Шахтный аккумуляторный электровоз — Википедия
Шахтный аккумуляторный электровоз — промышленный локомотив (электровоз), применяемый в угольной промышленности для различных целей.
Шахтные аккумуляторные электровозы составляют 80 % от общего числа применяемых в угольной промышленности локомотивов. Источником электроэнергии шахтных аккумуляторных электровозов являются щелочные никель-железные (ТНЖ и ТНЖШ), никель-кадмиевые (ТНК) и кислотные (PzS) тяговые аккумуляторы, заключённые в батарейный ящик. Шахтные аккумуляторные электровозы выпускаются сцепным весом: 4,5; 5; 7; 8; 10; 14 и 28 тонн.
Область применения шахтных аккумуляторных электровозов напрямую связана с уровнем их взрывозащиты.
Шахтные аккумуляторные электровозы, как правило, комплектуются электрооборудованием с уровнем взрывозащиты РВ (рудничное взрывобезопасное), однако из-за аккумуляторной батареи, не отвечающей этому уровню безопасности, имеют исполнение РП (рудничные повышенной надёжности).
Шахтные аккумуляторные электровозы в исполнении РП применяются:
- в откаточных выработках шахт I и II категорий по газу или опасных по пыли;
- в откаточных выработках со свежей струёй воздуха шахт III категории и сверхкатегорийных по газу;
- в откаточных выработках со свежей струёй воздуха на пластах, не опасных по внезапным выбросам, на шахтах, опасных по внезапным выбросам;
Шахтные аккумуляторные электровозы в исполнении РВ применяться:
- в откаточных выработках шахт, опасных по газу или пыли;
- в выработках шахт с исходящей струёй воздуха и тупиковых, проветриваемых вентиляторами местного проветривания;
- на шахтах III категории, сверхкатегорийных по газу и опасных по внезапным выбросам.
В последних двух случаях на электровозах должны быть предусмотрены переносные (индивидуальные) автоматические приборы контроля содержания метана.
Состав шахтного аккумуляторного электровоза[править | править код]
Шахтный аккумуляторный электровоз включает в себя:
- механическое оборудование, состоящее из рамы, буферов, сцепных устройств, кабины, тормозной и песочной систем, редукторов, колесных пар, буксов, батарейного ящика и другого;
- электрическое оборудование, состоящее из тяговых электродвигателей, аккумуляторной батареи, пускорегулирующей аппаратуры (контроллер, пусковые сопротивления, стабилизатор напряжения, автоматический выключатель), аппаратуры сигнализации и освещения.
Рама является основной несущей частью электровоза и служит для размещения на ней всего механического и электрического оборудования, а также создания необходимого сцепного веса. Представляет собой жесткую стальную конструкцию, состоящую из боковых и поперечных листов прокатной стали, скрепляемых сваркой или болтами. Для усиления рамы в средней её части приваривается связывающая полоса, предохраняющая раму от деформации при ударах.
В торцах рамы крепятся сцепные устройства, представляющие собой буфер двухстороннего действия с резиновыми амортизаторами и штыревой сцепкой карманного типа.
Кабина для управления электровозом оборудуется в передней (а на электровозах тяжёлого типа — и задней) частях рамы. Имеет смотровое окно и обеспечивает выход на обе стороны электровоза. В кабине размещаются сиденье машиниста, контроллер, стабилизатор напряжения, звуковой сигнализатор, штурвал тормозной системы, педали управления песочницами, штепсельная коробка, огнетушитель, с внешней стороны — фара освещения.
Тормозная система электровоза включает в себя колодочные тормоза на четыре колеса с ручным приводом и электродинамическое реостатное торможение. В целях фиксации колодочной тормозной системы в заторможенном состоянии последняя снабжена храповым устройством.
Песочная система электровоза предназначена для увеличения сцепления между колёсами и рельсами при трогании с места, при буксовании колёс во время движения и при экстренном торможении состава. Состоит из двух задних и двух передних песочниц, продольных и поперечных тяг, рукояток и педалей управления. Песочницы расположены таким образом, чтобы песок всегда высыпался впереди одной из колёсных пар.
Обе оси электровоза оборудованы индивидуальными взаимозаменяемыми приводами, в состав которых входят тяговый электродвигатель, редуктор, колёсная пара и две буксы. Редуктор может быть двухступенчатым (цилиндрическим или цилиндро-коническим).
Батарейный ящик занимает большую часть рамы аккумуляторного электровоза. Предназначен для размещения аккумуляторных элементов и защиты последних от механических повреждений и попадания воды. Изготавливается из стальных листов толщиной 6—8 мм, а для жёсткости окаймляется с верхней наружной стороны стальными полосами. На батарейном ящике устанавливается автоматический штепсельный выключатель, служащий для подключения батареи к схеме электровоза или зарядному столу.
Для непрерывного контроля и измерения концентрации водорода в батарейном ящике применяется автоматический газоанализатор (типа ПКВ-2 или ТП-1133В и др.). Газоанализатор обеспечивает включение световой сигнализации при достижении предельно-допустимой концентрации водорода (2,5 % по объёму) и выключение сигнализации после её снижения ниже допустимого значения (1,3 %). В комплект поставки газоанализатора ТП-1133В входят первичный преобразователь и блок измерения.
Взрывобезопасность батарейного ящика в исполнении РВ достигается за счёт средств, предотвращающих образование взрывчатых концентраций водорода внутри его оболочки.
В шахтном аккумуляторном электровозе применяются тяговые электродвигатели типа ЭДР-7П мощностью 12 кВт; ДРТ-10; ДРТ-13М мощностью 13 кВт и др..
Включение и выключение тяговых электродвигателей, а также осуществление необходимых режимов движения (пуск, выбег, длительная езда) и реверсирование производится контроллером типа ГР-9М, КРВ-2, КР или КТВ-2.
Защита электродвигателей от перегрузки и силовой цепи от токов короткого замыкания осуществляется автоматом (АВР-2123, АВР-2122, ВАР-4, ВАР-4М, ВРВ-150М, ВАБ и др.).Установка реле максимального тока на 200А производится на заводе-изготовителе.
Для освещения пути перед движущимся или стоящим электровозом служат взрывобезопасные фары ФВУ-3, ФРЭ1.0А, ФРЭ1,0А. Цепь освещения электровозов защищена плавкими предохранителями на 6А. Панель с плавкими вставками установлена в контроллере.
