Автоклавный газобетон — Википедия
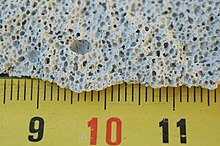
Автоклавный газобетон (АГБ), Autoclaved aerated concrete (AAC), также известный как автоклавный ячеистый бетон, автоклавный легкий бетон, автоклавный бетон, ячеистый бетон, пористый бетон, Aircrete, Hebel Block и Ytong (Итонг), СИБИТ (Сибирский Итонг) — легкий, сборный, пенобетонный строительный материал, изобретённый в середине 1920-х годов, который одновременно обеспечивает устойчивую структуру, звукоизоляцию и огнестойкость, устойчивость к плесени. Продукты автоклавного газобетона включают блоки, стеновые панели, напольные и кровельные панели, облицовочные (фасадные) панели и перемычки[1].
АГБ был создан в середине 1920-х годов шведским архитектором и изобретателем доктором Йоханом Акселем Эрикссоном[2], работающим с профессором Хенриком Крюгером в Королевском технологическом институте. Этот процесс был запатентован в 1924 году. В 1929 году производство началось в Швеции в городе Йххульт. Из «Yxhults Ånghärdade Gasbetong» позже стал первым зарегистрированным брендом строительных материалов в мире: Ytong. Другой бренд «Siporex» был создан в Швеции в 1939 году и в настоящее время лицензирует и владеет заводами в 35 точках по всему миру. Второй крупный международный ячеистый бетонный бренд Hebel восходит к основоположнику компании Йозефу Хебель из Меммингена. В 1943 году в Германии был открыт первый завод Hebel.
В 1978 году шведская команда Siporex Sweden открыла завод Siporex в Королевстве Саудовская Аравия — «Легкая строительная компания — Siporex — LCC SIPOREX», которая в большинстве своём поставила Ближний Восток, Африку и Японию. LAMP SIPOREX FACTORY работает более 40 лет. Сегодня газобетон производится многими компаниями, особенно в Европе и Азии. В Америке есть производство, а в Африке есть один завод в Египте. Производство АГБ в Европе значительно замедлилось, но промышленность быстро растет в Азии из-за сильного спроса на жилье и коммерческое пространство. В настоящее время Китай является крупнейшим в мире рынком бетона с несколькими сотнями заводов. Китай, Центральная Азия, Индия и Ближний Восток являются самыми большими с точки зрения производства и потребления АГБ [3].
Продукт aircrete продается, как и другие материалы для кладки, под разными торговыми марками. Ytong и Hebel являются брендами международной операционной компании Xella со штаб-квартирой в Дуйсбурге. Другими всемирно известными торговыми марками в Европе являются H + H Celcon (Дания) или Solbet (Польша). В России это марки СИБИТ (Сибирский Итонг), Бетолекс, Бонолит, Аэроблок и другие.
АГБ — это высоко термически изолирующий бетонный материал, используемый как для внутренней, так и для внешней конструкции. Изолирующая способность АГБ является одним из его преимуществ в строительстве. Он быстро кладется, поскольку материал может быть отшлифован или отрезан по размеру на месте с использованием стандартных электроинструментов из углеродистой стали.
АГБ хорошо подходит для городских районов с высотными зданиями и с высокими температурными колебаниями. Из-за своей плотности, высотные здания, построенные с использованием АГБ, требуют меньше стали и бетона для конструктивных элементов. Требование раствора для укладки блоков АГБ уменьшается из-за меньшего количества соединений. Повышенный тепловой КПД АГБ делает его пригодным для использования в районах с экстремальными температурами, поскольку он устраняет необходимость в отдельных материалах для строительства и изоляции, что приводит к более быстрому строительству и экономии затрат.
Материалы АГБ могут быть покрыты штукатуркой или штукатуркой для защиты от элементов или покрыты сайдинговыми материалами, такими как кирпич или винил.
Когда АГБ смешивают, происходит несколько химических реакций, которые дают АГБ его легкий вес (20% от веса бетона) и тепловые свойства. Алюминиевый порошок реагирует с гидроксидом кальция и водой с образованием водорода. Водородный газ пенится и удваивает объем сырьевой смеси, создавая пузырьки газа диаметром до 3 мм. В конце процесса вспенивания водород выходит в атмосферу и заменяется воздухом.
Когда слегка затвердевшая смесь извлекается из формы-ванны, они твердые, но всё ещё мягкие. Затем его разрезают струнами на блоки или панели и помещают в автоклавную камеру в течение 12 часов. Он упрочняется давлением пара, когда температура достигает 190 °C (374 °F), а давление достигает 8-12 бар, кварцевый песок реагирует с гидроксидом кальция с образованием гидрата силиката кальция, что даёт АГБ его высокую прочность и другие уникальные свойства , Из-за относительно низкой температуры используемые блоки АГБ не считаются обжигом, а легким бетонным кирпичным блоком. После процесса автоклавирования материал готов к немедленному использованию на строительной площадке. В зависимости от его плотности до 80% объема блока АГБ представляет собой воздух. Низкая плотность АГБ также объясняет низкую структурную прочность на сжатие. Он может выдерживать нагрузку до 8, что составляет примерно 50% от прочности на сжатие обычного бетона.
В 1978 году был открыт первый материал АГБ в государстве Персидского залива Королевства Саудовская Аравия — LCC SIPOREX — облегчённая строительная компания, поставляющая странам GCC аэрированные изделия из блоков и панелей.
С 1980 года во всем мире растет использование материалов АГБ. В Австралии, Бахрейне, Китае, Восточной Европе, Индии и Соединённых Штатах строятся новые производственные предприятия. АГБ все чаще используется разработчиками, архитекторами и домашними строителями по всему миру.
АГБ выпускается более 70 лет, и он предлагает несколько существенных преимуществ по сравнению с другими материалами для строительства, одним из наиболее важных из которых является его меньшее воздействие на окружающую среду.
- Повышенная тепловая эффективность уменьшает нагрузку на отопление и охлаждение зданий.
- Пористая конструкция обеспечивает превосходную огнестойкость.
- Минимизация образования твердых отходов во время использования из-за легкого разрезания.
- Эффективность ресурсов снижает воздействие на окружающую среду на всех этапах его жизненного цикла, от переработки сырья до утилизации отходов.
- Легкий вес экономит затраты и энергию при транспортировке, затратах на рабочую силу и увеличивает шансы на выживание во время сейсмической активности[3].
- Блоки большего размера приводят к более быстрой кладке.
- Снижает стоимость проекта.
- Экологичность: при использовании он помогает сократить не менее 30% отходов окружающей среды, в отличие от традиционного бетона. Снижается 50% выбросов парниковых газов. Когда это возможно, использование автоклавного газобетона является лучшим выбором для окружающей среды.
Энергосбережение: это отличное свойство, которое делает его отличным изолятором, а это означает. Когда он используется, обычно нет необходимости в дополнительной изоляции.- Огнестойкость: как и в случае обычного бетона, АГБ огнестойкий. Этот материал полностью неорганичен и не горюч.
- Отличная вентиляция: этот материал очень воздушный и позволяет рассеивать воду. Это уменьшит влажность внутри здания. АГБ будет поглощать влагу и высвобождать влагу; это помогает предотвратить конденсацию и другие проблемы, связанные с плесенью.
- Нетоксичен: в автоклавном газобетоне отсутствуют токсичные газы или другие токсичные вещества. Он не привлекает грызунов или других вредителей и не может быть поврежден ими.
