Что делают из металла?
С тех пор, как люди добыли металл и впервые изготовили из него орудие труда, все металлы прочно вошли в нашу жизнь. Сейчас без изделий из металла не обходится ни одна сфера жизни человека. Все металлы обладают отличными физическими свойствами. У них достаточно высокие температуры плавления и кипения, при этом, отличная пластичность, ковкость и электропроводность.
Все это объясняет столь широкое применение металлов в жизнедеятельности человека, а также причины, по которым именно из металлов изготавливают большую часть изделий, которые человек ежедневно применяет в собственной жизни. Для изготовления деталей из металла Вам стоит обратится центр металлообработки, где квалифицированные работники выполнят ваш заказ.
Металлы не горят в огне, большинство из них способны выдержать огромные температуры, не изменив, при этом, своих свойств. Но, к сожалению, не все, что используется человеком для жизни, изготавливается из металлов. В частности, жилище и другие здания и сооружения изготавливаются из материалов, которые плохо переносят высокие температуры и огонь, а, следовательно, вполне могут быть подвержены пожарам. Поэтому, чтобы облегчить эвакуацию с места пожара, необходимо везде вешать планы.
Металл активно используют и в художественной ковке.
После того, как рабочие чертежи утверждены, они попадают на производственный участок. Новые технологии проникли и на кузнечное производство, помогая создавать ажурные, неповторимые изделия, способные исправно служить не только Вам и Вашим детям, но внукам и даже их потомкам.
При всей современной технологичности, искусство художественной ковки, как и всякое искусство, не поддается автоматизации. Механика только помогает мастеру, но и в XXI веке кованое изделие все равно так же несет теплоту человеческих рук.
Металлы — Википедия
О соответствующем направлении рок-музыки см. Метал.Мета́ллы (от лат. metallum — шахта, рудник) — группа элементов в виде простых веществ, обладающих характерными металлическими свойствами, такими, как высокие тепло- и электропроводность, положительный температурный коэффициент сопротивления, высокая пластичность, ковкость и металлический блеск.
Из 118 химических элементов, открытых на 2019 год, к металлам часто относят (единого общепринятого определения нет, например, полуметаллы и полупроводники не всегда относят к металлам):
6 элементов в группе щелочных металлов: Li, Na, K, Rb, Cs, Fr;
4 в группе щёлочноземельных металлов: Ca, Sr, Ba, Ra; к щёлочноземельным также иногда относят Mg, и Be;
38 в группе переходных металлов:
— Sc, Ti, V, Cr, Mn, Fe, Co, Ni, Cu, Zn;
— Hf, Ta, W, Re, Os, Ir, Pt, Au, Hg;
— Rf, Db, Sg, Bh, Hs, Mt, Ds, Rg, Cn;
7 в группе лёгких металлов: Al, Ga, In, Sn, Tl, Pb, Bi;
7 в группе полуметаллов[1]: B, Si, Ge, As, Sb, Te, Po;
14 в группе лантаноиды + лантан (La):
Ce, Pr, Nd, Pm, Sm, Eu, Gd, Tb, Dy, Ho, Er, Tm, Yb, Lu;
14 в группе актиноиды (физические свойства изучены не у всех элементов) + актиний (Ac):
Th, Pa, U, Np, Pu, Am, Cm, Bk, Cf, Es, Fm, Md, No, Lr.
Также металлическими свойствами может обладать водород[2][3].
Таким образом, к металлам могут относится более 90 элементов из всех открытых.
В астрофизике термин «металл» может иметь другое значение и обозначать все химические элементы тяжелее гелия (см. Металличность).
Кроме того, в физике металлам, как проводникам, противопоставляется полупроводники и диэлектрики (см. также Полуметалл (спинтроника)
)[4].Некоторые группы/семейства металлов[править | править код]
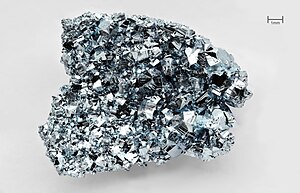
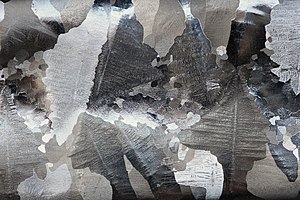
- Щелочные:
- Щёлочноземельные:
- Другие (которые зачастую не совсем правильно относят к щёлочноземельным):
- Переходные:
- Постпереходные:
- Тугоплавкие
- Металлы платиновой группы
- Цветные
- Благородные
- Монетные
Аморфные металлы[править | править код]
Слово «металл» заимствовано из немецкого языка. Отмечается в «Травнике» Николая Любчанина, написанном в 1534 году: «…злато и серебро всех металей одолеваетъ». Окончательно усвоено в Петровскую эпоху. Первоначально имело общее значение «минерал, руда, металл»; разграничение этих понятий произошло в эпоху М. В. Ломоносова[5].
![]() | Металлом называется светлое тело, которое ковать можно. Таких тел находим только шесть: золото, серебро, медь, олово, железо и свинец. Разделяются на высокие и простые металлы; которое разнство в том состоит, что высоких одним огнём без помощи других материй в пепел сожечь не можно, а напротив того простые через едину онаго силу в пепел обращаются. … За полуметаллы почитаются мышьяк, сурьма, висмут, цинк и ртуть.М. В. Ломоносов | ![]() |
Немецкое слово «metall» заимствовано из латинского языка, где «metallum» — «рудник, металл». Латинское, в свою очередь, заимствовано из греческого языка (μεταλλον — «рудник, копь»).[6]
Бо́льшая часть металлов присутствует в природе в виде руд и соединений. Они образуют оксиды, сульфиды, карбонаты и другие химические соединения. Для получения чистых металлов и дальнейшего их применения необходимо выделить их из руд и провести очистку. При необходимости проводят легирование и другую обработку металлов. Изучением этого занимается наука металлургия. Металлургия различает руды чёрных металлов (на основе железа) и цветных (в их состав не входит железо, всего около 70 химических элементов). Золото, серебро и платина относятся также к драгоценным (благородным) металлам. Кроме того, в малых количествах они присутствуют в морской воде и в живых организмах (играя при этом важную роль).
Известно, что организм человека на 3 % состоит из металлов[7]. Больше всего в организме кальция (в костях) и натрия, выступающего в роли электролита в межклеточной жидкости и цитоплазме. Магний накапливается в мышцах и нервной системе, медь — в печени, железо — в крови.
Подготовка руды
Металлы извлекают из земли в процессе добычи полезных ископаемых. Добытые руды служат относительно богатым источником необходимых элементов. Для выяснения нахождения руд в земной коре используются специальные поисковые методы, включающие разведку и исследование рудных месторождений. Месторождения руд разрабатываются открытым или карьерным способом и подземным или шахтным способом. Иногда применяется комбинированный (открыто-подземный) способ разработки рудных месторождений.
После извлечения руд они, как правило, подвергаются обогащению. При этом из исходного минерального сырья выделяют один или несколько полезных компонентов — рудный концентрат(ы), промпродукты и отвальные хвосты. В процессах обогащения используют отличия минералов полезного компонента и пустой породы в плотности, магнитной восприимчивости, смачиваемости, электропроводности, крупности, форме зёрен, химических свойствах и др.
Работа с рудой
Из добытой и обогащённой руды металлы извлекаются, как правило, с помощью химического или электролитического восстановления. В пирометаллургии для преобразования руды в металлическое сырьё используются высокие температуры, в гидрометаллургии применяют для тех же целей водную химию. Используемые методы зависят от вида металла и типа загрязнения.
Когда металлическая руда является ионным соединением металла и неметалла, для извлечения чистого металла она обычно подвергается выплавлению — нагреву с восстановителем. Многие распространённые металлы, такие как железо, медь, олово, плавят с использованием углерода в качестве восстановителя. Некоторые металлы, такие как алюминий и натрий, не имеют ни одного экономически оправданного восстановителя и извлекаются с применением электролиза.[8][9]
Сульфидные руды не улучшаются непосредственно до получения чистого металла, но обжигаются на воздухе, с целью преобразования их в окислы.
Твёрдость[править | править код]
Все металлы (кроме ртути и, условно, франция) при нормальных условиях находятся в твёрдом состоянии, однако обладают различной твёрдостью. Ниже в таблице приводится твёрдость некоторых металлов по шкале Мооса.
Температура плавления[править | править код]
Температуры плавления чистых металлов лежат в диапазоне от −39 °C (ртуть) до 3410 °C (вольфрам). Температура плавления большинства металлов (за исключением щелочных) высока, однако некоторые металлы, например, олово и свинец, могут расплавиться на обычной электрической или газовой плите.
Плотность[править | править код]
В зависимости от плотности, металлы делят на лёгкие (плотность 0,53 ÷ 5 г/см³) и тяжёлые (5 ÷ 22,5 г/см³). Самым лёгким металлом является литий (плотность 0,53 г/см³). Самый тяжёлый металл в настоящее время назвать невозможно, так как плотности осмия и иридия — двух самых тяжёлых металлов — почти равны (около 22,6 г/см³ — ровно в два раза выше плотности свинца), а вычислить их точную плотность крайне сложно: для этого нужно полностью очистить металлы, ведь любые примеси снижают их плотность.