Измерение скорости движения электровоза осуществляется скоростемером (CP-2GPB1ВИ или СР-35, СР), состоящим из двух приборов: датчика и показывающего прибора. Датчик устанавливается в корпусе редуктора привода и имеет механическую связь с валом электродвигателя. Показывающий прибор устанавливается в кабине машиниста. Связь между датчиком и показывающим прибором осуществляется электрическим путём.
Для питания фар электровоза и другой вспомогательной аппаратуры постоянным напряжением 24В служит стабилизатор напряжения во взрывобезопасном исполнении. Устанавливается в кабине, под сиденьем машиниста.
Для подачи сигналов во время движения используется звуковой сигнализатор, установленный в кабине машиниста. Представляет собой механический звонок, состоящий из чашки, бойка, рычажной передачи и педали.
Совершенствование шахтных аккумуляторных электровозов[править | править код]
В 1975 году на базе шахтного аккумуляторного электровоза АМ8Д Дружковским машиностроительным заводом был разработан и выпущен спаренный электровоз 2АМ8Д, в котором была применена безреостатная система управления с секционированием аккумуляторных батарей и ослаблением магнитного потока главных полюсов тяговых электродвигателей. Такая система позволила снизить непроизводительные затраты энергии аккумуляторной батареи в пусковом режиме электровоза.
С 2004 году на базе ходовой части электровоза АМ8Д серийно выпускается шахтный аккумуляторный электровоз нового технического уровня типа АРП8Т, в котором реализованы новая электрическая схема управления и ноу-хау в механической части.
АРП8Т комплектуется бесконтактной транзисторной системой управления, обеспечивающей все необходимые функции и заданные параметры без перегрузок и аварийных ситуаций и исключающей перегрев и преждевременный выход из строя тяговых электродвигателей,
Система электродинамического торможения электровоза с функцией подобной ABS (антиблокировочная система) легкового автомобиля в дополнение к механическим тормозам обеспечивает все необходимые виды торможения и его повышенную эффективность.
На электровозе устанавливается скоростемер СР, обеспечивающий точный контроль скорости движения локомотива.
Импульсный преобразователь напряжения ПНИ обеспечивает стабильные параметры питающего напряжения, отслеживает направление движения электровоза и автоматически включает соответствующую фару.
АРП8Т может комплектоваться как щелочными никель-железными (ТНЖШ), так и кислотными тяговыми аккумуляторными батареями (PzS).
При необходимости АРП8Т можно объединить в спаренный электровоз 2АРП-8Т.
- Ю. Ф. Бутт, Шахтный подземный транспорт: Справочное издание.
К-10 — Википедия
К-10 (КН-10,10КА) | |
---|---|
![]() Электровоз К-10 | |
Страна постройки | ![]() ![]() ![]() |
Заводы | |
Годы постройки | 1971–[по настоящее время] |
Всего построено | К-10 — более 5600, КН-10 — более 900 |
Род службы | шахтный, промышленный |
Род тока и напряжение в контактной сети | постоянный ток, 250 В |
Осевая формула | 2О |
Полный служебный вес | 10 т. |
Нагрузка от движущих осей на рельсы | 5 т. |
Длина локомотива | 4520, 4920 или 5200 мм (в зависимости от модификации) |
Диаметр колёс | 680 мм |
Ширина колеи | 550, 575, 600, 750 и 900 мм |
Тип ТЭД | НБ-33/20 (КН-10) |
Часовая мощность ТЭД | 2×33 кВт |
Сила тяги часового режима | 19 кН |
Скорость часового режима | 11.7 км/ч |
Длительная мощность ТЭД | 2×20 кВт |
Сила тяги длительного режима | 9,5 кН |
Конструкционная скорость | 25 км/ч |
Электрическое торможение | пуско-тормозные реостаты ПТР-27 |
Страны | ![]() ![]() ![]() |
Период | — |
![]() |
Это статья об электровозе. О крылатой ракете см. К-10С.
Электровоз К-10 — контактный узкоколейный шахтный электровоз, предназначенный для эксплуатации на шахтных и промышленных узкоколейных железных дорогах, электрифицированных по системе постоянного тока напряжением 250 В. Используется преимущественно для перевозки составов вагонеток по подземным рельсовым путям угольных шахт и рудников, неопасных по взрыву газа и пыли, но также применяется и в наземной эксплуатации на различных электрифицированных УЖД промышленных предприятий.
Первый электровоз этой серии был выпущен в 1971 году на Александровском машиностроительном заводе, с 1973 года по настоящее время выпускается серийно. В 2011 году был выпущен юбилейный локомотив этой серии с номером 5555[3]. На данный момент электровозы этой серии являются самыми распространёнными шахтными электровозами на территории России. Аналогичные электровозы, имеющие обозначение серии КН-10 и небольшие конструктивные отличия, выпускаются на Новочеркасском электровозостроительном заводе. Также доработанный аналог производится на заводе ЧАО ПКФ «Амплитуда» под маркировкой 10КА.
Электровозы К-10 (КН-10) представляют собой локомотивы с двумя ведущими колесными парами, расположенными в одной раме. Кабина машиниста расположена в концевой части электровоза. Электровозы имеют множество модификаций по форме и высоте кабины машиниста, длине кузова, типу токоприёмника и ширине колеи (наиболее распространенными являются модификации под 750 и 900 мм). Как правило, электровозы, поставляемые на наземные предприятия, оборудуются более просторными кабинами машиниста и рассчитаны на большую высоту контактного провода.
Основными составными узлами кузова являются рама и кабина управления. Рама кузова разборной конструкции, выполнена из двух боковин, соединенных литыми буферными брусьями по концам, двумя промежуточными балками и поперечной стенкой. Подвеска рамы — балансирная, состоит из двух наружных и двух внутренних пружин. Для сглаживания продольных колебаний подрессоренной части используются фрикционные амортизаторы. Верхняя часть кабины машиниста сварной конструкции, крепление её к раме осуществляется при помощи болтовых соединений. Кабина остеклена и снабжена стеклоочистителями, внутри имеется аппаратура управления электрическим и пневматическим оборудованием электровоза, а также сидение машиниста.