- Легкий: бетонные блоки, изготовленные из АГБ, составляют около одной пятой типичного бетона. Они изготавливаются в размерах, которые легко обрабатываются для быстрого возведения здания.
- Точность: панели и блоки из автоклавного газобетона производятся до нужных размеров, прежде чем они покинут завод. Существует меньше потребности в обрезке на месте. Так как блоки и панели так хорошо совмещены, существует сокращение использования отделочных материалов, таких как раствор.
- Долговечность: жизнь этого материала расширяется, поскольку на него не влияют суровый климат или экстремальные изменения в погодных условиях.
- Быстрая сборка: поскольку это легкий материал и он прост в работе, сборка намного.
- Хрупкая природа: с ними необходимо обращаться аккуратно, в отличие от глиняного кирпича, чтобы избежать поломки.
- Крепления: для блоков требуются более длинные и более тонкие винты при установке шкафов и настенных накладок.
- Влага: легко подвергается увлажнению, но в то же время легко способен отдавать влагу. В связи с этим, стены из газобетона в местах с интенсивным увлажнением нуждаются в защите от воздействия влаги, как внутри, так и снаружи.
Газобетон — Википедия
Газобетонные блокиПри производстве этого материала используются цемент, кварцевый песок и специализированные газообразователи, также, в состав смеси при его изготовлении иногда добавляют гипс, известь, промышленные отходы, такие, как, например, зола и шлаки металлургических производств.
Газообразование в замешенной на воде смеси обусловлено взаимодействием газообразователя, обычно мелкодисперсного металлического алюминия со сильнощелочным цементным или известковым раствором, в результате химической реакции образуются газообразный водород, вспенивающий цементный раствор, и алюминаты кальция.
Пылевидный алюминий неудобен для применения при замешивании раствора, так как сильно пылит. Поэтому в качестве специализированных газообразователей используются алюминиевые пасты и суспензии.
Типичный цикл производства газобетона: Перемешанные сухие ингредиенты смешиваются с водой, раствор заливается в форму. Происходит реакция щелочного водного раствора гидроксида кальция и газообразователя, приводящая к выделению водорода, который и «вспучивает» смесь. Смесь увеличивает объём и вспучивается как тесто. После предварительного схватывания цементного раствора, монолит извлекают из формы и разрезают на заготовки блоков, плит, панелей. После этого разрезанные заготовки подвергают обработке водяным паром в автоклаве для придания им окончательной прочности, либо высушиваются в электроподогреваемых сушильных камерах.
Газобетон легко обрабатывается: пилится, сверлится, строгается обычными стальными инструментами, даже без твердосплавных напаек. В него легко забиваются гвозди, скобы, установочные изделия. Со временем в процессе карбонизации прочность может уменьшаться на 20-30% [источник не указан 109 дней].Так как пористость, а соответственно газо- и паропроницаемость современных блоков выше, то и карбонизация и старение происходит значительно быстрее указанных 15-20 лет, чем это описано в исследовании Е.С. Силаенкова. Не горюч, так как состоит только из минеральных компонентов.
Имеет меньшую естественную радиоактивность по сравнению с обычным бетоном, так как в его состав не входит гранитный щебень, слюды, — составная часть природных гранитов, которые имеют повышенную естественную радиоактивность из-за концентрации в этих минералах тория и урана.
Газобетон применяется в жилищном, коммерческом и промышленном строительстве. Основной объем потребления занимают строительные (стеновые и перегородочные блоки), также применяются армированные изделия (перемычки и плиты перекрытия).
Классификация газобетонов
- По назначению:
- конструкционные.
- конструкционно-теплоизоляционные.
- теплоизоляционные[2].
- По условиям твердения:
- автоклавные (синтезного твердения) — твердеющие в среде насыщенного пара при давлении выше атмосферного;
- неавтоклавные (гидратационного твердения) — твердеющие в естественных условиях, при электропрогреве или в среде насыщенного пара при атмосферном давлении.
- По виду вяжущих и кремнеземистых компонентов подразделяют:
- по виду основного вяжущего:
- на известковых вяжущих, состоящих из извести-кипелки более 50 % по массе, шлака и гипса или добавки цемента до 15 % по массе;
- на цементных вяжущих, в которых содержание портландцемента 50 % и более по массе;
- на смешанных вяжущих, состоящих из портландцемента от 15 до 50 % по массе, извести или шлака, или шлако-известковой смеси;
- на шлаковых вяжущих, состоящих из шлака более 50 % по массе в сочетании с известью, гипсом или щелочью;
- на зольных вяжущих, в которых содержание высокоосновных зол 50 % и более по массе;
- по виду кремнеземистого компонента:
- на природных материалах — тонкомолотом кварцевом и других песках;
- на вторичных продуктах промышленности — золе-унос ТЭС, золе гидроудаления, вторичных продуктах обогащения различных руд, отходах ферросплавов и других.
- по виду основного вяжущего:
Теплопроводность
Теплопроводность — одна из основных характеристик газобетона. Благодаря малой плотности и низкой теплопроводности, газобетон применяется в теплоизолирующих конструкциях (несущие и перегородочные стены зданий и сооружений). Теплопроводность газобетона марки D500 в сухом виде равна 0,12 Вт/м°C, в 4 раза ниже, чем у полнотелого кирпича (0,45-0,55 Вт/м°C), и несколько ниже теплопроводности дерева (0,15 Вт/м°C). Наличие влаги существенно влияет на теплопроводность газобетона, поэтому в характеристиках обычно указываются две величины — теплопроводность газобетона в сухом состоянии (обозначается λ(α)), и теплопроводность при влажности 4% — λ(β). Теплопроводность также существенно зависит от плотности газобетона: чем выше плотность, тем выше теплопроводность (так, теплопроводность газобетона марки D1000 уже 0,29 Вт/м°C), но также и прочность.
Коэффициент теплопроводности, Вт/м*°C | ||||
---|---|---|---|---|
Плотность | D300 | D400 | D500 | D600 |
Сухой газобетон | 0,072 | 0,096 | 0,112 | 0,141 |
Газобетон при влажности 5% | 0,088 | 0,117 | 0,147 | 0,183 |
История появления технологии производства автоклавного газобетона
Для придания бетону пористой структуры чех Гоффман добавил в цементные и гипсовые растворы кислоты, углекислые и хлористые соли. Соли, взаимодействуя с растворами, выделяли газ, который и делал бетон пористым. За изобретённый газобетон Гоффман в 1889 году получил патент, но дальше этого у него дело не пошло.
Замысел Гоффмана развили американцы Аулсворт и Дайер. В качестве газообразователя в 1914 году они использовали порошки алюминия и цинка. В процессе химической реакции этих порошков с гашеной известью выделялся водород, который и способствовал образованию в бетоне пористой структуры. Это изобретение оказалось столь значимым, что его и поныне считают отправной точкой технологии изготовления газобетона.
Свой вклад в дело совершенствования газобетона (газосиликата) внёс шведский архитектор и ученый Юхан Аксель Эрикссон. В своих исследованиях он пытался вспучивать раствор извести, кремнезёмистых компонентов и цемента за счёт взаимодействия этого раствора с алюминиевым порошком. Этот подход увенчался успехом. В 1929 году в местечке Иксхульт фирмой «Итонг» (Ytong) был начат промышленный выпуск газобетона. Инженерами этой фирмы за основу была взята технология тепловлажностного воздействия в автоклавах на известково-кремнезёмистые компоненты, запатентованная в 1880 году немецким профессором В. Михаэлисом. Только за первый год работы этим предприятием было произведено 14 тысяч м³ газобетона (газосиликата). Следует заметить, что фирмой «Итонг» цемент не применялся вообще.