Пластичность[править | править код]
Большинство металлов пластичны, то есть металлическую проволоку можно согнуть, и она не сломается. Это происходит из-за смещения слоёв атомов металлов без разрыва связи между ними. Самыми пластичными являются золото, серебро и медь. Из золота можно изготовить фольгу толщиной 0,003 мм, которую используют для золочения изделий. Однако не все металлы пластичны. Проволока из цинка или олова хрустит при сгибании; марганец и висмут при деформации вообще почти не сгибаются, а сразу ломаются. Пластичность зависит и от чистоты металла; так, очень чистый хром весьма пластичен, но, загрязнённый даже незначительными примесями, становится хрупким и более твёрдым. Некоторые металлы, такие, как золото, серебро, свинец, алюминий, осмий, могут срастаться между собой, но на это могут уйти десятки лет.Электропроводность[править | править код]
Все металлы хорошо проводят электрический ток; это обусловлено наличием в их кристаллических решётках подвижных электронов, перемещающихся под действием электрического поля. Серебро, медь и алюминий имеют наибольшую электропроводность; по этой причине последние два металла чаще всего используют в качестве материала для проводов. Очень высокую электропроводность имеет также натрий, в экспериментальной аппаратуре известны попытки применения натриевых токопроводов в форме тонкостенных труб из нержавеющей стали, заполненных натрием. Благодаря малому удельному весу натрия, при равном сопротивлении натриевые «провода» получаются значительно легче медных и даже несколько легче алюминиевых.
Теплопроводность[править | править код]
Высокая теплопроводность металлов также зависит от подвижности свободных электронов. Поэтому ряд теплопроводностей похож на ряд электропроводностей, и лучшим проводником тепла, как и электричества, является серебро. Натрий также находит применение как хороший проводник тепла; широко известно, например, применение натрия в клапанах автомобильных двигателей для улучшения их охлаждения.
Наименьшая теплопроводность — у висмута и ртути.
Цвет[править | править код]
Цвет у большинства металлов примерно одинаковый — светло-серый с голубоватым оттенком. Золото, медь и цезий соответственно жёлтого, красного и светло-жёлтого цвета.
Взаимодействие с простыми веществами[править | править код]
На внешнем электронном уровне у большинства металлов небольшое количество электронов (1-3), поэтому они в большинстве реакций выступают как восстановители (то есть «отдают» свои электроны).
Реакции с простыми веществами
- С кислородом реагируют все металлы, кроме золота и платиновых металлов. Реакция с серебром происходит при высоких температурах, но оксид серебра(II) практически не образуется, так как он термически неустойчив. В зависимости от металла на выходе могут оказаться оксиды, пероксиды, надпероксиды:
- 4Li+O2=2Li2O{\displaystyle {\mathsf {4Li+O_{2}=2Li_{2}O}}} оксид лития
- 2Na+O2=Na2O2{\displaystyle {\mathsf {2Na+O_{2}=Na_{2}O_{2}}}} пероксид натрия
- K+O2=KO2{\displaystyle {\mathsf {K+O_{2}=KO_{2}}}} надпероксид калия
Чтобы получить из пероксида оксид, пероксид восстанавливают металлом:
- Na2O2+2Na=2Na2O{\displaystyle {\mathsf {Na_{2}O_{2}+2Na=2Na_{2}O}}}
Со средними и малоактивными металлами реакция происходит при нагревании:
- 3Fe+2O2=Fe3O4{\displaystyle {\mathsf {3Fe+2O_{2}=Fe_{3}O_{4}}}}
- 2Hg+O2=2HgO{\displaystyle {\mathsf {2Hg+O_{2}=2HgO}}}
- 2Cu+O2=2CuO{\displaystyle {\mathsf {2Cu+O_{2}=2CuO}}}
- С азотом реагируют только самые активные металлы, при комнатной температуре взаимодействует только литий, образуя нитриды:
- 6Li+N2=2Li3N{\displaystyle {\mathsf {6Li+N_{2}=2Li_{3}N}}}
При нагревании:
- 2Al+N2=2AlN{\displaystyle {\mathsf {2Al+N_{2}=2AlN}}}
- 3Ca+N2=Ca3N2{\displaystyle {\mathsf {3Ca+N_{2}=Ca_{3}N_{2}}}}
- С серой реагируют все металлы, кроме золота и платины.
Железо взаимодействует с серой при нагревании, образуя сульфид:
- Fe+S=FeS{\displaystyle {\mathsf {Fe+S=FeS}}}
- С водородом реагируют только самые активные металлы, то есть металлы IA и IIA групп, кроме Be. Реакции осуществляются при нагревании, при этом образуются гидриды. В реакциях металл выступает как восстановитель, степень окисления водорода −1:
- 2Na+h3=2NaH{\displaystyle {\mathsf {2Na+H_{2}=2NaH}}}
- Mg+h3=Mgh3{\displaystyle {\mathsf {Mg+H_{2}=MgH_{2}}}}
- С углеродом реагируют только наиболее активные металлы. При этом образуются ацетилениды или метаниды. Ацетилениды при взаимодействии с водой дают ацетилен, метаниды — метан.
- 2Na+2C=Na2C2{\displaystyle {\mathsf {2Na+2C=Na_{2}C_{2}}}}
- Na2C2+2h3O=2NaOH+C2h3{\displaystyle {\mathsf {Na_{2}C_{2}+2H_{2}O=2NaOH+C_{2}H_{2}}}}
С кислотами металлы реагируют по-разному. Металлы, стоящие в электрохимическом ряду активности металлов (ЭРАМ) до водорода, взаимодействуют практически со всеми кислотами.
Взаимодействие неокисляющих кислот с металлами, стоящими в электрическом ряду активности металлов до водорода[править | править код]
Происходит реакция замещения, которая также является окислительно-восстановительной:
- Mg+2HCl=MgCl2+h3↑{\displaystyle {\mathsf {Mg+2HCl=MgCl_{2}+H_{2}\uparrow }}}
- 2Al+2h4PO4=2AlPO4+3h3↑{\displaystyle {\mathsf {2Al+2H_{3}PO_{4}=2AlPO_{4}+3H_{2}\uparrow }}}
Взаимодействие концентрированной серной кислоты H2SO4 с металлами[править | править код]
Окисляющие кислоты могут взаимодействовать и с металлами, стоящими в ЭРАМ после водорода:
- Cu+2h3SO4=CuSO4+SO2↑+2h3O{\displaystyle {\mathsf {Cu+2H_{2}SO_{4}=CuSO_{4}+SO_{2}\uparrow +2H_{2}O}}}
Сильно разбавленная кислота реагирует с металлом по классической схеме:
- Mg+h3SO4=MgSO4+h3↑{\displaystyle {\mathsf {Mg+H_{2}SO_{4}=MgSO_{4}+H_{2}\uparrow }}}
При увеличении концентрации кислоты образуются различные продукты:
- Mg+2h3SO4=MgSO4+SO2↑+2h3O{\displaystyle {\mathsf {Mg+2H_{2}SO_{4}=MgSO_{4}+SO_{2}\uparrow +2H_{2}O}}}
- 3Mg+4h3SO4=3MgSO4+S↓+4h3O{\displaystyle {\mathsf {3Mg+4H_{2}SO_{4}=3MgSO_{4}+S\downarrow +4H_{2}O}}}
- 4Mg+5h3SO4=4MgSO4+h3S↑+4h3O{\displaystyle {\mathsf {4Mg+5H_{2}SO_{4}=4MgSO_{4}+H_{2}S\uparrow +4H_{2}O}}}
Реакции для азотной кислоты (HNO3)[править | править код]
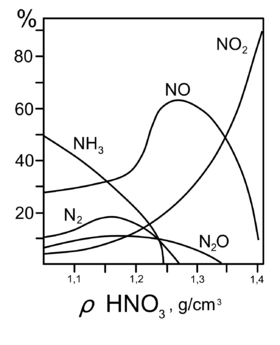
- Cu+4HNO3(60%)=Cu(NO3)2+2NO2↑+2h3O{\displaystyle {\mathsf {Cu+4HNO_{3}(60\%)=Cu(NO_{3})_{2}+2NO_{2}\uparrow +2H_{2}O}}}
- 3Cu+8HNO3(30%)=3Cu(NO3)2+2NO↑+4h3O{\displaystyle {\mathsf {3Cu+8HNO_{3}(30\%)=3Cu(NO_{3})_{2}+2NO\uparrow +4H_{2}O}}}
При взаимодействии с активными металлами вариантов реакций ещё больше:
- Zn+4HNO3(60%)=Zn(NO3)2+2NO2↑+2h3O{\displaystyle {\mathsf {Zn+4HNO_{3}(60\%)=Zn(NO_{3})_{2}+2NO_{2}\uparrow +2H_{2}O}}}
- 3Zn+8HNO3(30%)=3Zn(NO3)2+2NO↑+4h3O{\displaystyle {\mathsf {3Zn+8HNO_{3}(30\%)=3Zn(NO_{3})_{2}+2NO\uparrow +4H_{2}O}}}
- 4Zn+10HNO3(20%)=4Zn(NO3)2+N2O↑+5h3O{\displaystyle {\mathsf {4Zn+10HNO_{3}(20\%)=4Zn(NO_{3})_{2}+N_{2}O\uparrow +5H_{2}O}}}
- 5Zn+12HNO3(10%)=5Zn(NO3)2+N2↑+6h3O{\displaystyle {\mathsf {5Zn+12HNO_{3}(10\%)=5Zn(NO_{3})_{2}+N_{2}\uparrow +6H_{2}O}}}
- 4Zn+
Как получают и из чего делают железо (сталь)?
Железо и стали на его основе используются повсеместно в промышленности и обыденной жизни человека. Однако мало кто знает, из чего делают железо, вернее, как его добывают и преобразовывают в сплав стали.
Популярное заблуждение
Для начала определимся с понятиями, поскольку люди часто путаются и не совсем понимают, что такое железо вообще. Это химический элемент и простое вещество, которое в чистом виде не встречается и не используется. А вот сталь – это сплав на основе железа. Она богата на различные химические элементы, а также содержит углерод в своем составе, который необходим для придания прочности и твердости.