Длина кузова электровоза базовой комплектации по раме составляет 4520 мм, длина по буферам штыревых сцепок — 4920 мм, длина базы — 1200 мм, ширина кузова — 1350 мм, высота кузова по крыше кабины от головки рельса — 1650 мм. Расстояние от оси сцепного устройства до головки рельса при новых бандажах составляет 320 мм, Расстояние от головки рельса до рабочей поверхности токоприемника в рабочем положении — 1800—2300 мм. Минимальный радиус проходимых электровозом кривых составляет 12 метров.
Управление электровозом можно осуществлять как из кабины машиниста, так и дистанционно. Для дистанционного управления используется контроллер машиниста КМ-7, состоящий из двух переключателей управления: главного и реверсивного. Коммутирующие контакты главного переключателя собраны на базе кулачковых элементов и оснащены дугогасителями. Контакты реверсивного переключателя пальцевые.
Ходовая часть состоит из двух последовательно расположенных колесно-моторных блоков. Каждый блок включает в себя тяговый электродвигатель, колесную пару, цилиндрическо-конический редуктор и две буксы. На одном колесно-моторном блоке установлен датчик скорости. Тяговый двигатель НБ-33/20 постоянного тока расположен на подвеске опорно-осевого типа и представляет собой 4-полюсную электрическую машину с последовательным возбуждением, защищенного рудничного нормального исполнения, с самовентиляцией.
Стандартная модель электровоза снабжена токоприемником ТРН-Н пантографного типа с предохранительным устройством-синхронизатором, пружинным приводом на подъем и с ручным приводом на опускание из кабины. Рабочая высота токоприёмника составляет от 500 до 1100 мм, масса — 40 кг. Стабилизатор напряжения СН-7 предназначен для преобразования и поддержания в заданных пределах напряжения питания цепей освещения и вспомогательного оборудования.
Электровоз оборудован колодочным тормозом с ручным и пневматическим приводами и электродинамическим реостатным тормозом с ручным приводом от рукоятки контроллера машиниста. Для реостатного пуска и торможения используется пуско-тормозной резистор ПТР-27. Резистор представляет собой блок, состоящий из трех ленточных резисторов рамочного типа, и устанавливается в кузове электровоза.
Электровозы К-10 Зарайского завода строительных материалов[править | править код]
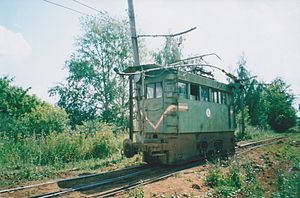
Один из первых электровозов серии К-10 поступил на Зарайский завод строительных материалов в 1971 году для перевозки песка из карьера на завод, где был подвергнут серьёзной модернизации кузова. Традиционная верхняя часть электровоза и прикреплённая к ней сбоку кабина машиниста была убрана, на её место устанавливалась кабина «дирижабельного» типа во всю длину кузова локомотива. Вход в кабину осуществляется с торца, противоположного пульту управления. Электрооборудование было перенесено под пол, а на крыше были установлены прожекторы и два типа токоприёмников — стандартный и боковой. Боковой токоприёмник выполнен в виде штанги, выдвигаемой вручную помощником машиниста, и используется при движении локомотива в точке погрузки, где подвешивание контактного провода возможно только сбоку от пути. Позднее в Зарайск поступило ещё 4 электровоза (последний локомотив — в 1991 году), которые были подвергнуты аналогичной модернизации.[4]
По состоянию на начало 2000-х годов, самый первый электровоз был списан и порезан, остальные 4 локомотива, получившие инвентарные номера от 1 до 4, использовались для перевозки вагонеток (при этом 2 локомотива находились в эксплуатации, а 2 отстаивались в тупиках). Локомотивы обслуживались бригадой из 2-х человек. По состоянию на 2005 год был отставлен от работы электровоз № 1, а в 2008 — № 2. В конце 2008 года узкоколейная железная дорога закрылась, и электровозы находились в заброшенном состоянии до 2010 года. Один из электровозов было решено сохранить как памятник, остальные вероятнее всего были порезаны на металлолом.
-
Заброшенный электровоз № 1
-
Электровоз № 3
-
Кабина электровоза № 3
Шахтный аккумуляторный электровоз — Википедия
Шахтный аккумуляторный электровоз — промышленный локомотив (электровоз) применяемый в угольной промышленности для различных целей.
Шахтные аккумуляторные электровозы составляют 80 % от общего числа применяемых в угольной промышленности локомотивов. Источником электроэнергии шахтных аккумуляторных электровозов являются щелочные никель-железные (ТНЖ и ТНЖШ), никель-кадмиевые (ТНК) и кислотные (PzS) тяговые аккумуляторы, заключённые в батарейный ящик. Шахтные аккумуляторные электровозы выпускаются сцепным весом: 4,5; 5; 7; 8; 10; 14 и 28 тонн.
Область применения
Область применения шахтных аккумуляторных электровозов напрямую связана с уровнем их взрывозащиты.
Шахтные аккумуляторные электровозы, как правило, комплектуются электрооборудованием с уровнем взрывозащиты РВ (рудничное взрывобезопасное), однако из-за аккумуляторной батареи, не отвечающей этому уровню безопасности, имеют исполнение РП (рудничные повышенной надёжности).
Аккумуляторные электровозы, оснащённые взрывобезопасным батарейным ящиком, в целом отвечают уровню взрывозащиты РВ.
Шахтные аккумуляторные электровозы в исполнении РП применяются:
- в откаточных выработках шахт I и II категорий по газу или опасных по пыли;
- в откаточных выработках со свежей струёй воздуха шахт III категории и сверхкатегорийных по газу;
- в откаточных выработках со свежей струёй воздуха на пластах, не опасных по внезапным выбросам, на шахтах, опасных по внезапным выбросам;
Шахтные аккумуляторные электровозы в исполнении РВ применяться:
- в откаточных выработках шахт, опасных по газу или пыли;
- в выработках шахт с исходящей струёй воздуха и тупиковых, проветриваемых вентиляторами местного проветривания;
- на шахтах III категории, сверхкатегорийных по газу и опасных по внезапным выбросам.
В последних двух случаях на электровозах должны быть предусмотрены переносные (индивидуальные) автоматические приборы контроля содержания метана.