Несколько иной метод производства газобетона внедрила в жизнь в 1934 году шведская фирма «Сипорекс» (Siporex). Он основывается на применении смеси из портландцемента и кремнезёмистого компонента. Известь в данном случае не применялась. Авторы этого метода — инженеры финн Леннарт Форсэн и швед Ивар Эклунд. Научные и практические достижения вышеперечисленных инженеров и стали впоследствии основой промышленного производства как газосиликатов, так и газобетонов во многих странах мира.
История производства ячеистых бетонов в СССР
Производство ячеистых бетонов в СССР стало активно развиваться в 1930-е годы. Автоклавные ячеистые бетоны (АЯБ) с газовой поризацией появились в промышленных масштабах к 1950-м годам. К 1960-м годам производство АЯБ стало самостоятельным развивающимся научным направлением, во многом опережающим европейские наработки в этой области.
К концу 1980-х годов в СССР из ячеистых бетонов было построено более 250 млн м² зданий различного назначения (жилых, общественных, производственных, животноводческих). При этом, несмотря на высокий уровень отечественных научных разработок, ориентиром для советской промышленности служили западно-европейские достижения (понижение плотности панелей и блоков вплоть до 300 кг/м³), основанные, в первую очередь, на стабильном сырье и оборудовании, обеспечивающем высокую однородность материала.
В 1987 г. с принятием очередной жилищной программы СССР основным средством её реализации стала научно-производственно-техническая программа «Система эффективного строительства жилых и общественных зданий из ячеистых бетонов», которая предполагала строительство около 250 новых заводов по производству АЯБ с доведением общего его выпуска к 1995 г. до 40-45 млн м³/год.
Планы по этой программе предусматривали не только механическое наращивание объёмов выпуска автоклавных бетонов. Важной задачей было также и снижение средней плотности выпускаемой продукции (для блоков она составляла 600—700 кг/м³). В программе говорилось: «Таким образом, семикратное увеличение производства ячеистых бетонов в нашей стране следует сопровождать двукратным снижением их объёмной массы».
К 2011 году производство ячеистого бетона в России составило более 3,2 млн м³/год, количество заводов-производителей АЯБ — более 80, до 2015 года планируется к запуску 10.
См. также
Примечания
ГОСТы и СНиПы
- ГОСТ 25485-89 «Бетоны ячеистые»
- ГОСТ 21520-89 «Блоки из ячеистых бетонов стеновые мелкие»
- СН 277-80 «Инструкция по изготовлению изделий из ячеистого бетона»
- ГОСТ 31359-2007 «Бетоны ячеистые автоклавного твердения. Технические условия»
- ГОСТ 31360-2007 «Изделия стеновые неармированные из ячеистого бетона автоклавного твердения»
Газобетон — Википедия
Газобетонные блоки Блоки различного размера из газобетона российского производстваГазобето́н — разновидность ячеистого бетона; строительный материал, искусственный камень с равномерно распределёнными по всему объёму приблизительно сферическими, замкнутыми, но сообщающимися друг с другом порами диаметром 1—3 мм. По технологии окончательной обработки газобетон подразделяют на автоклавный газобетон и «неавтоклавный».
При производстве этого материала используются цемент, кварцевый песок и специализированные газообразователи, также, в состав смеси при его изготовлении иногда добавляют гипс, известь, промышленные отходы, такие, как, например, зола и шлаки металлургических производств.
Газообразование в замешенной на воде смеси обусловлено взаимодействием газообразователя, обычно мелкодисперсного металлического алюминия со сильнощелочным цементным или известковым раствором, в результате химической реакции образуются газообразный водород, вспенивающий цементный раствор, и алюминаты кальция.
Пылевидный алюминий неудобен для применения при замешивании раствора, так как сильно пылит. Поэтому в качестве специализированных газообразователей используются алюминиевые пасты и суспензии.
Типичный цикл производства газобетона: Перемешанные сухие ингредиенты смешиваются с водой, раствор заливается в форму. Происходит реакция щелочного водного раствора гидроксида кальция и газообразователя, приводящая к выделению водорода, который и «вспучивает» смесь. Смесь увеличивает объём и вспучивается как тесто. После предварительного схватывания цементного раствора, монолит извлекают из формы и разрезают на заготовки блоков, плит, панелей. После этого разрезанные заготовки подвергают обработке водяным паром в автоклаве для придания им окончательной прочности, либо высушиваются в электроподогреваемых сушильных камерах.
Газобетон легко обрабатывается: пилится, сверлится, строгается обычными стальными инструментами, даже без твердосплавных напаек. В него легко забиваются гвозди, скобы, установочные изделия. Со временем газобетон ещё более твердеет. Не горюч, так как состоит только из минеральных компонентов.
Имеет меньшую естественную радиоактивность по сравнению с обычным бетоном, так как в его состав не входит гранитный щебень, слюды, — составная часть природных гранитов, которые имеют повышенную естественную радиоактивность из-за концентрации в этих минералах тория и урана.
Разнообразие строительных материалов на рынке приумножается с каждым десятилетием. Если в Средние Века основными материалами были искусственный камень, древесина и кирпич, то сейчас появилось множество новых стройматериалов с улучшенными эксплуатационными характеристиками. В их число вошел газобетон, промышленное производство которого началось только в 1929 году. Газобетон является разновидностью ячеистого бетона (к этой группе также относятся пенобетон и газопенобетон). Впервые изготовлен в 1889 году, а спустя 40 лет поступил в производство.
Газобетон применяется в жилищном, коммерческом и промышленном строительстве. Основной объем потребления занимают строительные (стеновые и перегородочные блоки), также применяются армированные изделия (перемычки и плиты перекрытия).
Классификация газобетонов
- По назначению:
- конструкционные.
- конструкционно-теплоизоляционные.
- теплоизоляционные.
- По условиям твердения:
- автоклавные (синтезного твердения) — твердеющие в среде насыщенного пара при давлении выше атмосферного;
- неавтоклавные (гидратационного твердения) — твердеющие в естественных условиях, при электропрогреве или в среде насыщенного пара при атмосферном давлении.
- По виду вяжущих и кремнеземистых компонентов подразделяют:
- по виду основного вяжущего:
- на известковых вяжущих, состоящих из извести-кипелки более 50 % по массе, шлака и гипса или добавки цемента до 15 % по массе;
- на цементных вяжущих, в которых содержание портландцемента 50 % и более по массе;
- на смешанных вяжущих, состоящих из портландцемента от 15 до 50 % по массе, извести или шлака, или шлако-известковой смеси;
- на шлаковых вяжущих, состоящих из шлака более 50 % по массе в сочетании с известью, гипсом или щелочью;
- на зольных вяжущих, в которых содержание высокоосновных зол 50 % и более по массе;
- по виду кремнеземистого компонента:
- на природных материалах — тонкомолотом кварцевом и других песках;
- на вторичных продуктах промышленности — золе-унос ТЭС, золе гидроудаления, вторичных продуктах обогащения различных руд, отходах ферросплавов и других.
- по виду основного вяжущего:
История появления технологии производства автоклавного газобетона
Для придания бетону пористой структуры чех Гоффман добавил в цементные и гипсовые растворы кислоты, углекислые и хлористые соли. Соли, взаимодействуя с растворами, выделяли газ, который и делал бетон пористым. За изобретённый газобетон Гоффман в 1889 году получил патент, но дальше этого у него дело не пошло.
