеков были получены в 1970 г. также в Японии.
Получение
Рис. 1. Структуры, образующиеся при окислении ПАН-волокна
УВ обычно получают термической обработкой химических или природных органических волокон, при которой в материале волокна остаются главным образом атомы углерода. Температурная обработка состоит из нескольких этапов. Первый из них представляет собой окисление исходного (полиакрилонитрильного, вискозного) волокна на воздухе при температуре 250 °C в течение 24 часов. В результате окисления образуются лестничные структуры, представленные на рис. 1. После окисления следует стадия карбонизации — нагрева волокна в среде азота или аргона при температурах от 800 до 1500 °C. В результате карбонизации происходит образование графитоподобных структур. Процесс термической обработки заканчивается графитизацией при температуре 1600-3000 °C, которая также проходит в инертной среде. В результате графитизации количество углерода в волокне доводится до 99 %. Помимо обычных органических волокон (чаще всего вискозных и полиакрилонитрильных), для получения УВ могут быть использованы специальные волокна из фенольных смол, лигнина, каменноугольных и нефтяных пеков.
Дополнительная переработка УВ
Углеродные волокна могут выпускаться в разнообразном виде: штапелированные (резаные, короткие) нити, непрерывные нити, тканые и нетканые материалы. Наиболее распространенный вид продукции — жгуты, пряжа, ровинг, нетканые холсты. Изготовление всех видов текстильной продукции производится по обычным технологиям, так же как для других видов волокон. Вид текстильной продукции определяется предполагаемым способом использования УВ в композиционном материале, точно так же, как и сам метод получения композита. Основные методы получения композитов, армированных углеродными волокнами, являются обычными для волокнистых материалов: выкладка, литье под давлением, пултрузия и другие. В настоящее время выпускается ряд видов УВ и УВМ, основные из которых перечислены ниже.
- На основе вискозных нитей и волокон:
- нити, ленты, ткани — Урал®;
- нетканый материал — Карбопон®;
- активированные сорбирующие ткани — Бусофит®,САУТ-1С, АУТ-М;
- активированные сорбирующие нетканые материалы — Карбопон-Актив®.
- На основе вискозных штапельных волокон:
- волокна и нетканые материалы: карбонизованые — Углен® (технология восстановлена на Светлогорском ПО «Химволокно») и графитированые — Грален®;
- На основе ПАН-нитей и жгутов:
- ленты и ткани — ЛУ®, УКН®, Кулон®, Элур®, ITECWRAP®.
- активированные сорбирующие волокна и нетканые материалы — Актилен®, Ликрон®;
- дисперсный порошок из размолотых волокон — Ваулен®, АУТ-МИ (для медицинских целей).
- На основе ПАН-волокон:
- Волокна и нетканые материалы: карбонизованные — Эвлон® и графитированные — Конкор®.
Выпускают УВ и за рубежом: в США — Торнел®, Целион®, Фортафил®; в Великобритании — Модмор®, Графил®; в Японии — Торейка®, Куреха-лон® и т. д.[1]
До 2007 г. в СНГ углеродные волокна производились на двух предприятиях: «Аргон» (г. Балаково, Россия) — производство на основе ПАН (полиакрилонитрила) и РУП «Светлогорское ПО Химволокно»[2] — производство на основе вискозы. Оба предприятия обладают собственными мощностями по производству прекурсора. Предприятие в Беларуси — крупнейший мировой производитель углеволокна из вискозы[3]. Существовавшие во времена СССР в г. Бровары (под Киевом, Украина), г. Запорожье (Украина) г. С.-Петербурге (НПО «Химволокно»), г. Шуе (Россия) утрачены.
В настоящее время в России углеволокнистые материалы производятся ОАО «НПК «Химпроминжиниринг» (входит в структуру Росатома)[4], ФГУП НИИграфит[5], НПЦ «УВИКОМ»[6], ООО «НИИ ВСУ «ИНТЕР/ТЭК»[7].