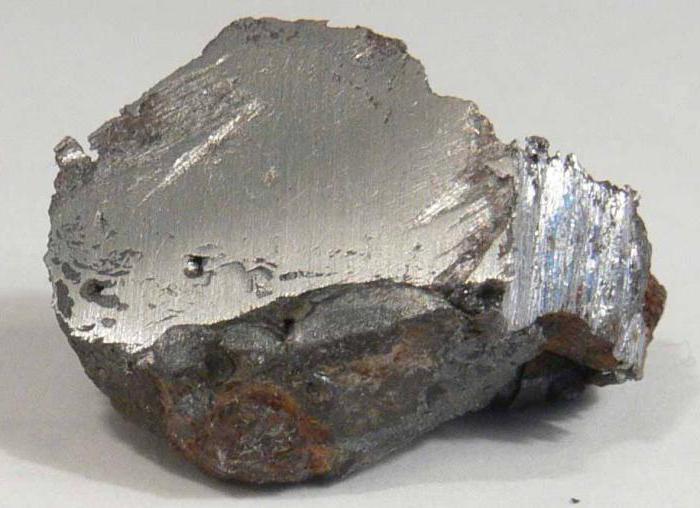
Следовательно, не совсем правильно рассуждать о том, из чего делают железо, так как оно представляет собой химический элемент, который есть в природе. Человек из него делает сталь, которая в дальнейшем может использоваться для изготовления чего-либо: подшипников, кузовов автомобилей, дверей и т. д. Невозможно перечислить все предметы, которые из нее производятся. Итак, ниже мы не будем разбирать, из чего делают железо. Вместо этого поговорим о преобразовании этого элемента в сталь.
Добыча
В России и мире существует множество карьеров, где добывают железную руду. Это огромные и тяжелые камни, которые достаточно сложно достать из карьера, так как они являются частью одной большой горной породы. Непосредственно на карьерах в горную породу закладывают взрывчатку и взрывают ее, после чего огромные куски камней разлетаются в разные стороны. Затем их собирают, грузят на большие самосвалы (типа БелАЗ) и везут на перерабатывающий завод. Из этой горной породы и будет добываться железо.
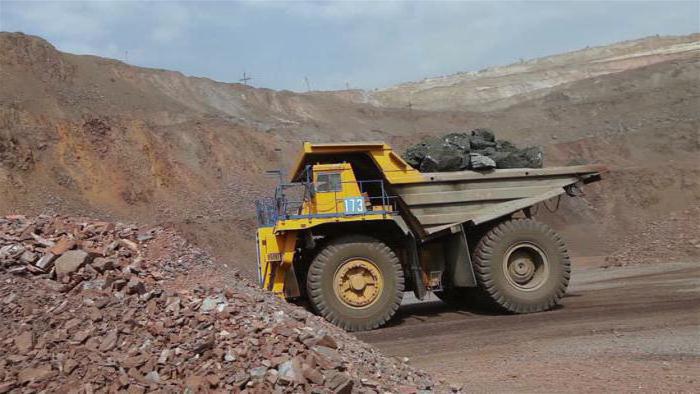
Иногда, если руда находится на поверхности, то ее вовсе необязательно подрывать. Ее достаточно расколоть на куски любым другим способом, погрузить на самосвал и увезти.
Производство
Итак, теперь мы понимаем, из чего делают железо. Горная порода является сырьем для его добычи. Ее отвозят на перерабатывающее предприятие, загружают в доменную печь и нагревают до температуры 1400-1500 градусов. Эта температура должна держаться в течение определенного времени. Содержащееся в составе горной породы железо плавится и приобретает жидкую форму. Затем его остается разлить в специальные формы. Образовавшиеся шлаки при этом отделяют, а само железо получается чистым. Затем агломерат подают в бункерные чаши, где он продувается потоком воздуха и охлаждается водой.
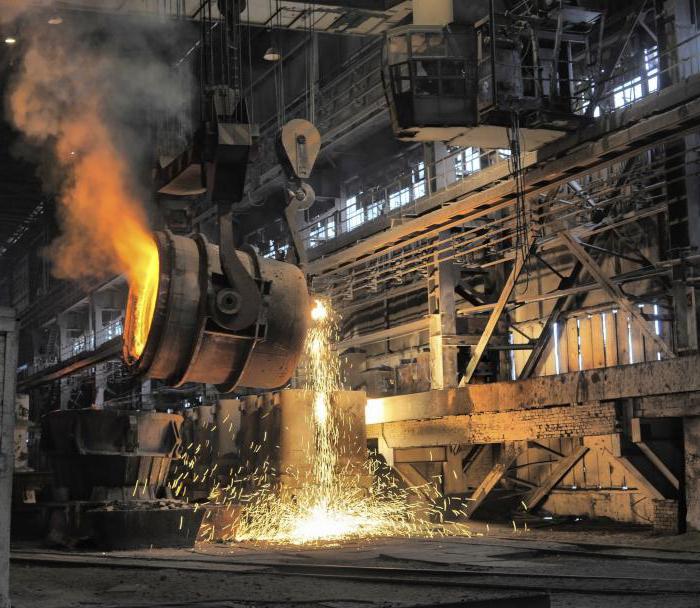
Есть и другой способ получения железа: горную породу дробят и подают на специальный магнитный сепаратор. Так как железо имеет способность намагничиваться, то минералы остаются на сепараторе, а вся пустая порода вымывается. Конечно, чтобы железо превратить в металл и придать ему твердую форму, его необходимо легировать с помощью другого компонента – углерода. Его доля в составе очень мала, однако именно благодаря нему металл становится высокопрочным.
Стоит отметить, что в зависимости от объема добавляемого в состав углерода сталь может получаться разной. В частности, она может быть более или менее мягкой. Есть, например, специальная машиностроительная сталь, при изготовлении которой к железу добавляют всего 0,75 % углерода и марганец.
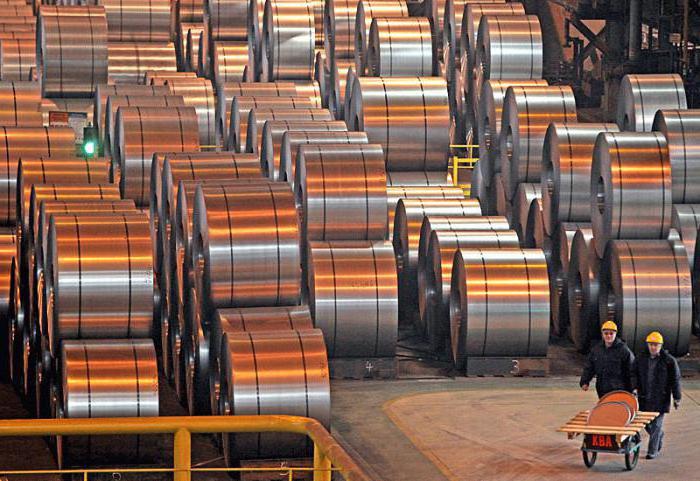
Теперь вы знаете, из чего делают железо и как его преобразовывают в сталь. Конечно, способы описаны весьма поверхностно, но суть они передают. Нужно запомнить, что из горной породы делают железо, из чего далее могут получать сталь.
Производители
На сегодняшний день в разных странах есть крупные месторождения железной руды, которые являются базой для производства мировых запасов стали. В частности, на Россию и Бразилию приходится 18 % мирового производства стали, на Австралию – 14 %, Украину – 11 %. Самыми крупными экспортерами является Индия, Бразилия, Австралия. Отметим, что цены на металл постоянно меняются. Так, в 2011 году стоимость одной тонны металла составляла 180 долларов США, а к 2016 году была зафиксирована цена в 35 долларов США за тонну.
Заключение
Теперь вы знаете, из чего состоит железо (имеется в виду металл) и как его производят. Применение этого материала распространено во всем мире, и его значение практически невозможно переоценить, так как используется он в промышленных и бытовых отраслях. К тому же экономика некоторых стран построена на базе изготовления металла и его последующего экспорта.
Мы рассмотрели, из чего состоит сплав. Железо в его составе смешивается с углеродом, и подобная смесь является основной для изготовления большинства известных металлов.
Зачем из метеоритного железа делают оружие | Екабу.ру


История «метеоритного» оружия
«Небесные камни» люди начали находить в глубокой древности. По мнению археологов, изделия из метеоритного железа являются самыми ранними образцами продукции чёрной металлургии. Географически они происходят из различных районов Ближнего Востока, где зародились первые цивилизации. Древнейшие артефакты такого рода относятся к V-II тысячелетиям до н.э. Распознать метеоритное железо можно по примеси никеля, доля которого, как правило, составляет около 5%. Разумеется, новая отрасль производства не могла бы появиться, если бы люди предварительно не научились обрабатывать более легкоплавкие цветные металлы.
По мнению исследователей, Владимира Завьялова и Натальи Тереховой, самым древним изделием из метеоритного железа можно считать так называемые бусы-пронизки, найденные в могильнике Герзех (северный Египет) – они были изготовлены в 3200 году до н.э. По форме эти украшения представляют собой свёрнутые в трубочку пластинки металла длиной 1,5 см. Технология их изготовления была сходна с той, которую древние мастера применяли при работе с золотом и медью.
Наряду с украшениями и орудиями труда из «небесного металла» делали оружие. Например, по одной из версий, метеоритное происхождение имеет железный клинок кинжала, найденного в гробнице Тутанхамона. Впрочем, содержание никеля в данном образце ниже, чем в большинстве других находок – всего 2,8%. Поэтому некоторые учёные сомневаются в том, что это именно метеоритное железо.
