Как определить состав металла? (тест по напильнику)
Этап 1: определение марки стали
Отобрав отслужившие свой век инструменты (надфили, напильники, рашпили, косы и т. п.), прежде всего следует определить, из какой марки стали они изготовлены. Чтобы круг поисков был как можно более ограниченным, следует знать, из каких видов стали изготавливается тот или иной инструмент. Так, напильники могут быть изготовлены как из инструментальной углеродистой стали (У10, У11, У12, У13), так и из легированной (ШХ6, ШХ9, ШХ15). Об этом можно узнать из перечня инструментов, приведенного ниже. Напильники, представленные в ассортименте КовкаПРО, изготовлены из высоколегированной стали твердостью 64-66HRC
Изделия из инструментальной и легированной стали:
Напильники — У10, У11, У12, У13, ШХ6, ШХ9, ШХ15
Надфили — У10, У11, У12
Рашпили — У7, У7А
Шаберы — У10, У12
Стамески, долота — У7, У8
Метчики — У10, У11, У12, Р9, 9ХС, Р18
Сверла по дереву — 9ХС
Сверла по металлу -Р9, Р18
Развертки – Р9, Р18, 9ХС
Фрезы – Р9, Р18
Зубила, отвертк – У7А, У8А, 7ХФ, 8ХФ
Кернеры – У7А, 7ХФ, 8ХФ
Швейные иглы- У7А, У8А
Пилы-ножовки – У8ГА
Полотна лучковой пилы – У8ГА, У10
Ножовочные полотна – У8, У8А, У9, У9А, У10, У10А, У11, У12
Ножницы по металлу – У12А
Молотки и кувалды – У7, У8
Топоры – У7
Косы, серпы – У7, У8
Вилы, зубья (клевцы) – У7, У8
грабель
Кузнечные инструменты – У7, У8
Этап 2: определение содержания углерода в стали
Как определить конкретно, из углеродистой или легированной стали сделан, например, напильник? Для этого следует прибегнуть к простому старинному способу. Мастера подметили, что мелкая металлическая стружка, получаемая при обработке металла абразивным кругом, раскаляясь, дает сноп искр, имеющий для каждого металла свои характерные особенности. «Соломинки», из которого состоит сноп искр, у каждой марки стали свои особые: длинные, короткие, сплошные, прерывистые, кучные и редкие, ровные или имеющие утолщения; от каждой из них могут отделяться, порой очень обильно, мелкие яркие звездочки; в расчет принимается яркость свечения снопа искр, а также цветовые оттенки — от светло-желтого до темно-красного.

Чем выше содержание углерода в стали, тем больше в снопе искр ярких звездочек. Если сталь содержит немного углерода, например около 0,12%, то искры, выходящие из-под абразивного диска, будут расходиться веером в виде слегка изогнутых черточек желто-соломенного цвета, имеющих утолщения в середине и на конце (1, см. рис. на с. 105). Сталь, содержащая 0,5% углерода, имеющая среднюю твердость, образует примерно такие же искры, но от места среднего утолщения у них отделяется небольшое количество звездочек (2). От высокоуглеродистой инструментальной стали отделяются обильные искры со звездочками (3). У хромистой стали искры длинные, оранжево-красные; от них, как тоненькие веточки от основной ветки, отходят под разными углами короткие искорки со звездочками на конце (4). Искры у вольфрамовой стали прерывающиеся, и к тому же у них небольшие утолщения на конце (5). Хромовольфрамовая быстрорежущая сталь дает одновременно короткие и длинные искры темно-красного цвета с утолщениями на конце (6).
Этап 3: испытание инструмента
Теперь вернемся к напильнику. Прежде чем приступить к его испытанию, необходимо обязательно надеть защитные очки, а недалеко от наждачного круга установить лист фанеры, окрашенной в черный цвет. На черном фоне искрение металла видно гораздо отчетливее, глазам приходится меньше напрягаться. Если мы с силой проведем напильником по наждачному кругу и получим обильные искры ярко-желтого цвета с множеством отделяющихся от них звездочек, то сможем сделать вывод, что он изготовлен из высокоуглеродистой инструментальной стали (У10—У13). И наоборот, сноп оранжево-красных длинных искр с разветвлениями и звездочками на конце говорит о том, что напильник сделан из легированной стали (ШХ6, ШХ9, ШХ15). Разумеется, таким способом определяется лишь примерный химический состав стали, но для любительской практики этого вполне достаточно. Зная, что напильник изготовлен из инструментальной стали указанных марок, по таблице определяют режим ее термической обработки.

Из таблицы видно, что сталь У11—У13, из которой сделан напильник, отжигается при температуре 750°С, а затем охлаждается постепенно на воздухе. Отжиг производят в муфельной печи, кузнечном горне или же в топке обычной печи. В электрической муфельной школьной печи отжигать металлические предметы удобно, так как встроенный термометр даст возможность проследить за температурой нагрева. Но глубина муфельной печи ограниченная. Если напильник в нее не входит, его оборачивают в несколько слоев брезентом и переламывают сильным ударом молотка.
Разломленный напильник вынимают из брезента, отжигают в муфельной печи, а затем медленно охлаждают. Образовавшаяся окалина часто мешает механической обработке. Поэтому, надев очки и рукавицы, ее сбивают молотком с помощью зубила.
Отожженная и обработанная инструментальная сталь становится достаточно мягкой: хорошо обрабатывается напильником, пилится и куется. При минимальной твердости она имеет максимальную пластичность и вязкость. Это дает возможность изготовить из нее штихели для гравирования, чеканы, зубильца, сечки, пробойки, другие инструменты для художественной обработки металла.
Изготовив из напильника нужный инструмент, его закаляют нагреванием согласно таблице до 780°С с последующим охлаждением в воде. После закалки сталь становится хрупкой, поэтому ее отпускают: нагревают до 180°С и охлаждают в воде или машинном масле. При отпуске температуру нагрева металла контролируют по так называемым цветам побежалости, которые соответствуют определенной температуре нагрева.
Как определить нержавейку?
Давайте поговорим о том, как определить некоторые свойства неизвестного нам куска стали. Определить марку стали на коленке, конечно, невозможно. У нас нет в кармане спектрометра. Да и хим.анализ для большинства недоступен. Однако, кое что мы все же сделать можем. Рассмотрим народный метод определения — ржавейка, нержавейка. С помощью магнита. Не магнитится, значит, нержавейка. Магнитится, совсем наоборот.
Этот метод корректен лишь отчасти. Магнитные свойства стали зависят от состава и, как следствие, от структуры стали. Нержавеющие стали бывают ферритные. Это 11-17% хрома, немного углерода и обладают магнитными свойствами. То есть они магнитятся. Аустенитные стали, нержавеющие: 18% хрома, 8% никеля. Вот как раз они не обладают или в меньшей степени обладают магнитными свойствами. Есть еще совмещенные аустенитно-ферритные. Это когда зажали немного никеля, добавляют его 2-4 % и наваливают туда до 25% хрома. Так же есть мартенситные нержавеющие стали. 12-17% хрома и выше. Имеют высокое содержание углерода, принимают закалку. То есть, это те стали, с которыми мы общаемся чаще всего. Это ножевые стали. Не только ножевые. Те, которые принимают закалку. Давайте рассмотрим на примере.
Нержавейка, на первый взгляд. Имеет магнитные свойства. Следующая ложка, тоже нержавейка. Не имеет магнитных свойств. Металл на некоторых инструментах магнитится лучше, на некоторых хуже. Ключ магнитится, сверло, стамеска. То есть, все тут достаточно проверенные стали. Из таких изделий, где не «китайский» состав, скажем так. Тут вполне объяснимые стали. И вот небольшой кусочек конструкционки. Тоже магнитится. Как мы видим, магнитом мы можем, определить, выявить, в принципе, нержавейку. Но только аустенитную. Это, в принципе, не противоречит утверждению, что магнитом можно выявить нержавейку. Но также мы не можем отрицать, что другая сталь не является при этом нержавейкой, если она магнитится. Поэтому, для определения коррозионных и других свойств я предлагаю использовать комплексный подход. То есть, магнитные свойства, мы конечно, будем рассматривать.
Как определить, какие свойства имеет та или иная сталь?