Свойства
УВ имеют исключительно высокую теплостойкость: при тепловом воздействии вплоть до 1600—2000 °С в отсутствии кислорода механические показатели волокна не изменяются. Это предопределяет возможность применения УВ в качестве тепловых экранов и теплоизоляционного материала в высокотемпературной технике. На основе УВ изготавливают углерод-углеродные композиты, которые отличаются высокой абляционной стойкостью. УВ устойчивы к агрессивным химическим средам, однако окисляются при нагревании в присутствии кислорода. Их предельная температура эксплуатации в воздушной среде составляет 300—350°С. Нанесение на УВ тонкого слоя карбидов, в частности SiC, или нитрида бора позволяет в значительной мере устранить этот недостаток. Благодаря высокой химической стойкости УВ применяют для фильтрации агрессивных сред, очистки газов, изготовления защитных костюмов и др. Изменяя условия термообработки, можно получить УВ с различными электрофизическими свойствами (удельное объёмное электрическое сопротивление от 2·10−3 до 106 ом/см) и использовать их в качестве разнообразных по назначению электронагревательных элементов, для изготовления термопар и др.
Активацией УВ получают материалы с большой активной поверхностью (300—1500 м²/г), являющиеся прекрасными сорбентами. Нанесение на волокно катализаторов позволяет создавать каталитические системы с развитой поверхностью.
Обычно УВ имеют прочность порядка 0,5—1 ГПа и модуль 20—70 ГПа, а подвергнутые ориентационной вытяжке — прочность 2,5—3,5 ГПа и модуль 200—450 ГПа. Благодаря низкой плотности (1,7—1,9 г/см³) по удельному значению (отношение прочности и модуля к плотности) механических свойств лучшие УВ превосходят все известные жаростойкие волокнистые материалы. Удельная прочность УВ уступает удельной прочности стекловолокна и арамидных волокон. На основе высокопрочных и высокомодульных УВ с использованием полимерных связующих получают конструкционные углеродопласты. Разработаны композиционные материалы на основе УВ и керамических связующих, УВ и углеродной матрицы, а также УВ и металлов, способные выдерживать более жесткие температурные воздействия, чем обычные пластики.
Применение
УВ применяют для армирования композиционных, теплозащитных, хемостойких в качестве наполнителей в различных видах углепластиков. Наиболее емкий рынок для УВ в настоящее время — производство первичных и вторичных структур в самолетах различных производителей, в том числе таких компаний как «Боинг» и «Эрбас» (до 30 тонн на одно изделие). По причине резко возросшего спроса в 2004—2006 гг. на рынке наблюдался большой дефицит волокна, что привело к его резкому подорожанию.
Из УВМ изготавливают электроды, термопары, экраны, поглощающие электромагнитное излучение, изделия для электро- и радиотехники. На основе УВ получают жесткие и гибкие электронагреватели, в том числе ставшие популярными т. н. «карбоновые нагреватели», обогреваемую одежду и обувь. Углеродный войлок — единственно возможная термоизоляция в вакуумных печах, работающих при температуре 1100 °C и выше. Благодаря химической инертности углеволокнистые материалы используют в качестве фильтрующих слоев для очистки агрессивных жидкостей и газов от дисперсных примесей, а также в качестве уплотнителей и сальниковых набивок. УВА и углеволокнистые ионообменники служат для очистки воздуха, а также технологических газов и жидкостей, выделения из последних ценных компонентов, изготовления средств индивидуальной защиты органов дыхания. Широкое применение находят УВА (в частности, актилен) в медицине для очистки крови и других биологических жидкостей. В специальных салфетках для лечения гнойных ран, ожогов и диабетических язв — незаменима ткань АУТ-М, разработанная в начале 80-х годов и опробованная при боевых действиях в Афганистане[8]. В настоящее время широко применяются углеродные сорбирующие салфетки «Сорусал» и «Легиус».[источник не указан 303 дня] Как лекарственное средство применяют при отравлениях (благодаря высокой способности сорбировать яды. Например препарат «Белосорб», или АУТ-МИ на основе светлогорского сорбента), как носители лекарственных и биологически активных веществ. УВ катализаторы используют в высокотемпературных процессах неорганических и органических синтеза, а также для окисления содержащихся в газах примесей (СО до CO2, SO2 до SO3 и др.). Широко применяется при изготовлении деталей кузова в автоспорте, а также в производстве спортивного инвентаря (клюшки, вёсла, лыжи, велосипедные запчасти, обувь ) и т. д.
Ссылки
- С. Симамура. Углеродные волокна. М.: «Мир», 1987.
- Конкин А. А., Углеродные и другие жаростойкие волокнистые материалы, М., 1974.
- СТО 73645443-03-2010 Система высокопрочного усиления железобетонных конструкций ITECWRAP®/ITECRESIN®, Е., 2011.