В начале I тысячелетия до н.э. метеоритные изделия добрались и до Восточной Европы. Например, в Калмыкии, в кургане Бичкин-Булук, относящемся к скифо-сарматской эпохе, советские археологи нашли листовидный наконечник копья явно «космического» происхождения.
Во времена фараонов и скифских царей железное оружие могли позволить себе лишь очень состоятельные люди. Сегодня же эти находки являются бесценными музейными экспонатами.
Метеоритное оружие в наши дни
Метеоритное железо сохраняет определенную ценность для оружейников и в настоящее время. По свойствам этот металл сравнивают с высокоуглеродистой сталью. Кроме того, современные мастера имеют возможность использовать куски метеорита любого размера, а не только мелкие осколки, как кузнецы древности. Однако в первую очередь изделия из метеоритного железа ценятся не из-за своих качеств, а из-за редкости материала.
В 1814 году российскому императору Александру I в честь победы над Наполеоном подарили «метеоритную» саблю. Она была изготовлена в мастерской Джона Проссера на улице Чаринг-Кросс в Лондоне, предположительно, методом холодной ковки. Эта сабля никогда не использовалась в бою, в настоящее время она хранится в коллекции государственного Эрмитажа.
Еще один образец холодного оружия из метеоритного железа был создан уже в нашем веке. Материалом для катаны «Меч небес» послужил обломок от гигантского метеорита Gibeon. Этот «космический гость» общим весом 26 тонн упал на Землю полмиллиона лет назад, и был обнаружен в Намибии в 1836 году. Катану выковал японский мастер Есиндо Есихара.
А в 2016 году американская оружейная компания Cabot Guns выпустила пару «метеоритных» копий легендарного кольта 1911 года. Пистолеты получили название Big Bang set («Большой взрыв»). Каждую деталь фактически вырезали из 30-килограммового куска того же метеорита Gibeon с помощью современных станков. Кольты имеют на поверхности специфический рисунок – Видманштеттенову структуру, которую невозможно получить в земных условиях. Оружие было выставлено на продажу по «астрономической» цене в 4,5 миллиона долларов.
Отметим, что у «метеоритного» оружия есть и критики. Так, авторские ножи из «небесного железа», несмотря на колоссальную рыночную цену, по мнению скептиков, непригодны к применению, так как они получаются слишком мягкими. Поэтому известные оружейные компании предпочитают делать из метеоритов не клинки, а рукоятки ножей.
История производства и использования железа — Википедия
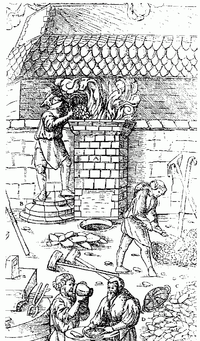
История производства и использования железа берёт своё начало в доисторической эпохе, скорее всего, с использования метеоритного железа. Выплавка в сыродутной печи применялась в XII веке до н. э. в Индии, Анатолии и на Кавказе. Также отмечается использование железа при выплавке и изготовлении орудий и инструментов в 1200 году до н. э. в Африке южнее Сахары[2][3]. Уже в первом тысячелетии до н. э. использовалось кованое железо (англ. Wrought iron). Об обработке железа упоминается в первой книге Библии (Быт. 4:22).
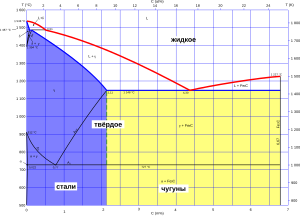
Материал, в обиходе называемый «железом», как правило, является сталью или чугуном и представляет собой сплав железа (Fe), как химического элемента, с углеродом (C). Кроме железа и углерода сплав содержит незначительные количества других химических элементов.
При концентрации углерода в сплаве менее 0,3 % получается мягкий пластичный тугоплавкий (температура плавления железа 1539 °C) сплав, за которым и закрепляется название его основного ингредиента — железа. Представление о том железе, с которым имели дело наши предки, сейчас можно получить, исследовав механические свойства гвоздя.
При концентрации углерода в сплаве от 0,3 до 2,14 % сплав называется «сталью». В первозданном виде сталь походит по своим свойствам на железо, но, в отличие от него, поддается закалке: при резком охлаждении после нагрева до определённых температур сталь приобретает большую твёрдость — замечательное достоинство, однако, почти совершенно сводимое на нет приобретённой в процессе той же закалки хрупкостью.
При концентрации углерода в сплаве свыше 2,14 % сплав называется «чугуном». Чугун — хрупкий легкоплавкий сплав, пригодный для литья, но не поддающийся обработке ковкой. Чугун насыщен графитовыми включениями, делающими его неоднородным и механически непрочным. Температура плавления чугуна варьируется от 1150 до 1300 °C.
Технологии производства и обработки железа и сплавов[править | править код]
Для производства железа исторически применялось несколько технологий, которые сложно расположить в хронологическом порядке.
Метеоритное железо[править | править код]
Использование железа началось намного раньше, чем его производство. Иногда люди находили куски серовато-чёрного металла, попавшие на Землю с метеоритами — метеоритное железо, использовали их для изготовления оружия: перековывали в кинжалы или наконечники копий. Метеоритное железо было более прочным и пластичным, чем бронза, и дольше «держало» остроту лезвия. Поскольку железные метеориты содержали железоникелевый сплав, можно предположить, что качество некоторых уникальных кинжалов могло соперничать с современным ширпотребом[4]. Однако, та же уникальность приводила к тому, что такое оружие оказывалось не на поле боя, а в сокровищнице очередного правителя.
Сыродутная печь[править | править код]
Первым устройством для получения железа из руды стала одноразовая сыродутная печь (сыродутный горн, домница). Несмотря на наличие недостатков способ получения железа с использованием такой печи долгое время оставался единственным способом получения железа из руды. На Руси появление первых домниц относят к IX веку[5].
Впервые железо научились обрабатывать народы Анатолии. Древние греки считали, что открывателями железа был народ халибов. В литературе этот народ назывался устойчивым выражением «отец железа». Слово «сталь» на греческом языке («Χάλυβς») происходит от этого этнонима.
«Железная революция» началась на рубеже I тысячелетия до нашей эры в Ассирии. Железные мечи научились изготавливать представители Гальштатской культуры. С VIII века до нашей эры сварочное железо быстро стало распространяться в Европе, в III веке до нашей эры оно вытеснило бронзу в Галлии, во II веке новой эры появилось в Германии, а в VI веке уже широко употреблялось в Скандинавии; племенами же, проживающими на территории будущей Руси — киммерийцами, а позже скифами и сарматами — железо использовалось ещё до н. э.. В Японии железный век наступил только в VII веке нашей эры.
Известный популяризатор науки Айзек Азимов так описывает историю перехода человечества из бронзового века в железный[6]:
![]() | Где-то около XV—XIV вв. до н. э. техника выплавки и науглероживания железа была разработана в кавказских предгорьях в Урарту. Эта страна находилась тогда под властью Хеттского царства, которое находилось на высшей точке своей мощи. Хеттские цари тщательно охраняли монополию на новую технику, ибо понимали её важность. Вначале получали только маленькие партии железа, и в течение нескольких столетий оно стоило порой в сорок раз дороже серебра. Но ещё до того, как выплавку можно было увеличить, а хеттам — этим воспользоваться, им пришёл конец. Хеттское царство было разрушено во время беспорядков, последовавших за движением «народов моря», и хеттская монополия на железо была нарушена. Технология выплавки железа быстро распространялась в том числе, конечно, в Ассирию, которая граничила с «железным царством» Урарту. Торговля железом восстановила процветание Ассирии. Открылся путь для новых завоеваний. Вторгшиеся в Грецию дорийские племена обладали железным оружием, именно поэтому они так легко покорили вооруженных бронзой ахейцев. Было железо и у «народов моря», и, когда филистимляне захватывали ханаанское побережье, в сражениях они использовали железное оружие, Но они были не настолько глупы, чтобы раскрывать секрет выплавки железа. Пока им удавалось хранить эту техническую тайну, израильтянам приходилось обороняться более примитивным оружием. Благодаря железу филистимляне не только легко закрепились на побережье, но и обложили данью ближайшие к ним племена. Около двух веков (до прихода к власти Давида в 1013 году до н. э.) им удавалось господствовать над более многочисленными израильскими племенами. | ![]() |
Первым шагом в зарождающейся чёрной металлургии было получение железа путём восстановления его из окиси. Болотная руда перемешивалась с древесным углём и закладывалась в печь. При высокой температуре, создаваемой горением угля, углерод начинал соединяться не только с атмосферным кислородом, но и с тем кислородом, который был связан с атомами железа.
После выгорания угля в печи оставалась так называемая «крица» — комок пористого восстановленного железа с примесью большого количества шлаков. Крицу потом снова разогревали и подвергали обработке ковкой, выколачивая шлак из железа. Полученный брусок железа (в котором всё же оставалось 2—4 % шлака) назывался «кричной болванкой». Долгое время ковка была основным процессом в технологии производства железа, причём, с приданием изделию формы она была связана в последнюю очередь. Ковкой получался сам материал.
Сварное оружие[править | править код]
Сталь производилась уже из готового железа путём насыщения углеродом последнего. При высокой температуре и недостатке кислорода углерод, не успевая окисляться, пропитывал железо. Чем больше было углерода, тем твёрже оказывалась сталь после закалки.
Как можно было заметить, ни один из перечисленных выше сплавов не обладает таким свойством, как упругость. Железный сплав может приобрести это качество, только если в нём возникает чёткая кристаллическая структура, что происходит, например, в процессе застывания из расплава. Проблема же древних металлургов заключалась в том, что расплавить железо они не могли. Для этого требуется разогреть его до 1540 °C, в то время как технологии древности позволяли достичь температур в 1000‑1300 °C. Вплоть до середины XIX века было невозможно расплавить железо и сталь с содержанием углерода менее 0,4 %, так как плавкость железных сплавов снижается по мере уменьшения концентрации углерода.