Глазами просто посмотреть на нее и понять, для чего этот предмет предназначен. Я предполагаю, например, что сверло изготовлено из р6м5. Не обязательно, что это так, но в большинстве случаев, это так. Ложки, мы знаем, не будут из углеродки. Какой-нибудь молоток не будет с высоким содержанием хрома. На ключе… У нас сейчас представлен хромванадиевый ключ, поэтому с этим сложнее.
Еще предмет из нашего набора интсрументов — нож из Китая, который продают, меняют с супермаркетах. В отношении его тоже можно предположить, какая там сталь. Просто анализ назначения предметов.
И третьим индикатором будет реакция стали на медный купорос. Вот такой раствор. 5:17 рисунок Вообще, он голубого цвета, но мы добавили натрий хлор, соль, в пропорции ½. Поэтому раствор стал зеленым. Возьмем спонжик и нанесем на каждую из сталей немного этого раствора. Стали, где это было необходимо, мы зачистили и заранее обезжирили. Реакция сильно зависит от температуры раствора. При температуре 50 градусов реакция происходит быстрее. От 50 до 80-90 градусов уже не такой быстрый скачок. Наносим небольшие капельки на изделия и наблюдаем практически мгновенную реакцию.
Мы видим, что на конструкционке и на стамеске зеленый раствор превратился в красноватый. Медный купорос вступил в реакцию и выделился хлорид меди. Это не ржавчина, как все думают. Как индикатор, он отличный! Потому что позволяет определить, что это сталь с минимумом или с полным отсутствием хрома, или других легирующих компонентов и с большим содержанием углерода в стали. На молотке мы также наблюдаем аналогичную ситуацию. Не успели поставить каплю, сразу же, буквально, выделился хлорид меди. Данный метод позволяет получить логическое значение – ржавейка, нержавейка, а еще очень хорошо показывает динамику окисления. Наносим раствор на наши ложки. Возьмем побольше раствора. Ложки тоже обезжирены. По-возможности, чуть-чуть снята пленка, но на нержавейках это бесполезно.
Обращаем внимание на цвет капель. Там, где они остались голубовато-зелеными, это и есть так называемая нержавеющая сталь. С чем можно сравнить? Из тех, которые быстро окислились и покраснели. Как можно быстро и просто увидеть разницу. Капля раствора, после нанесения сначала голубоватая, но тут же переходит в бордовый оттенок.
На двух ножах, из нашего набора пока никакой реакции нет. Это было видно сразу после нанесения. Хлорид меди не проступил. Это не значит, что эти стали супер-нержавеющие. Возможно, для того, чтобы реакция стала заметна, потребуется какое-то время. На конструкционке сразу проступило пятно хлорида меди. На стамеске то же самое. Яркая, почти мгновенная реакция. Что мы видим на р6м5 – сверле? То же самое. Есть красный оттенок хлорида меди. Но, так как р6м5 сложно легированная сталь, реакция происходит не так быстро, как с обычными углеродками. Хромванадиевый ключ получил цвет окисла черного цвета.
Проверим еще раз. Нанесем раствор в другом месте. Реакция аналогичная. Цвет окисла снова черный. Глазами незаметно, имеют ли эти пятна хотя бы слегка бордово-красноватый оттенок. Это интересно. На ноже, по прошествии некоторого времени, мы видим небольшое изменение цвета в желтый и где-то уже небольшое покраснение. Сравнивая две нержавейки мы можем наблюдать динамику процесса окисления. На втором ноже, абсолютно такой же цвет раствора, как и при нанесении. Проверяем ложку из ферритной стали магнитом. Изменений нет. Аустенитная, тоже без изменений.
Получается, магнит ни к чему не обязывает. Это не нержавейки. Но зато, с помощью магнита мы можем точно определить, что ложка, которая не магнитится, из аустинитной стали. Прошел 1 час времени. Смотрим на «китайский» нож. Кромку не держит и ржавеет как кусок углеродки. Капли раствора на втором ноже и на ложке из аустенитной нержавейки цвет не поменяли. Капля раствора на ложке из ферритной нержавейки слегка поменяла цвет. Соответственно, в ложке из аустенитной нержавейки присутствует никель в большом количестве, в ложке из ферритной нержавейки его нет.
Марки стали — Википедия
Марки стали — это классификация сталей по их химическому составу и физическим свойствам. В России, США[1], Европе[2], Японии[3] и Китае[4] используются различные способы маркировки для аналогичных сталей.
Сталь представляет собой сплав железа с углеродом, при этом содержание последнего в ней составляет не более 2,14 %, а железа более 50 %. Углерод придает сплаву твердость, но при его избытке металл становится слишком хрупким.
Одним из важнейших параметров, по которому стали делят на различные классы, является химический состав. Среди сталей по данному критерию выделяют легированные и углеродистые, последние подразделяются на мало- (углерода до 0,25 %), средне- (0,25-0,6 %) и высокоуглеродистые (в них содержится больше 0,6 % углерода).
Сталь подлежит обязательной маркировке.
Для уточнения сведений по конкретной марке стали могут использоваться так называемые марочники. 2-е (2003) и 3-е (2011) издания «Марочника сталей и сплавов» под ред. А. С. Зубченко содержат описание около 600 марок сталей и сплавов черных металлов, 4-е (2014) издание — более 700 марок[5].
Легированные стали, в отличие от нелегированных, имеют несколько иное обозначение, поскольку в них присутствуют элементы, специально вводимые в определённых количествах для обеспечения требуемых физических или механических свойств. К примеру:
- хром (Cr) повышает твёрдость и прочность
- никель (Ni) обеспечивает коррозионную стойкость и увеличивает прокаливаемость
- кобальт (Co) повышает жаропрочность и увеличивает сопротивление удару
- ниобий (Nb) помогает улучшить кислостойкость и уменьшает коррозию в сварных конструкциях.
Маркировка элементов сталей[править | править код]
Расшифровка марок сталей требует знать, какими буквами принято обозначать те или иные химические элементы, входящие в состав марки или сплава.
Если в самом конце марки стоит буква А, то таким образом обозначается высококачественная сталь, содержание фосфора и серы в которой сведено к минимуму (S<0,03 % и P<0,03 %), и соблюдены все условия высококачественного металлургического производства. Две буквы А в самом конце (АА) говорят о том, что данная марка стали особо чистая, то есть серы и фосфора в ней практически нет.
Буквенные обозначения «кп», «пс», «сп» применяются для указания степени раскисления стали[6]:
- «кп» — кипящая
- «пс» — полуспокойная
- «сп» — спокойная
Нестандартные стали обозначают по-разному. Так, опытные марки, выплавленные на заводе «Электросталь», обозначаются буквой И (исследовательские) и П (пробные) и порядковым номером, например, ЭИ179, ЭИ276, ЭП398 и т. д. Опытные марки, выплавленные на металлургическом заводе «Днепроспецсталь», обозначают ДИ 80, где Д — завод-изготовитель, И — исследовательская, 80 — порядковый номер, присвоенный марке стали.
Пример расшифровки марки стали 12Х18Н10Т[править | править код]
12Х18Н10Т — это популярная сталь (коррозионно-стойкая, жаростойкая аустенитного класса), которая применяется в сварных аппаратах и сосудах, работающих в разбавленных растворах кислот, в растворах щелочей и солей, а также в деталях, работающих под давлением при температуре от −196 °C до +600 °C[7].
Две цифры, стоящие в самом начале марки легированной стали, — это среднее содержание углерода в сотых долях процента. В данном примере содержание углерода составляет 0,12 %. Если вместо двух цифр стоит одна, то она показывает, сколько углерода (C) содержится в десятых долях процента. Если же цифр в начале марки стали совсем нет, то углерода в ней от 1 % и выше.
Буква Х и следующая за ней число 18 говорят, что в данной марке содержится 18 % хрома. Соотношение элемента в долях процента выражает только первое число, стоящее в начале марки, и это относится только к углероду. Все остальные числа в названии марки выражают количество конкретных элементов в процентах.
Далее следует комбинация Н10, это 10 % никеля.
В самом конце стоит буква Т без каких-либо цифр. Это значит, что содержание элемента мало, как правило, около 1 % (иногда — до 1,5 %). В данной марке легированной стали количество титана не превышает 1,5 %.
Итак, марка стали 12Х18Н10Т (конструкционная криогенная, аустенитного класса) содержит следующие сведения: 0,12 % углерода, 18 % хрома (Х), 10 % никеля (Н) и небольшое содержание титана (Т), не превышающее 1,5 %.