См.также
Примечания
Углеродное волокно — Википедия
Углеродное волокно — материал, состоящий из тонких нитей диаметром от 5 до 15 мкм, образованных преимущественно атомами углерода. Атомы углерода объединены в микроскопические кристаллы, выровненные параллельно друг другу. Выравнивание кристаллов придает волокну большую прочность на растяжение. Углеродные волокна характеризуются высокой силой натяжения, низким удельным весом, низким коэффициентом температурного расширения и химической инертностью.
Углеродное волокно Углеродная лентаИстория
Впервые получение и применение углеродных волокон было предложено и запатентовано в 1880 г. американским изобретателем Эдисоном для нитей накаливания в электрических лампах. Эти волокна получались в результате пиролиза хлопкового или вискозного волокна и отличались высокой пористостью и хрупкостью.
Вторично интерес к углеродным волокнам появился, когда велись поиски материалов, пригодных для использования в качестве компонентов для изготовления ракетных двигателей. Углеродные волокна по своим качествам оказались одними из наиболее подходящих для такой роли армирующими материалами, поскольку они обладают высокой термостойкостью, хорошими теплоизоляционными свойствами, коррозионной стойкостью к воздействию газовых и жидких сред, высокими удельными прочностью и жёсткостью.
Углеродное волокно 3К, 12К, 24КВ 1958 г. в США были получены УВ на основе вискозных волокон. При изготовлении углеродных волокон нового поколения применялась ступенчатая высокотемпературная обработка гидратцеллюлозных (ГТЦ) волокон (900 °C, 2500 °C), что позволило достичь значений предела прочности при растяжении 330—1030 МПа и модуля упругости 40 ГПа. Несколько позднее (в 1960 г.) была предложена технология производства коротких монокристаллических волокон («усов») графита с прочностью 20 ГПа и модулем упругости 690 ГПа. «Усы» выращивались в электрической дуге при температуре 3600 °C и давлении 0,27 МПа (2,7 атм). Совершенствованию этой технологии уделялось много времени и внимания на протяжении ряда лет, однако в настоящее время она применяется редко ввиду своей высокой стоимости по сравнению с другими методами получения углеродных волокон.
Почти в то же время в СССР и несколько позже, в 1961 г., в Японии были получены УВ на основе полиакрилонитрильных (ПАН) волокон. Характеристики первых углеродных волокон на основе ПАН были невысоки, но постепенно технология совершенствовалась и уже через 10 лет (к 1970 г.) были получены углеродные волокна на основе ПАН-волокон с пределом прочности 2070 МПа и модулем упругости 480 ГПа. Тогда же была показана возможность получения углеродных волокон по этой технологии с ещё более высокими механическими характеристиками: модулем упругости до 800 ГПа и пределом прочности более 3 ГПа. УВ на основе нефтяных пеков были получены в 1970 г. также в Японии.
Углеродная ткань плотностью 200 гр/м2Чэнь и Чун исследовали эффект углеродного волокна с добавкой кремнезема на усадку при высыхании бетона и пришли к выводу, что объемное соотношение углеродного волокна в количестве 0,19% (при средней длине волокна 5мм и диаметре 10 мкм) с отношением микрокремнезема, равным 15% от массы цемента, вызывало снижение усадки при высыхании до 84%. Исследователи обнаружили, что использование углеродного волокна с микрокремнеземом позволяет улучшить такие свойства, как прочность при сжатии и химическая стойкость[1].
Алхадиси Абдул Кадир и др. исследовали влияние добавки углеродного волокна на механические свойства легкого бетона. Волокно было добавлено в соотношении 0,5% 0,1%, 1,5% по объему. Все составы характеризовалось повышенной прочностью на сжатие и прочностью на разрыв, а также сопротивлению изгибу около 30% , 58% и 35%, соответственно, по сравнению с эталонной смеси[2].
Получение
Рис. 1. Структуры, образующиеся при окислении ПАН-волокна
УВ обычно получают термической обработкой химических или природных органических волокон, при которой в материале волокна остаются главным образом атомы углерода. Температурная обработка состоит из нескольких этапов. Первый из них представляет собой окисление исходного (полиакрилонитрильного, вискозного) волокна на воздухе при температуре 250 °C в течение 24 часов. В результате окисления образуются лестничные структуры, представленные на рис. 1. После окисления следует стадия карбонизации — нагрева волокна в среде азота или аргона при температурах от 800 до 1500 °C. В результате карбонизации происходит образование графитоподобных структур. Процесс термической обработки заканчивается графитизацией при температуре 1600-3000 °C, которая также проходит в инертной среде. В результате графитизации количество углерода в волокне доводится до 99 %. Помимо обычных органических волокон (чаще всего вискозных и полиакрилонитрильных), для получения УВ могут быть использованы специальные волокна из фенольных смол, лигнина, каменноугольных и нефтяных пеков.