Таким образом ни железо, ни сталь сами по себе для изготовления оружия не годились. Орудия и инструменты из чистого железа выходили слишком мягкими, а из чистой стали — слишком хрупкими. Потому, чтобы изготовить, например, меч, приходилось делать «бутерброд» из двух пластин железа, между которыми закладывалась стальная пластина. При заточке мягкое железо стачивалось и появлялась стальная режущая кромка.
Такое оружие, сваренное из нескольких слоёв с разными механическими свойствами, называлось сварным. Общими недостатками этой технологии являлись излишняя массивность и недостаточная прочность изделий. Сварной меч не мог пружинить, вследствие чего неизбежно ломался или гнулся при ударе о непреодолимую преграду.
Отсутствием упругости недостатки сварного оружия не исчерпывались. В дополнение к упомянутым недостаткам, его, например, невозможно было «толком» заточить. Железу можно было придать какую угодно остроту (хотя и стачивалось оно быстро), но и тупилась мягкая режущая кромка из железа почти мгновенно. Сталь же точиться не желала — режущая кромка крошилась. Здесь налицо полная аналогия с карандашами — мягкий грифель легко сделать острым, но он сразу затупится, а твёрдый до особой остроты не доведёшь — десять раз сломается. Так что, бритвы приходилось делать из железа и затачивать заново ежедневно.
В целом же сварное оружие не превосходило остротой столовый нож. Уже одно это обстоятельство требовало делать его достаточно массивным для придания удовлетворительных рубящих свойств.
Единственной мерой, позволяющей достичь сочетания остроты и твёрдости в рамках технологии сварки, была закалка изделия уже после его заточки. Применим же этот метод становился в случае, если стальная режущая кромка приваривалась просто к железному обуху, а не заключалась в «бутерброд» из железа. Либо после заточки могли быть закалены клинки, у которых железный сердечник покрывался снаружи сталью. Недостатком такого метода было то, что заточка оказывалась возможна лишь однажды. Когда стальное лезвие повреждалось и тупилось, весь клинок приходилось перековывать.
Тем не менее именно освоение техники сварки — несмотря на все её недостатки — произвело настоящий переворот во всех сферах человеческой деятельности и привело к огромному возрастанию производительных сил. Сварные орудия были вполне функциональны и, при том, общедоступны. Только с их распространением каменные орудия оказались окончательно вытеснены, и наступил век металла.
Железные орудия решительно расширили практические возможности человека. Стало возможным, например, строить рубленные из брёвен дома — ведь железный топор валил дерево уже не в три, как медный, а в 10 раз быстрее, чем каменный. Широкое распространение получило и строительство из тёсаного камня. Он, естественно, употреблялся и в эпоху бронзы, но большой расход сравнительно мягкого и дорогого металла решительно ограничивал такие эксперименты. Значительно расширились также и возможности земледельцев.
Булатная сталь и дамаск[править | править код]
Увидеть железо жидким металлурги смогли только в XIX веке, однако ещё на заре железной металлургии — в начале I тысячелетия до нашей эры — индийские мастера сумели решить проблему получения высокоуглеродистой стали с композитной структурой. Такую сталь называли булатом, но из-за сложности изготовления и отсутствия необходимых материалов в большей части мира эта сталь так и осталась индийским секретом на долгое время.
Более технологичный путь получения упругой стали, при котором не требовались ни особо чистая руда, ни графит, ни специальные печи, был найден в Китае во II веке нашей эры. Сталь перековывали до двенадцати раз, при каждой ковке складывая заготовку вдвое, в результате чего получался отличный оружейный материал, называемый «дамаском», из которого, в частности, делались японские катаны (мечи). Количество слоёв стали рассчитывается по формуле A=2Nx{\displaystyle A=2^{N}x}, где N{\displaystyle N} — количество проковок, а x{\displaystyle x} — изначальное количество видов (слоёв) стали, сковываемой в «бутерброд». При каждой ковке количество слоёв удваивалось, а после 12 проковок количество слоёв достигало 4096, и слои становились неразличимы.
Штукофен[править | править код]
Более высокую, по сравнению с сыродутной печью, ступень в развитии чёрной металлургии представляли собой постоянные высокие печи, называемые в Европе штукофенами. Это действительно была высокая печь — с четырёхметровой трубой для усиления тяги. Мехи штукофена «качались» уже несколькими людьми, а иногда и водяным двигателем. Штукофен имел дверцы, через которые раз в сутки извлекалась крица.
Изобретены штукофены были в Индии в начале первого тысячелетия до новой эры. В начале нашей эры они попали в Китай, а в VII веке вместе с «арабскими» цифрами арабы заимствовали из Индии и эту технологию. В конце XIII века штукофены стали появляться в Германии и Чехии (а ещё до того были на юге Испании) и в течение следующего века распространились по всей Европе.
Производительность штукофена была несравненно выше, чем сыродутной печи — в день он давал до 250 кг железа, а температура в нём оказывалась достаточна для науглероживания части железа до состояния чугуна. Однако штукофенный чугун при остановке печи застывал на её дне, смешиваясь со шлаками, а очищать металл от шлаков умели тогда только ковкой, но как раз ей-то чугун и не поддавался. Его приходилось выбрасывать.
Иногда, впрочем, штукофенному чугуну пытались найти какое-то применение. Например, древние индусы отливали из грязного чугуна гробы, а турки в начале XIX века — пушечные ядра. Трудно судить, сколь хорошими были гробы, но ядра из него получались невысокого качества.
Ядра для пушек из железистых шлаков в Европе отливали ещё в конце XVI века. Из литой брусчатки делались дороги. В Нижнем Тагиле до сих пор сохранились здания с фундаментами из литых шлаковых блоков[7].
Блауофен[править | править код]
Металлурги давно заметили связь между температурой плавления и выходом продукта — чем выше была температура, тем большую часть содержащегося в руде железа удавалось восстановить. Потому рано или поздно им приходила мысль улучшить штукофен — добавить предварительный подогрев воздуха и увеличить высоту трубы. В середине XV века в Европе появились печи нового типа — блауофены, которые сразу преподнесли сталеварам неприятный сюрприз.
Более высокая температура действительно значительно повысила выход железа из руды, но она же повысила и долю железа науглероживающегося до состояния чугуна. Теперь уже не 10 %, как в штукофене, а 30 % выхода составлял чугун — «свиное железо», ни к какому делу не годное. В итоге, выигрыш часто не окупал модернизации.
Блауофенный чугун, как и штукофенный, застывал на дне печи, смешиваясь со шлаками. Он выходил несколько лучшим, так как его самого было больше, следовательно, относительное содержание шлаков выходило меньше, но продолжал оставаться малопригодным для литья. Чугун, получаемый из блауофенов, оказывался уже достаточно прочен, но оставался ещё очень неоднородным. Из него выходили только предметы простые и грубые — кувалды, наковальни, пушечные ядра.
Кроме того, если в сыродутных печах могло быть получено только железо, которое потом науглероживалось, то в штукофенах и блауофенах внешние слои крицы оказывались состоящими из стали. В блауофенных крицах стали было даже больше, чем железа. С одной стороны, это было хорошо, но вот отделить сталь от железа оказалось весьма затруднительно. Содержание углерода становилось трудно контролировать. Только долгой ковкой можно было добиться однородности его распределения.
В своё время, столкнувшись с этими затруднениями, индусы не стали двигаться дальше, а занялись тонким усовершенствованием технологии и пришли к получению булата. Но индусов в ту пору интересовало не количество, а качество продукта. Европейцы, экспериментируя с чугуном, скоро открыли передельный процесс, поднявший металлургию железа на качественно новый уровень.
Доменная печь[править | править код]
Следующим этапом в развитии металлургии стало появление доменных печей. За счёт увеличения размера, предварительного подогрева воздуха и механического дутья, в такой печи всё железо из руды превращалось в чугун, который расплавлялся и периодически выпускался наружу. Производство стало непрерывным — печь работала круглосуточно и не остывала. За день она выдавала до полутора тонн чугуна. Перегнать же чугун в железо в горнах было значительно проще, чем выколачивать его из крицы, хотя ковка все равно требовалась — но теперь уже выколачивали шлаки из железа, а не железо из шлаков.
Хотя найденные в Китае чугунные изделия восходят к V веку до нашей эры[8], самые ранние доменные печи, производящие чугун в «чушках» (слитках), который мог переплавляться в очищенный чугун в вагранках, датируются III—II веками до нашей эры. Подавляющее большинство обнаруженных ранних мест доменного производства относятся к периоду после введения государственной монополии на соль и железорудную промышленность в 117 году до нашей эры (период правления императора У-ди, 141—87 до н. э.) в эпоху династии Хань (202 год до нашей эры — 220 год нашей эры). Большинство железоделательных мест, открытых до 117 года до нашей эры, занимались лишь литьём из заготовок, выплавленных в доменных печах в других районах, отдалённых от населённых пунктов[9][10].
В Европе доменные печи впервые были применены на рубеже XV—XVI веков. На Ближнем Востоке и в Индии эта технология появилась только в XIX веке (в значительной степени, вероятно, потому, что водяной двигатель из-за характерного дефицита воды на Ближнем Востоке не употреблялся). Наличие в Европе доменных печей позволило ей обогнать в XVI веке Турцию если не по качеству металла, то по валу. Это оказало несомненное влияние на исход борьбы, особенно когда оказалось, что из чугуна можно лить пушки.