Замысел Гоффмана развили американцы Аулсворт и Дайер. В качестве газообразователя в 1914 году они использовали порошки алюминия и цинка. В процессе химической реакции этих порошков с гашеной известью выделялся водород, который и способствовал образованию в бетоне пористой структуры. Это изобретение оказалось столь значимым, что его и поныне считают отправной точкой технологии изготовления газобетона.
Свой вклад в дело совершенствования газобетона (газосиликата) внёс шведский архитектор и ученый Юхан Аксель Эрикссон. В своих исследованиях он пытался вспучивать раствор извести, кремнезёмистых компонентов и цемента за счёт взаимодействия этого раствора с алюминиевым порошком. Этот подход увенчался успехом. В 1929 году в местечке Иксхульт фирмой «Итонг» (Ytong) был начат промышленный выпуск газобетона. Инженерами этой фирмы за основу была взята технология тепловлажностного воздействия в автоклавах на известково-кремнезёмистые компоненты, запатентованная в 1880 году немецким профессором В. Михаэлисом. Только за первый год работы этим предприятием было произведено 14 тысяч м³ газобетона (газосиликата). Следует заметить, что фирмой «Итонг» цемент не применялся вообще.
Несколько иной метод производства газобетона внедрила в жизнь в 1934 году шведская фирма «Сипорекс» (Siporex). Он основывается на применении смеси из портландцемента и кремнезёмистого компонента. Известь в данном случае не применялась. Авторы этого метода — инженеры финн Леннарт Форсэн и швед Ивар Эклунд. Научные и практические достижения вышеперечисленных инженеров и стали впоследствии основой промышленного производства как газосиликатов, так и газобетонов во многих странах мира.
История производства ячеистых бетонов в СССР
Производство ячеистых бетонов в СССР стало активно развиваться в 1930-е годы. Автоклавные ячеистые бетоны (АЯБ) с газовой поризацией появились в промышленных масштабах к 1950-м годам. К 1960-м годам производство АЯБ стало самостоятельным развивающимся научным направлением, во многом опережающим европейские наработки в этой области.
К концу 1980-х годов в СССР из ячеистых бетонов было построено более 250 млн м² зданий различного назначения (жилых, общественных, производственных, животноводческих). При этом, несмотря на высокий уровень отечественных научных разработок, ориентиром для советской промышленности служили западно-европейские достижения (понижение плотности панелей и блоков вплоть до 300 кг/м³), основанные, в первую очередь, на стабильном сырье и оборудовании, обеспечивающем высокую однородность материала.
В 1987 г. с принятием очередной жилищной программы СССР основным средством её реализации стала научно-производственно-техническая программа «Система эффективного строительства жилых и общественных зданий из ячеистых бетонов», которая предполагала строительство около 250 новых заводов по производству АЯБ с доведением общего его выпуска к 1995 г. до 40-45 млн м³/год.
Планы по этой программе предусматривали не только механическое наращивание объёмов выпуска автоклавных бетонов. Важной задачей было также и снижение средней плотности выпускаемой продукции (для блоков она составляла 600—700 кг/м³). В программе говорилось: «Таким образом, семикратное увеличение производства ячеистых бетонов в нашей стране следует сопровождать двукратным снижением их объёмной массы».
К 2011 году производство ячеистого бетона в России составило более 3,2 млн м³/год, количество заводов-производителей АЯБ — более 80, до 2015 года планируется к запуску 10.
Наиболее крупные и современные предприятия по выпуску газобетона в РФ, в основном, построены в 1990-е годы.
ГОСТы и СНиПы
- ГОСТ 25485-89 «Бетоны ячеистые»
- ГОСТ 21520-89 «Блоки из ячеистых бетонов стеновые мелкие»
- СН 277-80 «Инструкция по изготовлению изделий из ячеистого бетона»
- ГОСТ 31359-2007 «Бетоны ячеистые автоклавного твердения. Технические условия»
- ГОСТ 31360-2007 «Изделия стеновые неармированные из ячеистого бетона автоклавного твердения»
См. также
Примечания
Ссылки
Газобетон Википедия
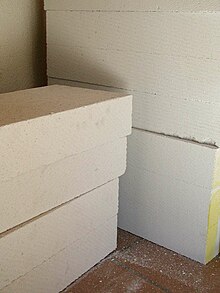
Газобето́н — лёгкий, ячеистый бетон с равномерно распределёнными по всему объёму замкнутыми порами[1] диаметром 1—3 мм. По технологии окончательной обработки различают автоклавный и «неавтоклавный» газобетон.
При производстве этого материала используются цемент, кварцевый песок и специализированные газообразователи, также в состав смеси при его изготовлении иногда добавляют гипс, известь, промышленные отходы, к примеру, зола и шлаки металлургических производств.
Газообразование в замешенной на воде смеси обусловлено взаимодействием газообразователя, обычно мелисперсного металлического алюминия с сильнощелочным цементным или известковым раствором, в результате химической реакции образуются газообразный водород, вспенивающий цементный раствор, и алюминаты кальция.
Пылевидный алюминий неудобен для применения при замешивании раствора, так как сильно пылит. Поэтому в качестве специализированных газообразователей используются алюминиевые пасты и суспензии.
Типичный цикл производства газобетона: Перемешанные сухие ингредиенты смешиваются с водой, раствор заливается в форму. Происходит реакция щелочного водного раствора гидроксида кальция и газообразователя, приводящая к выделению водорода, который и «вспучивает» смесь. Смесь увеличивает объём и вспучивается как тесто. После предварительного схватывания цементного раствора, монолит извлекают из формы и разрезают на заготовки блоков, плит, панелей. После этого разрезанные заготовки подвергают обработке водяным паром в автоклаве для придания им окончательной прочности, либо высушиваются в электроподогреваемых сушильных камерах.
Газобетон легко обрабатывается: пилится, сверлится, строгается обычными стальными инструментами, даже без твердосплавных напаек. В него легко забиваются гвозди, скобы, установочные изделия. Со временем в процессе карбонизации прочность может уменьшаться на 20-30% [источник не указан 215 дней].Так как пористость, а соответственно газо- и паропроницаемость современных блоков выше, то и карбонизация и старение происходит значительно быстрее указанных 15-20 лет, чем это описано в исследовании Е.С. Силаенкова. Не горюч, так как состоит только из минеральных компонентов.
Имеет меньшую естественную радиоактивность по сравнению с обычным бетоном, так как в его состав не входит гранитный щебень, слюды, — составная часть природных гранитов, которые имеют повышенную естественную радиоактивность из-за концентрации в этих минералах тория и урана.
Газобетон применяется в жилищном, коммерческом и промышленном строительстве. Основной объем потребления занимают строительные (стеновые и перегородочные блоки), также применяются армированные изделия (перемычки и плиты перекрытия).
Классификация газобетонов[ | ]
- По назначению:
- конструкционные.
- конструкционно-теплоизоляционные.
- теплоизоляционные[2].
- По условиям твердения:
- автоклавные (синтезного твердения) — твердеющие в среде насыщенного пара при давлении выше атмосферного;
- неавтоклавные (гидратационного твердения) — твердеющие в естественных условиях, при электропрогреве или в среде насыщенного пара при атмосферном давлении.