Дополнительная переработка УВ
Углеродные волокна могут выпускаться в разнообразном виде: штапелированные (резаные, короткие) нити, непрерывные нити, тканые и нетканые материалы. Наиболее распространенный вид продукции — жгуты, пряжа, ровинг, нетканые холсты. Изготовление всех видов текстильной продукции производится по обычным технологиям, так же как для других видов волокон. Вид текстильной продукции определяется предполагаемым способом использования УВ в композиционном материале, точно так же, как и сам метод получения композита. Основные методы получения композитов, армированных углеродными волокнами, являются обычными для волокнистых материалов: выкладка, литье под давлением, пултрузия и другие. В настоящее время выпускается ряд видов УВ и УВМ, основные из которых перечислены ниже.
- На основе вискозных нитей и волокон:
- нити, ленты, ткани;
- нетканый материал; Файл:Углеродный войлок
- активированные сорбирующие ткани;
- активированные сорбирующие нетканые материалы.
- На основе вискозных штапельных волокон:
- волокна и нетканые материалы: карбонизованые и графитированые;
- На основе ПАН-нитей и жгутов:
- ленты и ткани ;
- активированные сорбирующие волокна и нетканые материалы;
- дисперсный порошок из размолотых волокон.
- На основе ПАН-волокон:
- Волокна и нетканые материалы: карбонизованные и графитированные.
Свойства
УВ имеют исключительно высокую теплостойкость: при тепловом воздействии вплоть до 1600—2000 °С в отсутствие кислорода механические показатели волокна не изменяются. Это предопределяет возможность применения УВ в качестве тепловых экранов и теплоизоляционного материала в высокотемпературной технике. На основе УВ изготавливают углерод-углеродные композиты, которые отличаются высокой абляционной стойкостью. УВ устойчивы к агрессивным химическим средам, однако окисляются при нагревании в присутствии кислорода. Их предельная температура эксплуатации в воздушной среде составляет 300—370 °С. Нанесение на УВ тонкого слоя карбидов, в частности SiC, или нитрида бора позволяет в значительной мере устранить этот недостаток. Благодаря высокой химической стойкости УВ применяют для фильтрации агрессивных сред, очистки газов, изготовления защитных костюмов и др. Изменяя условия термообработки, можно получить УВ с различными электрофизическими свойствами (удельное объёмное электрическое сопротивление от 2·10−3 до 106 Ом/см) и использовать их в качестве разнообразных по назначению электронагревательных элементов, для изготовления термопар и др.
Активацией УВ получают материалы с большой активной поверхностью (300—1500 м²/г), являющиеся прекрасными сорбентами. Нанесение на волокно катализаторов позволяет создавать каталитические системы с развитой поверхностью.
Обычно УВ имеют прочность порядка 0,5—1 ГПа и модуль 20—70 ГПа, а подвергнутые ориентационной вытяжке — прочность 2,5—3,5 ГПа и модуль 200—450 ГПа. Благодаря низкой плотности (1,7—1,9 г/см³) по удельному значению (отношение прочности и модуля к плотности) механических свойств лучшие УВ превосходят все известные жаростойкие волокнистые материалы. Удельная прочность УВ уступает удельной прочности стекловолокна и арамидных волокон. На основе высокопрочных и высокомодульных УВ с использованием полимерных связующих получают конструкционные углеродопласты. Разработаны композиционные материалы на основе УВ и керамических связующих, УВ и углеродной матрицы, а также УВ и металлов, способные выдерживать более жёсткие температурные воздействия, чем обычные пластики.
Применение
УВ применяют для армирования композиционных, теплозащитных, химостойких и других материалов в качестве наполнителей в различных видах углепластиков. Наиболее ёмкий рынок для УВ в настоящее время — производство первичных и вторичных структур в самолетах различных производителей, в том числе таких компаний как «Boeing» и «Airbus» (до 30 тонн на одно изделие). По причине резко возросшего спроса в 2004—2006 гг. на рынке наблюдался большой дефицит волокна, что привело к его резкому подорожанию.