Состав шахтного аккумуляторного электровоза
Шахтный аккумуляторный электровоз включает в себя:
- механическое оборудование, состоящее из рамы, буферов, сцепных устройств, кабины, тормозной и песочной систем, редукторов, колесных пар, буксов, батарейного ящика и другого;
- электрическое оборудование, состоящее из тяговых электродвигателей, аккумуляторной батареи, пускорегулирующей аппаратуры (контроллер, пусковые сопротивления, стабилизатор напряжения, автоматический выключатель), аппаратуры сигнализации и освещения.
Рама является основной несущей частью электровоза и служит для размещения на ней всего механического и электрического оборудования, а также создания необходимого сцепного веса. Представляет собой жесткую стальную конструкцию, состоящую из боковых и поперечных листов прокатной стали, скрепляемых сваркой или болтами. Для усиления рамы в средней её части приваривается связывающая полоса, предохраняющая раму от деформации при ударах.
В торцах рамы крепятся сцепные устройства, представляющие собой буфер двухстороннего действия с резиновыми амортизаторами и штыревой сцепкой карманного типа.
Кабина для управления электровозом оборудуется в передней (а на электровозах тяжёлого типа — и задней) частях рамы. Имеет смотровое окно и обеспечивает выход на обе стороны электровоза. В кабине размещаются сиденье машиниста, контроллер, стабилизатор напряжения, звуковой сигнализатор, штурвал тормозной системы, педали управления песочницами, штепсельная коробка, огнетушитель, с внешней стороны — фара освещения.
Тормозная система электровоза включает в себя колодочные тормоза на четыре колеса с ручным приводом и электродинамическое реостатное торможение. В целях фиксации колодочной тормозной системы в заторможенном состоянии последняя снабжена храповым устройством.
Песочная система электровоза предназначена для увеличения сцепления между колёсами и рельсами при трогании с места, при буксовании колёс во время движения и при экстренном торможении состава. Состоит из двух задних и двух передних песочниц, продольных и поперечных тяг, рукояток и педалей управления. Песочницы расположены таким образом, чтобы песок всегда высыпался впереди одной из колёсных пар.
Обе оси электровоза оборудованы индивидуальными взаимозаменяемыми приводами, в состав которых входят тяговый электродвигатель, редуктор, колёсная пара и две буксы. Редуктор может быть двухступенчатым (цилиндрическим или цилиндро-коническим).
Батарейный ящик занимает большую часть рамы аккумуляторного электровоза. Предназначен для размещения аккумуляторных элементов и защиты последних от механических повреждений и попадания воды. Изготавливается из стальных листов толщиной 6 — 8 мм, а для жёсткости окаймляется с верхней наружной стороны стальными полосами. На батарейном ящике устанавливается автоматический штепсельный выключатель, служащий для подключения батареи к схеме электровоза или зарядному столу.
Для непрерывного контроля и измерения концентрации водорода в батарейном ящике применяется автоматический газоанализатор (типа ПКВ-2 или ТП-1133В и др.). Газоанализатор обеспечивает включение световой сигнализации при достижении предельно-допустимой концентрации водорода (2,5 % по объёму) и выключение сигнализации после её снижения ниже допустимого значения (1,3 %). В комплект поставки газоанализатора ТП-1133В входят первичный преобразователь и блок измерения.
Взрывобезопасность батарейного ящика в исполнении РВ достигается за счёт средств, предотвращающих образование взрывчатых концентраций водорода внутри его оболочки.
В шахтном аккумуляторном электровозе применяются тяговые электродвигатели типа ЭДР-7П мощностью 12 кВт; ДРТ-10; ДРТ-13М мощностью 13 кВт и др..
Включение и выключение тяговых электродвигателей, а также осуществление необходимых режимов движения (пуск, выбег, длительная езда) и реверсирование производится контроллером типа ГР-9М, КРВ-2, КР или КТВ-2.
Защита электродвигателей от перегрузки и силовой цепи от токов короткого замыкания осуществляется автоматом (АВР-2123, АВР-2122, ВАР-4, ВАР-4М, ВРВ-150М, ВАБ и др.).
Установка реле максимального тока на 200А производится на заводе- изготовителе.
Для освещения пути перед движущимся или стоящим электровозом служат взрывобезопасные фары ФВУ-3, ФРЭ1.0А, ФРЭ1,0А. Цепь освещения электровозов защищена плавкими предохранителями на 6А. Панель с плавкими вставками установлена в контроллере.
Измерение скорости движения электровоза осуществляется скоростемером (CP-2GPB1ВИ или СР-35, СР), состоящим из двух приборов: датчика и показывающего прибора. Датчик устанавливается в корпусе редуктора привода и имеет механическую связь с валом электродвигателя. Показывающий прибор устанавливается в кабине машиниста. Связь между датчиком и показывающим прибором осуществляется электрическим путём.
Для питания фар электровоза и другой вспомогательной аппаратуры постоянным напряжением 24В служит стабилизатор напряжения во взрывобезопасном исполнении. Устанавливается в кабине, под сиденьем машиниста.
Для подачи сигналов во время движения используется звуковой сигнализатор, установленный в кабине машиниста. Представляет собой механический звонок, состоящий из чашки, бойка, рычажной передачи и педали.
Совершенствование шахтных аккумуляторных электровозов
В 1975 году на базе шахтного аккумуляторного электровоза АМ8Д Дружковским машиностроительным заводом был разработан и выпущен спаренный электровоз 2АМ8Д, в котором была применена безреостатная система управления с секционированием аккумуляторных батарей и ослаблением магнитного потока главных полюсов тяговых электродвигателей. Такая система позволила снизить непроизводительные затраты энергии аккумуляторной батареи в пусковом режиме электровоза.
С 2004 году на базе ходовой части электровоза АМ8Д серийно выпускается шахтный аккумуляторный электровоз нового технического уровня типа АРП8Т, в котором реализованы новая электрическая схема управления и ноу-хау в механической части.
АРП8Т комплектуется бесконтактной транзисторной системой управления, обеспечивающей все необходимые функции и заданные параметры без перегрузок и аварийных ситуаций и исключающей перегрев и преждевременный выход из строя тяговых электродвигателей,
Система электродинамического торможения электровоза с функцией подобной ABS (антиблокировочная система) легкового автомобиля в дополнение к механическим тормозам обеспечивает все необходимые виды торможения и его повышенную эффективность.