- По виду вяжущих и кремнеземистых компонентов подразделяют:
- по виду основного вяжущего:
- на известковых вяжущих, состоящих из извести-кипелки более 50 % по массе, шлака и гипса или добавки цемента до 15 % по массе;
- на цементных вяжущих, в которых содержание портландцемента 50 % и более по массе;
- на смешанных вяжущих, состоящих из портландцемента от 15 до 50 % по массе, извести или шлака, или шлако-известковой смеси;
- на шлаковых вяжущих, состоящих из шлака бо
- по виду основного вяжущего:
Газобетон — Википедия. Что такое Газобетон
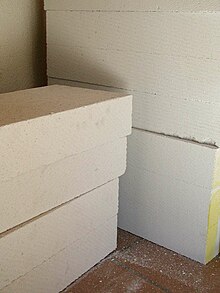
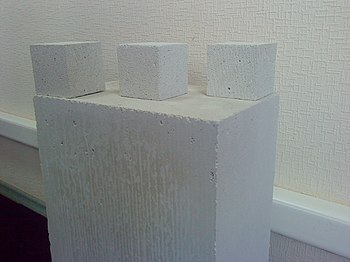
Газобето́н — разновидность ячеистого бетона; строительный материал, искусственный камень с равномерно распределёнными по всему объёму приблизительно сферическими, замкнутыми, но сообщающимися друг с другом порами диаметром 1—3 мм. По технологии окончательной обработки газобетон подразделяют на автоклавный газобетон и «неавтоклавный».
При производстве этого материала используются цемент, кварцевый песок и специализированные газообразователи, также, в состав смеси при его изготовлении иногда добавляют гипс, известь, промышленные отходы, такие, как, например, зола и шлаки металлургических производств.
Газообразование в замешенной на воде смеси обусловлено взаимодействием газообразователя, обычно мелкодисперсного металлического алюминия со сильнощелочным цементным или известковым раствором, в результате химической реакции образуются газообразный водород, вспенивающий цементный раствор, и алюминаты кальция.
Пылевидный алюминий неудобен для применения при замешивании раствора, так как сильно пылит. Поэтому в качестве специализированных газообразователей используются алюминиевые пасты и суспензии.
Типичный цикл производства газобетона: Перемешанные сухие ингредиенты смешиваются с водой, раствор заливается в форму. Происходит реакция щелочного водного раствора гидроксида кальция и газообразователя, приводящая к выделению водорода, который и «вспучивает» смесь. Смесь увеличивает объём и вспучивается как тесто. После предварительного схватывания цементного раствора, монолит извлекают из формы и разрезают на заготовки блоков, плит, панелей. После этого разрезанные заготовки подвергают обработке водяным паром в автоклаве для придания им окончательной прочности, либо высушиваются в электроподогреваемых сушильных камерах.
Газобетон легко обрабатывается: пилится, сверлится, строгается обычными стальными инструментами, даже без твердосплавных напаек. В него легко забиваются гвозди, скобы, установочные изделия. Со временем газобетон ещё более твердеет. Не горюч, так как состоит только из минеральных компонентов.
Имеет меньшую естественную радиоактивность по сравнению с обычным бетоном, так как в его состав не входит гранитный щебень, слюды, — составная часть природных гранитов, которые имеют повышенную естественную радиоактивность из-за концентрации в этих минералах тория и урана.
Разнообразие строительных материалов на рынке приумножается с каждым десятилетием. Если в Средние Века основными материалами были искусственный камень, древесина и кирпич, то сейчас появилось множество новых стройматериалов с улучшенными эксплуатационными характеристиками. В их число вошел газобетон, промышленное производство которого началось только в 1929 году. Газобетон является разновидностью ячеистого бетона (к этой группе также относятся пенобетон и газопенобетон). Впервые изготовлен в 1889 году, а спустя 40 лет поступил в производство.
Физико-механические свойства
- На производство газобетонного изделия требуется меньше цемента.
- Газобетон по простоте обработки сравним с деревом: он легко пилится, сверлится.
Применение
Газобетон применяется в жилищном, коммерческом и промышленном строительстве. Основной объем потребления занимают строительные (стеновые и перегородочные блоки), также применяются армированные изделия (перемычки и плиты перекрытия).
В малоэтажном индивидуальном строительстве самонесущая способность газобетонных блоков позволяет использовать их в качестве материала для наружных стен домов небольшой этажности (до пяти этажей). При строительстве многоэтажных каркасно-монолитных домов, когда блоки играют роль ограждающих конструкций (фасады и перегородки), этажность практически не ограничена.
Недостатки
К основным недостаткам газобетона относится быстрое разрушение материала под воздействием влаги[источник не указан 115 дней].
Строения после постройки необходимо обязательно закрывать от внешней среды, в противном случае, газобетон начинает разрушаться.
Согласно действующим ГОСТам долговечность газобетона определена на отметке в 50 лет.
Также среди недостатков газобетона стоит отметить:
- Низкая прочность монтажа крепёжных материалов(дюбель-саморезов, анкеров). Они не держатся, так как газобетон имеет пористую структуру. Особенно данный недостаток выражен в автоклавном газобетоне[источник не указан 115 дней].
- Низкая плотность газобетона влияет на кaчество установки окон и дверей, они со временем расшатываются. Особенно заметно в строениях, возведенных из автоклавного газобетона[источник не указан 115 дней].
- Свойства материала в значительной степени определяются бетонной составляющей.
- Стена из автоклавного газобетона имеет низкие показатели сцепления со штукатурной смесью[источник не указан 115 дней], а значит, требует дополнительной подготовки перед оштукатуриванием.
- Усадка газобетона в три раза больше, чем у полистиролбетона и пенобетона –2 мм/метр[источник не указан 115 дней].
- Блоки из газобетона относятся к группе горючести НГ, то есть они не горючи и огнестойки. Тем не менее, под воздействием высокой температуры, вблизи источника огня, газобетонные блоки начинают взрываться и хотя остающийся бетонный каркас не позволяет разрушится блокам до конца, их прочность и сопротивление теплопередаче при этом снижается в несколько раз. Использование газобетонных блоков без огнестойкой защиты запрещено действующим СНИП[источник не указан 115 дней].
Классификация газобетонов
- По назначению:
- конструкционные.
- конструкционно-теплоизоляционные.
- теплоизоляционные.
- По условиям твердения:
- автоклавные (синтезного твердения) — твердеющие в среде насыщенного пара при давлении выше атмосферного;
- неавтоклавные (гидратационного твердения) — твердеющие в естественных условиях, при электропрогреве или в среде насыщенного пара при атмосферном давлении.
- По виду вяжущих и кремнеземистых компонентов подразделяют:
- по виду основного вяжущего:
- на известковых вяжущих, состоящих из извести-кипелки более 50 % по массе, шлака и гипса или добавки цемента до 15 % по массе;
- на цементных вяжущих, в которых содержание портландцемента 50 % и более по массе;
- на смешанных вяжущих, состоящих из портландцемента от 15 до 50 % по массе, извести или шлака, или шлако-известковой смеси;
- на шлаковых вяжущих, состоящих из шлака более 50 % по массе в сочетании с известью, гипсом или щелочью;
- на зольных вяжущих, в которых содержание высокоосновных зол 50 % и более по массе;
- по виду кремнеземистого компонента:
- на природных материалах — тонкомолотом кварцевом и других песках;
- на вторичных продуктах промышленности — золе-унос ТЭС, золе гидроудаления, вторичных продуктах обогащения различных руд, отходах ферросплавов и других.
- по виду основного вяжущего:
История появления технологии производства автоклавного газобетона
Для придания бетону пористой структуры чех Гоффман добавил в цементные и гипсовые растворы кислоты, углекислые и хлористые соли. Соли, взаимодействуя с растворами, выделяли газ, который и делал бетон пористым. За изобретённый газобетон Гоффман в 1889 году получил патент, но дальше этого у него дело не пошло.
