Как соединить доски между собой в щит
После выбора пиломатериалов, я раскладываю доски в том виде, как они будут расположены в массиве. Во-первых, подбирая цвета в каждой заготовке, перемещайте и переворачивайте их до тех пор пока узоры структуры древесины, не совпадут. Прямая структура должна работать рядом с прямыми волокнами. Изогнутая структура древесины должна слиться с изогнутой структурой древесины. До склейки массива, заготовки необходимо выровнять используя шлифовальный, фуговальный станок или вручную рубанком.
Определите направление структуры древесины, глядя на край сращивание доски, см. Совет: Нарисуйте стрелку на каждой доске в направлении волокон, см. Это будет указателем на доске в дальнейшем. Есть еще одно условие в решении данной головоломки, как будет коробиться панель с изменением влажности? Для панелей, у которых торцы жестко скреплены планкой, коробление массива не является проблемой. Но массивы, у которых нет жесткого крепления торцов подвержены короблению.
Коробятся те массивы, у которых нет чередования годичных колец в противоположном направлении и они приобретают форму чаши, см. Уйти от коробления массива можно изменяя направление годичных колец в брусках по всей ширине массива. После того, как доски разложены в панели, нанесите мелом римские цифры по швам, см.
Римские цифры предотвращают возможность попутать бруски. Итак, какие критерии наиболее важны: внешний вид, цвет и направление волокон? Я стараюсь соединить направление волокон и структура древесины в панели, но часто, это компромиссные решения.

Когда вы подготавливаете сращивание доски в панель, то не должно быть даже небольших компромиссов. Сильная стяжка не нужна, когда детали имеют гладкие, прямые края. Если края не имеют прямого угла в брусках то форма чаши в массиве вам гарантирована, см.
Чтобы предотвратить это, убедитесь, что ваши станки настроены правильно. Получить гладкий, прямой край не сложно используя фуганок, см. Фуганок снимает одно количество стружки и вам не придется регулировать упор при каждом проходе. Медленно подавайте заготовку к режущей головке учитывая направление структуры древесины, см. После прохода получите прямой и ровный край готовый к поклейке. Если у вас нет фуганка, подготовить соединительные края можно циркулярной пилой, см.
Изготовьте параллельную прямую доску, затем сделайте проход доски на циркулярке используя только половину толщины и высоты пильного диска, см.
Инструменты и материалы для изготовления мебельного щита
Этот способ не дает поджогов и дает чистые, ровные края…. Таким образом, чтобы убедиться, что нет никаких сюрпризов соберите панель перед склеиванием, на сухую.
При подготовке клея убедитесь, что у него есть хорошая вязкость. Некоторые мастера мажут клей только по одному краю каждой доски. Это быстро, но не практично, нанесение клея на две кромки удалит воздух при склейке и заполнит все поры. Примечание: Если промазанная поверхность не глянцевая на вид, значит клей впитался в лес и его нужно добавить.
Как склеивают древесину – технология и тонкости
Многие предлагают удалять излишки клея влажной тряпкой. Не торопитесь этого делать, удалив клей откроется стыковочный шов в брусках и нарушится герметизация в стыке. Оставьте панель на несколько часов или даже на ночь, к тому времени клей просохнет и его можно будет соскоблить. Примечание: металлические трубы могут оставляя ржавое пятно на древесине. Есть два способа, чтобы выровнять панель.
Если в середине массива сращивание доски пучит вверх возьмите молоток и деревянную прокладку, легко простукивайте молотком через прокладку по массиву, см.
Доски пучит вниз, по краям массива положите бруски-прокладки и зажмите струбцинами их вместе с панелью, см. Примечание: Обязательно используйте под струбцинами деревянные бруски-прокладки, чтобы струбцины не оставили вмятины. После того, как доски собраны в панель и находятся на одном уровне, затяните струбцины до появления крошечных капелек клея вдоль каждой линии соединения.
Зажимы должны быть плотными, но главное, выравнивайте давление струбцин вдоль лини. Убедитесь, что давление на панель равномерное, смотрите по капелькам клея, в случае неравномерного давления добавьте или уберите струбцины.
Надежность и эстетика сложных конструкций из дерева во многом зависит от правильного выбора способа соединения ее составных частей. Особенно это актуально для карка
Мебельный щит своими руками: инструкция от мастеров
Содержание:
Успешные занятые люди должны иметь хобби. Это снимает стресс и уменьшает опасность инфаркта. Можно собирать фантики и монетки, а можно заняться серьезным ремеслом. Например, склеить мебельный щит своими руками. Процесс не так сложен, как может показаться, однако требует хотя бы минимального владения инструментом.
Инструменты и материалы для изготовления мебельного щита
- Дисковая пила.
- Фрезерный станок.
- Дрель.
- Молоток.
- Ленточная и плоскошлифовальная машинки. Можно зачищать дерево наждачной шкуркой, навернув ее на колодку. Правда, это будет немного дольше.
- Рейсмус.
- Струбцины или самодельные приспособления для стягивания досок.
- Длинная металлическая линейка, карандаш, рулетка.
- Пиломатериал.
- Фанера и тонкие рейки для сплачивания щита.
- Клей.
Подготовительные работы
Сначала определимся, какого размера мебельный щит нам нужен, чтобы запастись достаточным количеством материала. Заготовки в любом случае должны быть длиннее и толще, чем окончательные параметры щита. Доски выбираем из дерева одной породы, сухие и ровные, с минимумом сучков. Необходимо также знать основные свойства древесины. Предлагаем небольшой словарик столяра, чтобы не путаться в понятиях:
- Пласти – широкие продольные стороны досок.
- Делянки – отдельные бруски, планки, выпиленные из широкой доски.
- Ламели – цельные, несрощенные заготовки. Фактически то же самое, что и делянки.
- Свилеватость – беспорядочное расположение древесных волокон в заготовке. Встречается, когда доска выпилена из комля дерева.
- Заболонь – наружный слой древесины, расположенный сразу под корой.
По советам старых мастеров, как сделать мебельный щит хорошего качества, берутся делянки, имеющие соотношение ширины к толщине, как 3х1. Такая ламель стабильна, поскольку внутреннего напряжения древесины не хватает, чтобы расколоть рейку. Все мы видели доски, треснувшие с торца. Это тот самый случай, когда напряжение материала, вызванное неправильной сушкой, раскалывает заготовку. Значит, сначала распускаем пиломатериал на рейки шириной не более 15 см. В процессе распила заодно удаляем все дефектные участки досок.