На электровозе устанавливается скоростемер СР, обеспечивающий точный контроль скорости движения локомотива.
Импульсный преобразователь напряжения ПНИ обеспечивает стабильные параметры питающего напряжения, отслеживает направление движения электровоза и автоматически включает соответствующую фару.
АРП8Т может комплектоваться как щелочными никель-железными (ТНЖШ), так и кислотными тяговыми аккумуляторными батареями (PzS).
При необходимости АРП8Т можно объединить в спаренный электровоз 2АРП-8Т.
См. также
Литература
- Ю. Ф. Бутт, Шахтный подземный транспорт: Справочное издание.
ИСТОРИЯ ШАХТНЫХ ЭЛЕКТРОВОЗОВ НА СОВЕТСКОМ И ПОСТ-СОВЕТСКОМ ПРОСТРАНСТВЕ
Первые шахты, которые начали возникать в Донбассе были маленькими и примитивными. Откатка угля в них осуществлялась вручную. Постепенно, с укрупнением рудников, стали использовать лошадей. Появилась и шахтерская профессия – коногон, в обязанности которого входила транспортировка угля до шахтного ствола.
Коногон за работой
Как альтернатива «лошадиной откатке» начала применяться транспортировка угля с помощью канатов, так называемая «бесконечная откатка». Но широкого распространения она не получила.
Бесконечная откатка на макеевской шахте
С развитием электричества начали использовать электровозы, которые постепенно вытесняли конский труд из шахт. Первый рудничный локомотив создал немецкий инженер Сименс. В 1879 году на Германской промышленной выставке демонстрировался электровоз Сименса с тяговым усилием 3 тн. На выставке он катал посетителей по всей территории. Скорость составляла 6,5 км/час, а питался локомотив от третьего рельса постоянным током напряжением 160 вольт.
В 1882 г. фирмой «Siemens & Halske» для одной из шахт Германии был построен первый рудничный электровоз. Свой вклад в создание электровозов внес и американский изобретатель Дафт. В 1883 году он построил свой первый электровоз «Ампер». Эта машина весила две тонны и могла тянуть десять тонн с максимальной скоростью 9 миль в час (16,7 км/час), а ее мощность составляла 25 л.с. – значительный прогресс по сравнению с электровозом Сименса. После «Ампера» Дафт построил более мощные локомотивы «Вольта» и «Пачинотти».
Возможность перемещения грузов с помощью электромоторов привлекла к электровозам внимание многих горнопромышленны
В Донбассе впервые локомотивную откатку провели в 1921-23гг. Вначале на Брянском руднике вблизи Алчевска попробовали в работе три бензиновых локомотива, а на шахте Лидиевка – один электровоз. Затем в 1924 году произвели закупку партии электровозов во Франции. Они работали на шахтах Рутченковского рудоуправления и неплохо себя показали.
Французский электровоз, 1924г. Рутченковское рудоуправление
Производство шахтных электровозов советской промышленностью было начато в 1924-1925 гг. Краматорский завод изготовил несколько контактных электровозов, которые работали в шахте «Артем» Александро-Груше
К началу 1930-х годов, а это было время индустриализации Советского Союза, на шахтах стал особенно заметен разрыв между потенциальной возможностью увеличения добычи и низкой пропускной способностью транспортных звеньев. Откатка нуждалась в механизации. Это было возможно только при серийном выпуске электровозов. Подготовка к выпуску электровозов началась на московском заводе «Динамо». Одновременно было закуплено 130 шахтных электровозов за границей.
В 1932 году советская промышленность выпустила 32 аккумуляторных электровоза. Но изготовление советской промышленностью подземных локомотивов не было достаточным и закупки электровозов за границей продолжались. Перелом в механизации шахтного транспорта произошел в годы Второй и Третьей советских пятилеток. К концу 1934 года советские электровозы составили уже 74% общего количества и с этого года закупка зарубежных локомотивов прекратилась. А в Генеральном плане механизации шахт Донбасса электровозная откатка была признана основным видом транспорта для шахт. Другие виды откатки допускались, только при невозможности осуществления электровозной откатки или нецелесообразнос
Первые рудничные аккумуляторные электровозы выпускал московский завод «Динамо» в кооперации с Подольским машиностроительн
Одновременно велись работы по созданию контактных электровозов. Они имели ряд несомненных преимуществ перед аккумуляторными, но круг их применения был узок из-за безопасности по взрывозащищеннос
Правительство наметило переход от частичной механизации угледобычи к комплексной механизации всех процессов. В это время разрыв между механизацией откатки и механизацией выемки и доставки заметно уменьшился. В 1940г. электровозная откатка в общем грузопотоке подземного транспорта составляла 64,5% против 5,5% в 1932г. Одновременно снизилась доля канатной откатки с 11,7% до 9,1%. Конная откатка применялась только на второстепенных откаточных выработках с небольшими грузопотоками. Еще немного статистики: на 1 января 1941 года на шахтах Донецкого бассейна оставалось 5 536 лошадей.
Успехи в механизации откаточных работ в Донецком бассейне были неразрывно связаны с применением малогабаритных контактных и аккумуляторных электровозов. Аккумуляторные – 1-АЛТ-1- выпустили в 1938 году, контактные – 1-ТЛ-1 – в 1939 году и к 1940 году их общее количество составляло 271 шт.
Проводились работы по улучшению и исправлению конструктивных недоработок уже выпускавшихся электровозов. В 1938г. был изготовлен опытный образец контактного электровоза II-ТР, успешно прошедший испытания на шахте №1 им.Челюскинцев г. Сталино и с января 1939г. запущенный в серийное производство. Они заменили устаревшие электровозы типа ЭТР. В 1940г. началось серийное производство аккумуляторных электровозов серии II-АР. В 1939-1941гг. велись работы по выпуску тяжелых контактных локомотивов сцепным весом 14 тн.
Война поломала привычный ход жизни и качественно отбросила назад многих производителей. В годы войны Александровский машиностроительн
К началу восстановительны
Основание этого предприятия характерно для многих современных промышленных производств Донбасса. В августе 1920 г. на базе заводов Донецкого и Торецкого обществ был создан единый Торецкий сталелитейный и механический завод. Завод изготавливал оборудование для шахт и железных дорог.