Замысел Гоффмана развили американцы Аулсворт и Дайер. В качестве газообразователя в 1914 году они использовали порошки алюминия и цинка. В процессе химической реакции этих порошков с гашеной известью выделялся водород, который и способствовал образованию в бетоне пористой структуры. Это изобретение оказалось столь значимым, что его и поныне считают отправной точкой технологии изготовления газобетона.
Свой вклад в дело совершенствования газобетона (газосиликата) внёс шведский архитектор и ученый Юхан Аксель Эрикссон. В своих исследованиях он пытался вспучивать раствор извести, кремнезёмистых компонентов и цемента за счёт взаимодействия этого раствора с алюминиевым порошком. Этот подход увенчался успехом. В 1929 году в местечке Иксхульт фирмой «Итонг» (Ytong) был начат промышленный выпуск газобетона. Инженерами этой фирмы за основу была взята технология тепловлажностного воздействия в автоклавах на известково-кремнезёмистые компоненты, запатентованная в 1880 году немецким профессором В. Михаэлисом. Только за первый год работы этим предприятием было произведено 14 тысяч м³ газобетона (газосиликата). Следует заметить, что фирмой «Итонг» цемент не применялся вообще.
Несколько иной метод производства газобетона внедрила в жизнь в 1934 году шведская фирма «Сипорекс» (Siporex). Он основывается на применении смеси из портландцемента и кремнезёмистого компонента. Известь в данном случае не применялась. Авторы этого метода — инженеры финн Леннарт Форсэн и швед Ивар Эклунд. Научные и практические достижения вышеперечисленных инженеров и стали впоследствии основой промышленного производства как газосиликатов, так и газобетонов во многих странах мира.
История производства ячеистых бетонов в СССР
Производство ячеистых бетонов в СССР стало активно развиваться в 1930-е годы. Автоклавные ячеистые бетоны (АЯБ) с газовой поризацией появились в промышленных масштабах к 1950-м годам. К 1960-м годам производство АЯБ стало самостоятельным развивающимся научным направлением, во многом опережающим европейские наработки в этой области.
К концу 1980-х годов в СССР из ячеистых бетонов было построено более 250 млн м² зданий различного назначения (жилых, общественных, производственных, животноводческих). При этом, несмотря на высокий уровень отечественных научных разработок, ориентиром для советской промышленности служили западно-европейские достижения (понижение плотности панелей и блоков вплоть до 300 кг/м³), основанные, в первую очередь, на стабильном сырье и оборудовании, обеспечивающем высокую однородность материала.
В 1987 г. с принятием очередной жилищной программы СССР основным средством её реализации стала научно-производственно-техническая программа «Система эффективного строительства жилых и общественных зданий из ячеистых бетонов», которая предполагала строительство около 250 новых заводов по производству АЯБ с доведением общего его выпуска к 1995 г. до 40-45 млн м³/год.
Планы по этой программе предусматривали не только механическое наращивание объёмов выпуска автоклавных бетонов. Важной задачей было также и снижение средней плотности выпускаемой продукции (для блоков она составляла 600—700 кг/м³). В программе говорилось: «Таким образом, семикратное увеличение производства ячеистых бетонов в нашей стране следует сопровождать двукратным снижением их объёмной массы».
К 2011 году производство ячеистого бетона в России составило более 3,2 млн м³/год, количество заводов-производителей АЯБ — более 80, до 2015 года планируется к запуску 10.
Наиболее крупные и современные предприятия по выпуску газобетона в РФ, в основном, построены в 1990-е годы.
ГОСТы и СНиПы
- ГОСТ 25485-89 «Бетоны ячеистые»
- ГОСТ 21520-89 «Блоки из ячеистых бетонов стеновые мелкие»
- СН 277-80 «Инструкция по изготовлению изделий из ячеистого бетона»
- ГОСТ 31359-2007 «Бетоны ячеистые автоклавного твердения. Технические условия»
- ГОСТ 31360-2007 «Изделия стеновые неармированные из ячеистого бетона автоклавного твердения»
Выводы
Можно сделать несколько выводов про газобетон:
- Газобетон – разновидность ячеистого бетона.
- Состоит из нескольких элементов: очищенный кварцевый песок, вода, цемент, известь, алюминиевый преобразователь.
- Газоблок хорошо подходит для изготовления: элементов теплоизоляции, огнестойких изделий, стеновых блоков различных габаритов, панелей перекрытия.
- Обладает множеством преимуществ, среди которых экологичность, малый удельный вес, прекрасные тепло- и звукоизоляционные характеристики, наличие системы «паз-гребень», устойчивость к негативным факторам окружающей среды, простой монтаж и удобная транспортировка и т.д.
- В строительстве используется для возведения несущих и каркасных стен, внутренних перегородок, заполнения монолитно-каркасных конструкций, ремонта стен.
См. также
Примечания
Ссылки
Газобетон — Википедия
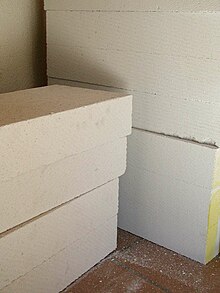
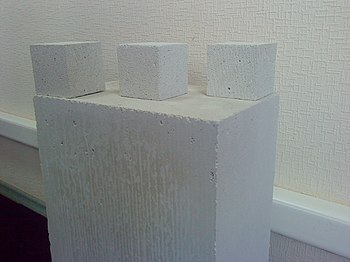
Газобето́н — разновидность ячеистого бетона; строительный материал, искусственный камень с равномерно распределёнными по всему объёму приблизительно сферическими, замкнутыми, но сообщающимися друг с другом порами диаметром 1—3 мм. По технологии окончательной обработки газобетон подразделяют на автоклавный газобетон и «неавтоклавный».
При производстве этого материала используются цемент, кварцевый песок и специализированные газообразователи, также, в состав смеси при его изготовлении иногда добавляют гипс, известь, промышленные отходы, такие, как, например, зола и шлаки металлургических производств.
Газообразование в замешенной на воде смеси обусловлено взаимодействием газообразователя, обычно мелкодисперсного металлического алюминия со сильнощелочным цементным или известковым раствором, в результате химической реакции образуются газообразный водород, вспенивающий цементный раствор, и алюминаты кальция.
Пылевидный алюминий неудобен для применения при замешивании раствора, так как сильно пылит. Поэтому в качестве специализированных газообразователей используются алюминиевые пасты и суспензии.
Типичный цикл производства газобетона: Перемешанные сухие ингредиенты смешиваются с водой, раствор заливается в форму. Происходит реакция щелочного водного раствора гидроксида кальция и газообразователя, приводящая к выделению водорода, который и «вспучивает» смесь. Смесь увеличивает объём и вспучивается как тесто. После предварительного схватывания цементного раствора, монолит извлекают из формы и разрезают на заготовки блоков, плит, панелей. После этого разрезанные заготовки подвергают обработке водяным паром в автоклаве для придания им окончательной прочности, либо высушиваются в электроподогреваемых сушильных камерах.
Газобетон легко обрабатывается: пилится, сверлится, строгается обычными стальными инструментами, даже без твердосплавных напаек. В него легко забиваются гвозди, скобы, установочные изделия. Со временем газобетон ещё более твердеет. Не горюч, так как состоит только из минеральных компонентов.
Имеет меньшую естественную радиоактивность по сравнению с обычным бетоном, так как в его состав не входит гранитный щебень, слюды, — составная часть природных гранитов, которые имеют повышенную естественную радиоактивность из-за концентрации в этих минералах тория и урана.