ОПРЕДЕЛЕНИЕ СВАРИВАЕМОСТИ И МАРКИ СТАЛИ ПО ИСКРАМ
Иногда приходится выполнять сварочные работы без какой-либо информации о свариваемом материале.
Данная статья поможет «дедовским» методом определить марку стали по искрам на абразивном круге, а также оценить — стоит ли браться за сварку в том или ином случае.
Свариваемые без ограничений
(стали свариваемые распространенными способами сварки, как правило без подогрева и термообработки)
Сталь марок Ст2 и СтЗ — искры светло-желтые, разветвления несколько более развиты и тоньше, чем сама нить; на концах искр стрелочки, звездочек нет. В начале искры имеется красно-желтый пучок от прикосновения заготовки к абразивному кругу
Сталь 10 — искры светло-желтые с малым количеством разветвлений, небольшое количество удлиненных звездочек, кончики нитей острые, в середине некоторых звездочек имеется красно-желтые слабые пучочки. В начале искры имеется красно-желтый пучок от прикосновения заготовки к абразивному кругу
Сталь марок 15, 20 — искры светло-желтые, разветвлений и зведочек больше, чем у стали 10, но красно-желтых пучочков в звездочках меньше трех-пяти. В начале имеется пучок от прикосновения заготовки к абразивному кругу
Сталь марок 25, 30 — искры светло-желтые, разветвлений много, густые звездочки, концы нитей тонкие, во многих звездочках имеются красно-желтые крупинки в виде горошинок. В начале искры имеется красно-желтый пучок от прикосновения заготовки к абразивному кругу
Железо Армко (Сталь 10895) — искры светло-желтые прямые без разветвлений с двумя-тремя короткими красными нитями в середине. В начале искры имеется красно-желтый пучок от прикосновения заготовки к абразивному кругу
Сталь 12Х18Н9 — искры светло-желтые, короткие, в небольшом количестве, почти без разветвлений с красно-желтым пучком в конце разветвления и тремя-пятью мелкими красными крупинками на разветвлениях. В начале искры имеется красно-желтый пучок от прикосновения заготовки к абразивному кругу
Ограниченно свариваемые
(стали свариваемые распространенными способами сварки, как правило требуется предварительный подогрев и последующая термообработка)
Сталь 12X13 — искры светло-желтые, короткие, с небольшими пучкообразными разветвлениями, с мелкими красными крупинками. В начале искры имеется красно-желтый пучок от прикосновения заготовки к абразивному кругу
Сталь 12ХНЗА — искры желтые, разветвления более развитые и толще, на концах искр стрелочки, звездочек нет. В начале искры имеется красно-желтый пучок от прикосновения заготовки к абразивному кругу
Сталь 4 — искры светло-желтые, разветвления тоньше, чем нити, и гуще, чем стали Ст2 и СтЗ, звездочек нет. В начале искры имеется красно-желтый пучок от прикосновения заготовки к абразивному кругу
Сталь марок 20ХНМ, 20НЗ — искры желтые, в центре искр выделяется несколько ярких звездочек, на концах искр имеются стрелочки и несколько красных крупинок в звездочках. В начале искры имеется ярко-красный пучок от прикосновения заготовки к абразивному кругу
Сталь марок 4ХС, ЗОХГСА, 35ХГСА — искры светло-желтые, на концах нитей стрелочки, на разветвлениях выделяется несколько светлых звездочек с небольшими светло-красными крупинками в середине. В начале искры имеется светло-красный пучок от прикосновения заготовки к абразивному кругу
Трудносвариваемые стали
(трудносвариваемые стали требуют ограниченное тепловложение при сварке, предварительный/сопутствующий подогрев, последующую термообработку, но даже эти меры не во всех случаях позволяют предотвратить дефекты в сварных швах)
Сталь марок 40ХН, ХНМ — искры светло-желтые, в центре искр выделяются густые звездочки, на концах нитей небольшое количество стрелочек, в некоторых звездочках имеются красные крупинки. В начале искры имеется ярко-красный пучок от прикосновения заготовки к абразивному кругу
Сталь марок 40, 45 — искры светло-желтые, разветвления сильно развиты, на разветвлениях имеются крупные звездочки, в центре которых имеются красно-желтые крупинки. В начале искры имеется светло-красный пучок от прикосновения заготовки к абразивному кругу
Сталь Р9. Первый вид определения — искры светло-малиновые с желто-красным пучком в начале, разветвления простые и редкие с небольшими желто-красными крупинками на концах. В начале искры имеется ярко-красный пучок от прикосновения заготовки к абразивному кругу
Сталь Р9. Второй вид определения искры темно-малиновые, нити с ярким желто-красным пучком в начале, разветвления с крупинками на кончиках, с редкими и мелкими разветвлениями. В начале искры имеется ярко-красный пучок от прикосновения заготовки к абразивному кругу
Сталь Р18. Первый вид определения — искры темно-малиновые с желто-красным пучком в начале, нити прямолинейные, без разветвлений с одной-двумя светло-желтыми крупинками, на концах пучка искры. В начале искры имеется светло-желтый пучок от прикосновения заготовки к абразивному кругу
Сталь Р18. Второй вид определения — искры темно-малиновые с желто-красным пучком в начале, на концах двух-трех нитей небольшие разветвления, с светло-желтыми крупинками на концах пучка. В начале искры имеется ярко-красный пучок от прикосновения заготовки к абразивному кругу
Не применяются для сварных конструкций
Сталь Х12Ф1 — искры желтые, короткие, густые звёздочки, концы нитей острые с отдельными красными крупинками. В начале искры имеется красно-желтый пучок от прикосновения заготовки к абразивному кругу
Сталь автоматная 12 — искры светло-желтые с тонкими разветвлениями и с большим количеством звездочек: на концах нитей стрелочки, а в середине некоторых звездочек слабые красно-желтые пучочки. В начале искры имеется красно-желтый пучок от прикосновения заготовки к абразивному кругу
Сталь марок У8, У10 — искры светло-желтые, разветвлений и звездочек больше и крупнее, чем у стали 15 и 20, с большим количеством красно-желтых пучочков в звездочках. В начале искры имеется красно-желтый пучок от прикосновения заготовки к абразивному кругу
Сталь У12 — искры светло-желтые, крупные густые звездочки, в трех-пяти звездочках имеются красно-желтые пучочки. В начале искры имеется красно-желтый пучок от прикосновения заготовки к абразивному кругу
Сталь 38ХМЮА — искры желтые, на концах нитей стрелочки, а в середине нитей имеются несколько крупных звездочек с небольшими красными крупинками. В начале имеется небольшой светло-красный пучок от прикосновения заготовки к абразивному кругу
Сталь марок X, ХГ, ШХ15, ШХ9 — искры желтые, на разветвлениях большое количество крупных светло-красных звездочек с мелкими желтыми крупинками в середине. В начале искры имеется светло-красный пучок от прикосновения заготовки к абразивному кругу
Сталь 9ХС — искры темно-желтые со светло-красными разветвлениями и большим количеством звездочек с желтыми крупинками в середине. В начале искры от прикосновения заготовки к абразивному кругу получаются ярко-красные пучки с переходом на светло-желтые и светло-красные разветвления
Сталь ЗХ2В8 — искры темно-малиновые, нити длинные с ярким желто-красным пучком в конце нитей; в пучке имеются крупинки со светло-желтыми кончиками, с редкими и мелкими разветвлениями. В начале искры имеется ярко-красно-желтый пучок от прикосновения заготовки к абразивному кругу
Сталь ХВГ — искры темно-малиновые, светлые и яркие разветвления с мелкими отдельными желто-красными пучками и крапинками. На концах коротких и длинных нитей имеются ярко-красные звездочки со светло-желтыми крупинками в середине. В начале искры имеется ярко-красно-желтый пучок от прикосновения заготовки к абразивному кругу
Сталь ХВ5 — искры темно-малиновые, разветвления с желто-красными пучками и крупинках на концах, некоторые нити более светлые и яркие. В начале искры имеется ярко-красно-желтый пучок от прикосновения заготовки к абразивному кругу
Похожие материалы
Конструкционная сталь — Википедия
![]() | Эта статья или раздел описывает ситуацию применительно лишь к одному региону (СССР/Россия), возможно, нарушая при этом правило о взвешенности изложения. Вы можете помочь Википедии, добавив информацию для других стран и регионов. |
Конструкцио́нная сталь — сталь, которая применяется для изготовления различных деталей, механизмов и конструкций в машиностроении и строительстве и обладает определёнными механическими, физическими и химическими свойствами. Конструкционные стали подразделяются на несколько подгрупп.