В 1938 г. завод переходит в подчинение Наркомата угольной промышленности СССР и становится заводом угольного машиностроения. В начале 1941 г. завод имел в своем составе 24 цеха и изготавливал платформы на гусеничном ходу для торфяной промышленности; погрузочные машины АМ-2; экскаваторы системы Рикмана; породопогрузочны
Нападение Германии на СССР в 1941 г. прервало работу завода. 11 октября 1941 г. завершилась эвакуация завода в г.Александровск Пермской области, где он был быстро восстановлен и начал выпуск продукции для нужд фронта.
В октябре 1943 г., после освобождения Дружковки, началось восстановление машиностроительн
В 1949 году был разработан государственный стандарт на рудничные электровозы постоянного тока. Унифицированы конструкции электровозов. Разработаны технические, а затем и рабочие проекты электровозов 7КР, 10КР, 14КР, 8АРП и 12АРП. К началу 1950-х годов численность парка электровозов превысила довоенную. Увеличилась и номенклатура выпускаемых электровозов. В 1958-1962гг. создаются мощные рудничные локомотивы, имеющие большой сцепной вес, большие скорости движения и полностью удовлетворяющие требованиям безопасности при работе в газовой среде. На Дружковском машиностроительн
Немного статистики. В 1966г. на шахтах Донбасса для транспортных целей использовалось свыше 1850 наклонных выработок, общая протяженность выработок – 1400 км, из них более 400 км двухпутевых. Средняя численность рабочих подземного транспорта на 1000 тн суточной добычи составляла 101 человек. С 1960-х гг. рудничные электровозы оборудовались исключительно аккумуляторными элементами ТЖН-300, ТЖН-350, ТЖН-450, ТЖН-550 производства Луганского и Курского аккумуляторных заводов. Электровозы 8АРП и 10КР не уступали лучшим иностранным образцам, а тяжелые электровозы 14 КР-1 по многим техническим характеристикам их превосходили.
Когда Украина стала независимым государством, наиболее распространенным в Донбассе был электровоз АМ8Д, созданный в конце 1980-х Дружковским машзаводом. Разработка двадцатилетней давности не соответствовала требованиям по безопасности шахтного электротранспорт
В Донецке, на базе ремонтного завода было создано предприятие «Амплитуда». Постоянно занимаясь ремонтом АМ8Д, специалисты Частного акционерного общества ПКФ «Амплитуда» «прощупали» все его слабые и сильные места и точно знали, как улучшить механизм с точки зрения безопасности – самой важной точки зрения под землей. Руководством «Амплитуды» была создана команда высококвалифицир
Сегодня ЧАО ПКФ «Амплитуда» отличается высоким ассортиментом выпускаемой продукции. Освоен выпуск контактных шахтных электровозов 14КА, 10КА, 7КА, 4КА, аккумуляторных электровозов АРП8Т, АРП4,5Т, АРП7Т, АРП2Т, комплектующего электрооборудова
Аккумуляторный электровоз АРП2Т (ЧАО «ПКФ «Амплитуда», Украина)
Контактный электровоз 10КА (ЧАО «ПКФ «Амплитуда», Украина)
Шахтный аккумуляторный электровоз — Википедия
Шахтный аккумуляторный электровоз — промышленный локомотив (электровоз) применяемый в угольной промышленности для различных целей.
Шахтные аккумуляторные электровозы составляют 80 % от общего числа применяемых в угольной промышленности локомотивов. Источником электроэнергии шахтных аккумуляторных электровозов являются щелочные никель-железные (ТНЖ и ТНЖШ), никель-кадмиевые (ТНК) и кислотные (PzS) тяговые аккумуляторы, заключённые в батарейный ящик. Шахтные аккумуляторные электровозы выпускаются сцепным весом: 4,5; 5; 7; 8; 10; 14 и 28 тонн.
Область применения
Область применения шахтных аккумуляторных электровозов напрямую связана с уровнем их взрывозащиты.
Шахтные аккумуляторные электровозы, как правило, комплектуются электрооборудованием с уровнем взрывозащиты РВ (рудничное взрывобезопасное), однако из-за аккумуляторной батареи, не отвечающей этому уровню безопасности, имеют исполнение РП (рудничные повышенной надёжности).
Аккумуляторные электровозы, оснащённые взрывобезопасным батарейным ящиком, в целом отвечают уровню взрывозащиты РВ.
Шахтные аккумуляторные электровозы в исполнении РП применяются:
- в откаточных выработках шахт I и II категорий по газу или опасных по пыли;
- в откаточных выработках со свежей струёй воздуха шахт III категории и сверхкатегорийных по газу;
- в откаточных выработках со свежей струёй воздуха на пластах, не опасных по внезапным выбросам, на шахтах, опасных по внезапным выбросам;
Шахтные аккумуляторные электровозы в исполнении РВ применяться:
- в откаточных выработках шахт, опасных по газу или пыли;
- в выработках шахт с исходящей струёй воздуха и тупиковых, проветриваемых вентиляторами местного проветривания;
- на шахтах III категории, сверхкатегорийных по газу и опасных по внезапным выбросам.
В последних двух случаях на электровозах должны быть предусмотрены переносные (индивидуальные) автоматические приборы контроля содержания метана.
Состав шахтного аккумуляторного электровоза
Шахтный аккумуляторный электровоз включает в себя:
- механическое оборудование, состоящее из рамы, буферов, сцепных устройств, кабины, тормозной и песочной систем, редукторов, колесных пар, буксов, батарейного ящика и другого;
- электрическое оборудование, состоящее из тяговых электродвигателей, аккумуляторной батареи, пускорегулирующей аппаратуры (контроллер, пусковые сопротивления, стабилизатор напряжения, автоматический выключатель), аппаратуры сигнализации и освещения.
Рама является основной несущей частью электровоза и служит для размещения на ней всего механического и электрического оборудования, а также создания необходимого сцепного веса. Представляет собой жесткую стальную конструкцию, состоящую из боковых и поперечных листов прокатной стали, скрепляемых сваркой или болтами. Для усиления рамы в средней её части приваривается связывающая полоса, предохраняющая раму от деформации при ударах.
В торцах рамы крепятся сцепные устройства, представляющие собой буфер двухстороннего действия с резиновыми амортизаторами и штыревой сцепкой карманного типа.