Из УВ изготавливают электроды, термопары, экраны, поглощающие электромагнитное излучение, изделия для электро- и радиотехники. На основе УВ получают жёсткие и гибкие электронагреватели, в том числе ставшие популярными т. н. «карбоновые нагреватели», обогревающие одежду и обувь. Углеродный войлок — единственно возможная термоизоляция в вакуумных печах, работающих при температуре 1100 °C и выше. Благодаря химической инертности углеволокнистые материалы используют в качестве фильтрующих слоёв для очистки агрессивных жидкостей и газов от дисперсных примесей, а также в качестве уплотнителей и сальниковых набивок. УВА и углеволокнистые ионообменники служат для очистки воздуха, а также технологических газов и жидкостей, выделения из последних ценных компонентов, изготовления средств индивидуальной защиты органов дыхания. Широкое применение находят УВА (в частности, актилен) в медицине для очистки крови и других биологических жидкостей. В специальных салфетках для лечения гнойных ран, ожогов и диабетических язв — незаменима ткань АУТ-М, разработанная в начале 80-х годов и опробованная при боевых действиях в Афганистане[3]. Как лекарственное средство применяют при отравлениях (благодаря высокой способности сорбировать яды. Например препарат «Белосорб», или АУТ-МИ на основе светлогорского сорбента), как носители лекарственных и биологически активных веществ. УВ катализаторы используют в высокотемпературных процессах неорганического и органического синтеза, а также для окисления содержащихся в газах примесей (СО до CO2, SO2 до SO3 и др.). Широко применяется при изготовлении деталей кузова в автоспорте, а также в производстве спортивного инвентаря (клюшки, вёсла, лыжи, велосипедные рамы и компоненты, обувь) и т. д.
Углеволокно применяется в строительстве в различных системах внешнего армирования (СВА) — при его помощи усиливают железобетонные, металлические, каменные и деревянные конструктивные элементы зданий и сооружений с целью устранения последствий разрушения материала и коррозии арматуры в результате длительного воздействия природных факторов и агрессивных сред в процессе эксплуатации, а также для сейсмоусиления. Суть данного метода заключается в повышении прочности элементов, воспринимающих нагрузки в процессе эксплуатации зданий и сооружений, с помощью углеродных тканей, ламелей и сеток. Усиление строительных конструкций углеволокном повышает несущую способность без изменения структурной схемы объекта.
См. также
Примечания
Ссылки
- С. Симамура. Углеродные волокна. М.: «Мир», 1987.
- Конкин А. А., Углеродные и другие жаростойкие волокнистые материалы, М., 1974.
- Время углеродного волокна
Углеволокно — это… Что такое Углеволокно?
Углеродное волокно
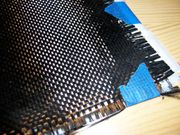
История
Впервые получение и применение углеродных волокон (УВ) (точнее, нитей) было предложено и запатентовано известным американским изобретателем — Томасом Алва Эдисоном в 1880 г. в качестве нитей накаливания в электрических лампах. Эти волокна получались в результате пиролиза хлопкового или вискозного волокна и отличались хрупкостью и высокой пористостью и впоследствии были заменены вольфрамовыми нитями. В течение последующих 20 лет он же предложил получать углеродные и графитированные волокна на основе различных природных волокон. Вторично интерес к углеродным волокнам появился в середине XX в., когда велись поиски материалов, пригодных для использования в качестве компонентов композитов для изготовления ракетных двигателей. УВ по своим качествам оказались одними из наиболее подходящих для такой роли армирующими материалами, поскольку они обладают высокой термостойкостью, хорошими теплоизоляционными свойствами, коррозионной стойкостью к воздействию газовых и жидких сред, высокими удельными прочностью и жесткостью. В 1958 г. в США были получены УВ на основе вискозных волокон. При изготовлении углеродных волокон нового поколения применялась ступенчатая высокотемпературная обработка ГТЦ-волокон (900 °C, 2500 °C), что позволило достичь значений предела прочности при растяжении 330—1030 МПа и модуля упругости 40 ГПа. Несколько позднее (в 1960 г.) была предложена технология производства коротких монокристаллических волокон («усов») графита с прочностью 20 ГПа и модулем упругости 690 ГПа. «Усы» выращивались в электрической дуге при температуре 3600 °C и давлении 0,27 МПа (2,7 атм). Совершенствованию этой технологии уделялось много времени и внимания на протяжении ряда лет, однако в настоящее время она применяется редко ввиду своей высокой стоимости по сравнению с другими методами получения углеродных волокон. Почти в то же время в России и несколько позже, в 1961 г., в Японии были получены УВ на основе полиакрилонитрильных (ПАН) волокон. Характеристики первых углеродных волокон на основе ПАН были невысоки, но постепенно технология совершенствовалась и уже через 10 лет (к 1970 г.) были получены углеродные волокна на основе ПАН-волокон с пределом прочности 2070 МПа и модулем упругости 480 ГПа. Тогда же была показана возможность получения углеродных волокон по этой технологии с еще более высокими механическими характеристиками: модулем упругости до 800 ГПа и пределом прочности более 3 ГПа. УВ на основе нефтяных пеков были получены в 1970 г. также в Японии. За счет специальных технологических приемов механические свойства УВ из пеков могут быть повышены до уровня волокон на основе ПАН. С этого времени разработки УВ развивались во многих фирмах и организациях мира, которые соревновались в достижении наиболее высоких механических свойств. Это соревнование продолжается и сегодня, однако, достигнув рекордных значений, повышать дальше показатели механических свойств оказалось весьма трудно.
