Лакокрасочные покрытия металлов — Цветные металлы
Лакокрасочные покрытия металлов
Категория:
Цветные металлы
Лакокрасочные покрытия металлов
Лакокрасочные покрытия получают путем нанесения на детали лакокрасочных материалов; их широко применяют для предохранения летательных аппаратов и двигателей от коррозии, для улучшения аэродинамических свойств поверхности, а также в Целях маскировки.
После нанесения на покрываемую поверхность лакокрасочные материалы высыхают и образуют плотную пленку, хорошо сцепляющуюся с покрытой поверхностью, достаточно прочную и эластичную, сохраняющую связь с деталью практически при всех изменениях внешних условий в процессе хранения, транспортировки и эксплуатации.
Лакокрасочные материалы классифицируются по характеру процесса пленкообразования и по виду.
Рис. 1. Схема защиты стали анодным (а) и катодным (б) покрытиями
По характеру процесса пленкообразования, или высыхания, все лакокрасочные материалы подразделяются на две группы-материалы на основе растительных масел и материалы на основе нитроцеллюлозы и смол.
1. Материалы на основе растительных масел
Образование пленки у этих материалов происходит в результате длительного процесса физико-химического изменения растительного масла под действием воздуха, света и температуры. Происходящее при этом присоединение кислорода воздуха к молекулам масла сообщает лакокрасочной пленке высокую вязкость и достаточную прочность.
2. Материалы на основе нитроцеллюлозы и смол
Быстровысыхающие лакокрасочные материалы изготовляются на основе нитроцеллюлозы, глифталевой, перхлорвиниловой и других смол. Образование пленок у этих материалов происходит за счет испарения растворителей из жидкого слоя лака или краски. Оставшаяся при этом нитроцеллюлоза или смола образует пленку с необходимыми защитными свойствами.
По виду лакокрасочные материалы подразделяются на четыре группы:
1. Грунт, предназначающийся для непосредственной защиты изделия от коррозии и обеспечения прочной связи основной лакокрасочной пленки с поверхностью изделия.
2. Шпаклевка, служащая для выравнивания покрываемой поверхности.
3. Краска, применяемая для получения основного слоя покрытия, защищающего деталь от внешней среды.
4. Лак, используемый для получения последнего, отделочного слоя покрытия, придающего поверхности детали гладкость и хорошую обтекаемость.
На рис. 2 представлен разрез полного лакокрасочного покрытия, включающего все описанные слои.
Рис. 2 Схема разреза полного лакокрасочного покрытия
Пленкообразователи служат основой лакокрасочных материалов, из них образуются защитные пленки лакокрасочного подпития’. В качестве пленкообразователей применяются растительные масла, эфиры целлюлозы и смолы.
Из растительных масел применяются древесное (тунговое), льняное, конопляное, подсолнечное и другие. Основным качеством этих масел является способность их высыхать, характеризуемая йодным числом, показывающим ненасыщенность масла и, следовательно, способность его окисляться и высыхать. Йодным числом называется число граммов иода, присоединяющегося к 100 г масла. У высыхающего льняного масла оно равно 190, а у невысыхающего касторового —всего лишь 85.
Для лакокрасочных материалов применяют не сами масла, а олифы, представляющие собой масла, уплотненные (частично окисленные) выдержкой при повышенной температуре и, следовательно, более густые. Кроме того, в олифу вводят ускорители сушки.
Ускорители сушки (сиккативы) представляют собой вещества, каталитически ускоряющие процесс высыхания масел. Они выполняют роль передатчиков кислорода. В качестве сиккативов используются высшие окислы кобальта, марганца и свинца.
Льняное масло без сиккатива высыхает через 70 час, то же масло со свинцовым сиккативом высыхает через 21 час, с марганцевым — через 4 час, а с кобальтовым — через 2,5 час.
Нитроцеллюлоза, а также глифталевая, перхлорвиниловая, эпоксидная и кремнийорганическая смолы также являются плен-кообразователями. Они образуют прочные и стойкие в различных средах защитные пленки. Высыхание и отвердевание их происходит вследствие испарения растворителя. Поэтому введение в них ускорителей сушки — сиккативов не требуется.
Пигменты и красители вводятся в лакокрасочные материалы для увеличения прочности и защитной способности пленки, а также для придания ей определенной окраски. Красящие вещества, не растворяющиеся в связующем, называются пигментами, растворяющиеся — красителями.
Пигменты представляют собой тонко размолотые минеральные вещества.
По цвету пигменты можно разделить на две группы:
1. Ахроматические пигменты: белые, представляющие собой в основном различные белила — цинковые, свинцовые, титановые; серые — алюминиевая пудра, цинкоЬая пыль; черные — сажа, жженая кость.
2. Хроматические пигменты: желтые — охра, цинковый и свинцовый крон; красные — свинцовый и железный сурик, киноварь и мумия; зеленые — окись хрома, медянка; синие — уль рамарин, берлинская лазурь.
Пластификаторы представляют собой вещества, вводимые нитроцеллюлозные лаки для сохранения эластичности пленки q течением времени, предупреждения отслаивания ее от поверхно сти металла, растрескивания, морщения и для понижения во пламеняемости пленки. Предполагается, что пластификатор внедряясь между макромолекулами нитроцеллюлозы, облегчает скольжение их друг относительно друга. В качестве пластифика торов применяются фталаты (эфиры фталевой кислоты), фос фаты (эфиры фосфорной кислоты) и касторовое масло.
Наполнители представляют собой тонко размолотые мел, тальк, каолин и другие порошки, вводимые в грунты и шпаклев ки для придания им соответствующих химических и физико-ме ханических свойств.
Растворители представляют собой органические летучие жид кости, применяемые для растворения пленкообразователей, улетучивающиеся в процессе образования пленки.
До недавнего времени не было общепринятой классификации и системы обозначения лакокрасочных материалов; по этой причине их названия носят случайный характер. В настоящее время ГОСТ 9825—61 предусмотрена единая классификация и маркировка лакокрасочных материалов. Обозначения лакокрасочных материалов определяются основной смолой или эфиром целлюлозы, введенными в состав пленкообразующего вещества и группой, к которой отнесен данный лакокрасочный материал.
Для смол, эфиров целлюлозы и масел приняты обозначения, главные из которых приведены ниже: битумы — БТ; глифтали — ГФ; пентафтали — ПФ; фенольные — ФЛ; меламинные — МЛ; кремнийорганические — КО; эпоксидные — ЭП; перхлорвинило-вые — ХВ; нитроцеллюлоза — НЦ; ацетилцеллюлоза — АЦ; масла растительные — МА.
По назначению лакокрасочные материалы делятся на восемь групп, обозначенных в таблице 38.
Обозначение (марка) лаков, грунтовок и шпаклевок состоит из пяти групп знаков, следующих одна за другой слева направо.
Первая группа определяет вид лакокрасочного материала, например: «лак», «эмаль», «грунтовка», «шпаклевка».
Вторая группа определяет основную смолу, входящую в состав пленкообразующего вещества. Между второй и третьей группой знаков ставится тире; третья группа определяет преимущественное значение материала и обозначается цифрой согласно таблице 38.
Четвертая группа определяет порядковый номер, присвоенный данному лакокрасочному материалу в группе, к которой он отнесен.
Пятая группа — относится в основном к эмалям и определяет их цвет — «красная», «синяя» и т. п.
Ниже приведены примеры обозначения лаков, эмалей и грунтовок.
Грунтовка коричневая на основе фенолформальдегидной смолы: грунтовка ФЛ—013 коричневая.
Эмаль голубая нитроцеллюлозная для внутренних работ: эмаль НЦ—25 голубая.
Лак глифталевый электроизоляционный: лак ГФ—95.
Обозначения масляных красок также состоят из пяти групп знаков, например: краска МА—11 коричневая, что означает — краска масляная для наружных (1) работ; (для внутренних работ первая цифра правее тире — 2). Для красок часто вместо слова «краска» указывается пигмент, например «белила цинковые», «охра» и т. п.
Основными лакокрасочными материалами, применяемыми для покрытия летательных аппаратов и двигателей, наземных транспортных средств, наземного оборудования и конструкций, являются грунты, шпаклевки, краски, эмали и лаки.
Грунты предназначаются для нанесения первого слоя лакокрасочного покрытия и могут изготавливаться на основе растительных масел, смол или нитроцеллюлозы.
Наряду с этим в качестве грунта под лакокрасочное покры тие в ряде случаев используются неметаллические неорганиче ские покрытия, например фосфатные на стали и окисные на алю минии.
Грунты для металлов делятся на пять групп: изолирующие; с пигментами основного характера; пассивирующие; протекторные и фосфатирующие.
Изолирующие грунты изготовляются на основе инертных пигментов. К ним относятся, например, грунты с железным суриком. Для покрытия дюралюминиевых и магниевых деталей применяется лаковый желтый грунт АЛГ-1 ‘) на основе масляного лака и цинкового крона.
Для стальных деталей применяется глифталеЕый коричневый грунт № 138 на основе глифталевого лака и железного сурика или свинцового крона. Покрытия этим грунтом отличаются хорошими антикоррозионными свойствами, хорошей адгезией, эластичностью и механической прочностью.
Для деталей из легких сплавов и дерева применяются нитро-грунты, состоящие из нитроцеллюлозы, смолы, пластификаторов, пигментов и растворителей. Для легких сплавов используются грунты АГ-10с и АГ-ЗА, для деталей из дерева — желтый грунт дд-пз.