Кабина для управления электровозом оборудуется в передней (а на электровозах тяжёлого типа — и задней) частях рамы. Имеет смотровое окно и обеспечивает выход на обе стороны электровоза. В кабине размещаются сиденье машиниста, контроллер, стабилизатор напряжения, звуковой сигнализатор, штурвал тормозной системы, педали управления песочницами, штепсельная коробка, огнетушитель, с внешней стороны — фара освещения.
Тормозная система электровоза включает в себя колодочные тормоза на четыре колеса с ручным приводом и электродинамическое реостатное торможение. В целях фиксации колодочной тормозной системы в заторможенном состоянии последняя снабжена храповым устройством.
Песочная система электровоза предназначена для увеличения сцепления между колёсами и рельсами при трогании с места, при буксовании колёс во время движения и при экстренном торможении состава. Состоит из двух задних и двух передних песочниц, продольных и поперечных тяг, рукояток и педалей управления. Песочницы расположены таким образом, чтобы песок всегда высыпался впереди одной из колёсных пар.
Обе оси электровоза оборудованы индивидуальными взаимозаменяемыми приводами, в состав которых входят тяговый электродвигатель, редуктор, колёсная пара и две буксы. Редуктор может быть двухступенчатым (цилиндрическим или цилиндро-коническим).
Батарейный ящик занимает большую часть рамы аккумуляторного электровоза. Предназначен для размещения аккумуляторных элементов и защиты последних от механических повреждений и попадания воды. Изготавливается из стальных листов толщиной 6 — 8 мм, а для жёсткости окаймляется с верхней наружной стороны стальными полосами. На батарейном ящике устанавливается автоматический штепсельный выключатель, служащий для подключения батареи к схеме электровоза или зарядному столу.
Для непрерывного контроля и измерения концентрации водорода в батарейном ящике применяется автоматический газоанализатор (типа ПКВ-2 или ТП-1133В и др.). Газоанализатор обеспечивает включение световой сигнализации при достижении предельно-допустимой концентрации водорода (2,5 % по объёму) и выключение сигнализации после её снижения ниже допустимого значения (1,3 %). В комплект поставки газоанализатора ТП-1133В входят первичный преобразователь и блок измерения.
Взрывобезопасность батарейного ящика в исполнении РВ достигается за счёт средств, предотвращающих образование взрывчатых концентраций водорода внутри его оболочки.
В шахтном аккумуляторном электровозе применяются тяговые электродвигатели типа ЭДР-7П мощностью 12 кВт; ДРТ-10; ДРТ-13М мощностью 13 кВт и др..
Включение и выключение тяговых электродвигателей, а также осуществление необходимых режимов движения (пуск, выбег, длительная езда) и реверсирование производится контроллером типа ГР-9М, КРВ-2, КР или КТВ-2.
Защита электродвигателей от перегрузки и силовой цепи от токов короткого замыкания осуществляется автоматом (АВР-2123, АВР-2122, ВАР-4, ВАР-4М, ВРВ-150М, ВАБ и др.).
Установка реле максимального тока на 200А производится на заводе- изготовителе.
Для освещения пути перед движущимся или стоящим электровозом служат взрывобезопасные фары ФВУ-3, ФРЭ1.0А, ФРЭ1,0А. Цепь освещения электровозов защищена плавкими предохранителями на 6А. Панель с плавкими вставками установлена в контроллере.
Измерение скорости движения электровоза осуществляется скоростемером (CP-2GPB1ВИ или СР-35, СР), состоящим из двух приборов: датчика и показывающего прибора. Датчик устанавливается в корпусе редуктора привода и имеет механическую связь с валом электродвигателя. Показывающий прибор устанавливается в кабине машиниста. Связь между датчиком и показывающим прибором осуществляется электрическим путём.
Для питания фар электровоза и другой вспомогательной аппаратуры постоянным напряжением 24В служит стабилизатор напряжения во взрывобезопасном исполнении. Устанавливается в кабине, под сиденьем машиниста.
Для подачи сигналов во время движения используется звуковой сигнализатор, установленный в кабине машиниста. Представляет собой механический звонок, состоящий из чашки, бойка, рычажной передачи и педали.
Совершенствование шахтных аккумуляторных электровозов
В 1975 году на базе шахтного аккумуляторного электровоза АМ8Д Дружковским машиностроительным заводом был разработан и выпущен спаренный электровоз 2АМ8Д, в котором была применена безреостатная система управления с секционированием аккумуляторных батарей и ослаблением магнитного потока главных полюсов тяговых электродвигателей. Такая система позволила снизить непроизводительные затраты энергии аккумуляторной батареи в пусковом режиме электровоза.
С 2004 году на базе ходовой части электровоза АМ8Д серийно выпускается шахтный аккумуляторный электровоз нового технического уровня типа АРП8Т, в котором реализованы новая электрическая схема управления и ноу-хау в механической части.
АРП8Т комплектуется бесконтактной транзисторной системой управления, обеспечивающей все необходимые функции и заданные параметры без перегрузок и аварийных ситуаций и исключающей перегрев и преждевременный выход из строя тяговых электродвигателей,
Система электродинамического торможения электровоза с функцией подобной ABS (антиблокировочная система) легкового автомобиля в дополнение к механическим тормозам обеспечивает все необходимые виды торможения и его повышенную эффективность.
На электровозе устанавливается скоростемер СР, обеспечивающий точный контроль скорости движения локомотива.
Импульсный преобразователь напряжения ПНИ обеспечивает стабильные параметры питающего напряжения, отслеживает направление движения электровоза и автоматически включает соответствующую фару.
АРП8Т может комплектоваться как щелочными никель-железными (ТНЖШ), так и кислотными тяговыми аккумуляторными батареями (PzS).
При необходимости АРП8Т можно объединить в спаренный электровоз 2АРП-8Т.
См. также
Литература
- Ю. Ф. Бутт, Шахтный подземный транспорт: Справочное издание.
Электровоз контактный шахтный К-10 — MiningWiki — шахтёрская энциклопедия
Материал из MiningWiki — свободной шахтёрской энциклопедии
Электровоз К-10Электровоз К-10 — контактный узкоколейный шахтный электровоз, предназначенный для эксплуатации на шахтных и промышленных узкоколейных железных дорогах, электрифицированных по системе постоянного тока напряжением 250 В. Используется преимущественно для перевозки составов вагонеток по подземным рельсовым путям угольных шахт и рудников, неопасных по взрыву газа и пыли, но также применяется и в наземной эксплуатации на различных электрифицированных УЖД промышленных предприятий.