Перед сборкой щита учитываем, что древесина при усушке коробится в разных направлениях. Сильнее всего – по направлению годичных колец (тангенциальное направление), в два раза слабее – по направлению сердцевинных линий (радиальное направление). Напиленные заготовки склеиваем в порядке, указанном на самом первом фото:
Щиты a и b: сердцевина сплачивается с сердцевиной, заболонь с заболонью. Это позволит избежать коробления при усушке щита, снижающего прочность клеевых соединений.
Щиты c и d: заготовки с выраженной свилеватостью ориентируем по линиям годовых колец, тогда деформация готового щита будет намного меньше.
Пошаговая инструкция по изготовлению мебельного щита
- Укладываем доски в нужное положение, добиваясь оптимального расположения годовых колец. Перед тем, как разобрать конструкцию, помечаем материал понятным нам образом (например, начертив треугольник). Разметка поможет в дальнейшем быстро найти нужную ламель. Торцы досок перед склейкой необходимо отфуговать.
- Чтобы изготовление мебельного щита своими руками пошло быстрее, складываем доски в пачку и промазываем торцы клеем. Если уложить делянки в полиэтиленовый мешок, клей будет схватываться медленней, и мы успеем собрать заготовки в щит.
- Если в хозяйстве имеются большие струбцины, стягиваем склеенную древесину ими. Многие мастера применяют такое приспособление, как вайма, собранная из обрезков досок. Стягивающий момент обеспечивается забиванием клиньев между упором и торцом доски. Можно сжать доски между кронштейнами металлических стеллажей. Принцип тот же самый – сплачивание кромок происходит при помощи клиньев и деревянных брусков.
- Тщательно, не жалея времени, просушиваем склеенный щит. Для получения ровной и гладкой поверхности древесину стругаем, шлифуем, одновременно удаляя следы клея.
Способы соединения делянок в щите
Как сделать мебельный щит своими руками, чтобы в дальнейшем древесина сохраняла первоначальную стабильность? Справиться с короблением щита, вызванным свилеватостью пиломатериала, можно несколькими путями.
Склеиваем ламели на шпонках (нижний щит на фото 6) или используем завершающие наконечники, по примеру чертежной доски. Для фиксации недлинных досок применяем наконечник с узлом паз-гребень (верхний щит на фото), соединенный с ламелями заподлицо. Наконечник может иметь выступ над одной (средний щит) или обеими пластями, в зависимости от назначения изделия.
Если мебельный щит намечено использовать в условиях постоянного колебания влажности, целесообразнее будет не склеивать доски. Компенсация древесины при частом разбухании достигается различными способами сплачивания делянок. Верхний щит на фото 7 соединен в четверть, средний – в четверть со снятием фаски с верхних кромок. Доски нижнего щита сплочены также в четверть, но уже с выборкой профильных кромок на лицевой стороне.
Еще один вид сопряжения делянок без использования клея – это применение нащельных планок. Верхний щит на фото 8 стянут обычной рейкой, средний – профилированной планкой без пазов, нижний – профилированной планкой с пазами.
Если мебельный щит будет эксплуатироваться при постоянной механической нагрузке, в условиях высокой влажности и перепада температур, то доски должны иметь более мощное сопряжение. На фото 9 показаны примеры подобных соединений. Верхний щит собран на шкантах, средний – на фанерную рейку. Ширина рейки должна равняться толщине делянок, толщина рейки – одной трети толщины делянок.
На примере нижнего щита показано соединение в шпунт, применяемое при настилании пола или облицовке перегородок. Все эти методы могут быть использованы при изготовлении разборных щитов (к примеру, для раздвижной мебели). Клей в указанных соединениях не применяется.
Склеивание ламелей на шкантах требует идеальной точности расположения отверстий, иначе геометрия щита будет нарушена. Разметка гнезд производится маркерами. Сверлить торцы лучше всего с использованием сверлильной стойки и упора. Глубина обеих отверстий в сумме должна превышать длину крепежного элемента на 2-3 мм.
Если нет фрезерного станка, пазы и профили на торцах выводят с помощью дрели, закрепленной на стойке. На инструмент устанавливают соответствующую фрезу и включают высокие обороты.
Собранный, просушенный и отшлифованный щит опиливаем до нужных размеров. Теперь можно пускать его в работу – делать мебель, двери, подоконники, обшивать стены и потолки. Прочность, эстетичность, натуральность мебельных щитов – это лучшие рекомендации для строительного материала.
Технология склеивания массивной древесины
Содержание страницы
1. Способы склеивания массивной древесины по длине
1.1. Виды шиповых соединений
Очень часто при изготовлении различных изделий из древесины необходимо соединить разные детали склеиванием. Применение шипового соединения придает изделию необходимую прочность.
Шиповое соединение состоит из двух частей — шипа и гнезда проушины. Шип — это выступ, который находится на конце одной из соединяемых деталей. Шип вставляется в проушину либо гнездо другой соединяемой детали. Можно встретить одинарный (рис. 1), двойной (рис. 1) и многократный шипы (рис. 1). Шипы делятся на цельные и вставные. Цельным называется шип, который составляет с деталью единое целое. Вставной шип выполняется отдельно от детали. Помимо приведенных существует еще несколько цельных шиповых соединений: «ласточкин хвост» (рис. 1, ), зубчатое соединение (рис. 1).
Кроме повышения прочности изделия шиповое соединение может применяться с целью повышения полезного выхода. На рисунке показан мебельный щит с сучками и без сучков.
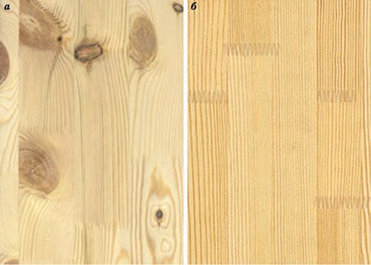
Мебельный щит без сучков имеет лучший внешний вид по сравнению с предыдущим.