Разнообразие строительных материалов на рынке приумножается с каждым десятилетием. Если в Средние Века основными материалами были искусственный камень, древесина и кирпич, то сейчас появилось множество новых стройматериалов с улучшенными эксплуатационными характеристиками. В их число вошел газобетон, промышленное производство которого началось только в 1929 году. Газобетон является разновидностью ячеистого бетона (к этой группе также относятся пенобетон и газопенобетон). Впервые изготовлен в 1889 году, а спустя 40 лет поступил в производство.
Газобетон применяется в жилищном, коммерческом и промышленном строительстве. Основной объем потребления занимают строительные (стеновые и перегородочные блоки), также применяются армированные изделия (перемычки и плиты перекрытия).
Классификация газобетонов
- По назначению:
- конструкционные.
- конструкционно-теплоизоляционные.
- теплоизоляционные.
- По условиям твердения:
- автоклавные (синтезного твердения) — твердеющие в среде насыщенного пара при давлении выше атмосферного;
- неавтоклавные (гидратационного твердения) — твердеющие в естественных условиях, при электропрогреве или в среде насыщенного пара при атмосферном давлении.
- По виду вяжущих и кремнеземистых компонентов подразделяют:
- по виду основного вяжущего:
- на известковых вяжущих, состоящих из извести-кипелки более 50 % по массе, шлака и гипса или добавки цемента до 15 % по массе;
- на цементных вяжущих, в которых содержание портландцемента 50 % и более по массе;
- на смешанных вяжущих, состоящих из портландцемента от 15 до 50 % по массе, извести или шлака, или шлако-известковой смеси;
- на шлаковых вяжущих, состоящих из шлака более 50 % по массе в сочетании с известью, гипсом или щелочью;
- на зольных вяжущих, в которых содержание высокоосновных зол 50 % и более по массе;
- по виду кремнеземистого компонента:
- на природных материалах — тонкомолотом кварцевом и других песках;
- на вторичных продуктах промышленности — золе-унос ТЭС, золе гидроудаления, вторичных продуктах обогащения различных руд, отходах ферросплавов и других.
- по виду основного вяжущего:
Видео по теме
История появления технологии производства автоклавного газобетона
Для придания бетону пористой структуры чех Гоффман добавил в цементные и гипсовые растворы кислоты, углекислые и хлористые соли. Соли, взаимодействуя с растворами, выделяли газ, который и делал бетон пористым. За изобретённый газобетон Гоффман в 1889 году получил патент, но дальше этого у него дело не пошло.
Замысел Гоффмана развили американцы Аулсворт и Дайер. В качестве газообразователя в 1914 году они использовали порошки алюминия и цинка. В процессе химической реакции этих порошков с гашеной известью выделялся водород, который и способствовал образованию в бетоне пористой структуры. Это изобретение оказалось столь значимым, что его и поныне считают отправной точкой технологии изготовления газобетона.
Свой вклад в дело совершенствования газобетона (газосиликата) внёс шведский архитектор и ученый Юхан Аксель Эрикссон. В своих исследованиях он пытался вспучивать раствор извести, кремнезёмистых компонентов и цемента за счёт взаимодействия этого раствора с алюминиевым порошком. Этот подход увенчался успехом. В 1929 году в местечке Иксхульт фирмой «Итонг» (Ytong) был начат промышленный выпуск газобетона. Инженерами этой фирмы за основу была взята технология тепловлажностного воздействия в автоклавах на известково-кремнезёмистые компоненты, запатентованная в 1880 году немецким профессором В. Михаэлисом. Только за первый год работы этим предприятием было произведено 14 тысяч м³ газобетона (газосиликата). Следует заметить, что фирмой «Итонг» цемент не применялся вообще.
Несколько иной метод производства газобетона внедрила в жизнь в 1934 году шведская фирма «Сипорекс» (Siporex). Он основывается на применении смеси из портландцемента и кремнезёмистого компонента. Известь в данном случае не применялась. Авторы этого метода — инженеры финн Леннарт Форсэн и швед Ивар Эклунд. Научные и практические достижения вышеперечисленных инженеров и стали впоследствии основой промышленного производства как газосиликатов, так и газобетонов во многих странах мира.
История производства ячеистых бетонов в СССР
Производство ячеистых бетонов в СССР стало активно развиваться в 1930-е годы. Автоклавные ячеистые бетоны (АЯБ) с газовой поризацией появились в промышленных масштабах к 1950-м годам. К 1960-м годам производство АЯБ стало самостоятельным развивающимся научным направлением, во многом опережающим европейские наработки в этой области.
К концу 1980-х годов в СССР из ячеистых бетонов было построено более 250 млн м² зданий различного назначения (жилых, общественных, производственных, животноводческих). При этом, несмотря на высокий уровень отечественных научных разработок, ориентиром для советской промышленности служили западно-европейские достижения (понижение плотности панелей и блоков вплоть до 300 кг/м³), основанные, в первую очередь, на стабильном сырье и оборудовании, обеспечивающем высокую однородность материала.
В 1987 г. с принятием очередной жилищной программы СССР основным средством её реализации стала научно-производственно-техническая программа «Система эффективного строительства жилых и общественных зданий из ячеистых бетонов», которая предполагала строительство около 250 новых заводов по производству АЯБ с доведением общего его выпуска к 1995 г. до 40-45 млн м³/год.
Планы по этой программе предусматривали не только механическое наращивание объёмов выпуска автоклавных бетонов. Важной задачей было также и снижение средней плотности выпускаемой продукции (для блоков она составляла 600—700 кг/м³). В программе говорилось: «Таким образом, семикратное увеличение производства ячеистых бетонов в нашей стране следует сопровождать двукратным снижением их объёмной массы».
К 2011 году производство ячеистого бетона в России составило более 3,2 млн м³/год, количество заводов-производителей АЯБ — более 80, до 2015 года планируется к запуску 10.
Наиболее крупные и современные предприятия по выпуску газобетона в РФ, в основном, построены в 1990-е годы.
ГОСТы и СНиПы
- ГОСТ 25485-89 «Бетоны ячеистые»
- ГОСТ 21520-89 «Блоки из ячеистых бетонов стеновые мелкие»
- СН 277-80 «Инструкция по изготовлению изделий из ячеистого бетона»
- ГОСТ 31359-2007 «Бетоны ячеистые автоклавного твердения. Технические условия»
- ГОСТ 31360-2007 «Изделия стеновые неармированные из ячеистого бетона автоклавного твердения»
См. также
Примечания
Ссылки
Газобетон — Вікіпедія
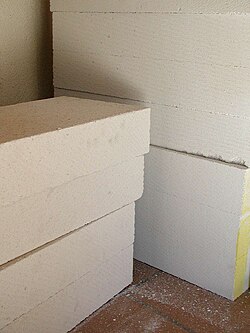
Газобетон — різновид пористого бетону; будівельний матеріал, штучний камінь з рівномірно розподіленими по всьому об’єму приблизно сферичними, замкнутими, один з одним порами діаметром 1-3 мм. При виробництві цього матеріалу використовуються цемент, кварцовий пісок і спеціалізований газоутворювач, також, до складу суміші при його виготовленні іноді додають гіпс, вапно, промислові відходи, такі, як, наприклад, зола і шлаки металургійних виробництв.
Газоутворення в замішаної на воді суміші обумовлено взаємодією газоутворювача, зазвичай дрібнодисперсного металевого алюмінію зі сильнолужним цементним або вапняним розчином, в результаті хімічної реакції утворюються газоподібний водень, який спінює цементний розчин, і алюмінати кальцію.