Грунт с пигментами основного характера (свинцовый сурик, цинковые белила) отличается повышенной водостойкостью в результате образования сложных комплексных соединений при взаимодействии пигмента с пленкообразователем.
Пассивирующие грунты отличаются пассивирующими свойствами и содержат хроматы металлов: цинковый крон, хромат свинца и другие.
Протекторные грунты включают порошкообразный металлический пигмент, имеющий более низкий электродный потенциал по сравнению с покрываемым металлом. Примером таких грунтов могут служить цинковые протекторные грунты ПС.
Фосфатирующие грунты (ФХЛ) содержат хромовый ангидрид и фосфорную кислоту, способные фосфатировать поверхность стальных деталей, улучшать адгезию и защиту от коррозии.
Шпаклевка наносится на слой грунта до полного выравнивания поверхности. По составу шпаклевки могут быть масляные (лаковые) и нитрошпаклевки.
Шпаклевка представляет собой густую пасту, состоящую примерно из 80% пигментов и наполнителей (железный сурик, цинковые белила, охра, мел и другие), затертых на различных пленкообразующих веществах.
Для покрытия по грунту № 138 наружных поверхностей применяется шпаклевка ЛШ-1.
Выравнивание и сплошное покрытие поверхностей деталей из легких сплавов по грунту АЛГ-1 осуществляется коричневой шпаклевкой № 175 на глифталевом лаке.
Деревянные детали покрываются желто-зеленой нитрошпак-левкой АШ-30, содержащей 7% нитроцеллюлозы, 5% смолы, 45о/0 пигмента, небольшое количество амилацетата в качестве растворителя и остальное наполнитель. Расход ее до 300 г/м2.
Эмали и краски предназначаются для нанесения основного слоя лакокрасочного покрытия. Краски представляют собой суспензии мелкорастертых пигментов в пленкообразователе. Эмали или эмалевые краски в отличие от обычных красок при высыхании образуют твердую блестящую пленку с хорошим лаковым глянцем, напоминающим эмали ‘).
По эксплуатационной стойкости краски и эмали подразделяются на атмосферостойкие, химически стойкие, термостойкие и жаростойкие.
Атмосферостойкими являются масляные краски 4БО (ГОСТ 5786—51) защитного цвета, приготовленная на олифе, а также зеленая масляная эмаль А24г, светло-коричневая А21 и другие. Высокой атмосферостойкостью отличаются также эмали на основе перхлорвиниловых материалов, например защитная эмаль ПХВ-715Т серая, голубая, коричневая и другие.
Химически стойкие предназначаются для эксплуатации в кислотах, щелочах и других агрессивных средах. К ним относятся материалы на основе перхлорвиниловой смолы. Так, например, для защиты от серной, азотной, фосфорной и других кислот, а также от щелочей и растворов солей предназначаются грунты ХСГ, эмали ХСЭ и лаки ХСЛ.
Термостойкие лакокрасочные покрытия под действием высоких температур не изменяют внешнего вида, защитных и физи-ко-химических свойств. Они получаются преимущественно на алкидно-масляной или кремнийорганической основе в сочетании с пигментами: железным суриком, графитом, алюминиевой пудрой и другими. Термостойкая эмаль черная 4-1 стойка при температурах 200—250° в течение 200 часов; срок службы в атмосферных условиях — около года. Эмаль жаростойкая АЛ-70 отличается стойкостью при температурах до 350° в течение 350 — 400 часов, срок службы в атмосферных условиях около 18 месяцев.
Жаростойкие покрытия получаются при использовании лакокрасочных материалов на основе кремнийорганических и перхлорвиниловых смол. Примером может служить композиция, состоящая из жаростойкого лака ФГ-9, представляющего собой смесь кремнийорганической смолы Ф-9 и полуфабриката ФХ-02, растворенных в толуоле и смешанных с алюминиевой пудрой. Эта эмаль применяется для деталей, работающих при температуре до 500° в течение 300 часов.
Для окраски трубопроводов и агрегатов систем летательных аппаратов и двигателей применяются глифталевые эмали различных цветов. Для нанесения опознавательных знаков и окраски противопожарной аппаратуры применяется красная пентаф-талевая эмаль марки А67.
Нитроэмали представляют собой растворы нитроцеллюлозы в летучих органических растворителях, смешанные с наполнителями, пигментами, смолами и пластификаторами.
Для окраски изделий, не подвергающихся непосредственному действию атмосферы, широкое применение находят нитроэмали марки ДМ различных цветов.
Окраска шкал и стрелок приборов, указателей и надписей осуществляется композициями, содержащими наряду с обычными составляющими светящиеся вещества — люминофоры. При изготовлении светящейся краски на один литр лака добавляется 400 г цинкового, цинково-кадмиевого или щелочно-земельного светосостава.
Лаки служат главным образом для защиты лакокрасочных покрытий, а также для окончательной отделки окрашенной поверхности. Применяются масляные, смоляные и эфироцеллюлоз-ные лаки.
Масляные лаки представляют собой сплавы смол с олифами, растворенные в скипидаре. В зависимости от соотношения количества масла и смолы эти лаки подразделяются на жирные, полужирные и тощие. Жирные лаки по сравнению с тощими образуют более плотную и эластичную пленку.
Жирный масляный лак марки 17А применяется для сталей и алюминиевых сплавов. Для декоративной отделки приборов применяется лак марки ЛМ-33, так называемый лак-кристалл «Мороз».
Смоляные лаки представляют собой растворы смол в растворителях. Примером их могут служить бакелитовые лаки, представляющие собой растворы резольных смол в этиловом спирте.
Эфироцеллюлозные лаки являются растворами нитроцеллюлозы, ацетилцеллюлозы и других эфиров целлюлозы. Главное применение получили нитролаки.
Реклама:
Читать далее:
Защита пленками сложного химического состава
Статьи по теме:
Лакокрасочные покрытия по металлу — Справочник химика 21
На очищаемые поверхности деталей пасту наносят кистью или шпателем, а при больших размерах поверхностей — растворо-насосом. Толщина слоя пасты 2—5 мм, время выдержки пасты на детали 15—60 мин. В этом случае гарантируется снятие слоя ржавчины толщиной до 1 мм. Если слой ржавчины большей толщины, увеличивают время выдержки пасты на детали или наносят пасту повторно. После удаления пасты поверхность обильно промывают водой или насухо протирают ветошью, а затем — 10%-ным раствором соли Мажеф или 10%-ным раствором ортофосфорной кислоты. На очищенной поверхности металла образуется пленка, защищающая металл от окисления на 1—2 суток. Кроме того, пленка улучшает адгезию лакокрасочных покрытий с поверхностью и удлиняет срок их службы. [c.74]Для защиты металлов от атмосферной коррозии широко применяют нанесение различных защитных неметаллических (смазки, лакокрасочные покрытия) и металлических (цинковых, никелевых, многослойных) покрытий или превращение поверхностного слоя металла в химическое соединение (окисел, фосфат), обладающее защитными свойствами. [c.383]
Наиболее распространена защита алюминия и его сплавов от коррозии электрохимическим оксидированием, при котором окисление достигается действием электрического тока (см. работу 5 этого раздела). Алюминиевые изделия помещают в электролит в качестве анода, поэтому метод обработки носит название — анодное окисление, или анодирование. При анодировании на алюминии и его сплавах получают пленки толщиной 5—20 мк, а в специальных случаях до 200—300 мк. Анодирование применяется не только для защиты от коррозии и улучшения адгезии (сцепления) с лакокрасочными покрытиями, но и для декоративной отделки поверхности металла, получения на ней фотоизображений, повышения стойкости против истирания, получения поверхностного электро- и теплоизоляционного слоя и слоя высокой твердости. Твердость анодной окисной пленки на чистом алюминии 1500 кг/мм , т. е. выше, чем твердость закаленной инструментальной стали. С помощью анодных пленок алюминия изготовляют алюминиевые выпрямители и конденсаторы. В последнее время анодная окисная пленка используется как подслой для лучшего сцепления алюминия с гальваническими покрытиями (хромом, никелем, серебром и др.). [c.146]
Нанесение неметаллических покрытий. Эффективную защиту металлов от коррозии обеспечивают различные лакокрасочные покрытия. Для создания таких покрытий используются лаки, краски, полимеры. Эти покрытия отличаются хорошей водостойкостью. Они обеспечивают механическую защиту металлов от коррозии. [c.219]
Неметаллические защитные покрытия могут быть как неорганическими, так и органическими. Защитное действие этих покрытий сводится в основном к изоляции металла от окружающей среды. В качестве неорганических покрытий могут быть неорганические эмали, оксиды металлов, соединения хрома, фосфора и др. К органическим относятся лакокрасочные покрытия, покрытия смолами, пластмассами, полимерными пленками, резиной. [c.220]
Повышение защитных свойств и долговечности лакокрасочного покрытия автомобиля, гаражей и т.п. за счет предварительного фосфатирования поверхности окрашиваемого металла [c.51]
Коэффициент линейного расширения покрытия в 14 раз выше коэффициента линейного расширения металла. При покрытии полиэтиленом выпуклых поверхностей металлов разница в коэффициенте линейного расширения приводит к повышению адгезии при покрытии полиэтиленом вогнутых поверхностей возникают напряжения, направленные на отрыв покрытий, поэтому полиэтилен наносят на прослойки полиэтилена с наполнителями или же на эластичные грунтовочные лакокрасочные покрытия. [c.423]
В качестве антикоррозионных покрытий для химической аппаратуры используются металлы, неметаллические материалы неорганического и органического происхождения, полимерные и лакокрасочные покрытия. [c.150]