Получение
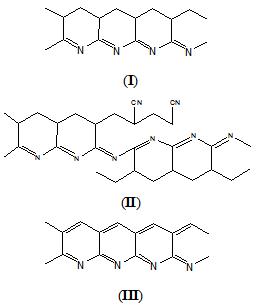
Рис. 1. Структуры, образующиеся при окислении ПАН-волокна
УВ обычно получают термической обработкой химических или природных органических волокон, при которой в материале волокна остаются главным образом атомы углерода. Температурная обработка состоит из нескольких этапов. Первый из них представляет собой окисление исходного (полиакрилонитрильного, вискозного) волокна на воздухе при температуре 250 °C в течение 24 часов. В результате окисления образуются лестничные структуры, представленные на рис. 1. После окисления следует стадия карбонизации — нагрева волокна в среде азота или аргона при температурах от 800 до 1500 °C. В результате карбонизации происходит образование графитоподобных структур. Процесс термической обработки заканчивается графитизацией при температуре 1600-3000°С, которая также проходит в инертной среде. В результате графитизации количество углерода в волокне доводится до 99 %. Помимо обычных органических волокон (чаще всего вискозных и полиакрилонитрильных), для получения У. в. могут быть использованы специальные волокна из фенольных смол, лигнина, каменноугольных и нефтяных пеков.
Дополнительная переработка УВ
Углеродные волокна могут выпускаться в разнообразном виде: штапелированные (резаные, короткие) нити, непрерывные нити, тканые и нетканые материалы. Наиболее распространенный вид продукции — жгуты, пряжа, ровинги, нетканые холсты. Изготовление всех видов текстильной продукции производится по обычным технологиям, так же как для других видов волокон. Вид текстильной продукции определяется предполагаемым способом использования УВ в композиционном материале, точно так же, как и сам метод получения композита. Основные методы получения композитов, армированных углеродными волокнами, являются обычными для волокнистых материалов: выкладка, литье под давлением, пултрузия и другие. В настоящее время выпускается ряд видов УВ и УВМ, основные из которых перечислены ниже. На основе вискозных нитей и волокон: • нити, ленты, ткани — Урал®; • нетканый материал — Карбопон®; • активированные сорбирующие ткани — Бусофит®,САУТ-1С, АУТ-М; • активированные сорбирующие нетканые материалы — Карбопон-Актив®. На основе вискозных штапельных волокон: • волокна и нетканые материалы: карбонизованые — Углен® (технология восстановлена на Светлогорском ПО «Химволокно») и графитированые — Грален®; На основе ПАН-нитей и жгутов: • ленты и ткани — ЛУ®, УКН®, Кулон®, Элур®. • активированные сорбирующие волокна и нетканые материалы — Актилен®, Ликрон®; • дисперсный порошок из размолотых волокон — Ваулен®, АУТ-МИ (для медицинских целей). На основе ПАН-волокон: • Волокна и нетканые материалы: карбонизованные — Эвлон® и графитированные — Конкор®. Выпускают УВ и за рубежом: в США — Торнел®, Целион®, Фортафил®; в Великобритании — Модмор®, Графил®; в Японии — Торейка®, Куреха-лон® и т. д.[1].