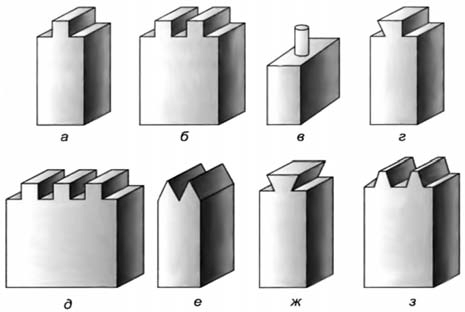
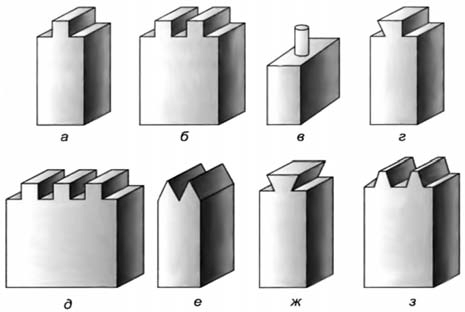
Рис. 1 Виды шипов: а — одинарный; б — двойной; в — круглый; г — односторонний «ласточкин хвост»; д — многократный; , е,ж — «ласточкин хвост»; з — зубчатый.
Как известно, существуют различные виды пороков строения древесины, которые могут значительно ухудшить внешний вид изделия. К ним относят сучки, трещины, обзол и др. (рис. 2). Эти пороки выпиливают (рис. 3), фрезеруют шиповое соединение (рис. 4), оставшиеся части брусков сращивают по длине. Зубчатый шип некоторым образом зрительно ухудшает внешний вид, поэтому такие детали применяются под покраску (рис. 5).
Склеивание короткомерных пиломатериалов из массивной древесины по длине позволяет повысить полезный выход. Склеивание в торец характеризуется низкой прочностью (менее 10% прочности натуральной древесины) и поэтому не применяется. Склеивание на ус (рис. 6) является достаточно прочным соединением. Однако при этом требует большой длины шипа и как следствие увеличения расхода материала. Склеивание на зубчатый шип (рис. 6) наиболее предпочтительно, так как обеспечивает 50–60% прочности от цельной древесины.
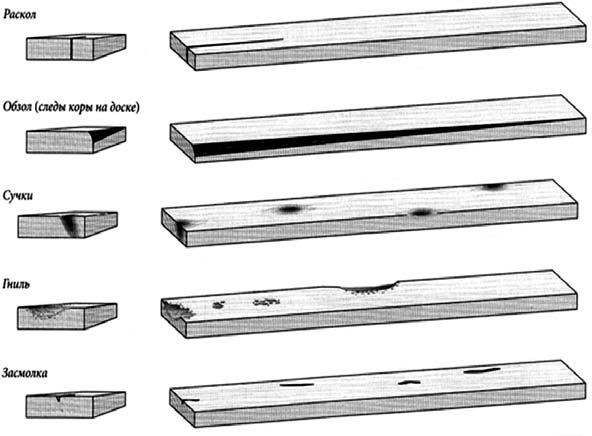
Рис. 2 Пороки строения древесины в пиломатериалах
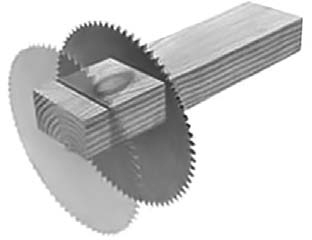
Рис. 3 Схема удаления пороков
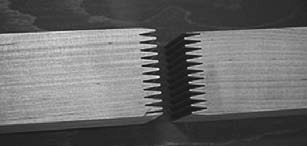
Рис. 4 Зубчатое шиповое соединение
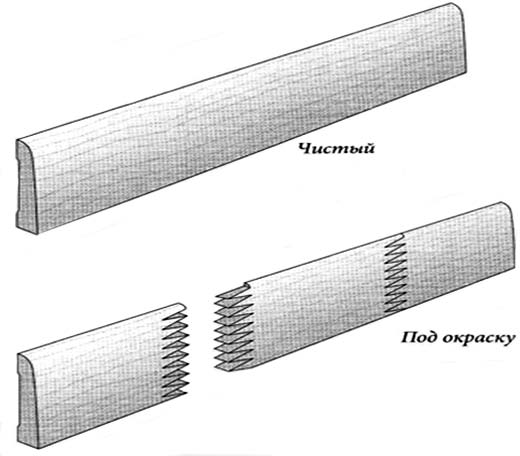
Рис. 5 Склеивание по длине
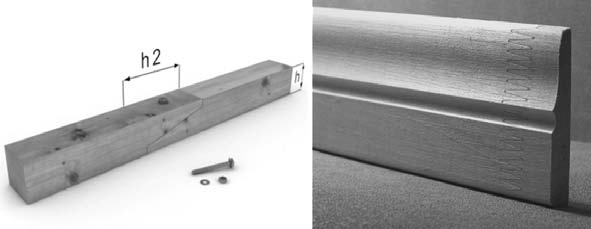
Рис. 6 Виды зубчатого шипового соединения: а — склеивание на ус; б — склеивание на зубчатый шип.
1.2. Параметры зубчатого шипового соединения
Горизонтальные шипы применяются в соединениях, не требующих высоких прочностных свойств, вертикальные шипы — в конструкционных соединениях.
Зубчатое соединение характеризуется шагом, длиной и величиной затупления (рис. 7).
Зазор необходим для удаления излишков клея. Длина шипа выбирается в зависимости от назначения (обшивка, наличник — 5 мм; настил — 30 мм).
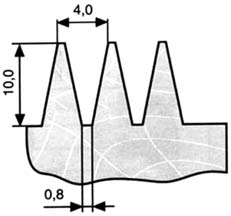
Рис. 7 Параметры зубчатого шипа
Вид применяемого при склеивании клея выбирается в зависимости от назначения. Поливинилацетатные, карбамидоформальдегидные и казеиновые клеи применяются при изготовлении изделий, эксплуатируемых внутри помещений; фенолоформальдегидные — для изделий, эксплуатируемых снаружи помещений.
Формирование шипа производится в два этапа: выравнивание поверхности (чистовая торцовка) и фрезерование шипа на фрезерных или шипорезных станках. С противоположной стороны бруска шаг зубчатого соединения должен быть смещен на полшага.
1.3. Технология склеивания по длине
Склеивание заготовок по длине выполняется в следующей последовательности. Вначале производится продольный раскрой на многопильных станках. Затем поперечный раскрой на кратные заготовки с удалением дефектных мест (рис. 8).
Для фрезерования зубчатого шипа применяются фрезы (рис. 9).