Лакокрасочные материалы. Расширение жилищного строительства, увеличение вьшуска легковых автомобилей, мебели, холодильников и бытовых приборов обусловливают ускоренное развитие производства лакокрасочных материалов. В подотрасли ведется интенсивное техническое перевооружение, так как, в отличие от предприятий бытовой химии, лакокрасочные заводы в СССР представлены главным образом старыми предприятиями. Намечается ввести в строй новые мощности по выпуску лаков и эмалей на основе конденсационных и эпоксидных смол, порошковых красок, нетоксичных во дно дисперсионных красок. Срок службы лакокрасочных покрытий металлов должен быть доведен до 15-20 лет. [c.6]
Испытание на удар. Такие испытания показывают сопротивление покрытий деформации и деструкции в результате резкого удара. Они в значительной степени проясняют взаимосвязь между металлом и покрытием. Изменения адгезии, происходящие в результате химической реакции на. границе раздела лакокрасочное покрытие— металл, будут отражены в этом виде испытаний. [c.596]
Химически стойкие покрытия применяются в сотнях различных случаев, где лакокрасочные покрытия металла работают в кислых и щелочных средах, растворах солей или атмосфере, насыщенной агрессивными газами. [c.70]
Наиболее распространенным методом защиты металлов от коррозии в морской воде являются лакокрасочные покрытия на виниловой (этинолевые краски), фенолформальдегидной (краски АИШ), каменноугольной, битумной основе. Для подготовки металлической поверхности под покрытия применяют холодное фос- [c.403]
Старые защитные смазки — пушечная, ПП-95/5, ГОИ-54, технический вазелин — предохраняют все основные металлы и сплавы от атмосферной коррозии и не взаимодействуют с ними, а также с металлическими, фосфатными и оксидными покрытиями и большей частью лакокрасочных покрытий. Однако эти смазки имеют низкую температуру сползания (30—40 С) и поэтому не могут применяться для защиты от коррозии изделий, которые хранятся и транспортируются в условиях жаркого климата и особенно в тропиках. [c.693]
Очистка металлической поверхности от ржавчины вручную не обеспечивает полного удаления продуктов коррозии, поэтому лучше применять метод химической обработки поверхности, сущность которого заключается в том, что продукты коррозии при обработке превращаются в нерастворимые прочно связанные с металлом комплексные соединения, поверх которых наносится лакокрасочное покрытие. [c.154]
Наряду с оксидированием часто применяют фосфатирование, т. е. создание на поверхности металла защитной пленки, состоящей из нерастворимых в воде фосфатов железа и марганца. Фосфатирование служит не только для
1.5. Лакокрасочные защитные покрытия
Лакокрасочные покрытия — один из самых распространенных и надежных способов защиты от коррозии. Они дешевы и доступны, имеют простую технологию нанесения на поверхность, легко восстанавливаются в случае повреждения, отличаются разнообразием внешнего вида и цвета.
Ежегодно более 80 % металлоизделий, используемых в народном хозяйстве, подвергаются окрашиванию. В 1999 г. производство лакокрасочных материалов достигло 26,7 млн.т. Это свидетельствует об огромных масштабах средств, вовлеченных в сферу производства этого вида противокоррозионной защиты.
Эффективность применения лакокрасочных покрытий, как показывают данные рис. 3, целесообразна при условии долговечности эксплуатации не более 10 лет и скорости коррозии металла до 0,05 мм/год. Если требуется повышение долговечности или скорость коррозии металла составляет 0,5-1,0 мм/год, то следует применять комбинированные покрытия. Например, цинковые плюс лакокрасочное покрытие. Такое покрытие позволяет увеличить срок защиты до 30 лет.
Защитные действия лакокрасочного покрытия заключаются в создании на поверхности металлического изделия сплошной пленки, которая препятствует агрессивному воздействию окружающей среды и предохраняет металл от разрушения.
Компонентами лакокрасочных материалов служат пленкообразующие вещества, растворители, пластификаторы, пигменты, наполнители, катализаторы (сиккативы).
Лаки — это коллоидные растворы высыхающих масел или смол в органических растворителях. Защитное твердое покрытие образуется вследствие испарения растворителя или полимеризации масла или смолы при нагревании или под действием катализатора.
Краски представляют собой суспензию минеральных пигментов в пленкообразователе.
Эмали — это раствор лака, в который введены измельченные пигменты.
Пленкообразователи — это природные масла, естественные или искусственные смолы. Масла по своему составу представляют собой сложные эфиры, т.е. являются продуктом взаимодействия кислот и спиртов. В основу классификации масел положена их способность к высыханию.
Наиболее распространенный масляный пленкообразователь — олифа. Натуральную олифу получают из высыхающих растительных масел, обработанных при 300 °С с целью частичной полимеризации. На воздухе олифа окисляется и полимеризуется до твердого состояния.
Растворители пленкообразующих веществ придают лакокрасочным покрытиям такую вязкость, при которой они легко наносятся на поверхность. В дальнейшем растворители испаряются. Растворителями могут быть: спирты, ацетон, бензин, скипидар, толуол, ксилол, этилацетат и др.
Пластификаторы или смягчители — это вещества повышающие эластичность пленок после высыхания. К ним относятся касторовое масло, каучуки, дибутилфталат, трикрезилфосфат, эфиры адипиновой кислоты.
Количество пластификаторов, вводимых в смесь, составляет 20-75 % от массы пленкообразователя.
Краски и пигменты вводят в состав лакокрасочных композиций для придания им определенного цвета. Краски растворяются в растворителях, а пигменты находятся в них в нерастворимом мелкодисперсном состоянии. Размер частиц от 0,5 до 5 мкм. В качестве пигментов используют охру, сурик свинцовый, хром свинцовый, цинковые белила, порошки металлов. Пигменты повышают твердость, атмосферную и химическую стойкость, износостойкость и т.д.
Наполнители — это инертные вещества, которые вводят в лаки и краски для снижения расхода пигментов, а также для улучшения антикоррозионных свойств пленки. К ним относятся мел, тальк, каолин, асбестовая пыль и др.
Наполнители образуют прочную основу всей пленки. Частицы наполнителя распределяются в пленке между частицами пигмента и заполняют имеющиеся в ней промежутки. Благодаря этому пленка приобретает повышенную влагостойкость и антикоррозионные свойства. Схема строения лакокрасочной пленки представлена на рис. 8.
Рис.8. Строение лакокрасочной плёнки
Сиккативы или катализаторы представляют собой магниевые и кобальтовые соли жирных органических кислот. Их вводят в состав композиций для ускорения высыхания масляных пленок.
Успешная противокоррозионная защита лакокрасочными материалами в значительной степени зависит от соблюдения технологии получения покрытий. Основными факторами, влияющими на срок службы покрытия, являются:
• способ подготовки поверхности;
• методы нанесения и отверждения лакокрасочного покрытия;
• толщина комплексного покрытия.
Лакокрасочные покрытия
Категория: Малярные работы
Лакокрасочные покрытия
На деревянную мебель — фанерованную и из цельных досок, а также на другие изделия из древесины наносят прозрачные лакокрасочные материалы, которые ярче выявляют красоту дерева. Металлические изделия обычно защищают лакокрасочными покрытиями от коррозии, окрашивают непрозрачными (глянцевыми, матовыми и полуматовыми) эмалями и красками.
Лакокрасочные материалы получают на основе олиф или синтетических смол. Вид связующего в обозначении лаков и эмалей указывает двухбуквенный индекс: МЛ — меламинные смолы, МЧ — мочевинные, ПФ — пентафта-левые, ГФ — глифталевые, ХВ, ХС — поливинилхлорид-ные, перхлорвиниловые, НЦ — нитроцеллюлозные, ЭП — эпоксидные, ЭФ — эпоксиэфирные, ПЭ — полиэфирные, АК, АС — полиакриловые, УР — полиуретановые, УРФ — алкидно-уретановые, БТ — битумные. В цифровом обозначении лаков и эмалей первая цифра определяет назначение (1 и 5 — для наружных и внутренних работ, 2 — только для внутренних работ, 0 — грунтовки, 00 — шпатлевки). Следующие цифры обозначают цвет лакокрасочного материала. Выпускаемые советской промышленностью лаки и эмали изготавливаются самых различных цветов. Например, нитроцеллюлозная эмаль НЦ-25 выпускается 19 цветов.
В специализированных магазинах, помимо отечественных лакокрасочных материалов, продается большое количество различных импортных лаков, красок и эмалей. Их свойства и назначение, а также способы применения указаны на этикетках или прилагаемых инструкциях.
Поверхность древесины, на которую надлежит нанести лакокрасочное покрытие, должна быть сухой, чистой, хорошо отшлифованной, с исправленными внешними дефектами. Поверхность древесины неплотная, некоторые ее породы имеют мелкие поры, разбросанные в направлении волокон (бук), другие — глубокие беспорядочные риски (например дуб). Не следует, однако, рассматривать как порок глубокие риски на некоторых видах буковой мебели — их наносят специально. На фанерованной поверхности эти поры заделывают мастиками. Мастику приготовляют, загущая синтетический (например ПФ-283) лак тонкоизмельченным наполнителем (отмученным мелом, баритом, гипсом). Затем смесь тщательно растирают в ступке и окрашивают минеральным светостойким красителем, по тону соответствующим самому темному оттенку рисунка древесины. После этого в ступку добавляют разбавитель (уайт-спирит). Обычно процентное соотношение этих компонентов принимают равным 6:8: 86. Мастику втирают в риску под углом кистью или шпателем, тампоном. После обработки остатки мастики удаляют и на следующий день зачищают шлифовальной шкуркой зернистостью 10—8.