Качество конструкционных углеродистых сталей[править | править код]
Качество конструкционных углеродистых сталей определяется наличием в стали вредных примесей фосфора (P) и серы (S). Фосфор придаёт стали хладноломкость (хрупкость). Сера — самая вредная примесь — придаёт стали красноломкость. Содержание вредных примесей в стали:
- Обыкновенного качества — P и S — до 0,05 % (маркировка Ст).
- Качественная — P и S — до 0,035 % (маркировка Сталь).
- Высококачественная — P и S — до 0,025 % (маркировка А в конце марки).
- Особовысококачественная — Р и S — до 0,015 % (маркировка Ш в конце марки).
Стали конструкционные углеродистые обыкновенного качества[править | править код]
Широко применяются в строительстве и машиностроении как наиболее дешёвые, технологичные, обладающие необходимыми свойствами при изготовлении конструкций массового назначения. В основном эти стали используют в горячекатанном состоянии без дополнительной термической обработки с ферритно-перлитной структурой.
В зависимости от последующего назначения конструкционные углеродистые стали обыкновенного качества ранее подразделялись на три группы: А, Б, В. В актуальной версии ГОСТ 380-2005 данная классификация отсутствует.
По степени раскисления[править | править код]
Степень раскисления определяется содержанием кремния (Si) в этой стали. По степени раскисления углеродистые стали обыкновенного качества делятся на:
- спокойные (СП) — не менее 0,12 % (Si)
- полуспокойные (ПС) — 0.07-0.12 % (Si)
- кипящие (КП) — не более 0,07 % (Si)
Маркировка[править | править код]
Основные марки конструкционных углеродистых сталей обыкновенного качества:
Ст1кп2; Ст2пс; Ст3Гпс; Ст4-2; … Ст6сп3.
- Ст — показывает, что сталь обыкновенного качества.
- Первая цифра — номер по ГОСТу (от 0 до 6).
- Буква Г после первой цифры — повышенное содержание марганца (Mn) (служит для повышения прокаливаемости стали).
- сп; пс; кп — степень раскисления стали. спокойная, полуспокойная, кипящая. Чем спокойнее сталь, тем более однородной структурой и химическим составом по сечению отливки она обладает.
- Вторая цифра — номер категории стали (от 1 до 6 — чем выше цифра, тем большее количество параметров стали контролируется)
- ). Сталь 1-й категории цифрой не обозначается.
- Тире между цифрами указывает, что заказчик не предъявлял требований к степени раскисления стали.
Применение[править | править код]
Стали углеродистые качественные (улучшаемые)[править | править код]
Качественными углеродистыми сталями являются стали марок: Сталь08; Сталь10; Сталь15 …; Сталь78; Сталь80; Сталь85,
Также к этому классу относятся с повышенным содержанием марганца (Mn — 0.7-1.0 %): Сталь 15Г; 20Г … 65Г, имеющие повышенную прокаливаемость.
Маркировка[править | править код]
- Сталь — слово «Сталь» указывает, что данная углеродистая сталь качественная. (В настоящее время слово «Сталь» не пишется, указывается только индекс и последующие буквы)
- Цифра — указывает на содержание в стали углерода (С) в сотых долях процента.
Применение[править | править код]
Низкоуглеродистые стали марок Сталь08, Сталь08КП, Сталь08ПС относятся к мягким сталям, применяемым чаще всего в отожжённом состоянии для изготовления деталей методом холодной штамповки — глубокой вытяжки. Стали марок Сталь10, Сталь15, Сталь20, Сталь25 обычно используют как цементируемые, а высокоуглеродистые Сталь60 … Сталь85 — для изготовления пружин, рессор, высокопрочной проволоки и других изделий с высокой упругостью и износостойкостью.
Сталь30 … Сталь50 и аналогичные стали с повышенным содержанием марганца Сталь30Г, Сталь40Г, Сталь50Г применяют для изготовления самых разнообразных деталей машин.
Стали повышенной обрабатываемости (автоматные)[править | править код]
К сталям с повышенной обрабатываемостью или автоматным сталям относят стали с высоким содержанием серы и фосфора, а также стали, специально легированные селеном (Se), теллуром (Те) или свинцом (Pb). Указанные элементы способствуют повышению скорости резания, уменьшают усилие резания и изнашиваемость инструмента, улучшают чистоту и размерную точность обработанной поверхности, облегчают отвод стружки из зоны резания и т. д. Эти стали используют в массовом производстве для изготовления деталей на станках-автоматах.
Стали с повышенным содержанием серы и фосфора обладают пониженными механическими свойствами и их используют для изготовления малонагруженных неответственных деталей (например, метизов).
По мере развития технологий лазерной резки были разработаны специальные конструкционные стали для лазерной резки. Их отличительной особенностью является более предсказуемое поведение листа после резки (пониженный уровень внутренних напряжений в металле)[1].
Маркировка[править | править код]
В начале обозначения марки автоматной стали всегда стоит буква «А», например А12, А20, А35.
Легированные конструкционные стали применяются для наиболее ответственных и тяжелонагруженных деталей машин. Практически всегда эти детали подвергаются окончательной термической обработке — закалке с последующим высоким отпуском в районе 550—680 °C (улучшение), что обеспечивает наиболее высокую конструктивную прочность.
Легирующие элементы — химические элементы, которые вносят в состав конструкционных сталей для придания им требуемых свойств. Ведущая роль легирующих элементов в конструкционных сталях заключается и в существенном повышении их прокаливаемости. Основными легирующими элементами этой группы сталей являются хром (Cr), марганец (Mn), никель (Ni), молибден (Mo), ванадий (V) и бор (В). Содержание углерода (С) в легированных конструкционных сталях — в пределах 0.25-0.50 %.
Маркировка[править | править код]
- Две цифры в начале маркировки указывают на конструкционные стали. Это содержание в стали углерода в сотых долях процента.
- Буква без цифры — определённый легирующий элемент с содержанием в стали менее 1 %.(А — азот, Р — бор, Ф — ванадий, Г — марганец, Д — медь, К — кобальт, М — молибден, Н — никель, С — кремний, Х — хром, П — фосфор, Ч — редкоземельные металлы, В — вольфрам, Т — титан, Ю — алюминий, Б — ниобий)
- Буква и цифра после неё — определённый легирующий элемент с содержанием в процентах (цифра).
- Буква А в конце маркировки — указывает на высококачественную сталь.
Например 38Х2Н5МА — это среднелегированная высококачественная хромоникелевая конструкционная сталь. Химический состав: углерод — около 0,38 %; хром — около 2 %; никель — около 5 %; молибден — около 1 %.
Стали конструкционные теплоустойчивые[править | править код]
К теплоустойчивым конструкционным относятся стали, используемые в энергетическом машиностроении для изготовления котлов, сосудов, паронагревателей, паропроводов, а также в других отраслях промышленности для работы при повышенных температурах. Рабочие температуры теплоустойчивых сталей достигают 600—650 °C, причём детали из них должны работать без замены длительное время (до 10000-20000 ч.).
При давлениях 6 МПа и температурах до 400 °C используются углеродистые котельные стали (12К, 15К, 18К, 20К). Для деталей энергоблоков, работающих при давлении до 25.5 МПа и температурой до 585 °C применяются стали, легированные хромом, молибденом, ванадием. Содержание углерода 0.08-0.27 %. Термообработка этих сталей заключается в закалке или нормализации с обязательным высоким отпуском.
Стали конструкционные подшипниковые[править | править код]
Особенностью эксплуатации подшипников являются высокие локальные нагрузки. В связи с этим к чистоте стали предъявляются чрезвычайно высокие требования, особенно по неметаллическим включениям карбидной неоднородности. Обеспечение высокой статической грузоподъёмности достигается применением в качестве материала для подшипников заэвтектоидных легированных хромом сталей, обработанных на высокую твёрдость.
Маркировка[править | править код]
ШХ9, ШХ15.
- Содержание углерода — около 1 %;
- Содержание хрома в десятых долях процента (например: ШХ15 — хром — около 1,5 %)
Стали конструкционные рессорно-пружинные[править | править код]
14ХН4А, 38Х2Н5М, 20ХН3А.