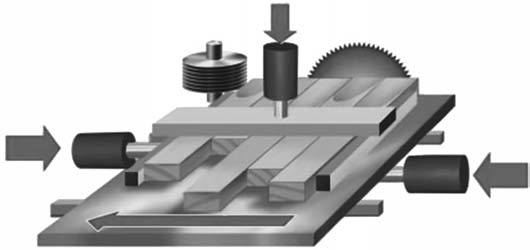
Рис. 8 Выпиливание дефектных мест
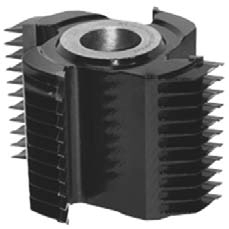
Рис. 9 Фреза для фрезерования зубчатого шипа
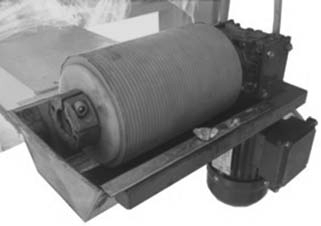
Рис. 10 Клеевые вальцы
Нанесение клея может быть осуществлено кистью, окунанием или гребенчатыми клеевыми вальцами (рис. 10). Расход клея составляет до 400 г/м2.
Лучшим способом является склеивание брусков бесконечной длины с последующим их раскроем на требуемый размер (см. рис. 11).
Сборка и запрессовка производится в пневматических или гидравлических ваймах (см. рис. 12). Горизонтальное давление обеспечивает плотный контакт зубчатого соединения. А вертикальное давление создается для предотвращения выгибания заготовки.
Продолжительность запрессовки с выдавливанием излишков клея составляет 2 с. Отверждение клея происходит вне установки. Сила и надежность самозаклинивания достаточны для раскроя сразу после склеивания. Прочность склеивания характеризуется пределом прочности при статическом изгибе.
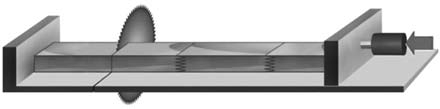
Рис. 11 Схема сращивания брусков с последующим их раскроем на требуемый размер
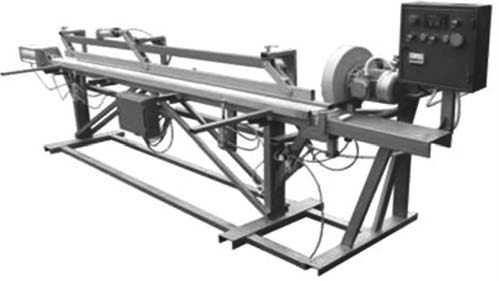
Рис. 12 Вайма для склеивания на зубчатый шип
2. Технология изготовления мебельных щитов
2.1. Схема технологического процесса изготовления мебельных щитов из массивной древесины
Мебельный щит склеивается из деревянных строганых брусков (реек) шириной от 10 до 50 мм. При изготовлении мебельных щитов применяется древесина хвойных и лиственных пород. Мебельные щиты применяются при изготовлении столярно-строительных изделий, деталей интерьера, но чаще всего в мебельном производстве.
Схема технологического процесса изготовления мебельных щитов из массивной древесины представлена на рисунке 13.
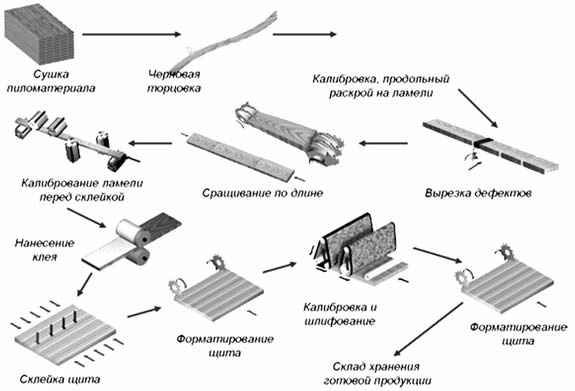
Рис. 13 Схема технологического процесса изготовления мебельного щита
Для склеивания мебельных щитов используют бруски (ламели), из которых удалены дефекты и сращенные по длине. Нанесение клея на поверхность производят ручным способом (рис. 14) или при помощи клеевых вальцов.
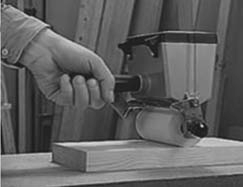
Рис. 14 Нанесение клея ручным способом
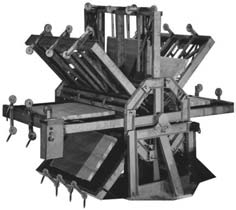
Рис. 15 Веерная вайма с механическим зажимом
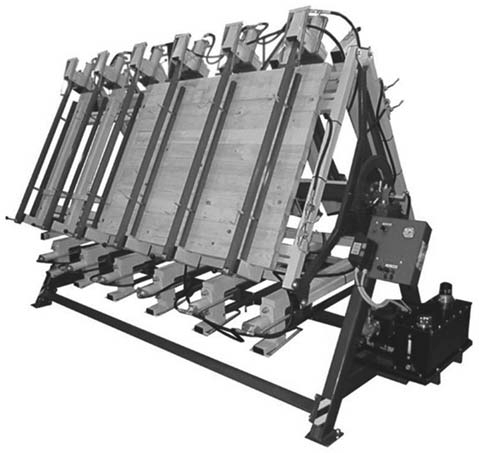
Рис. 16 Ваймы с гидравлическим зажимом
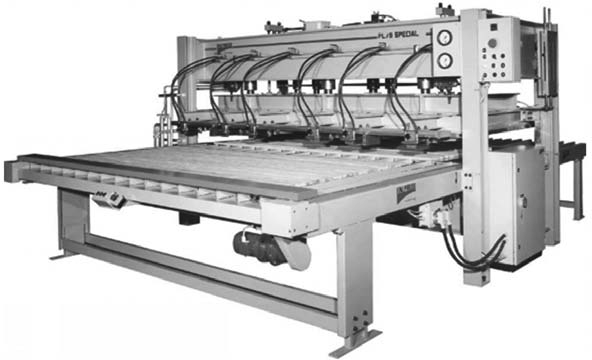
Рис. 17 Одноэтажный гидравлический пресс для склеивания мебельных щитов
Для склеивания могут применяться ваймы, в которых зажим брусков с нанесенным клеем механический. Для увеличения производительности их делают веерными (см. рис. 15). При склеивании щитов также могут применяться ваймы (прессы) с гидравлическим зажимом (рис. 16). Склеенные в ваймах бруски могут быть смещены относительно друг друга, что потребует выравнивания поверхности щитов в рейсмусовых станках.