Пентафталевый лак ПФ-283 и глифталевый лак ГФ-166 приготовлены на основе алкидных смол. Лаки применяют для нанесения покрытий по масляным краскам, на деревянные и металлические поверхности, для наружных и внутренних работ. Лаки наносят кистью или распылением. Разбавители — ксилол, сольвент, скипидар, иногда — смесь одного из них с уайт-спиритом (1 : 1). Пожароопасность и токсичность лаков требуют защиты кожи и слизистых, работать с ними необходимо на открытом воздухе или в помещении, оборудованном приточно-вытяжной вентиляцией.
Мочевиноалкидный лак МЛ-2111 предназначен для отделки деревянных изделий при внутренних и наружных работах. Лак наносят распылением в один — три слоя, время сушки каждого слоя 2—3 ч. После выдержки последнего слоя в течение 24 ч его шлифуют шкуркой зернистостью 6—5.
Полиуретановый лак УР-2104М пригоден для покрытия древесины. Лак наносят распылением по грунтовке ВЛ-0278. Время сушки 2 ч, выдержка перед дальнейшей обработкой 6 ч. Покрытие шлифуют вручную бумажной или тканевой шкуркой зернистостью 4—3.
Н итроцеллюлозные лаки НЦ-218, НЦ-223, НЦ-243 (матовый) и другие получили широкое применение для отделки мебели и других изделий из дерева. Вначале на поверхность наносят грунтовку (ПМ-1 или БНК), сушат 1—2 ч, шлифуют шкуркой зернистостью 5—4, а затем напыляют один-два слоя лака. Разбавитель РМЛ. Покрытие шлифуют шкуркой зернистостью 5—4, нитро-политурой НЦ-314 (14—17 %-ная концентрация в уайт-спирите) или полировочной пастой № 290. Расход лаков 85—100 г/м2.
Полиэфирные лаки ПЭ-246 (парафиносодержащий) и ПЭ-232 (беспарафиновый) используют для отделки различных изделий из дерева. Лаки наносят кистью или наливом. Между первым и вторым слоями делают выдержку 20—30 мин, время сушки последнего слоя 10 ч при комнатной температуре. Окончательную отделку выполняют шлифовальной шкуркой зернистостью 4—3 и полировочной пастой 290 или полировочным составом типа 291.
Полиэфирные лаки ПЭ-232 и ПЭ-250 применяют для отделки изделий из древесины, эксплуатируемых в помещениях, с последующей полировкой. Лаки поставляются в виде двух компонентов: основы и инициатора полимеризации. Перед применением лак смешивают с инициатором в количестве 3,6 % массы лака ПЭ-232 и 3,3 % массы лака ПЭ-250. Затем смесь разбавляют растворителем Р-219 или ацетоном. На поверхности лаки наносят распылением или наливом. При комнатной температуре лаки можно использовать в течение 22—28 ч. Время сушки лака ПЭ-232 12 ч, лака ПЭ-250 8 ч.
Аналогичные лаки ПЭ-250М и ПЭ-250ПМ дают соответственно матовое и полуматовое покрытия, не требующие полировки. Эти лаки наносят распылением. Время сушки 8 ч, время использования 28 ч.
Лак БТ-5100 представляет собой раствор нефтяного битума в смеси органических растворителей. Лак предназначен для защиты внутренних поверхностей изделий от контакта специальных веществ. Перед применением лак разбавляют смесью ксилола с уайт-спиритом (1:1). Лак наносят кистью, время сушки при комнатной температуре 2 ч.
Эпоксидные лаки и отвердитель смешивают с разбавителем и через 30 мин растирают кистью. Светлая древесина иногда приобретает красноватый оттенок под действием агрессивных веществ, содержащихся в лаке. Через 24 ч тампоном наносят на поверхность немного керосина и шлифуют ее шкуркой зернистостью 4—3. Эту операцию целесообразно выполнять электрической кругло- и лен-точношлифовальной головкой. После этого очищают и осушают всю поверхность, обезжиривают бензином или ацетоном и наносят на нее верхний слой этого же лака. Если качество поверхности неудовлетворительно, через 24 ч поверхность прошлнфовывают вновь, обезжиривают и наносят лаковое покрытие вторично.
Травление и отбеливание. Если цвет фанеры не соответствует требованиям, перед нанесением лака ее можно осветлить или придать ей иной оттенок. При этом следует помнить, что светлая фанера со временем темнеет, а морилки — наоборот, светлеют.
Для отбеливания используют пергидроль — 30 %-ный раствор перекиси водорода, который наносят кистью из капрона или другого синтетического волокна. Следующая операция — нанесение водного раствора аммиака. Сразу же после появления белой пены фанеру откладывают для сушки. Этот процесс повторяют до достижения нужного тона. Перед отбеливанием рекомендуется нанести на изделие раствор едкого натра (48 г на 100 г воды), просушить и обработать перекисью.
Отбеливание можно выполнить 5 %-ным водным раствором щавелевой кислоты. После обработки поверхность промывают теплой водой. Эти операции необходимо выполнять в, защитных очках.
Для травления фанеры применяют водорастворимые протравы и медный купорос, хлорное железо и медь и т. д. Операции выполняют по инструкции.
После пропитки и сушки сухую поверхность фанеры шлифуют стеклянной шкуркой зернистостью 8—6.
Лакокрасочные покрытия металлов
Нитроцеллюлозная эмаль НЦ-259 предназначена для внутренних работ. Покрытие, нанесенное на очищенную, обезжиренную и отполированную поверхность металлов, защищает ее от поверхностного окисления, т. е. от потери глянца и окраски. Эмаль наносят распылением или кистью, она быстро сохнет, обладает влагостойкостью. Расход лака — 100 г/‘м2, разбавитель — уайт-спирит. Синтетический лак для наружных работ используют для нанесения на металлы прозрачных атмосферостойких покрытий. На отполированную и обезжиренную поверхность металла кистью или краскораспылителем наносят с интервалом 24 ч два слоя лака, после чего зачищают мокрой шлифовкой, применяя тонкозернистую шкурку № 4—3 и, как правило, полируют. Расход лака — 100 г/1,5 м2.
Шпатлевание
Выше были рассмотрены специальные мастики для обработки древесины. Теперь речь пойдет о шпатлевках для металлов и универсальных мастиках. Для выравнивания не очень нагруженных механической силой деталей (кузовов) в зоне соединений и сварных швов толщиной свыше 0,5 мм применяют шпатлевки эпоксидные, ПФ-002 и ИЦ-008 с такими влагостойкими наполнителями, как минеральные и стеклянные волокна или крошка.
Шпатлевки наносят на сухие обезжиренные поверхности чистого металла. После шлифования (не менее чем через 8 ч) и очистки наносят грунтовку. На металлы наносят кистью грунтовки, например ГФ-073, ПФ-033, ЭП-076. Обычно стремятся применять шпатлевку и лакокрасочные материалы одного характера, т. е. масляные или нитроцеллюлозные (возможные сочетания будут описаны ниже). На хорошо высушенное основание наносят обычные шпатлевки. Вначале густой шпатлевкой заполняют крупные неровности (они не должны быть больше 0,5 мм, иначе слой шпатлевки растрескивается), которые после сушки зашлифовывают. Затем менее густой смесью шпатлюют всю остальную поверхность. На ровные поверхности шпатлевку наносят жестким шпателем, а на закругленные — мягким шпателем из резины или ПВХ.
Под покрытия для наружных работ применяют масляную шлифующуюся шпатлевку ПФ-002. Ее наносят шпателем, а затем шлифуют: на древесине и кладке — сухим, на металле — мокрым способом, применяя водостойкие шлифовальные шкурки зернистостью 16—12.
Под покрытия для внутренних работ используют масляные и синтетические наносимые шпателем шпатлевки, которые можно зачищать сухой шлифовкой через 10 ч. На шлифованную и зачищенную шпатлевку наносят распылением слой масляной мастики. В качестве грунта эта мастика является почти универсальной — ее применяют для древесины и металлов, для наружных и внутренних работ. Через 14 ч поверхность шлифуют шкуркой № 5—4 мокрым способом. Для кузовов автомобилей и мебели применяют наносимую распылением цветную нитроцеллюлозную эмаль НЦ-25, не требующую полировки.
Для верхних покрытий древесины при внутренних работах, как правило, используют масляные составы. Древесину вначале покрывают олифой, а при необходимости шпатлюют. На шлифованную и зачищенную поверхность кистью наносят олифовую краску марки МА, цвет которой должен соответствовать заданному тону. Через 2 дня операцию повторяют, а затем поверхность отделывают сухой шлифовкой и тщательно полируют. После этого кистью наносят слой и сушат в течение трех суток. Расход краски — 100 г/м2, разбавитель — РС-2.
Нитроцеллюлозная эмаль НЦ-11 предназначена для наружных и внутренних работ но дереву и металлам. Наносят ее обычно распылением, разбавляя растворителями №№ 646, 647 и 648. Эмаль можно наносить и кистью, но поскольку она быстро сохнет и растворяет предыдущие слои, ее не растирают, а быстро наносят флейцем слой за слоем.