Общее требование, предъявляемое к рессорно-пружинным сталям, — обеспечение высокого сопротивления малым пластическим деформациям (предел упругости) и релаксационной стойкости (сопротивление релаксации напряжений). Эти характеристики обеспечивают точность и надёжность работы пружин и постоянство во времени таких эксплуатационных свойств, как крутящий момент, силовые параметры. Пружинные стали в виде проволоки и ленты упрочняют холодной пластической деформацией и закалкой на мартенсит с последующим отпуском. Готовые пружины подвергают стабилизирующему отпуску.
- ↑ Лазерная резка (рус.). Информационный сайт «О сварке». Дата обращения 27 сентября 2013.
- Стали и сплавы. Марочник. Справ. изд./ В. Г. Сорокин и др. Науч. С77. В. Г. Сорокин, М. А. Гервасьев — М.: «Интермет Инжиниринг», 2001 — 608с, илл. ISBN 5-89594-056-0
1. ГОСТ 380-2005
Поиск сталей, сплавов, ферросплавов и чугунов
Поиск сталей, сплавов, ферросплавов и чугунов — Марочник сталей и сплавовПоиск сталей, сплавов, ферросплавов и чугунов
Поиск по химическому составу материалаОбласть поиска все материалы ферросплав сталь конструкционная сталь инструментальная сталь для отливок сталь, сплав жаропрочные сталь коррозионно-стойкая сталь специального назначения сталь электротехническая сплав прецизионный чугун алюминий, сплав алюминия бронза золото, сплав золота латунь магний, сплав магния медь, сплав меди никель, сплав никеля олово, сплав олова платина, сплав платины палладий, сплав палладия свинец, сплав свинца серебро, сплав серебра титан, сплав титана цинк, сплав цинка порошковая металлургия прочие металлы и сплавы материалы для сварки и пайки |
Поиск по механическим свойствам материала
Область поиска все материалы сталь конструкционная сталь инструментальная сталь для отливок сталь, сплав жаропрочные сталь коррозионно-стойкая сталь специального назначения сталь электротехническая сплав прецизионный чугун алюминий, сплав алюминия бронза золото, сплав золота латунь магний, сплав магния медь, сплав меди никель, сплав никеля олово, сплав олова свинец, сплав свинца серебро, сплав серебра титан, сплав титана цинк, сплав цинка |
Поиск по физическим свойствам материала
Область поиска все материалы сталь конструкционная сталь инструментальная сталь для отливок сталь, сплав жаропрочные сталь коррозионно-стойкая сталь специального назначения сталь электротехническая сплав прецизионный чугун алюминий, сплав алюминия бронза золото, сплав золота латунь магний, сплав магния медь, сплав меди никель, сплав никеля олово, сплав олова свинец, сплав свинца серебро, сплав серебра титан, сплав титана цинк, сплав цинка |
Марочник стали и сплавов. К о н т а к т н а я и н ф о р м а ц и я © 2003 — 2020 Контент сайта защищен Авторским свидетельством № 7533 от 8.05.2003 г. При использовании информации сайта гиперссылка на «Марочник стали и сплавов » (splav-kharkov.com) обязательна Администрация сайта не несет ответственность за достоверность данных Раньше данный сайт располагался по адресу: splav.kharkov.com |
определение, классификация, химический состав и применение
Как часто мы слышим слово «сталь». И произносят его не только профессионалы в области металлургического производства, но и обыватели. Без стали не обходится ни одна прочная конструкция. По сути, когда мы говорим о чем-то металлическом, то подразумеваем изделие из стали. Узнаем, из чего она состоит, и как ее классифицируют.
Определение
Сталь – это самый, пожалуй, популярный сплав, основой которого являются железо и углерод. Причем доля последнего колеблется от 0,1 до 2,14 %, а первый не может быть ниже 45 %. Простота производства и доступность сырья имеют определяющее значение при распространении этого металла на все сферы деятельности человека.
Основные характеристики материала меняются в зависимости от его химического состава. Определение стали, как сплава, состоящего из двух компонентов, железа и углерода, нельзя назвать полным. В него может входить, например, хром — для придания жаропрочности, а никель, чтобы обеспечить устойчивость к коррозии.
Обязательные компоненты материала способствуют появлению дополнительных преимуществ. Так, железо делает сплав ковким и легко деформируемым при определенных условиях, а углерод – прочность и твердость одновременно с хрупкостью. Именно поэтому его доля так мала в общей массе стали. Определение способа производства сплава привело к содержанию в нем марганца в количестве 1 % и кремния – 0,4 %. Существует целый ряд примесей, которые появляются при плавлении металла и от которых пытаются избавиться. Наряду с фосфором и серой, кислород и азот также ухудшают свойства материала, делая его менее прочным и изменяя пластичность.
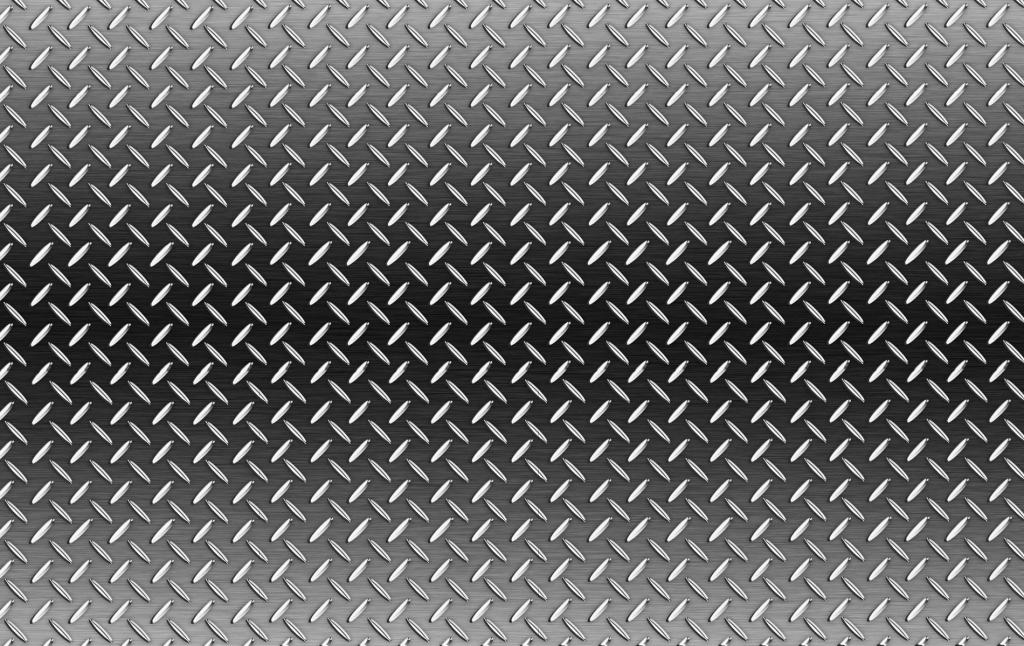
Классификация
Определение стали как металла с определенным набором характеристик, конечно, не вызывает сомнений. Однако именно ее состав позволяет классифицировать материал по нескольким направлениям. Так, например, различают металлы по следующим признакам:
- по химическому;
- по структурному;
- по качеству;
- по назначению;
- по степени раскисления;
- по твердости;
- по свариваемости стали.
Определение стали, маркировка и все ее характеристики будут описаны далее.
Маркировка
К сожалению, не существует мирового обозначения сталей, что значительно затрудняет торговые операции между странами. В России определена буквенно-цифровая система. Буквами обозначают название элементов и способ раскисления, а цифрами – их количество.