Этого недостатка лишены щиты, склеенные в одно( этажных гидравлических прессах (рис. 17).
Поверхность щитов получается более ровной, и в этом случае не требуется обработка в рейсмусных станках. Для уменьшения продолжительности склеивания плиты пресса выполнены обогреваемыми. При изготовлении мебельных щитов необходимо соблюдать следующие правила.
- Склеиваемые бруски для предотвращения коробления должны собираться «вразбежку» (в соседних брусках направление волокон не должно совпадать).
- Ширина брусков должна быть кратной двум-трем толщинам = (2–3).
- Промежуток времени от нанесения клея на поверхность до склеивания не должен превышать 5 мин.
- Боковые поверхности реек для предотвращения появления щелей между ними должны быть строго перпендикулярны пласти.
- Склеиваемые бруски не должны быть покоробленными и их желательно склеивать сразу после строгания.
- Влажность древесины должна быть 8 ± 2%.
- Расход клея 180–220 г/м2. После склеивания щи( тов должна быть предусмотрена технологическая выдержка в плотных стопах в течение 5–24 ч.
- В верхних щитах пачки могут подсыхать верхние слои после склеивания. Для предотвращения коробления верхних щитов всю пачку необходимо укрывать полиэтиленом.
- Щиты длиной более 2 м подвергаются короблению в большей степени, чем короткие, к тому же их труднее обрабатывать. Поэтому лучше склеивать заготовки не( больших размеров.
2.2. Форматная обрезка и шлифование мебельных щитов
После склеивания производится обрезка мебельных щитов по формату (рис. 18) на форматно-обрезных станках. Для предотвращения образования сколов на поверхности щита в обрезных станках должны быть установлены подрезатели (рис. 19).
Готовые плиты имеют значительную разнотолщинность. Кроме того, на поверхности плит могут быть раз, личные дефекты — вмятины, загрязнения и т. д. По, этому после склеивания и выдержки щитов производят шлифование их поверхности на широколенточных шлифовальных станках. Обработка производится шлифовальными лентами разной зернистости в два этапа (рис. 20).
Вначале шлифовальными лентами более крупной зернистости снимают примерно 70% от величины припуска (калибруют), затем лентами с более мелкой зернистостью снимают оставшийся припуск (рис. 21). На первом этапе шлифования применяют отечественные шлифовальные ленты с номером зернистости 40–50, импортные — 36–40. На втором этапе шлифования применяют ленты с номером зернистости отечественные 16–25, им, портные — 80–100. Общий припуск на шлифование составляет 1–2 мм.
Сортируют плиты в зависимости от количества и видов дефектов строения древесины на поверхности (рис. 22) и от дефектов обработки поверхности. Качество склеивания оценивают по прочности при скалывании по клеевому слою (не менее 4 МПа).
Также контролируют предел отклонения размеров разных длин диагоналей, шероховатость, покоробленность. Качественные показатели мебельных щитов регламентируются требованиями заказчика или нормативных документов. Хранят плиты в сухих отапливаемых помещениях.
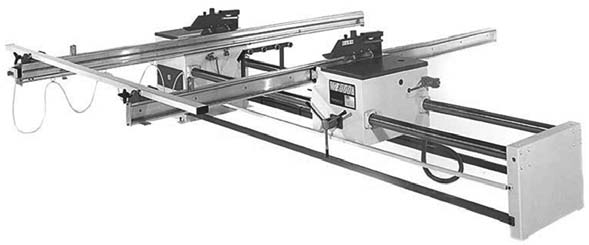
Рис. 18 Форматно-обрезной станок для обрезки кромок по формату
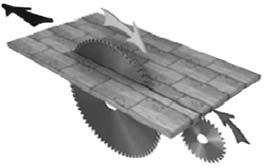
Рис. 19 Применение подрезателей при обрезке щитов
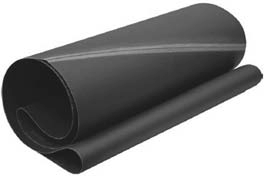
Рис. 20 Широкие шлифовальные ленты для обработки поверхности мебельных щитов
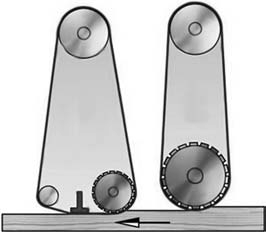
Рис. 21 Схема двухэтапной обработки мебельных щитов в шлифовальных станках
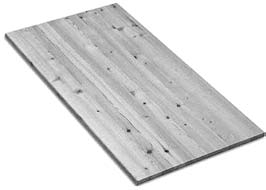
Рис. 22 Мебельный щит
3. Клееные деревянные конструкции
3.1. Преимущества клееных деревянных конструкций
Клееные деревянные конструкции применяют при изготовлении конструкций и изделий строительного назначения.
Благодаря легкости, прекрасным эстетическим и теплотехническим свойствам, высокой прочности и огнестойкости клееная древесина все чаще используется в объектах строительства и реконструкции. С ее применением можно создавать покрытия зданий различного назначения пролетами до 100 м. Богатый опыт применения этого материала позволяет использовать его в строительстве как жилых, так и производственных или общественных зданий любой сложности.
Несмотря на то что клееные деревянные конструкции являются достаточно новым материалом, они могут беспрепятственно применяться не только в малоэтажном домостроении, но и в таких социально значимых объектах, как спорткомплексы, аквапарки, торговые центры, мосты. Естественно, проекты должны соответствовать всем существующим строительным нормативам и требованиям. Если есть какие%то отступления, то в проекте могут быть предусмотрены компенсирующие мероприятия (покрытие конструкций защитными пропитками) или разработка специальных технических условий.
Для изготовления клееных деревянных конструкций применяют древесину хвойных и лиственных пород. Породу древесины определяют по назначению и условиям эксплуатации конструкций. Для изготовления несущих конструкций используются в основном пиломатериалы хвойных пород (сосна, ель, лиственница) не ниже II сорта по ГОСТ 1713%2007. Для изготовления ненесущих конструкций используются в основном пиломатериалы хвойных пород (сосна, ель, лиственница) не ниже III сорта по ГОСТ 1713-2007.