Асфальтовое покрытие для металлов. Если черный цвет не является помехой, для черных металлов применяют битумный лак БТ-577 или пековый лак. На зачищенную и обезжиренную поверхность стальной детали, работающей во влажной среде, кистью накосят масляную суриковую грунтовку; расход — 100 г/0,8 м2. Через 2 дня наносят второй слой. Затем через 2 дня кистью или распылителем наносят асфальтовый лак, а еще через день — последний слой (разбавитель РС-2). Расход лака — 100 г/м2. Лак сушат в течение недели. Внешний вид покрытия — черный, блестящий, размягчается на солнце.
Полуматовое покрытие для стальных деталей, работающих во влажной среде. Если нужен любой цвет, кроме черного, повторяют приведенный выше процесс, а для надежности наносят третий слой сурика после сушки предыдущего слоя в течение двух дней. Вместо асфальтового лака применяют любую масляную краску, предназначенную для окрашивания металлоконструкций, работающих в воде и влажной среде. С интервалами 2 дня кистью наносят три слоя краски. Расход — 100 г/0,7 м2.
Синтетическое цветное глянцевое покрытие для наружных поверхностей. С целью ускорения процесса в качестве грунта применяют синтетическую грунтовку (глифтале-вую, пентафталевую), которую наносят кистью. Через 12 ч наносят второй слой.’ Расход грунтовки — 100 г/м2. В качестве верхнего покрытия кистью наносят с двухдневным интервалом два слоя (лучше — три) соответствующей синтетической эмали; расход эмали — 100 г/м2.
Зпоксиэфирную грунтовку для влажной среды типа ЭФ наносят на металлы распылением, особенно эффективно двухслойное покрытие на оцинкованной листозон стали и цветных металлах.
Нитроцеллюлозный лак для кузовов, мебели и других изделий. Рассмотрим еще раз указанный процесс, включая шпатлевание, На зачищенную и обезжиренную поверхность вначале наносят эпоксидную шпатлевку, выравнивая самые крупные дефекты. На следующий день ее зачищают сухой шлифовальной шкуркой зернистостью 12, а затем наносят кистью синтетическую грунтовку ГФ-020 или № 147. На следующий день шпателем заделывают мелкие дефекты масляной шлифующейся мастикой и через 10 ч обрабатывают шлифовальной шкуркой зернистостью 12—10. После этого тщательно очищают от зерен абразива, сушат и краскораспылителем наносят слой эмали НЦ-11, НЦ-1113, затем сушат в течение 24 ч и зачищают мокрой шлифовальной шкуркой зернистостью 10—8. Вновь тщательно очищают, сушат и краскораспылителем наносят с интервалом 3 ч три слоя той же нитро-целлюлозной эмали. На следующий день шлифуют мокрым способом шкуркой 5—4 до получения гладкой поверхности. После этого вновь смывают зерна абразива и шлифуют тканевым диском с пастой № 289. Затем вновь смывают загрязнения, надевают новый круг и полируют поверхность пастой № 290. В заключение опять промызают поверхность и глянцуют овечьим мехом, смоченным «Полировальной водой № 1».
Полиэфирные полирующиеся лаки (например ПЭ-246, ПЭ-232) выпускают нескольких цветов. Эмаль и отверди-тель смешивают по инструкции. Лаки применяются для окрашивания кузовов, мебели и т. д. Они отличаются высокой прочностью при отслаивании и истирании. Способ полирования и шлифования изложен в предыдущем абзаце.
Двухкомпонентные полиуретановые эмали и лаки, в том числе грунты и пропитывающие лаки, например УР-175. Материалы обладают высокой прочностью при отслаивании, истирании и стойкостью против воздействия химикалий. Эти эмали и лаки используют для покрытия кузовов автомобилей, фюзеляжей самолетов, мебели, бетона, деревянных полов, облицовки стен, специальных деталей для резиновых изделий. Покрытия наносят кистью или краскораспылителем с давлением до 0,3 МПа; их нельзя наносить,.краскораспылителями высокого давления и в электростатическом поле.
Поливинилацетальные краски марки ВЛ разбавляют водой. Пигменты, продаваемые в тубах или тигелях, смешивают между собой. Краски применяют только для внутренних работ для древесины, штукатурки, бетона, каменной кладки и металлов. Древесину пропитывают олифой, через 2 дня шлифуют сухой шкуркой 12, промывают и наносят слой шпатлевки. Сухим способом шлифуют шкуркой № 10—8, очищают и флейцем наносят грунтовку, разбавленную водой. Через 3 ч кистью или краскораспылителем для надежности наносят два слоя верхней краски. Через 15 дней покрытие отвердевает, и его можно промыть водой. Старые масляные лакокрасочные покрытия достаточно тщательно промыть, прошлифовать шкуркой, а затем, как правило, без грунтовки нанести верхний слой краски. Кисти промывают водой сразу же после окончания работы.
Малярные работы — Лакокрасочные покрытия
Лакокрасочные покрытия металлов — Лакокрасочные покрытия — Основные сведения
3 мая 2012Нитроцеллюлозная эмаль НЦ-259 предназначена для внутренних работ. Покрытие, нанесенное на очищенную,
обезжиренную и отполированную поверхность металлов, защищает ее от поверхностного окисления, т. е. от потери глянца и окраски. Эмаль наносят распылением или кистью, она быстро сохнет, обладает влагостойкостью. Расход лака — 100 г/м2, разбавитель — уайт-спирит. Синтетический лак для наружных работ используют для нанесения на металлы прозрачных атмосферостойких покрытий.
На отполированную и обезжиренную поверхность металла кистью или краскораспылителем наносят с интервалом 24 ч два слоя лака, после чего зачищают мокрой шлифовкой, применяя тонкозернистую шкурку № 4 — 3 и, как правило, полируют. Расход лака — 100 г/1,5 м2.
Шпатлевание
Выше были рассмотрены специальные мастики для обработки древесины. Теперь речь пойдет о шпатлевках для металлов и универсальных мастиках.
Для выравнивания не очень нагруженных механической силой деталей (кузовов) в зоне соединений и сварных швов толщиной свыше 0,5 мм применяют шпатлевки эпоксидные, ПФ-002 и НЦ-008 с такими влагостойкими наполнителями, как минеральные и стеклянные волокна или крошка.
Шпатлевки наносят на сухие обезжиренные поверхности чистого металла. После шлифования (не менее чем через 8 ч) и очистки наносят грунтовку. На металлы наносят кистью грунтовки, например ГФ-073, ПФ-033, ЭП-076. Обычно стремятся применять шпатлевку и лакокрасочные материалы одного характера, т. е. масляные или нитроцеллюлозные (возможные сочетания будут описаны ниже).
На хорошо высушенное основание наносят обычные шпатлевки. Вначале густой шпатлевкой заполняют крупные неровности (они не должны быть больше 0,5 мм, иначе слой шпатлевки растрескивается), которые после сушки зашлифовывают. Затем менее густой смесью шпатлюют всю остальную поверхность. На ровные поверхности шпатлевку наносят жестким шпателем, а на закругленные — мягким шпателем из резины или ПВХ.
Под покрытия для наружных работ применяют масляную шлифующуюся шпатлевку ПФ-002. Ее наносят шпателем, а затем шлифуют: на древесине и кладке — сухим, на металле — мокрым способом, применяя водостойкие шлифовальные шкурки зернистостью 16 — 12.
Под покрытия для внутренних работ используют масляные и синтетические наносимые шпателем шпатлевки, которые можно зачищать сухой шлифовкой через 10 ч. На шлифованную и зачищенную шпатлевку наносят распылением слой масляной мастики.
В качестве грунта эта мастика является почти универсальной — ее применяют для древесины и металлов, для наружных и внутренних работ.
Через 14 ч поверхность шлифуют шкуркой № 5 — 4 мокрым способом. Для кузовов автомобилей и мебели применяют наносимую распылением цветную нитроцеллюлозную эмаль НЦ-25, не требующую полировки.
«Домашняя мастерская»,
Ф.Кусл, Ф.Крамериус
Пентафталевый лак ПФ-283 и глифталевый лак ГФ-166 приготовлены на основе алкидных смол. Лаки применяют для нанесения покрытий по масляным краскам, на деревянные и металлические поверхности, для наружных и внутренних работ. Лаки наносят кистью или распылением. Разбавители — ксилол, сольвент, скипидар, иногда — смесь одного из них с уайт-спиритом (1:1). Пожароопасность и токсичность лаков требуют защиты…
Для верхних покрытий древесины при внутренних работах, как правило, используют масляные составы. Древесину вначале покрывают олифой, а при необходимости шпатлюют. На шлифованную и зачищенную поверхность кистью наносят олифовую краску марки МА, цвет которой должен соответствовать заданному тону. Через 2 дня операцию повторяют, а затем поверхность отделывают сухой шлифовкой и тщательно полируют. После этого кистью наносят…
Нитроцеллюлозный лак для кузовов, мебели и других изделий. Рассмотрим еще раз указанный процесс, включая шпатлевание. На зачищенную и обезжиренную поверхность вначале наносят эпоксидную шпатлевку, выравнивая самые крупные дефекты. На следующий день ее зачищают сухой шлифовальной шкуркой зернистостью 12, а затем наносят кистью синтетическую грунтовку ГФ-020 или № 147. На следующий день шпателем заделывают мелкие дефекты…
Защитные покрытия: виды, функции, особенности
Уникальной разновидностью неметаллических защитных покрытий являются антифрикционные материалы. По внешнему виду они напоминают краски, однако вместо пигментов содержат частицы твердых смазочных веществ, которые равномерно распределены в смеси связующих компонентов и растворителей.