Первый электровоз этой серии был выпущен в 1971 году на Александровском машиностроительном заводе, с 1973 года по настоящее время выпускается серийно. В 2011 году был выпущен юбилейный локомотив этой серии с номером 5555. На данный момент электровозы этой серии являются самыми распространёнными шахтными электровозами на территории России. Аналогичные электровозы, имеющие обозначение серии КН-10 и небольшие конструктивные отличия, выпускаются на Новочеркасском электровозостроительном заводе. Так же доработанный аналог производится на заводе ЧАО ПКФ «Амплитуда» по маркировкой 10КА.
Электровозы К-10 (КН-10) представляют собой локомотивы с двумя ведущими колесными парами, расположенными в одной раме. Кабина машиниста расположена в концевой части электровоза. Электровозы имеют множество модификаций по форме и высоте кабины машиниста, длине кузова, типу токоприёмника и ширине колеи (наиболее распространенными являются модификации под 750 и 900 мм). Как правило, электровозы, поставляемые на наземные предприятия, оборудуются более просторными кабинами машиниста и рассчитаны на большую высоту контактного провода.
Основными составными узлами кузова являются рама и кабина управления. Рама кузова разборной конструкции, выполнена из двух боковин, соединенных литыми буферными брусьями по концам, двумя промежуточными балками и поперечной стенкой. Подвеска рамы — балансирная, состоит из двух наружных и двух внутренних пружин. Для сглаживания продольных колебаний подрессоренной части используются фрикционные амортизаторы. Верхняя часть кабины машиниста сварной конструкции, крепление ее к раме осуществляется при помощи болтовых соединений. Кабина остеклена и снабжена стеклоочистителями, внутри имеется аппаратура управления электрическим и пневматическим оборудованием электровоза, а также сидение машиниста.
Длина кузова электровоза базовой комплектации по раме составляет 4520 мм, длина по буферам штыревых сцепок — 4920 мм, длина базы — 1200 мм, ширина кузова — 1350 мм, высота кузова по крыше кабины от головки рельса — 1650 мм. Расстояние от оси сцепного устройства до головки рельса при новых бандажах составляет 320 мм, Расстояние от головки рельса до рабочей поверхности токоприемника в рабочем положении — 1800—2300 мм. Минимальный радиус проходимых электровозом кривых составляет 12 метров.
Управление электровозом можно осуществлять как из кабины машиниста, так и дистанционно. Для дистанционного управления используется контроллер машиниста КМ-7, состоящий из двух переключателей управления: главного и реверсивного. Коммутирующие контакты главного переключателя собраны на базе кулачковых элементов и оснащены дугогасителями. Контакты реверсивного переключателя пальцевые.
Ходовая часть состоит из двух последовательно расположенных колесно-моторных блоков. Каждый блок включает в себя тяговый электродвигатель, колесную пару, цилиндрическо-конический редуктор и две буксы. На одном колесно-моторном блоке установлен датчик скорости. Тяговый двигатель НБ-33/20 постоянного тока расположен на подвеске опорно-осевого типа и представляет собой 4-полюсную электрическую машину с последовательным возбуждением, защищенного рудничного нормального исполнения, с самовентиляцией.
Стандартная модель электровоза снабжена токоприемником ТРН-Н пантографного типа с предохранительным устройством-синхронизатором, пружинным приводом на подъем и с ручным приводом на опускание из кабины.
Рабочая высота токоприёмника составляет от 500 до 1100 мм, масса — 40 кг. Стабилизатор напряжения СН-7 предназначен для преобразования и поддержания в заданных пределах напряжения питания цепей освещения и вспомогательного оборудования.
Электровоз оборудован колодочным тормозом с ручным и пневматическим приводами и электродинамическим реостатным тормозом с ручным приводом от рукоятки контроллера машиниста. Для реостатного пуска и торможения используется пуско-тормозной резистор ПТР-27. Резистор представляет собой блок, состоящий из трех ленточных резисторов рамочного типа, и устанавливается в кузове электровоза.
Технические характеристики | |||
---|---|---|---|
Сцепная масса, т | 10 | ||
Параметры часового режима:
| 66 11,7 1900 | ||
Напряжение сети, В | 250 | ||
Ширина колеи, мм | 600, 750, 900 | ||
Габаритные размеры, мм: | 5200 1350 1650 | ||
Клиренс, мм | 80 |
Электровоз контактный шахтный К-10 — это оборудование рудничного транспорта | |
---|---|
Электровоз шахтный контактный — SMZ
Электровоз шахтный контактный — SMZул. Светлодарская, 65, г. Славянск, Донецкая обл., Украина, 84122
Электровоз рудничный контактный модель Эр.К14У-750-М1 выполняет функции тягового локомотива при транспортировании составов вагонеток с полезным ископаемым, оборудованием, материалами и/или породой, а также для перевозки людей в специальных пассажирских вагонетках по подземным горным выработкам оборудованных рельсовой колеей шириной 750мм шахт и рудников, неопасных по газу и пыли.
В электровозе применена индивидуальная пружинная подвеска рамы, разъемная букса, усовершенствованы редуктор и тормозная система. Кабина машиниста выполнена отдельно от рамы электровоза и имеет свою подвеску
Параметр | Значение |
Масса электровоза, кг | 14000 |
Мощность тяговых электродвигателей часового режима, кВт, не менее | 45×2=90 |
Скорость часового режима (средняя), км/ч | 12,6 |
Сила тяги часового режима, кН | 25 |
Жесткая база (по конечным парам), мм | 1700 |
Ширина колеи колесной пары (между ребордами),мм | 750 |
Габаритные размеры: |
|
— длина по буферам, мм | 5200 |
— ширина по раме,мм | 1350 |
— высота по кабине машиниста,мм | 1700 |
Диаметр колеса, мм | 680 |
Клиренс (дорожный просвет), мм | 115 |
Рабочий диапазон движений токоприемников, мм | 1800-2500 |
Система управления | Реостатная, транзисторная |
Рабочее напряжение, Вольт/род тока | 250 / постоянный |
error: Content is protected !!