Химический состав
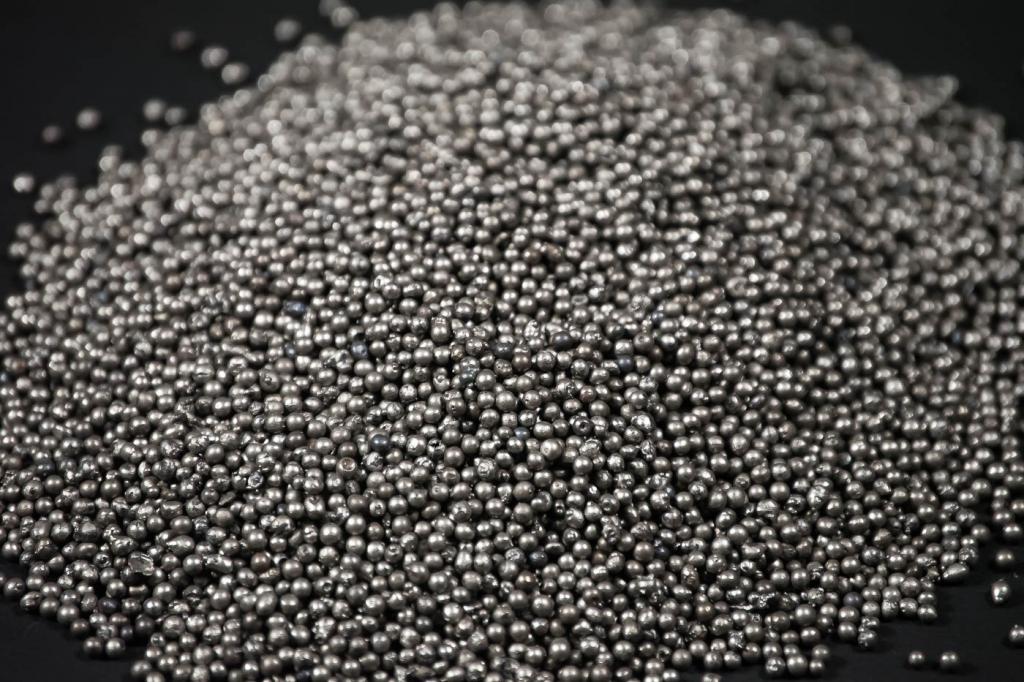
Существует два способа деления стали по химическому составу. Определение, которое дают современные учебники, позволяет различать углеродистый и легированный материал.
Первый признак определяет сталь как малоуглеродистую, среднеуглеродистую и высокоуглеродистую, а второй – низколегированную, среднелегированную и высоколегированную. Малоуглеродистым называют металл, который может включать согласно ГОСТу 3080-2005, помимо железа, следующие составляющие:
- Углерод – до 0,2 %. Он способствует термическому упрочнению, за счет которого временное сопротивление и твердость повышается в два раза.
- Марганец в количестве до 0,8 % активно вступает с кислородом в химическую связь и не допускает образование оксида железа. Металл лучше выдерживает динамические нагрузки и более податлив термическому упрочнению.
- Кремний – до 0,35 %. С помощью него становятся лучше механические характеристики, такие как вязкость, прочность, свариваемость.
По ГОСТу определение стали в качестве малоуглеродистой дают металлу, который содержит, кроме полезных, целый ряд вредных примесей в следующем количестве. Это:
- Фосфор – до 0,08 % отвечает за появление хладноломкости, ухудшает выносливость и прочность. Снижает ударную вязкость металла.
- Сера – до 0,06 %. Она усложняет обработку металла давлением, увеличивает отпускную хрупкость.
- Азот. Снижает технологические и прочностные свойства сплава.
- Кислород. Снижает прочность и препятствует обработке инструментов при резке.
Следует отметить, что низко- или малоуглеродистые стали отличаются особой мягкостью и пластичностью. Они хорошо деформируются как в горячем, так и в холодном состоянии.
Определение стали среднеуглеродистой так же, как и ее состав, конечно, отличаются от материала, описанного выше. И самым большим различием является количество углерода, которое колеблется от 0,2 до 0,45 %. Такой металл имеет небольшую вязкость и пластичность наряду с отличными свойствами по прочности. Из среднеуглеродистой стали обычно изготавливают детали, применяемые при обычных силовых нагрузках.
Если же содержание углерода составляет свыше 0,5 %, то такая сталь называется высокоуглеродистой. Она имеет повышенную твердость, сниженную вязкость, пластичность, используется при штамповке инструмента и деталей методом горячего и холодного деформирования.
Помимо выявления имеющегося в стали углерода, определение характеристик материала возможно через находящиеся в ней дополнительные примеси. Если в металл, кроме обычных элементов, целенаправленно вводят хром, никель, медь, ванадий, титан, азот в химически связанном состоянии, то его называют легированным. Такие добавки снижают риск хрупкого разрушения, увеличивают коррозионную стойкость и прочность. Их количество и обозначает степень легирования стали:
- низколегированная – имеет до 2,5 % легирующих добавок;
- среднелегированная – от 2,5 до 10 %;
- высоколегированная – до 50 %.
Что это значит? Например, повышение каких-либо свойств стали обеспечиваться следующим образом:
- Добавление хрома. Позитивно действует на механические характеристики уже в количестве 2 % от общего объема.
- Введение никеля от 1 до 5 % увеличивает температурный запас вязкости. И снижает хладноломкость.
- Марганец работает так же, как и никель, хотя значительно дешевле. Однако способствует повышению чувствительности металла к перегреву.
- Вольфрам — карбидобразующая добавка, обеспечивающая высокую твердость. Поскольку препятствует росту зерна при нагреве.
- Молибден – дорогостоящая добавка. Которая повышает теплостойкость быстрорежущих сталей.
- Кремний. Увеличивает кислотостойкость, упругость, окалиностойкость.
- Титан. Может способствовать образованию мелкозернистой структуру, если сочетается с хромом и марганцем.
- Медь. Повышает антикоррозионные свойства.
- Алюминий. Увеличивает жаростойкость, окалийность, ударную вязкость.
Структура
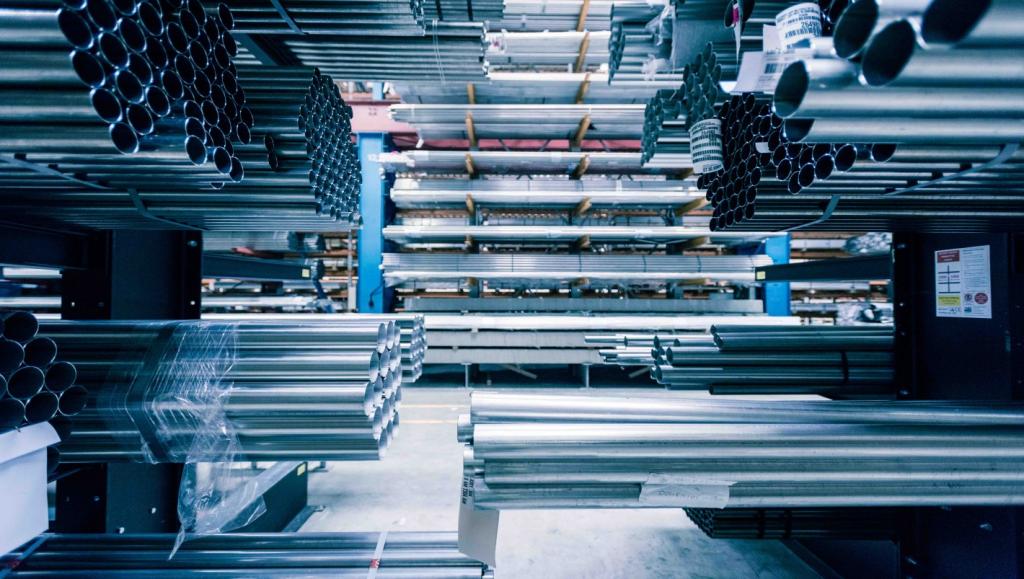
Определение состава стали было бы неполным без изучения ее структуры. Однако этот признак непостоянен, и может зависеть от целого ряда факторов, таких как: режим термообработки, скорость охлаждения, степень легирования. Согласно правилам структуру стали следует определять после отжига или нормализации. После отжига металл разделяют на:
- доэвтектоидную структуру – с избыточным ферритом;
- эвтектоидную, которая состоит из перлита;
- заэвтектоидную – со вторичными карбидами;
- ледебуритную – с первичными карбидами;
- аустенитную – с гранецентрированной кристаллической решеткой;
- ферритную – с кубической объемоцентрированной решеткой.
Определение класса стали возможно после нормализации. Под ней понимают вид термической обработки, включающий в себя нагрев, выдержку и последующее охлаждение. Здесь различают перлитный, аустенитный и ферритный классы.
Качество
Определение типов стало по качеству возможным по четырем направлениям. Это:
- Обыкновенного качества – это стали с содержанием углерода до 0,6 %, которые выплавляют в мартеновских печах или в конвертерах с использованием кислорода. Они считаются наиболее дешевыми и уступают по характеристикам металлам других групп. Примером таких сталей являются Ст0, Ст3сп, Ст5кп.
- Качественные. Яркими представителями этого типа являются стали Ст08кп, Ст10пс, Ст20. Выплавляются они с применением тех же печей, но с более высокими требованиями к шихте и процессам производства.