В противокоррозионной практике для изоляции металла от воздействия агрессивных сред используются специальные защитные покрытия. Все они подразделяются на металлические и неметаллические.
Металлические – анодные и катодные – покрытия наносятся на поверхности методами газотермического напыления, окунания, гальванизации, плакирования или диффузии.
К неметаллическим защитным покрытиям относятся лакокрасочные составы, полимерные пленки, силикатные эмали, резины, оксиды металлов, соединения фосфора, хрома и др.
Рассмотрим эти виды покрытий подробнее.
Металлические защитные покрытия
В качестве анодных металлических покрытий выступают металлы, электрохимический потенциал которых меньше, чем у обрабатываемых материалов. У катодных он, наоборот, выше.
Анодные покрытия обеспечивают электрохимическую защиту металлических поверхностей и выполняют свои функции даже при нарушении целостности слоя.
Катодные препятствуют попаданию агрессивных сред к основному металлу благодаря образованию механического барьера. Они лучше защищают поверхности от агрессивных воздействий, но только в случае неповрежденности.
В зависимости от способа нанесения металлические покрытия подразделяются на следующие виды.
Гальванические покрытия
Гальванизация – это электрохимический метод нанесения металлического защитного покрытия для защиты поверхностей от коррозии и окисления, улучшения их прочности и износостойкости, придания эстетичного внешнего вида.
Гальванические покрытия применяются в авиа- и машиностроении, радиотехнике, электронике, строительстве.
В зависимости от назначения конкретных деталей выделяют защитные, защитно-декоративные и специальные гальванические покрытия.
Защитные служат для изоляции металлических деталей от воздействия агрессивных сред и предотвращения механических повреждений. Защитно-декоративные предназначены для придания деталям эстетичного внешнего вида и их защиты от разрушительных внешних воздействий.
Специальные покрытия улучшают характеристики обрабатываемых поверхностей, обеспечивая их более высокой износостойкостью, электроизоляционными свойствами, повышенной прочностью и т.д.
Разновидностями гальванических покрытий являются меднение, хромирование, цинкование, железнение, никелирование, латунирование, родирование, золочение, серебрение и пр.
Газотермическое напыление
Представляет собой перенос расплавленных частиц материала на обрабатываемую поверхность газового или плазменным потоком. Покрытия, образованные таким методом, отличаются термо- и износостойкостью, хорошими антикоррозионными, антифрикционными и противозадирными свойствами, электроизоляционной или электропроводной способностью. В качестве напыляемого материала выступают проволоки, шнуры, порошки из металлов, керамики и металлокерамики.
Выделяют следующие методы газотермическогого напыления:
- Газопламенное напыление: самый простой и недорогой метод, применяемый для защиты крупных площадей поверхности от коррозии и восстановления геометрии деталей
- Высокоскоростное газопламенное напыление: используется для образования плотных металлокерамических и металлических покрытий
- Детонационное напыление: применяется для нанесения защитных покрытий, восстановления небольших поврежденных участков поверхности
- Плазменное напыление: используется для создания тугоплавких керамических покрытий
- Электродуговая металлизация: для нанесения антикоррозионных металлических покрытий на большие площади поверхности
- Напыление с оплавлением: применяется тогда, когда риск деформации деталей отсутствует или он оправдан
Погружение в расплав
При использовании этого метода обрабатываемые детали окунаются в расплавленный металл (олово, цинк, алюминий, свинец). Перед погружением поверхности обрабатываются смесью хлорида аммония (52-56 %), глицерина (5-6 %) и хлорида покрываемого металла. Это позволяет защитить расплав от окисления, а также удалить оксидные и солевые пленки.
Данный метод нельзя назвать экономичным, так как наносимый металл расходуется в больших количествах. При этом толщина покрытия неравномерна, а наносить расплав в узкие зазоры и отверстия, например, на резьбу, не представляется возможным.
Термодиффузионное покрытие
Данное покрытие, материалом для которого выступает цинк, обеспечивает высокую электрохимическую защиту стали и черных металлов. Оно обладает высокой адгезией, стойкостью к коррозии, механическим нагрузкам и деформации.
Слой термодиффузионного покрытия имеет одинаковую толщину даже на деталях сложных форм и не отслаивается в процессе эксплуатации.
Плакирование
Метод представляет собой нанесение металла термомеханическим способом: путем пластичной деформации и сильного сжатия. Чаще всего таким образом создаются защитные, контактные или декоративные покрытия на деталях из стали, алюминия, меди и их сплавов.
Плакирование осуществляется в процессе горячей прокатки, прессования, экструзии, штамповки или сваривания взрывом.
Виды и особенности неметаллических покрытий
Неметаллические покрытия подразделяются на органические и неорганические. Они создают на обрабатываемых поверхностях тонкую, инертную по отношению к агрессивным веществам пленку, которая предохраняет детали от негативных воздействий окружающей среды.
Лакокрасочные защитные покрытия
В состав таких покрытий входят пленкообразующие вещества, наполнители, пигменты, пластификаторы, растворители и катализаторы. Варьирование состава позволяет получать материалы со специфическими свойствами (токопроводящие, декоративные, особопрочные, жаростойкие и т.п.). Покрытия такого рода не только защищают изделия в различных условиях, но и придают им эстетичный внешний вид.
В группу лакокрасочных покрытий входят лаки, краски, грунтовки, олифы, шпаклевки.
Силикатные эмали
Применяются для изделий, работающих при высоких температурах, в химически агрессивных средах.
Эмалевое защитное покрытие формируется с помощью порошка или пасты. Процесс проходит в несколько этапов. Сначала на изделие наносится грунтовая эмаль – она улучшает адгезию, уменьшает термические и механические напряжения.
Затем, после спекания первого слоя при температуре +880… + 920 °С, накладывается покровная эмаль, после чего изделие снова подвергается нагреванию до +840… +860 °С.
Если требуется нанести несколько слоев силикатной эмали, вышеописанные операции проводят поочередно несколько раз. Изделия из чугуна, к примеру, обрабатывают в 2-3 подхода.
Застывшая эмаль представляет собой тонкое, похожее на стекло, покрытие. Его основным недостатком является сравнительно низкая прочность – под воздействием ударных нагрузок эмаль может растрескиваться или скалываться.
Полимерные защитные покрытия
В число наиболее распространенных полимеров, применяющихся для защиты металлов от коррозии, входят полистирол, полиэтилен, полипропилен, полиизобутилен, фторопласты, эпоксидные смолы и др.
Полимерное покрытие осуществляется методами окунания, газотермического или вихревого напыления, обычной кистью. Остывая, оно образует на поверхности сплошную защитную пленку толщиной несколько миллиметров.
Разновидностью полимерных являются антифрикционные покрытия (АФП). Внешне эти материалы похожи на краски, однако вместо пигментов они содержат высокодисперсные частицы твердых смазочных веществ, которые равномерно распределены в смеси связующих компонентов и растворителей.
Основу АФП могут составлять дисульфид молибдена, графит, политетрафторэтилен (ПТФЭ) и прочие твердые смазки, в качестве связующих применяются акриловые, фенольные, полиамид-имидные, эпоксидные смолы, титанат, полиуретан и некоторые другие специальные компоненты.
Антифрикционные твердосмазочные покрытия (АТСП), а также специальные растворители и очистители для предварительной подготовки поверхностей разрабатывает российская компания «Моделирование и инжиниринг».
АТСП MODENGY применяются в средне- и тяжелонагруженных узлах трения скольжения (направляющих, зубчатых передачах, подшипниках и т.д.), на деталях двигателей внутреннего сгорания (юбках поршней, подшипниках скольжения, дроссельной заслонке), в резьбовых соединениях и крепеже, трубопроводной арматуре, пластиковых и металлических элементах автомобилей (замках, петлях, пружинах, скобах, механизмах регулировки и т.д.), а также в других парах трения металл-металл, металл-резина, полимер-полимер, металл-полимер.
Материалы MODENGY наносятся однократно на весь срок службы деталей, позволяя создавать узлы трения, не требующие дальнейшего обслуживания и применения традиционных смазочных материалов.
Антифрикционные покрытия MODENGY отличаются:
- Высокой несущей способностью
- Работоспособностью в запыленной среде
- Низким коэффициентом трения
- Широким диапазоном рабочих температур
- Высокой износостойкостью
- Противозадирными и антикоррозионными свойствами
- Стойкостью к воздействию кислот, щелочей, растворителей и других химикатов
- Работоспособность в условиях радиации и вакуума
Покрытия ложатся тонким слоем, поэтому практически не меняют исходные размеры деталей, зато обеспечивают им необходимый комплекс триботехнических и защитных свойств.
Применение АТСП MODENGY позволяет эффективно управлять трением, повышать ресурс и энергоэффективность оборудования.
Оксидные защитные пленки
Оксидирование – это окислительно-восстановительная реакция металлов, которая возникает благодаря их взаимодействию с кислородом, электролитом или специальными кислотно-щелочными составами. В результате этого процесса на металлических поверхностях образуется защитная пленка, которая увеличивает их твердость, снижает риск образования задиров, улучшает приработку деталей и повышает срок их службы.
Оксидирование используется для получения защитных и декоративных покрытий, а также для формирования диэлектрических слоев. Различают химические, анодные (электрохимические), термические, плазменные и лазерные методы этой обработки.
Резиновые защитные покрытия
Гуммирование, или создание защитных покрытий резины или эбонита, осуществляется для защиты различных емкостей, трубопроводов, цистерн, химических аппаратов, резервуаров для перевозки и хранения химических веществ от воздействия внешней среды.