Георгий Агрикола так описывает средневековую технологию плавки[11]:
![]() | Обычай выдающихся плавильщиков, умеющих управлять четырьмя элементами (имеются в виду земля, воздух, огонь и вода — вне цитаты), таков. Они смешивают в правильных пропорциях руды, содержащие земли, и загружают их в печи. Затем льют нужное количество воды и умело управляют движением воздуха, поступающего из мехов, забрасывая руду туда, где огонь горит с наибольшей силой. Мастер равномерно обрызгивает водой внутреннее пространство печи, слегка увлажняя древесный уголь с тем, чтобы к нему приставали мелкие частицы руды; иначе эти частицы приводятся в движение силой дутья и огня и уносятся вместе с дымом. | ![]() |
Также Агрикола верно объясняет необходимость изменения конструкции печи в зависимости от типа руд[11]:
![]() | Так как природа руд, подлежащих плавке, бывает различной, плавильщикам приходится устраивать горн то выше, то ниже и устанавливать трубу, куда вводятся насадки мехов под меньшим или большим углом для того, чтобы дутье при надобности было более или менее сильным. Если руды нагреваются и плавятся легко, то для работы плавильщиков необходим низкий горн, а труба должна быть установлена под небольшим углом, чтобы дутье было легкое. Наоборот, если руды нагреваются и плавятся медленно, то требуется высокий горн, а труба должна быть установлена с крутым уклоном, чтобы обеспечить сильное дутье. Для руд этого рода нужна весьма горячая печь, в которой сначала расплавляются шлаки, штейны или легкоплавкие камни для того, чтобы руда не могла пригореть к поду горна и закрыть выпускное отверстие. | ![]() |
Передельный процесс[править | править код]
С XVI века в Европе получил распространение так называемый передельный процесс в металлургии — технология, при которой железо ещё при получении за счёт высокой температуры плавления и интенсивного науглероживания перегонялось в чугун, а уже затем, жидкий чугун, освобождаясь от лишнего углерода при отжиге в горнах, превращался в сталь.
Из передельной стали уже можно было изготавливать кривые мечи (например, сабли), чего не позволяла сделать сварная технология.
Применение угля, коксование, пудлингование, горячее дутьё[править | править код]
С начала XVII века европейской кузницей стала Швеция, производившая половину железа в Европе. В середине XVIII века её роль в этом отношении стала стремительно падать в связи с очередным изобретением — применением в металлургии каменного угля.
Прежде всего надо сказать, что до XVIII века включительно каменный уголь в металлургии практически не использовался — из-за высокого содержания вредных для качества продукта примесей, в первую очередь — серы. С XVII века в Англии каменный уголь, правда, начали применять в пудлинговочных печах для отжига чугуна, но это позволяло достичь лишь небольшой экономии древесного угля — большая часть топлива расходовалась на плавку, где исключить контакт угля с рудой было невозможно.
Потребление же топлива в металлургии уже тогда было огромно — домна (доменная печь) пожирала воз угля в час. Древесный уголь превратился в стратегический ресурс. Именно изобилие дерева в самой Швеции и принадлежащей ей Финляндии позволило шведам развернуть производство таких масштабов. Англичане, имевшие меньше лесов (да и те были зарезервированы для нужд флота), вынуждены были покупать железо в Швеции до тех пор, пока не научились использовать каменный уголь. Его ввёл в употребление в XVII веке Клемент Клерк и его мастера кузнечных дел и литья.
С 1709 году в местечке Коулбрукдейл Абрахам Дарби, основатель целой династии металлургов и кузнецов, использовал кокс для получения чугуна из руды в доменной печи. Из него поначалу делали лишь кухонную утварь, которая отличалась от работы конкурентов лишь тем, что её стенки были тоньше, а вес меньше. В 1750-х годах сын Дарби (Абрахам Дарби II) построил ещё несколько домен, и к этому времени его изделия были ещё и дешевле, чем изготовленные на древесном угле. В 1778 году внук Дарби, Абрахам Дарби III, из своего литья построил в Шропшире знаменитый Железный мост, первый мост в Европе, полностью состоящий из металлических конструкций.
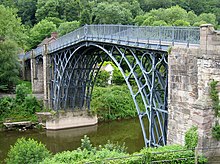
Для дальнейшего улучшения качества чугуна в 1784 году Генри Корт разработал процесс пудлингования. Среди многих металлургических профессий того времени, пожалуй, самой тяжелой была профессия пудлинговщика. Пудлингование было основным способом получения железа почти на протяжении всего XIX века. Это был очень тяжёлый и трудоёмкий процесс. Работа при нём шла так. На подину пламенной печи загружались чушки (слитки) чугуна; чушки расплавляли. По мере выгорания из металла углерода и других примесей температура плавления металла повышалась, и из жидкого расплава начинали «вымораживаться» кристаллы довольно чистого железа. На подине печи собирался комок слипшейся тестообразной массы. Рабочие-пудлинговщики приступали к операции накатывания крицы при помощи железного лома. Перемешивая ломом массу металла, они старались собрать вокруг лома комок, или крицу, железа. Такой комок весил до 50—80 кг и более. Крицу вытаскивали из печи и подавали сразу под молот — для проковки с целью удаления частиц шлака и уплотнения металла[7].
Рост производства и улучшение качества английского металла к концу XVIII века позволило Великобритании полностью отказаться от импорта шведского и российского железа. Развернулось сооружение каналов, позволявших перевозить уголь и металлы.
С 1830 по 1847 год производство металла в Англии возросло более чем в 3 раза. Применение горячего дутья при плавке руды, начавшееся в 1828 году, втрое сократило расход топлива и позволило использовать в производстве низшие сорта каменного угля, С 1826 по 1846 год экспорт железа и чугуна из Великобритании увеличился в 7,5 раза[12].
Конвертерное производство и мартеновские печи[править | править код]
В 1856 году Генри Бессемер получил патент на новую технологию производства стали (бессемеровский процесс). Он изобрёл конвертер — устройство, в котором сквозь жидкий чугун, получаемый в доменных печах, продувался воздух. В конвертере происходит выгорание углерода, растворённого в железе, что позволяет получать сталь в существенно больших количествах, чем это было ранее доступно.
Альтернативой применения конвертера на протяжении XX века являлась мартеновская печь, в которой также происходило дожигание углерода. К концу XX века мартеновские печи стали очевидно устаревшей технологией и были вытеснены кислородно-конвертерным производством стали.
В середине XX века был изобретён турбодетандер, позволяющий снизить затраты на производство кислорода. Кислород стал достаточно дешёвым, чтобы получить массовое применение в сталелитейной промышленности. Продувка расплавленного чугуна кислородом существенно разогревает металл, что упрощает производство (железо не «вымораживается», а остаётся жидким), позволяет также в конвертер сбрасывать металлолом для переплавки, а также в ряде случаев улучшает качество металла за счёт отсутствия растворённого в металле азота.
Электрометаллургия[править | править код]
Способность постоянного электрического тока восстанавливать металлы была обнаружена ещё в самом начале XIX века, однако отсутствие мощных источников электроэнергии ограничивало применение этих процессов лабораторными исследованиями. Появление в начале XX века мощных электростанций позволило создать промышленные технологии электрометаллургии. Изначально такие процессы применялись для производства цветных металлов, но к середине XX века пришли и в чёрную металлургию. Широкое применение нашли процессы электрической рудовосстанавливающей плавки, при которой железная руда, смешенная с незначительным количеством углерода, подвергается воздействию мощной электрической дуги, где происходит электрическое восстановление железа на катоде и выгорание примесей на аноде. Таким способом удаётся получить чугун высокого качества, сократить расход кислорода и снизить уровень выбросов углекислого газа. Передельные электрометаллургические процессы дают возможность плавить чугун в вакууме, в среде защитного газа, в присутствии химически активных легирующих элементов, что позволяет получать легированные стали высокого качества и специальные стали (жаропрочные, радиационно стойкие). Стали, получение которых возможно только электрометаллургическими процессами называют электросталями.
Восстановление водородом[править | править код]
Доменные печи и конвертерное производство является достаточно современным, но весьма грязным для экологии процессом. При том, что большая часть железа получается в кислородно-конвертерном производстве, велики и выбросы углекислого и угарного газов в атмосферу. Модной альтернативой становится прямое восстановление железа из руды водородом. При этом образующиеся частички железа расплавляются в электрических печах, после чего добавляется углерод и получается сталь.
Кузнецы-любители[править | править код]
Первыми производство железных изделий организовали кузнецы-любители — обычные крестьяне, промышлявшие таким ремеслом в свободное от обработки земли время. Кузнец сам находил «руду» (болотная руда вблизи ржавого болота или красный песок), сам выжигал уголь, сам строил сыродутную печь и выплавлял железо, сам ковал, сам обрабатывал.
Умение мастера на данном этапе закономерно было ограничено выковыванием изделий самой простой формы. Инструментарий же его состоял из мехов, каменных молота и наковальни и точильного камня. Железные орудия производились с помощью каменных инструментов.
Если удобные для разработки залежи руды имелись поблизости, то и целая деревня могла заниматься производством железа, но такое было возможным только при наличии устойчивой возможности выгодного сбыта продукции, чего практически не могло быть в условиях натурального хозяйства.
При такой организации производства железа, никогда не удавалось за его счёт полностью покрыть все потребности в самом простом оружии и самых необходимых орудиях труда. Из камня продолжали изготавливаться топоры, из дерева — гвозди и плуги. Металлические доспехи оставались недоступными даже для вождей. Концентрация железных изделий составляла всего порядка 200 граммов на душу населения[источник не указан 1105 дней].