До 2007 г. в СНГ углеродные волокна производятся на двух предприятиях: «Аргон» (г. Балаково, Россия) — производство на основе ПАН (полиакрилонитрила) и РУП «Светлогорское ПО Химволокно» (г. Светлогорск, Беларусь, www.sohim.by) — производство на основе вискозы. Оба предприятия обладают собственными мощностями по производству прекурсора. Предприятие в Беларуси — крупнейший мировой производитель углеволокна из вискозы (http://www.promvest.info/354/5338/). По некоторым данным, продолжают работать обе линии НПО «Химволокно» в г. Мытищи. Существовавшие во времена СССР в г. Бровары (под Киевом, Украина), г. Запорожье (Украина) г. С.-Петербурге (НПО «Химволокно»), г. Шуе (Россия) утрачены безвозвратно. Неясна судьба производств в г. Челябинск и г. Электроугли Московской области. Предположительно, частичное оборудование (печи активации) имеются в распоряжении АО «Неорганика», г. Электросталь.
Компания ОАО «НПК «Химпроминжиниринг» (входит в структуру Росатома) является единственным в России производителем углеродных волокон и одним из не многих производителей ПАН-прекурсоров, которые выпускаются на ее дочерних предприятиях – ООО «Аргон» (г. Балаково Саратовской области), ООО «Завод углеродных и композиционных материалов» http://zukm.ru/ (г. Челябинск) и ООО «СНВ» (г. Саратов). Так же ПАН-прекурсоры (нить, жгут) выпускает ФГУП «ВНИИСВ» (г.Тверь).Основными потребителями углеродных волокон являются предприятия атомной отрасли, а также авиационные предприятия и предприятия военно-промышленного комплекса. ОАО «НПК «Химпроминжиниринг» планирует к 2020 году выйти на объем производства не менее 3000 тонн углеродных волокон в год.
Свойства
УВ имеют исключительно высокую теплостойкость: при тепловом воздействии вплоть до 1600—2000 °С в отсутствии кислорода механические показатели волокна не изменяются. Это предопределяет возможность применения УВ в качестве тепловых экранов и теплоизоляционного материала в высокотемпературной технике. На основе УВ изготавливают углерод-углеродные композиты, которые отличаются высокой абляционной стойкостью. УВ устойчивы к агрессивным химическим средам, однако окисляются при нагревании в присутствии кислорода. Их предельная температура эксплуатации в воздушной среде составляет 300—350°С. Нанесение на УВ тонкого слоя карбидов, в частности SiC, или нитрида бора позволяет в значительной мере устранить этот недостаток. Благодаря высокой химической стойкости УВ применяют для фильтрации агрессивных сред, очистки газов, изготовления защитных костюмов и др. Изменяя условия термообработки, можно получить УВ с различными электрофизическими свойствами (удельное объёмное электрическое сопротивление от 2·10^-3 до 10^6 ом/см) и использовать их в качестве разнообразных по назначению электронагревательных элементов, для изготовления термопар и др.
Активацией УВ получают материалы с большой активной поверхностью (300—1500 м²/г), являющиеся прекрасными сорбентами. Нанесение на волокно катализаторов позволяет создавать каталитические системы с развитой поверхностью.
Обычно УВ имеют прочность порядка 0,5—1 Гн/м² и модуль 20—70 Гн/м², а подвергнутые ориентационной вытяжке — прочность 2,5—3,5 Гн/м² и модуль 200—450 Гн/м². Благодаря низкой плотности (1,7—1,9 г/м³) по удельному значению (отношение прочности и модуля к плотности) механических свойств УВ превосходят все известные жаростойкие волокнистые материалы. На основе высокопрочных и высокомодульных УВ с использованием полимерных связующих получают конструкционные углеродопласты. Разработаны композиционные материалы на основе УВ и керамических связующих, УВ и углеродной матрицы, а также УВ и металлов, способные выдерживать более жесткие температурные воздействия, чем обычные пластики.
Применение
УВ применяют для армирования композиционных, теплозащитных, хемостойких в качестве наполнителей в различных видах углепластиков. Наиболее емкий рынок для УВ в настоящее время — производство первичных и вторичных структур в самолетах «Боинг» и «Аэробус» (до 30тн на одно изделие). По причине резко возросшего спроса в 2004-2006г.г. на рынке наблюдался большой дефицит волокна, что привело к его резкому удорожанию.