Защитное покрытие может быть сформировано из мягкой или твердой резины. Консистенция контролируется добавками серы: мягкая содержит от 2 до 4 % этого вещества, твердая – от 30 до 50 %.
Покрытие наносится на предварительно очищенные и обезжиренные поверхности. Скопившийся после обработки воздух выдавливается валиком. В качестве заключительного этапа гуммирования проводится вулканизация изделий.
Резиновые покрытия являются хорошими диэлектриками, обладают стойкостью ко многим кислотам и щелочам (но не к сильным окислителям). Из существенных недостатков резиновых покрытий можно выделить их старение со временем.
Смазки и пасты
При длительном хранении и перевозке металлоизделий в качестве защитных покрытий могут использоваться специальные смазки и пасты – они препятствуют попаданию на поверхности влаги, пыли и различных газообразных веществ, наносятся кистью или методом распыления.
Консервационные материалы изготавливаются на основе минеральных масел (вазелинового, машинного) и воскообразных веществ (воска, парафина, мыла). Очень популярны смазки, в состав которых входит 5 % парафина и 95 % петролатума (смеси парафинов, масел и минеральных восков – церезинов).
Главный недостаток паст и смазок, применяющихся в качестве защитных покрытий, состоит в том, что целостность образовавшейся пленки легко нарушить. Именно поэтому лучшей альтернативой пластичных составов являются антифрикционные покрытия.
Лаки и краски для огнезащиты металла: виды и типы
Составы этих материалов, являющихся одним из видов огнезащиты металлических конструкций, нужны, чтобы предотвратить резкий нагрев несущего каркаса зданий, элементов инженерных сетей в ходе развития пожара, так как иначе металлические конструкции быстро деформируются, вплоть до полного обрушения.
Обработка металлоконструкций огнестойкими красками, лаками является одним из эффективных, востребованных видов пассивной огнезащиты, что связано, в том числе небольшим расходом материалов по сравнению со штукатурками, пастами, мастиками.
Применение
Лакокрасочная продукция для металлоконструкций используются с целью огнезащитного покрытия несущего каркаса – ферм, пролетов, в том числе сложной геометрической формы; балок, колонн, опор как зданий промышленных, так и общественных объектов, везде, где степень огнестойкости строений невозможно обеспечить без доведения металлических конструкций, до требуемого противопожарными нормами предела стойкости к огню.
Зачастую защита металла от огня необходима для стальных конструкций, не только образующих несущий каркас внутри его строительного объема, но и расположенных снаружи; в зависимости от проектных решений, в том числе в необходимости усиления сейсмической устойчивости.
В таких случаях необходима атмосферостойкая огнезащитная краска или лак, способные без растрескивания, шелушения, осыпания из-за воздействия влаги, ветра, резких ежесуточных перепадов температуры, а также при минусовой температуре, вплоть до критически низких значений, длительное время эксплуатироваться на открытом воздухе.
Появление стойких к огню, резкому повышению температуры воздуха в защищаемых помещениях, пожарных отсеках, секциях строений различного функционального назначения, а также не подверженных атмосферному воздействию огнезащитных красок и лаков, позволило эффективно покрывать несущие стальные конструкции зданий, инженерных, технологических сооружений в тех случаях, когда использовать огнезащитные штукатурки, пасты, мастики, а также конструктивную огнезащиту из огнестойкого гипсокартона с заполнением пустот огнезащитным базальтовым материалом невозможно или нецелесообразно по разным объективным причинам.
Преимуществами применения огнестойких красок и лаков на объектах защиты, по сравнению с традиционными покрытиями, также являются:
- Намного меньший расход материалов, даже при многослойном покрытии, что не только снижает затраты заказчика, но и значительно уменьшает нагрузку на несущие конструкции зданий, в том числе на фермы, балки, междуэтажные перекрытия, фундамент. Зачастую это бывает критически необходимым при проектировании строений большого объема, в том числе спортивных, культурно-зрелищных сооружений или зданий с атриумами.
- Покрытие огнезащитными красками, лаками не портит, а напротив, эффектно декорирует внешний вид защищаемых металлических конструкций, что важно для архитекторов и дизайнеров.
- Они не только надежно защищают металл от воздействия пламени, высокотемпературных потоков тепла, но и от прямого контакта с влагой, О2 воздуха, препятствуя активному окислению, образованию ржавчины в результате коррозии, в том числе химической; что не редкость в защищаемых помещениях с высокой категорией по взрывопожарной опасности, агрессивной средой.
Огнезащитные лаки, как и краски применяют для покрытия несущих строительных конструкций, транзитных воздуховодов в пожароопасных зонах, помещениях; коробов, шахт систем дымоудаления, подачи воздуха; а также для огнезащиты кабеля и кабельных линий; как финишный защитный, декорирующий слой по другим огнестойким покрытиям – краскам, штукатуркам, мастикам, совместимых с ними.
Подводя итоги, можно сделать вывод: при нормальных условиях – это одни из видов высококачественной лакокрасочной продукции, обладающие всеми ее преимуществами применения как внутри, так и снаружи строений.
А при возникновении в них или в противопожарных разрывах вблизи них высокотемпературного очага возгорания – эффективные огнезащитные покрытия, выдерживающие воздействие огня, высокой температуры в течение периода, требуемого противопожарными нормами.
Виды и типы
Компаниями производителями разработаны и серийно производятся два вида такой специальной лакокрасочной продукции, совмещающей основные функции – защиту металла от внешних атмосферных воздействий, от огня и высокой температуры:
- Вспучивающаяся краска является наиболее распространенной товарной группой огнестойких красок и лаков.
При прямом контакте с открытым пламенем, высокотемпературным тепловым потоком от распространяющегося внутри или снаружи здания пожара, они в силу своего химического состава, являясь термически активными материалами, быстро и многократно – в десятки раз увеличиваются в объеме; образовывают вспененный слой обугленного коксового покрытия, напоминающего по виду и внутренней структуре вулканическую пемзу.
Состав, в свою очередь, за счет ничтожно низкой теплопроводности, эффективно препятствует прогреву металлических конструкций. Это надежное огнезащитное покрытие несущего каркаса зданий, важных элементов инженерных систем жизнеобеспечения зданий – электрических кабельных трасс, воздуховодов вентиляции, в том числе систем противодымной защиты.
- Не вспучивающая (сохраняющая объем) огнестойкая краска или лак, также являются многослойными покрытиями, но они не изменяют своего первоначального объема даже при сильном огневом, тепловом воздействии.
Их физико-химический механизм огнезащиты отличается от вспучивающихся огнестойких покрытий. В основе силикаты, часто называемые в обиходе жидким стеклом, которые создают на поверхности металлических конструкций и элементов систем жизнеобеспечения защищаемых объектов плотное покрытие, надежно защищающее от внешних воздействий при нормальных условиях.
А при резком высокотемпературном воздействии состав спекается, образуя слой покрытия, аналогичный керамическим эмалям, который эффективно предохраняет защищаемую поверхность металла от быстрого нагрева, деформации и разрушения.
Недостатками таких огнестойких красок, лаков являются больший расход материалов, меньшая огнезащитная эффективность, чем у вспучивающихся аналогов, поэтому они применяются на объектах гораздо реже.
Состав и описание
Основная техническая характеристика огнестойких лаков, красок – это их огнезащитная эффективность, регламентируемая НПБ 236-97, ГОСТ Р 53295-2009 для средств огнезащиты стальных конструкций. По их определениям, требованиям она варьируется от 7 группы с пределом стойкости к огню 15 мин до 3 группы – 90 мин, и максимальной 1 группы – 150 мин.
Химический состав огнестойких красок, лаков компаниями производителями как в рекламных проспектах, так и в заводской сопроводительной документации на поставляемую товарную продукцию редко раскрывается, что, конечно, обусловлено коммерческой тайной, нежеланием открывать рецептуры создания таких инновационных материалов конкурентам.
Из открытых сведений известно, что в них используются пленкообразующие вещества, вспенивающиеся под воздействием высокой температуры реагенты, в том числе термически активный графит; некоторые виды солей, а также мелко помолотые минеральные наполнители.
На российском рынке огнезащитных средств наиболее популярны следующие марки красок, лаков:
- Крауз. Под этой маркой НПО «Стройзащита» выпускает три вида вспучивающихся огнезащитных красок по металлу: Крауз, Крауз-Ультра – на водной основе, создающие покрытия с огнезащитной эффективностью 90 мин, наносимых в помещениях при температуре выше 0 ℃; Крауз-Р – на органическом растворителе, до 120 мин, которую можно наносить до – 15 ℃. Срок эксплуатации покрытий – до 25 лет.
- Kron–SW – это огнезащитная краска для металлических конструкций, имеющая огнезащитную эффективность 120 мин. Условия нанесения – не ниже – 15 ℃. Гарантийный срок эксплуатации покрытий – 25 лет, с финишным покрытием – до 50 лет.
- Neomid (Неомид). Под этой торговой маркой выпускается много видов продукции как для огнезащиты древесины, так для металлоконструкций, в том числе всесезонная краска по металлу Neomid 050, предназначенная для работ как внутри помещений, так и на открытом воздухе при низких значениях температуры, но без прямого воздействия воды. Обеспечение огнезащитной эффективности в диапазоне от 45 до 120 мин, окраска при температуре – не ниже – 25 ℃ при влажности воздуха до 80%.