На таком уровне доступности железа находились в начале нашей эры наиболее отсталые племена среди бриттов, германцев и славян. В XII‑XIII веке прибалты и финны сражаясь с крестоносцами пользовались ещё каменным и костяным оружием. Все эти народы умели уже делать железо, но ещё не могли получить его в необходимом количестве.[источник не указан 1105 дней]
Профессиональные кузнецы[править | править код]
Следующим этапом развития чёрной металлургии были профессиональные кузнецы, которые всё ещё сами выплавляли металл, но на добычу железоносного песка и выжигания угля чаще уже отправляли других мужиков — в порядке натурального обмена. На этом этапе кузнец, обычно, уже имел помощника-молотобойца и как-то оборудованную кузницу.
С появлением кузнецов концентрация железных изделий возрастала в 4‑5 раз. Теперь уже каждый крестьянский двор мог быть обеспечен персональным ножом и топором. Возрастало и качество изделий. Кузнецы профессионалы, как правило, владели техникой сварки и могли вытягивать проволоку. В принципе, такой умелец мог получить и дамаск, если знал как, но производство дамаскового оружия требовало такого количества железа, что не могло ещё быть сколько-то массовым.
В XVIII-XIX веках деревенские кузнецы умудрялись даже изготовлять стволы к нарезному оружию, но в этот период они уже пользовались оборудованием, которое сделали не сами. Некоторого масштаба перенос ремесленного производства из города в деревню становился возможным на таком этапе развития города, когда стоимость даже довольно сложного оборудования оказывалась незначительной.
Средневековые же деревенские кузнецы сами делали свои орудия труда. Как умели. Поэтому рядовой мастер обычно преуспевал в изготовлении предметов простой плоской формы, но положительно затруднялся, когда требовалось изготовить трёхмерное изделие, или состыковать несколько изделий между собой — что, например, требовалось для создания надёжного шлема. Изготовить же такое сложное изделие, как спусковой механизм для арбалета, деревенскому кузнецу было непосильно — для этого ведь потребовались бы даже измерительные устройства.
Не было у кустарных кузнецов и специализации — и мечи, и иголки, и подковы делал один и тот же мастер. Более того, во все времена сельские кузнецы были заняты в первую очередь именно изготовлением наиболее необходимых односельчанам простейших производственных и бытовых орудий, но не оружия.
Впрочем, последнее отнюдь не отменяет того обстоятельства, что в примитивных культурах даже самый заурядный кузнец считался несколько сродни колдуну, хотя, более адекватно его можно уподобить художнику. Выковывание даже обычного меча было настоящим искусством.
Теоретически всё выглядело просто: надо только наложить одна на другую три полоски металла, проковать их, и клинок готов. На практике, однако, возникали проблемы — с одной стороны надо было добиться прочной сварки и даже взаимопроникновения слоев, а с другой, нельзя было нарушать равномерность толщины слоя (а она-то и была — с лист бумаги) и, тем более, допустить, чтобы слой разорвался. А, ведь, обработка производилась тяжёлым молотом.
До разделения труда между городом и деревней годовое производство железа не превышало 100 граммов в год на человека, форма изделий была очень простой, а качество — низким, и, когда описывается вооружение какого-нибудь варяга, систематически упускается из вида, что речь идёт об оружии вождя, откопанном в его кургане. Варвары, которым курганы не полагались, вооружались существенно проще. На данном уровне развития производительных сил (характерном, например, для галлов, франков, норманнов, Руси X века) тяжёлое вооружение могло иметься только у аристократии — не более одного воина в броне на 1000 человек населения.
На новый уровень металлообрабатывающая промышленность вступила только тогда, когда стало возможным разделение труда и возникновение специальностей. Мастер железо покупал, причём уже нужного качества, покупал инструменты, необходимые по его профилю, и нанимал подмастерьев. Если уж он и делал ножи, то сдавал их на реализацию ящиками. Если делал мечи, то не по два в год, а по четыре в неделю. И, естественно, обладал большим опытом в их изготовлении.
Но для возникновения специализации непременно требовался город — хоть на несколько тысяч жителей — чтобы мастер мог всё купить и продать. Даже очень крупные призамковые посёлки (а их население тоже иногда достигало нескольких тысяч человек) не давали такой возможности — ведь в них не только ничего не производилось на продажу в другие поселения, но и отсутствовал даже внутренний товарообмен.
Чем более был развит обмен, тем больше могло быть мастеров и их специализаций, сформироваться разделение труда. Но для значительного развития обмена требовались деньги и сравнительная стабильность.
Ещё больший прогресс мог быть достигнут организацией мануфактуры, но вокруг неё требовалось выстроить уже 50-тысячный город, и наличие ещё нескольких таких же поблизости.
Тем не менее, даже после сосредоточения ремесленного производства в городах, колоритная фигура кузнеца оставалась непременным элементом пасторального ландшафта вплоть до начала, а кое-где и до середины XX века. Долгое время крестьяне просто не имели возможности покупать городские изделия. На ранних этапах развития обмена квалифицированные ремесленники обслуживали только господствующие классы — в первую очередь военные сословия.
После распространения штукофенов[править | править код]
Кустарное производство железа, однако, перестало практиковаться сразу после распространения штукофенов. Кузнецы начали покупать железо в слитках, а ещё чаще — железный лом, на предмет перековки мечей на орала.
Когда же развитие товарности хозяйства сделало ремесленные изделия доступными широким массам, кузнецы ещё долго занимались починкой сделанных в городах орудий.
Параллельно с решением организационных моментов улучшение методов обработки металлов требовало и совершенствования техники. Поскольку же основным методом была ковка, то усовершенствованию подлежали в первую очередь молоты.
Дело было в том, что, если ковка осуществлялась ручным молотом, то и размер изделия оказывался ограничен физическими возможностями кузнеца. Человек был способен отковать деталь весом не более нескольких килограммов. В большинстве случаев этого оказывалось достаточно, но при изготовлении, скажем, деталей осадных машин без механического молота, приводимого в движение водяным колесом, мулами или рабочими, было уже не обойтись.
Проблема выковывания массивных (до нескольких центнеров) деталей была решена ещё в античности, но в период средних веков она обрела новую остроту, так как крицы, получаемые из штукофенов, тоже нельзя было отковать кувалдой.
Конечно, можно было делить их на небольшие части, но, при этом, в каждой оказалось бы своё, причём неизвестное, содержание углерода, а потом, для изготовления мало-мальски крупного изделия полученные куски пришлось бы сковывать обратно.
Всё это было крайне невыгодно. Ковать крицу надо было целиком. Потому, штукофен по-хорошему требовалось комплектовать даже не одной, а тремя водяными машинами — одна качала мехи, другая — орудовала молотом, третья — откачивала воду из шахты. Без третьей тоже было никак — кустарными заготовками штукофен рудой было не обеспечить.
Впрочем, объёмы производства зависели не столько от технологий, сколько от организации труда. Если металлург не отвлекался на другие задачи, то и сыродутных печей он мог наделать куда больше. Так, в Риме производство достигло 1.5 килограмма на человека в год, и этого не хватало — железо в Рим возили даже из Китая. В Европе же и Азии даже с использованием штукофенов производство редко достигало килограмма. Но с появлением доменных печей в Европе этот показатель разом утроился, а
Что получается из переработанного металлолома, макулатуры, пластика
Большая часть вещей, отправляющихся в мусорное ведро, а затем на свалку, содержит компоненты и материалы, пригодные для переработки и повторного использования. В первую очередь это касается изделий из бумаги, картона, дерева, пластика, стекла и металла. Неслучайно контейнеры именно для этих материалов чаще всего устанавливают при организации раздельного сбора отходов в разных странах.
Переработка металлолома
Металлический лом, пожалуй, один из самых востребованный тип отходов. Его собирают даже там, где нет сложившейся системы раздельного сбора мусора. Особенно высоко ценятся изделия из цветных металлов, но и переработка одной тонны черного металла позволяет сэкономить 1,15 тонны железной руды, 635 кг угля и 54 кг известняка, а также до 75% энергии, необходимой для производства того же количества нового материала. А при переработке алюминиевых банок экономия энергии достигает 95%. Одно из главных преимуществ вторичного использования металла – его можно перерабатывать гнутым, обгоревшим или поржавевшим. После переплавки металлолом можно использовать для производства практически любых изделий из того же материала без ухудшения их свойств.
Интересные факты: в одной тонне старых компьютерных комплектующих содержится то же количество золота, что и в 18 тоннах золотоносной породы. В компании Apple есть специальный робот Liam, который занимается подготовкой к утилизации старых смартфонов, планшетов и иных фирменных изделий. Он способен не только разбирать их, но и разделять содержащиеся в гаджетах золото, платину, серебро, медь, кобальт, литий и другие вещества.
Как используют макулатуру
Ещё один удобный вид материала для переработки – бумага и картон. Во времена существования СССР макулатуру, то есть предназначенные для переработки бумажные и картонные изделия, собирали весьма активно, однако сейчас для потребителя это не слишком выгодно, чего нельзя сказать об экономике и экологии. Одна тонна переработанной макулатуры позволяет сохранить примерно 17 деревьев, сэкономить 40% энергии и 30 % воды для производства аналогичных изделий.
Из бумажного вторсырья производят упаковку, туалетную бумагу, различную полиграфическую продукцию и многое другое. Правда, есть один нюанс – для повторного использования подходит не всякая бумага, а ещё она должна быть сухой и чистой.
Для чего собирают банки и бутылки
При производстве стеклянных банок и бутылок не используются добавки и покрытия, которые могут помешать их переработке, поэтому именно эти изделия обычно принимают на пунктах приема вторсырья. Переработка одной лишь бутылки позволяет сэкономить до 400 Вт электроэнергии. Универсальную тару можно повторно использовать после дезинфекции, а стеклобой применяется при производстве различных строительных материалов.