Безопасность и долговечность деревянных клееных конструкций в определенной степени зависит от типа и марки применяемого клея, его эксплуатационных и технологических свойств. К основным эксплуатационным свойствам клеев, применяемых в производстве клееной древесины, относят прочность клеевого соединения, т. е. его способность сохранять прочность в течение заданного срока эксплуатации изделий; эластичность клеевого соединения; водостойкость как способность клеевого соединения сохранять прочность после длительного или интенсивного воздействия воды на изделия; морозостойкость, биостойкость, температуро- и пожаростойкость, т. е. способность клея сохранять прочность при воздействии высоких температур и открытого огня. Клеевые системы характеризуются разнообразием композиций смол с различными свойствами, используемых отвердителей и наполнителей, способами нанесения клея.
При выборе средств и способов защиты деревянных клееных конструкций основное внимание должно быть обращено на предохранение их от переменного увлажнения и высушивания. При соблюдении требований конструкционной профилактики вероятность выхода из строя деревянных клееных конструкций массивного сечения в зданиях в результате биоразрушения столь незначительна, что подвергать их биозащитной обработке, как правило, не требуется.
По функциональному назначению средств для обработки клееных деревянных конструкций можно разделить на четыре основные группы:
- декоративные;
- влагозащитные;
- биозащитные;
- огнезащитные.
На практике часто приходится сталкиваться с необходимостью проведения комплексной и комбинированной обработки клееной древесины. Например, если в процессе эксплуатации не исключено увлажнение древесины, способное привести к появлению грибов, то необходимо предусмотреть защиту клееных деревянных конструкций не только от биоразрушения, но и от увлажнения.
В ряде случаев помимо биовлагозащитной обработки по требованиям пожарной безопасности необходима огнезащита клееных деревянных конструкций. Для защиты торцов массивных клееных элементов от увлажнения и расслаивания при эксплуатации в условиях повышенной или переменной влажности используют гидроизолирующие мастичные составы.
Применению клееной древесины в качестве конструкционного материала способствует целый ряд ее свойств:
- малая собственная масса при высокой прочности;
- высокая заводская готовность конструкций;
- технологичность изготовления изделий различных габаритов и форм; простота сборки и обработки конструкций на строительной площадке;
- восполняемость сырьевой базы.
В гражданском строительстве клееные деревянные конструкции привлекают возможностью создания разнообразных конструктивных схем, в том числе пространственных.
Важным отличием деревянных клееных конструкций от железобетонных и металлических является простота изготовления индивидуальных изделий. В гражданских зданиях типа спортзалов, крытых рынков, манежей, павильонов использование клееных деревянных конструкций снижает вес покрытия в 4–5 раз, трудоемкость монтажа до 20%, расход стали до 50%.
Достоинство деревянных клееных конструкций — возможность создания конструкций практически любых размеров и форм. Однако проектирование и изготовление оригинальных конструкций целесообразно лишь для отдельных зданий и сооружений, в том числе уникальных по размерам или по техническому решению. В остальных случаях следует использовать унифицированные конструкции и их элементы, более доступные для серийного изготовления.
3.2. Технологический процесс изготовления клееных деревянных конструкций
Схема технологического процесса изготовления клееных деревянных конструкций приведена в таблице 1.
Технологический процесс изготовления клееного бруса для несущих конструкций рассмотрим на примере предприятия «Нижегородский деревообрабатывающий комбинат» ДОК-78.
Таблица 1. Схема технологического процесса изготовления клееных деревянных конструкций
Технологический процесс производства клееного бруса начинается на складе, где осуществляется сортировка лесоматериалов хвойных пород, после чего производится изготовление на лесопильном станке обрезных пиломатериалов (рис. 23).
Далее производится сушка пиломатериалов в сушильных камерах с автоматическим программированием управления, функциями нагрева, вентиляции и увлажнения (рис. 24).
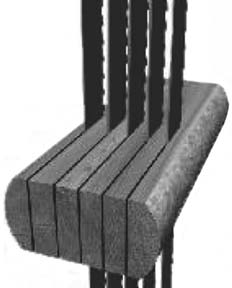
Рис. 23 Изготовление обрезных пиломатериалов
Четырехсторонний станок продольного фрезерования обрабатывает стороны ламелей для придания правильных геометрических размеров и вскрытия дефектов (см. рис. 25). Из станка выходят гладкие заготовки требуемых размеров прямоугольного сечения с прямой кромкой.
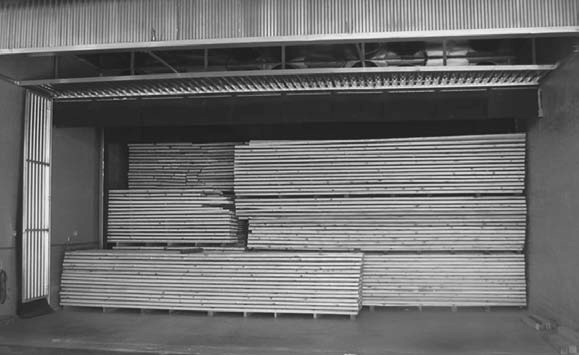
Рис. 24 Сушилка с пакетами пиломатериалов
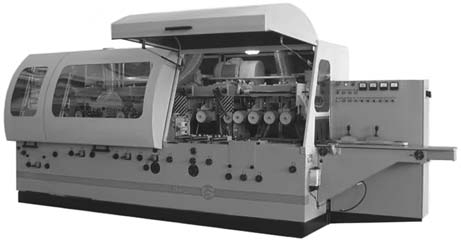
Рис. 25 Четырехсторонний строгальный станок
Автоматический торцовочный станок линии оптимизации осуществляет вырезку промаркированных оператором пороков в автоматическом режиме. Пороки маркируются флуоресцентным мелом, который распознается расположенной на пиле камерой. При наличии трещин на торцах досок они автоматически выпиливаются без предварительной маркировки. Отходы отбрасываются, а кондиционные заготовки направляются к линии сращивания в длину на зубчатый шип.
На линии сращивания сначала фрезеруют на торцах заготовки зубчатый шип, а затем наносят на них клей и прессуют заготовки в доску или балку бесконечной длины, которая затем торцуется на требуемые размеры. После чего производится технологическая выдержка для отверждения клея продолжительностью до 8 ч в зависимости от вида клея.