- Кроме них, существует огнезащитная лакокрасочная продукция марок Pirex–metal plus, Нертекс, Термобарьер, Стабитерм, Негорин.
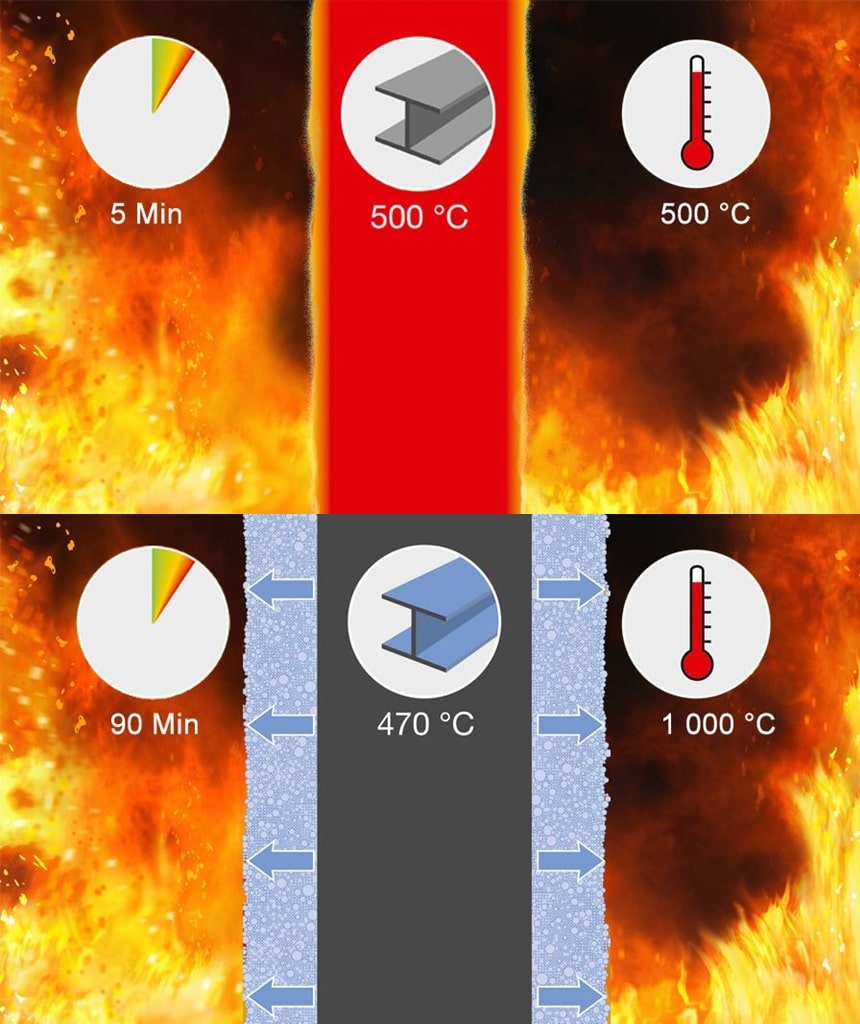
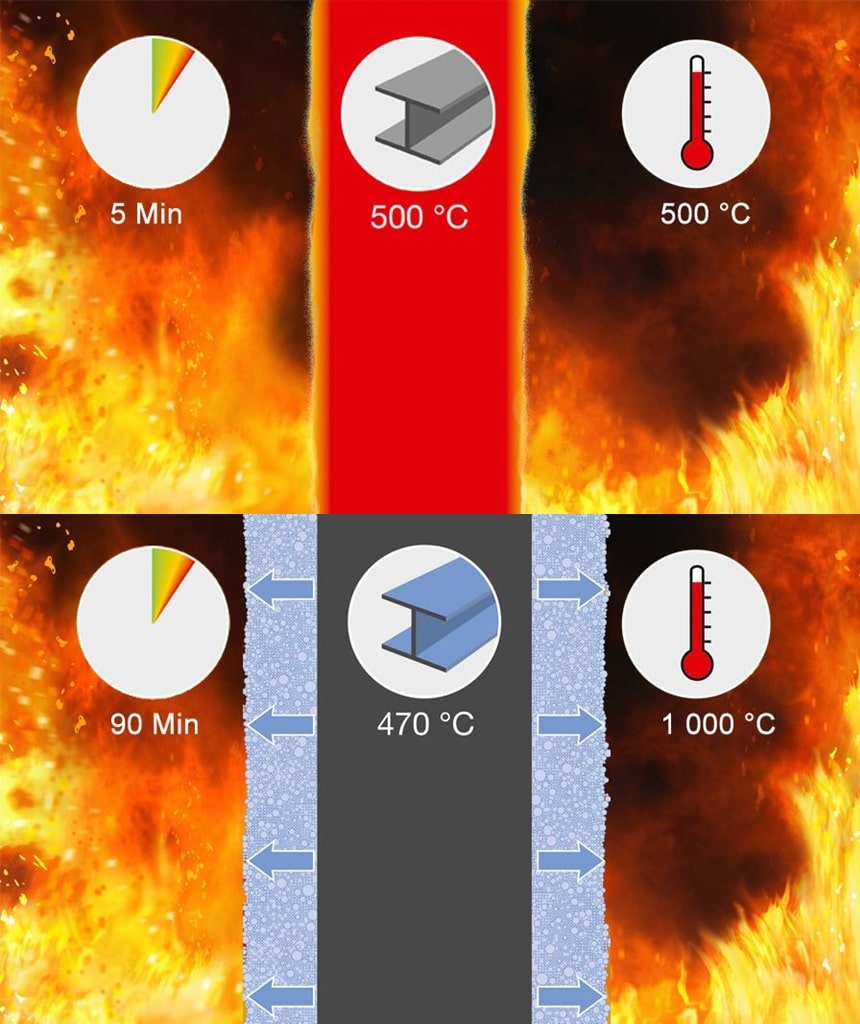
Сертификат соответствия
Согласно статье 150 ФЗ-123 для подтверждения качества, огнезащитной эффективности огнестойких лакокрасочных покрытий на любую партию серийной продукции, применяемой для окраски металлических конструкций несущего каркаса зданий, элементов инженерных систем; независимо от объема поставки, требуется сертификат пожарной безопасности, в котором должна указываться следующая информация:
- Марка, наименование огнезащитной краски, лака.
- Группа огнезащитной эффективности.
- Виды, названия, количество, необходимая толщина слоев грунтовок, финишных защитных, декоративных покрытий, совместимых с поставляемой огнезащитной продукцией.
- Толщина слоев огнезащитных красок, лаков, а также их расходы для получения многослойных покрытий для различных групп огнезащитной эффективности.
Требования
- Лакокрасочные изделия создавать покрытия, с требуемой для различных металлоконструкций огнезащитной эффективностью.
- Образующиеся после окраски многослойные огнезащитные покрытия должны быть долговечными, не растрескиваться, не разрушаться под внешними воздействиями, включая высокую влажность воздуха, образование конденсата, вибрацию.
- Не должны выделять пары ядовитых химических соединений как при нормальных условиях, так и в процессе образования вспучивающегося теплозащитного слоя при огневом, тепловом воздействии.
- Отвечать требованиям эстетики в готовом виде после нанесения финишного слоя, для чего должна быть возможна их колеровка в различные цвета.
Заказчики, специалисты проектных организаций, предприятий, проводящих огнезащитные работы на основании лицензионных разрешений от МЧС, по требованиям противопожарных норм без проблем находят оптимальные варианты из многообразия видов огнестойкой лакокрасочной продукции для каждого конкретного случая огнезащиты металлоконструкций строений различного назначения.
Правила нанесения
Принцип проведения работ как внутри, так и снаружи объектов защиты с использованием таких лакокрасочных материалов – это покраска в несколько слоев, количество которых в зависимости от требуемого предела стойкости к огню покрытия определяется в сопроводительной заводской документации на продукцию, где также указывается расход огнезащитной краски на 1 м2 по металлу.
Огнезащитная обработка обязательно чередуется полным просушиваем каждого слоя огнестойкой краски, лака.
Существует четыре этапа работ при использовании для покрытия металлоконструкций огнезащитных красок, лаков:
- Тщательная подготовка поверхности металла, включающая очистку от слоев прежних лакокрасочных покрытий; загрязнений – ржавчины, следов горючих жидкостей; пылевых, солевых отложений.
- Методы такой подготовки разнообразны – от механической обработки металлических поверхностей ручным или электрифицированным инструментом, пескоструйными аппаратами до химической очистки органическими растворителями, преобразователями ржавчины.
- Крайне важно также обезжиривание поверхностей металлоконструкций для обеспечения высокой адгезии при наложении покрытия.
- Грунтование различными материалами, по физико-химическим свойствам совместимыми с огнезащитной лакокрасочной продукцией, что как дает защиту металлу от возможной коррозии, так и способствует более надежному контакту красок, лаков с поверхностью металлоконструкций, без риска растрескивания, отслоения.
- Окраска металлоконструкций вручную с использованием кистей, валиков, или с применением промышленного оборудования для проведения окрасочных работ – краскопультов, станций безвоздушного распыления.
- Нанесение защитных, финишных декоративных покрытий, как предохраняющих огнезащитные краски, лаки от внешних, в том числе атмосферных воздействий, так и придающих им приятный внешний вид, что достигается, в том числе колеровкой.
Довольно часто в качестве финишного покрытия по огнестойкой краске применяется лак от той же компании производителя, что гарантирует их максимальную совместимость, долговечность получаемого комбинированного огнезащитного покрытия.