Что можно сделать из переработанного пластика
Переработка пластмассы – одно из самых перспективных и активно развивающихся направлений в сфере вторичного использования сырья. Задача осложняется большим количество разновидностей пластмассы и содержанием в изделиях из неё различных добавок, однако современные технологии позволяют решить эту проблему. Кроме того, иногда пластиковые изделия используют даже в непереработанном виде. К примеру, в 2010 году в Тайбэе одна из тайваньских компаний построила выставочный павильон из 1,5 миллиона пластиковых бутылок, а на Филиппинах из них даже строят учебные заведения.
Впрочем, переработка пластика открывает более широкие перспективы. Из него делают различную тару, элементы внутренней обшивки автомобилей, корпуса различных гаджетов, мебель, стройматериалы, спортинвентарь, одежду и многое другое.
Интересные факты:
- Компании H&M, Adidas, Levi’s активно используют утилизированный пластик при производстве тканей, а Nike – для производства спортивного инвентаря.
- В Индии новые дороги на 10% состоят из переработанного пластика, смешанного с битумом. В 2015 местное правительство обязало строителей использовать эту технологию.
- В 2015 году голландская компания PlasticRoad разработала технологию по производству из пластиковых отходов модулей с полостями для прокладки коммуникаций для строительства дорог.
- В Екатеринбурге установленные вдоль проспекта Ленина ограждения и скамейки в парке «Зелёная роща» изготовлены пластиковых изделий, переработанных местной компанией «Уралтермопласт».
- Британская компания Lightweight Tiles LTD производит из пластиковых отходов черепицу, по внешнему виду напоминающую керамическую.
Что делают из алюминия? Сферы применения данного металла
Производство алюминия в России идет полным ходом. Всего за год здесь изготавливается свыше 4 000 000 тонн этого сплава. Вопреки популярному заблуждению именно этот металл является самым распространенным на планете, после него идет железо. Но что делают из алюминия, ведь известно, что он применяется в разных отраслях промышленности? В частности, можно выделить машиностроение, авиацию, химическую промышленность и даже гражданское строительство, не говоря уже о производстве предметов бытового применения.
Авиация
Сплав алюминия является основным конструкционным материалом, который используется в современной авиапромышленности. Его потребление резко возросло на этапе развития самолетами дозвуковых и сверхзвуковых скоростей.
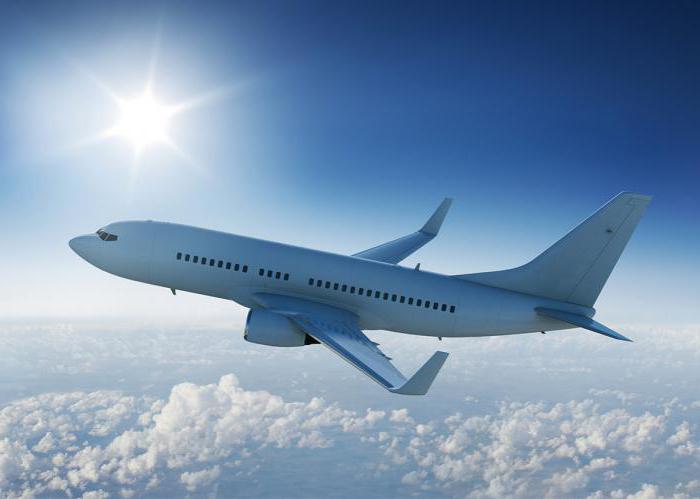
На данный момент существуют сплавы различных серий – от 2ххх до 7ххх. Металл версии 2ххх используется для работы при очень высоких температурах, при этом у него высокий коэффициент вязкости разрушения. Сплавы серии 7ххх используются для создания деталей, которые будут эксплуатироваться под большой нагрузкой и низкой температурой. Они отличаются высокой сопротивляемостью коррозии. Малонагруженные узлы уместно делать из сплавов серии 3ххх, 5ххх, 6ххх. Такие используются в масло-, гидро- и топливных системах.
В России при создании узлов для самолетов используют высокопрочные алюминиевые сплавы, которые предварительно подвергаются термической обработке. Также активно используются сплавы средней прочности. Обшивка лайнера, крылья, фюзеляж, киль и т. д. – все эти элементы изготавливаются именно из этого материала. Сплав 1420 активно используется для создания сварного фюзеляжа пассажирского лайнера. Теперь понимаем, что делают из алюминия в авиации.
Космическая техника
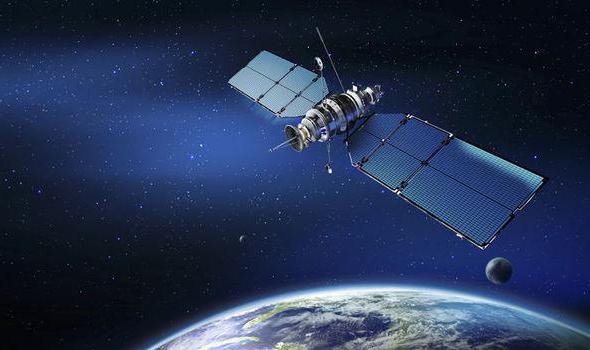
Также данный металл обладает преимуществом при создании космической техники. Благодаря небольшому весу и высоким показателям удельной прочности из алюминия можно изготовить баки, носовые и межбаковые части ракеты. Этот металл хорошо работает при криогенных температурах в контакте с гелием, водородом и кислородом. У него происходит криогенное упрочнение – явление, при котором показатели прочности при понижении температуры растут.
Однако это еще не все, что делают из алюминия. Он находит применение и в других отраслях.
Судостроение
В основном в этой отрасли промышленности материал используют для изготовления корпусов судов, а также коммуникаций для оборудования и палубных надстроек. Благодаря применению этого металла конструкторам удалось на 50-60 % снизить массу судов, благодаря чему достигается высокая экономия топлива и повышенная грузоподъемность, маневренность и скорость также растут.
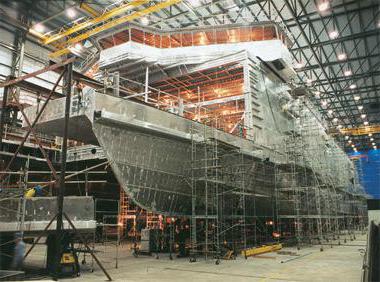
Железнодорожный транспорт
Подвижный состав на железной дороге эксплуатируется в тяжелых условиях, он подвергается ударным нагрузкам. Поэтому и требования к материалам изготовления таких составов высоки. Алюминий целесообразно применять для изготовления железнодорожных составов из-за высокой удельной прочности, небольшой силы инерции, а также повышенной коррозионной стойкости. К тому же в специальных алюминиевых емкостях можно перевозить продукты нефтехимической и химической промышленности.
Автомобильная промышленность
В автомобилях уместно использовать металлы высокой прочности и небольшой массы. При этом они должны быть устойчивыми к коррозии и обладать декоративной поверхностью. Такое вещество, как алюминий, из чего делают кузовы легковых автомобилей, как раз соответствует этим критериям. Благодаря ему производителям удается снизить вес транспорта, сделать его более экономичным и повысить грузоподъемность, а высокая стойкость к коррозии существенно повышает срок эксплуатации автомобиля.
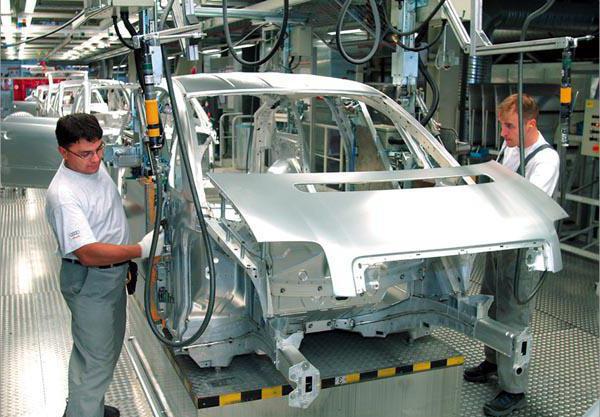
Также из сплавов могут изготавливать балки и рамы тяжелых грузовых машин.
Строительство
В гражданском или промышленном строительстве алюминиевые сплавы тоже активно используются. Их перспективность подтверждена мировой практикой и технико-экономическими расчетами. Применение алюминия позволяет уменьшить металлоемкость и повысить надежность и долговечность конструкции. Большинство современных зданий со стеклянными фасадами имеют «скелет» из данного материала.
Нефтехимическая промышленность
При разработке деталей, применяемых в оборудовании для разведки, добычи и переработки нефти, предъявляются строгие требования к материалу. Бурильное оборудование становится более легким и эффективным при использовании сплавов алюминия, что позволяет упростить его транспортировку и прохождение глубины.
Эти сплавы являются идеальными для изготовления емкостей для хранения нефти. Нефтегазопроводные, бурильные или насосно-компрессорные алюминиевые трубы также тут активно применяются. В частности, для этого используется сплав Д16.
Производство бытовых предметов
В быту не счесть вещей, которые делаются из этого металла. В частности, популярностью пользуются алюминиевые лестницы – они есть практически в каждом доме, гараже. Кухонная утварь, кронштейны для телевизоров – все эти элементы могут быть выполнены из алюминия, что уже говорить про более мелкие предметы.
Алюминиевые лестницы, кстати, уверенно вытеснили железные, так как последние очень тяжело переносить с места на место. Это еще раз демонстрирует преимущество этого металла. Перечислять изготавливаемые из него предметы быта можно очень долго.