Пилоподібний алюміній незручний для застосування при замішуванні розчину, бо створюе багато пилюки. Тому, як спеціалізовані газоутворювачі використовуються алюмінієві пасти і суспензії.
Типовий цикл виробництва газобетону: Перемішані сухі інгредієнти змішуються з водою, розчин заливається в форму. Відбувається реакція лужного водного розчину гідроксиду кальцію і газоутворювача, що приводить до виділення водню, який і «спучує» суміш. Суміш збільшує обсяг і спучується як тісто. Після попереднього схоплювання цементного розчину, моноліт виймають з форми і розрізають на заготовки блоків, плит, панелей. Після цього розрізані заготовки піддають обробці водяною парою в автоклаві для додання їм остаточної міцності, або висушуються в електропідігріваємих сушильних камерах. За технологією остаточної обробки газобетон підрозділяють на «автоклавний» і «неавтоклавний».
Газобетон легко обробляється: пиляється, свердлиться, стружиться звичайними сталевими інструментами, навіть без твердосплавних напайок. У нього легко забиваються цвяхи, скоби, настановні вироби. З часом газобетон ще більш твердне. Не горючий, тому що складається тільки з мінеральних компонентів.
Має меншу природну радіоактивність у порівнянні зі звичайним бетоном, так як в його склад не входить гранітний щебінь, слюди, — складова частина природних гранітів, мають підвищену природну радіоактивність через концентрацію в цих мінералах торію та урану.
Газобетон широко використовується як будівельний матеріал у всьому світі. В даний час (2014) його виробляють більше 240 заводів у 50 країнах з сумарною потужністю близько 60 млн м³ будівельних виробів з газобетону.
Фізико-механічні властивості[ред. | ред. код]
- На виробництво газобетонного виробу потрібно менше цементу.
- Газобетон за простотою обробки порівняємо з деревом: він легко пиляється, свердлиться.
Газобетон застосовується в житловому, комерційному та промисловому будівництві. Основний обсяг споживання займають будівельні (стінові й перегородкові блоки), також застосовуються армовані вироби (перемички та плити перекриття).
У малоповерховому індивідуальному будівництві самонесуча здатність газобетонних блоків дозволяє використовувати їх як матеріал для зовнішніх стін будинків невеликої поверховості (в середньому до трьох поверхів). При будівництві багатоповерхових каркасно-монолітних будинків, коли блоки відіграють роль огороджувальних конструкцій (фасади і перегородки), поверховість практично не обмежена.
Класифікація газобетонів[ред. | ред. код]
За призначенням:
- конструкційні.
- конструкційно-теплоізоляційні.
- теплоізоляційні.
За умовами твердіння:
- автоклавні (синтезного твердіння) — тверднуть в середовищі насиченої пари при тиску вище атмосферного;
- неавтоклавні (гідратаційного твердіння) — тверднуть в природних умовах, при електропрогріванні або в середовищі насиченої пари при атмосферному тиску.
За видом в’яжучих і кремнеземистих компонентів підрозділяють:
1. За видом основного в’яжучого:
- на вапняних в’яжучих, які складаються з вапна-кипілки більше 50 % за масою, шлаку і гіпсу або добавки цементу до 15 % за масою;
- на цементних в’яжучих, в яких вміст портландцементу 50 % і більше по масі;
- на змішаних в’яжучих, які складаються з портландцементу від 15 до 50 % за масою, вапна або шлаку, або шлако-вапняної суміші;
- на шлакових в’яжучих, які складаються з шлаку більше 50 % за масою в поєднанні з вапном, гіпсом або лугом;
д) на зольних в’яжучих, в яких вміст високолужних зол 50 % і більше по масі;
2. За видом кремнеземистого компонента:
- а) на природних матеріалах -тонкомолотому кварцовому та інших пісках;
- б) на вторинних продуктах промисловості — золі-виносу ТЕС, золі гідровидалення, вторинних продуктах збагачення різних руд, відходах феросплавів та інших.
Історія появи технології виробництва автоклавного газобетону[ред. | ред. код]
Для того, щоб зробити структуру бетону пористою, чех Гоффман додав в цементні і гіпсові розчини кислоти, вуглекислі й хлористі солі. Солі, взаємодіючи з розчинами, виділяли газ, який і робив бетон пористим. За винайдений газобетон Гоффман в 1889 році отримав патент, але далі цього у нього справа не пішла.
Задум Гоффмана розвинули американці Аулсворт і Дайер. Як газоутворювач у 1914 році вони використовували порошки алюмінію і цинку. У процесі хімічної реакції цих порошків з гашеним вапном виділявся водень, який і сприяв утворенню в бетоні пористої структури. Це винахід виявився настільки значущим, що його і понині вважають відправною точкою технології виготовлення газобетону.
Свій внесок у справу вдосконалення газобетону (газосилікату) додав шведський архітектор і вчений Юхан Аксель Ерікссон. У своїх дослідженнях він намагався спучувати розчин вапна, кремнеземистих компонентів і цементу за рахунок взаємодії цього розчину з алюмінієвим порошком. Цей підхід увінчався успіхом. У 1929 році в містечку Іксхульт фірмою «Ітонг» (Ytong) був початий промисловий випуск газобетону. Інженерами цієї фірми за основу була взята технологія тепловологістного впливу в автоклавах на вапняно-кремнеземисті компоненти, запатентована в 1880 році німецьким професором В. Міхаелісом. Тільки за перший рік роботи цим підприємством було вироблено 14000 м³ газобетону (газосилікату). Слід зауважити, що фірмою «Ітонг» цемент не застосовувався взагалі.
Дещо інший метод виробництва газобетону впровадила в життя в 1934 році шведська фірма «Сипорекс» (Siporex). Він ґрунтується на застосуванні суміші з портландцементу і кремнеземистого компонента. Вапно в даному випадку не застосовувалася. Автори цього методу — інженери фін Леннарт Форсен і швед Івар Еклунд. Наукові та практичні досягнення вищеперелічених інженерів і стали згодом основою промислового виробництва як газосилікату, так і газобетонів в багатьох країнах світу.
- Крихкість. Стіни з газобетону не бояться механічних пошкоджень, але окремі блоки вимагають до себе дбайливого ставлення. Вони просто можуть розкришитися або надломитися.
- Гігроскопічність. Пориста структура є одночасно перевагою і недоліком газоблоків, адже вони забезпечують циркуляцію повітря, але дуже швидко вбирають вологу. Впоратися з проблемою допоможе тільки правильна внутрішня і зовнішня обробка.
- Особлива система кріплень. Через технологічні особливості даного будівельного матеріалу до нього не підходять традиційні елементи кріплення. Додаткові компоненти не входять в комплект для продажу. Тому є досить відчутні додаткові витрати, про які рекламщики замовчують.
Порівняльна таблиця цегли і газобетону[ред. | ред. код]
Порівняння параметрів цегли та газобетону | ||
---|---|---|
Параметр | Керамічна цегла | Газобетон |
Межа міцності на стиск, кг/см² | 110÷220 | 25÷50 |
Маса стіни (1 м³) | 1200÷2000 | 700÷900 |
Теплопровідність, Вт/мК | 0,32÷0,46 | 0,10÷0,12 |
Морозотривкість, циклів | 50÷100 | 50 |
Вологопоглинання (% до маси) | 5÷12 | 20 |
Вогнетривкість (клас) | 1 | 1 |