Четырехсторонний станок продольного фрезерования осуществляет строгание ламелей с верхней и нижней пластей детали.
Клеенаносящий станок (рис. 26) осуществляет нанесение клея на поверхность детали, после чего заготовки подаются в пресс для склеивания (рис. 27).
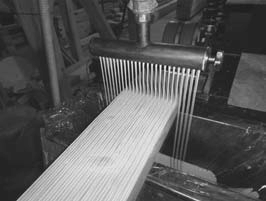
Рис. 26 Нанесение клея на поверхность детали
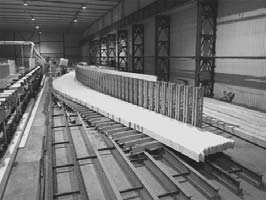
Рис. 27 Пресс для склеивания клееных деревянных конструкций
Режим прессования:
- температура помещения, °C 16;
- температура клея, °C 18 ± 1;
- жизнеспособность клея, ч 2–4;
- расход клея, г/м2 250–350;
- время открытой выдержки (от нанесения клея до сборки), мин 10;
- время закрытой выдержки (от сборки до запрессовки), мин 30;
- давление, МПа 3–5;
- время прессования, ч 8–10;
- время выдержки после запрессовки, ч 8. Транспортировка склеенных заготовок осуществляется цеховым краном.
Станок продольного фрезерования балок выполняет двух- или четырехстороннюю обработку прямых или гнутых балок с фаской или без. В настоящее время для этих целей используются станки с рабочей шириной от 400 до 2600 мм. При производстве только прямых балок перед и после станка должен располагаться роликовый транспортер, для прямых и гнутых балок необходима подвижная тележка, так как сам строгальный станок установлен на поворотном круге и поворачивается в зависимости от радиуса балки. Укладка детали перед станком и съем ее после обработки осуществляется с помощью крана, а для небольших изделий — с помощью штабелеукладчика.
К оборудованию для завершающих операций относятся станок для торцовки и раскроя балок и бруса и обрабатывающий центр. Также требуется многочисленный ручной инструмент, применяющийся для формирования различных врезок, сверления и фрезерования, необходимого для строительных конструкций.
С помощью толкателя брус роликовым транспортером направляется в торцовочный станок, где сначала производится врезание, а затем балка раскраивается на длины в соответствии с заданной программой.
Операция упаковки необходима для защиты балок при транспортировке от загрязнения и влажности. Обычно изделия оборачивают пленкой (стандартными считаются сечения от 6×12 до 16×36 см и длиной 12–18 м) и затем укладывают на склад временного хранения.
Для защиты от увлажнения и разрушения клеевого слоя на торцовые поверхности конструкции наносят эпоксидную шпатлевку на рабочем месте.
Режим нанесения шпатлевки:
- температура воздуха, °C 18–20;
- относительная влажность, % 65–75;
- расход шпатлевки, кг/м2 1,9.
Следующей операцией по изготовлению клееных конструкций является отделка, которая осуществляется на отделочных участках. Конструкции укладываются в пакеты и с помощью крана подаются на транспортные тележки и удаляются из цеха для дальнейшей обработки. Обрезки, стружка, опилки удаляются с помощью пневматического транспорта.
4. Технология клееного бруса
4.1. Область применения клееного бруса
Изготовление деталей строительного назначения из клееного бруса значительно улучшает прочностные и эксплуатационные характеристики изделий. Балки из клееного бруса используются при устройстве полов, крыш и потолков (рис. 28). Также из клееного бруса изготавливаются стены (рис. 29).
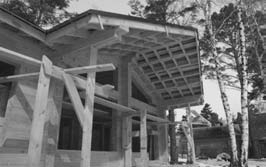
Рис. 28 Применение клееного деревянного бруса в деревянном домостроении
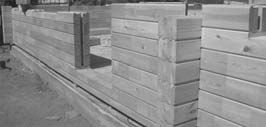
Рис. 29 Стены дома из клееного бруса
Клееный брус применяется при изготовлении деревянных окон (рис. 30).
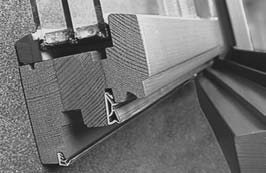
Рис. 30 Применение клееного бруса при изготовлении окон
4.2. Основные операции технологического процесса изготовления клееных деревянных конструкций
Схема технологического процесса изготовления клееных деревянных конструкций приведена на рисунке 31. Технологический процесс изготовления клееного бруса состоит из следующих основных операций (рис. 32–41):
- поперечный раскрой пиломатериалов и вырезка дефектных мест на торцовочном станке;
- фрезерование зубчатого шипа;
- склеивание заготовок по длине;
- предварительная торцовка пиломатериала на торцовочном станке;
- строгание ламелей с четырех сторон на четырехстороннем строгальном станке;
- нанесение клея на поверхность ламелей;
- склеивание заготовок на гидравлическом вертикальном прессе;
- фрезерование профиля заготовки;
- чистовая торцовка в размер;
- выпиливание или фрезерование пазов под сборочные элементы;
- упаковка.