- Высококачественные стали плавят в электропечах, что гарантирует увеличение чистоты материала по неметаллическим включениям, то есть улучшение механических свойств. К таким материалам относят Ст20А, Ст15Х2МА.
- Особовысококачественные — изготавливают по методу специальной металлургии. Их подвергают электрошлаковому переплаву, который обеспечивает очистку от сульфидов и оксидов. К сталям этого типа относят Ст18ХГ-Ш, Ст20ХГНТР-Ш.
Конструкционные стали
Это, пожалуй, самый простой и понятный для обывателя признак. Различают конструкционные, инструментальные и специального назначения стали. Конструкционные принято разделять на:
- Строительные – это углеродистые стали обыкновенного качества и представители низколегированного ряда. К ним предъявляется несколько требований, основное из которых – свариваемость на достаточно высоком уровне. Примером служат СтС255, СтС345Т, СтС390К, СтС440Д.
- Из цементируемых делают изделия, которые работают в условиях поверхностного износа и параллельно испытывают динамические нагрузки. К ним относят малоуглеродистые стали Ст15, Ст20, Ст25 и некоторые легированные: Ст15Х, Ст20Х, Ст15ХФ, Ст20ХН, Ст12ХНЗА, Ст18Х2Н4ВА, Ст18Х2Н4МА, Ст18ХГТ, Ст20ХГР, Ст30ХГТ.
- Для холодной штамповки используют прокат листвой из качественных низкоуглеродистых образцов. Таких как Ст08Ю, Ст08пс, Ст08кп.
- Улучшаемые стали, которые подвергаются улучшению в процессе закалки и высокого отпуска. Это среднеуглеродистые (Ст35, Ст40, Ст45, Ст50), хромистые (Ст40Х, Ст45Х, Ст50Х, Ст30ХРА, Ст40ХР) стали, а также хромокремниемарганцевые, хромоникельмолибденовые и хромоникелевые.
- Рессорно-пружинные имеют упругие свойства и сохраняют их длительное время, так как имеют высокую степень сопротивляемости к усталости и разрушению. Это углеродистые представители Ст65, Ст70 и стали легированные (Ст60С2, Ст50ХГС, Ст60С2ХФА, Ст55ХГР).
- Высокопрочные образцы – те, которые имеют прочность в два раза большую, чем иные конструкционные стали, достигаемую термической обработкой и химическим составом. В основной массе это легированные среднеуглеродистые стали, например, Ст30ХГСН2А, Ст40ХН2МА, Ст30ХГСА, Ст38ХН3МА, СтОЗН18К9М5Т, Ст04ХИН9М2Д2ТЮ.
- Шарикоподшипниковые стали отличаются особой выносливостью, высокой степенью износоустойчивости и прочности. К ним обязательно предъявляются требования по отсутствию разного рода включений. К этим образцам относятся высокоуглеродистые стали с содержанием хрома в составе (СтШХ9, СтШХ15).
- Автоматные стали определение имеют следующее. Это образцы для использования при изготовлении неответственных изделий, таких как болты, гайки, винты. Такие запасные части обычно обрабатываются резанием. Поэтому основной задачей является повышение обрабатываемости деталей, чего добиваются введением в материал теллура, селена, серы и свинца. Такие добавки способствуют образованию при обработке ломкой и короткой стружки и уменьшению трения. Основные представители автоматных сталей обозначаются так: СтА12, СтА20, СтА30, СтАС11, СтАС40.
- К коррозионностойким относят легированные стали с содержанием хрома около 12 %, поскольку он образует оксидную пленку на поверхности, препятствующую возникновению коррозии. Представителями этих сплавов являются Ст12Х13, Ст20Х17Н2, Ст20Х13, Ст30Х13, Ст95Х18, Ст15Х28, Ст12Х18НЮТ,
- Износостойкие образцы применяют в изделиях, которые работают при абразивном трении, ударах и сильном давлении. Примером могут служить детали железнодорожных путей, дробильных и гусеничных машин, такая как Ст110Г13Л.
- Жаропрочные стали могут работать при высоком нагреве. Их используют при изготовлении труб, газо- и паротурбинных запчастей. Это в основном высоколегированные малоуглеродистые образцы, имеющие обязательно в составе никель, которые могут содержать добавки в виде молибдена, нобия, титана, вольфрама, бора. Примером могут являться Ст15ХМ, Ст25Х2М1Ф, Ст20ХЗМВФ, Ст40ХЮС2М, Ст12Х18Н9Т, СтХН62МВКЮ.
- Жаростойкие отличаются особой стойкостью против химических разрушений в воздухе, газовых и печных, окислительных и науглероживающих средах, но проявляют ползучесть при серьезных нагрузках. Представителями этого типа являются Ст15Х5, Ст15Х6СМ, Ст40Х9С2, Ст20Х20Н14С2.
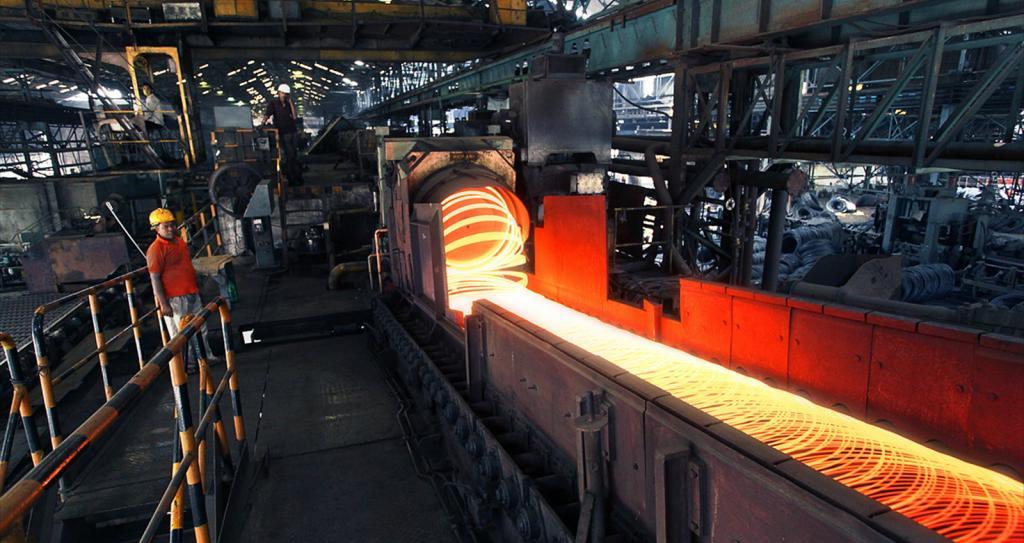
Стали инструментального назначения
В этой группе сплавы делят на штамповые, для режущих и измерительных инструментов. Стали для штампов бывают двух видов.
- Материал для холодного деформирования должен иметь высокую степень твердости, прочности, износостойкости, теплостойкости. Но иметь достаточную вязкость (СтХ12Ф1, СтХ12М, СтХ6ВФ, Ст6Х5ВМФС).
- Материал для горячего деформирования отличается хорошей прочностью и вязкостью. Наряду с износостойкостью и окалиностойкостью (Ст5ХНМ, Ст5ХНВ, Ст4ХЗВМФ, Ст4Х5В2ФС).
Стали для измерительных инструментов, кроме износостойкости и твердости, должны отличаться постоянством размеров и легко шлифоваться. Из этих сплавов изготавливаются калибры, скобы, шаблоны, линейки, шкалы, плитки. Примером могут быть сплавы СтУ8, Ст12Х1, СтХВГ, СтХ12Ф1.
Определение групп сталей для режущих инструментов осуществляется достаточно легко. Такие сплавы должны обладать режущей способностью и высокой твердостью продолжительное время, даже если подвергаются нагреву. К ним относят углеродистые и легированные инструментальные, а также быстрорежущие стали. Здесь можно назвать следующих ярких представителей: СтУ7, СтУ13А, Ст9ХС, СтХВГ, СтР6М5, СтРЮК5Ф5.