Из УВМ изготовляют электроды, термопары, экраны, поглощающие электромагнитное излучение, изделия для электро- и радиотехники. На основе УВ получают жесткие и гибкие электронагреватели, в том числе ставшие полулярными т.н. «карбоновые нагреватели», обогреваемую одежду и обувь. Углеродный войлок — единственно возможная термоизоляция в вакуумных печах, работающих при температуре 1100 С и выше. Благодаря химической инертности углеволокнистые материалы используют в качестве фильтрующих слоев для очистки агрессивных жидкостей и газов от дисперсных примесей, а также в качестве уплотнителей и сальниковых набивок. УВА и углеволокнистые ионообменники служат для очистки воздуха, а также технологических газов и жидкостей, выделения из последних ценных компонентов, изготовления средств индивидуальной защиты органов дыхания. Широкое применение находят УВА (в частности, актилен) в медицине для очистки крови и других биологических жидкостей. В специальных салфетках для лечения гнойных ран, ожогов и диабетических язв — незаменима ткань АУТ-М, разработанная в начале 80-х годов и опробованная в Афганистане (http://www.health-ua.com/articles/2291.html). Как лекарственное средство применяют при отравлениях (благодаря высокой способности сорбировать яды. Например препарат «Белосорб», или АУТ-МИ на основе светлогорского сорбента), как носители лекарственных и биологически активных веществ. УВ катализаторы используют в высокотемпературных процессах неорганических и органических синтеза, а также для окисления содержащихся в газах примесей (СО до CO2, SO2 до SO3 и др.).
Ссылки
[1] К. Перепелкин, «Текстиль» 2 (4), 2003
[2] С. Симамура. Углеродные волокна. М.: «Мир», 1987 г.
[3] Конкин А. А., Углеродные и другие жаростойкие волокнистые материалы, М., 1974.
Wikimedia Foundation. 2010.
Углеродное волокно Википедия
Углеродное волокно — материал, состоящий из тонких нитей диаметром от 5 до 15 мкм, образованных преимущественно атомами углерода. Атомы углерода объединены в микроскопические кристаллы, выровненные параллельно друг другу. Выравнивание кристаллов придает волокну большую прочность на растяжение. Углеродные волокна характеризуются высокой силой натяжения, низким удельным весом, низким коэффициентом температурного расширения и химической инертностью.
Углеродное волокно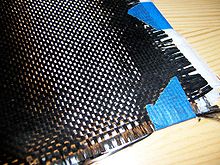
История[ | ]
Впервые получение и применение углеродных волокон было предложено и запатентовано в 1880 г. американским изобретателем Эдисоном для нитей накаливания в электрических лампах. Эти волокна получались в результате пиролиза хлопкового или вискозного волокна и отличались высокой пористостью и хрупкостью.
Вторично интерес к углеродным волокнам появился, когда велись поиски материалов, пригодных для использования в качестве компонентов для изготовления ракетных двигателей. Углеродные волокна по своим качествам оказались одними из наиболее подходящих для такой роли армирующими материалами, поскольку они обладают высокой термостойкостью, хорошими теплоизоляционными свойствами, коррозионной стойкостью к воздействию газовых и жидких сред, высокими удельными прочностью и жёсткостью.
Углеродное волокно 3К, 12К, 24КВ 1958 г. в США были получены УВ на основе вискозных волокон. При изготовлении углеродных волокон нового поколения применялась ступенчатая высокотемпературная обработка гидратцеллюлозных (ГТЦ) волокон (900 °C, 2500 °C), что позволило достичь значений предела прочности при растяжении 330—1030 МПа и модуля упругости 40 ГПа. Несколько позднее (в 1960 г.) была предложена технология производства коротких монокристаллических волокон («усов») графита с прочностью 20 ГПа и модулем упругости 690 ГПа. «Усы» выращивались в электрической дуге при температуре 3600 °C и давлении 0,27 МПа (2,7 атм). Совершенствованию этой технологии уделялось много времени и внимания на протяжении ряда лет, однако в настоящее время она применяется редко ввиду своей высокой стоимости по сравнению с другими методами получения углеродных волокон.
Почти в то же время в СССР и несколько позже, в 1961 г., в Японии были получены УВ на основе полиакрилонитрильных (ПАН) волокон. Характеристики первых углеродных волокон на основе ПАН были невысоки, но постепенно технология совершенствовалась и уже через 10 лет (к 1970 г.) были получены углеродные волокна на основе ПАН-волокон с пределом прочности 2070 МПа и модулем упругости 480 ГПа. Тогда же была показана возможность получения углеродных волокон по этой технологии с ещё более высокими механическими характеристиками: модулем упругости до 800 ГПа и пределом прочности более 3 ГПа. УВ на основе нефтяных пеков были получены в 1970 г. также в Японии.