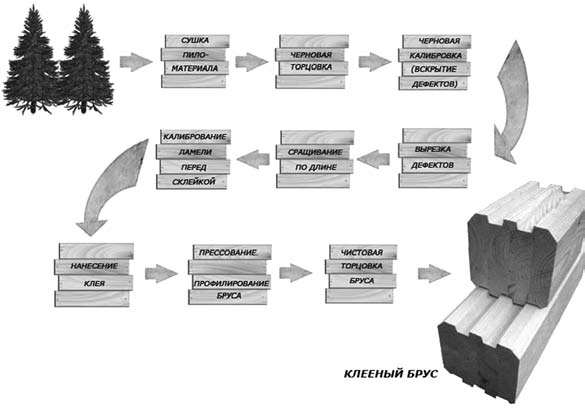
Рис. 31 Схема технологического процесса изготовления клееных деревянных конструкций
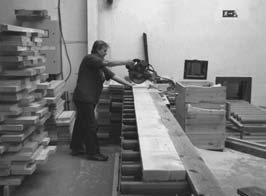
Рис. 32 Поперечный раскрой пиломатериалов на торцовочном станке
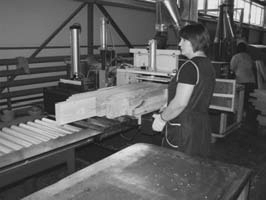
Рис. 33 Торцовка и вырезка дефектных мест
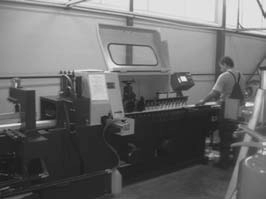
Рис. 34 Склеивание заготовок по длине на линии сращивания
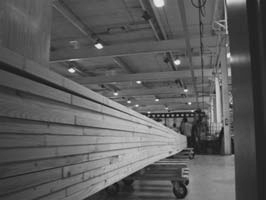
Рис. 35 Фрезерование ламелей с четырех сторон
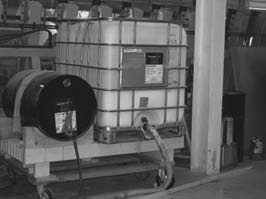
Рис. 36 Нанесение клея на поверхность ламелей на четырехстороннем строгальном станке
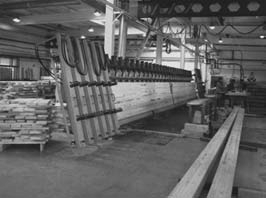
Рис. 37 Склеивание заготовок на гидравлическом вертикальном прессе
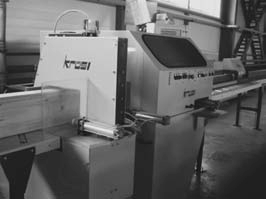
Рис. 38 Фрезерование профиля заготовки на четырехстороннем строгальном станке
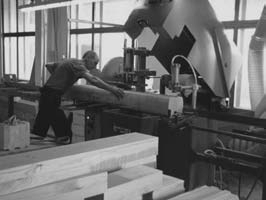
Рис. 39 Чистовая обрезка в размер
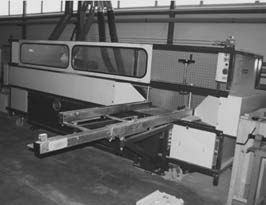
Рис. 40 Выпиливание углов
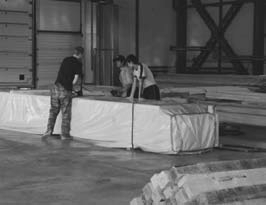
Рис. 41 Упаковка деталей клееного бруса
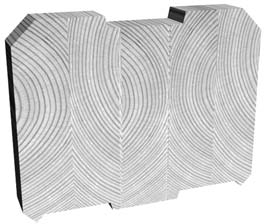
Рис. 42 Схема сборки ламелей клееного бруса «вразбежку»
При изготовлении клееного бруса необходимо учитывать возможность появления коробления в процессе эксплуатации. Для уменьшения вероятности коробления клееного бруса в процессе эксплуатации сборка заготовок должна производиться таким образом, чтобы направления волокон в смежных ламелях не совпадали (рис. 42).
Просмотров: 1 069
Способы соединения мебельных щитов. Соединения деревянных щитов под углом. Как сделать глухие лицевые соединения, используя разметчик центра шипа
Поиск по сайту:
До создания современных технологий и фурнитуры, мебель изготовлялась плотниками. В качестве крепежей для соединения панелей между собой использовались замковые соединения, шипы, шканты, клинья, эта же «фурнитура» применялась при строительстве деревянных домов и т.д.
Для жесткости соединений использовали клей, естественно, ни о какой идеальной точности в соединениях не было и речи. Только виртуоз, орудуя такими инструментами, как пила, стамеска, мог более менее точно выдержать размеры.
Сейчас такие соединения деталей специально используются для того, чтобы придать мебели стиль «под старину». В этой статье описаны основные крепежи и фурнитура, которые используются в которые используются в , и т.д.
Этот тип крепления редко используется как самостоятельный, его применяют только для придания жесткости совместно с эксцентриковыми стяжками.
Главная его функция — препятствование смещению панелей относительно друг к другу и придании дополнительной жесткости креплению. Используется совместно с эксцентриковой стяжкой. Производится он из жестких пород натурального дерева, имеет цилиндрическую форму. Это очень простая и дешевая деталь, которая используется в деревянных соединениях с незапамятных времен.
Винтовая стяжка
Винтовая стяжка состоит из винта и бочонка, они используются крепления торца одной панели к пласти другой. Например: крепление полки к боковой панели.
Это очень прочное крепление за счет большого хода стягивания. Единственным недостатком этого крепежа является видимость головки винта с лицевой стороны панели.
Можно, конечно, их закрыть специальными заглушками, но это тоже не панацея. Заглушки на внешней панели шкафа смотрятся не эстетично.
Для установки этого вида крепежа необходимы навыки, новички могут столкнуться с такой проблемой, как совмещение отверстий бочонка с отверстием в торце полки, да и вытащить из своего гнезда не нужный бочонок не так просто.
Но неудобства при сборке и эстетическая погрешность с лихвой компенсируется надежностью и долговечностью соединения. соединения!
Стяжка коническая
Коническая стяжка часто используется для крепления толстых панелей Дсп (25 мм, 38 мм)
Один из его плюсов- отсутствие видимых шляпок с лицевой стороны панелей. В отличии от винта в винтовой стяжке, шток используемый в конической стяжке вкручивается в панель. У самой стяжки – 2 отверстия одно – для штока, которое вкручивается в пласт панели, второе для винта конической стяжки.
Недостатком этого вида крепежа является не большой ход стягивания, при больших нагрузках со временем могут расшататься отверстия под винт штока, тогда стяжка просто перестанет работать!
Мебельный уголок
Довольно простой вид крепежа, прост в установке. Не требует никаких дополнительных отверстий в панелях для его установки. Бывают как металлические, так и пластиковые варианты.
Довольно прочный вид крепления и недорогой по цене. Из недостатков – он виден и выглядит не эстетично, особенно из пластика. Но это основной вид крепления во встроенной мебели, так как эксцентрики и евровинты используют только для крепления полок ДСП между собой.
Евровинт
Этот крепеж чаще используется для сборки модулей кухонной мебели и в мебели класса эконом. Так же, как и у винтовой стяжки, с лицевой стороны боковой панели шкафа видны шляпки евровинта, либо заглушки.
Он вкручивается в торец полки с предварительно просверленным отверстием. Эта стяжка также относится к классу эконом. Для ее установки просверливаются 2 отверстия- в торец полки и в пласть детали. Крепятся они перпенд