Раскисление сплава
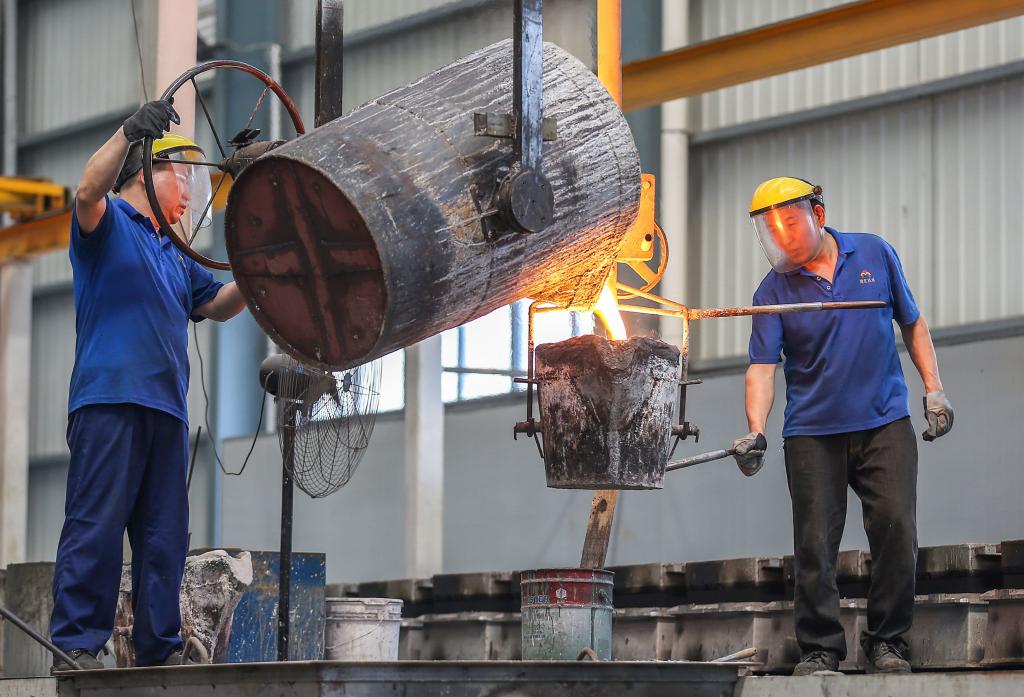
Определение стали по степени раскисления подразумевает три ее вида: спокойная, полуспокойная и кипящая. Само же понятие обозначает удаление кислорода из жидкого сплава.
У спокойной стали при затвердевании газы почти не выделяются. Так происходит из-за полного удаления кислорода и образования сверху слитка усадочной раковины, которую затем обрезают.
У полуспокойной стали газы выделяются частично, то есть больше, чем в спокойных, но меньше, чем в кипящих. Здесь отсутствует раковина, как в предыдущем случае, но вверху образуются пузыри.
Кипящие сплавы выделяют большое количество газа при затвердевании, а в поперечном сечении достаточно просто заметить разницу химического состава между верхним и нижним слоями.
Твердость
Это понятие обозначает способность материала сопротивляться более твердому, проникающему в него. Определение твердости стало возможно с использованием трех методов: Л. Бринеля, М. Роквелла, О. Викерса.
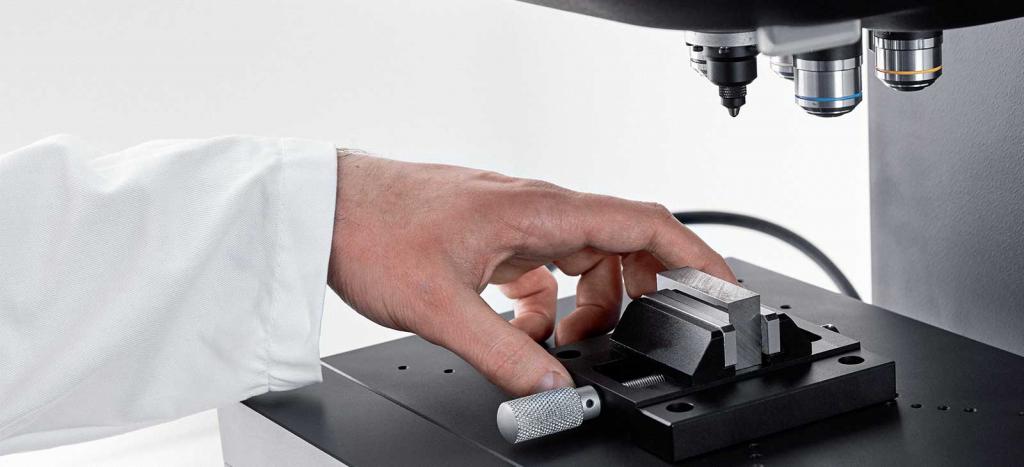
Согласно способу Бринеля закаленный стальной шарик вдавливают в отшлифованную поверхность образца. Изучая диаметр отпечатка, определяют твердость.
Метод определения твердости стали по Роквеллу. Он основан на подсчете глубины проникновения наконечника в виде алмазного конуса с углом в 120 градусов.
По Викерсу в испытываемый образец вдавливается алмазная четырехгранная пирамида. С углом 136 градусов у противоположных граней.
Можно ли определить марку стали без химического анализа? Специалисты в области металловедения способны узнать марку стали по искре. Определение составляющих металла возможно при его обработке. Так, например:
- Сталь ХВГ имеет темно-малиновые искры с желто-красными крапинками и пучками. На концах разветвленных нитей появляются ярко-красные звездочки с желтыми крупками в середине.
- Сталь Р18 также определяется по темно-малиновым искрам с желтыми и красными пучками в начале, однако нити прямые и не имеют разветвлений. На концах пучков имеются искры с одной или двумя светло-желтыми крупинками.
- Стали марок ХГ, Х, ШХ15, ШХ9 имеют желтые искры со светлыми звездочками. И красными крупинками на разветвлениях.
- Сталь У12Ф отличается светло-желтыми искрами с густыми и крупными звездами. С несколькими красно-желтыми пучками.
- Стали 15 и 20 имеют светлые желтые искры, много разветвлений и звезд. Но мало пучков.
Определение стали по искре является достаточно точным методом для специалистов. Однако обыватели не могут дать характеристику металлу, изучив только цвет искры.
Свариваемость
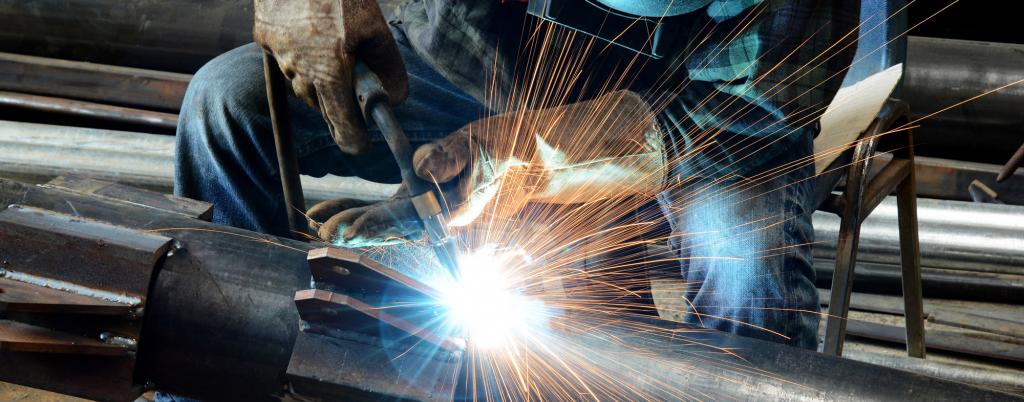
Свойство металлов образовывать соединение при определенном воздействии называется свариваемостью сталей. Определение данного показателя возможно после того, как будет выявлено содержание железа и углерода.
Считается, что хорошо соединяются посредством сварки низкоуглеродистые стали. Когда содержание углерода превышает 0,45 %, свариваемость ухудшается и становится наиболее плохой при большом содержании углерода. Это происходит и потому, что повышается неоднородность материала, а на границах зерен выделяются сульфидные включения, которые приводят к образованию трещин и увеличению внутреннего напряжения.
Также действуют и легирующие компоненты, ухудшая соединение. Самыми неблагоприятными для сварки называют такие химические элементы как хром, молибден, марганец, кремний, ванадий, фосфор.
Однако соблюдение технологии при работе с низколегированными сталями обеспечивает хороший процент свариваемости без применения специальных мероприятий. Определение свариваемости возможно после оценки ряда важных качеств материала, в числе которых:
- Скорость охлаждения.
- Химический состав.
- Вид первичной кристаллизации и структурных изменений при сварке.
- Возможность металла образовывать трещины.
- Склонность материала к возникновению закалочных формирований.